Shipyard Employment eTool
General Working Conditions >> Health and Sanitation
In the maritime industry, particularly in a shipyard environment, workers are exposed to health effects that include communicable diseases, heat-related illness, health effects related to the delay of urination and defecation, and the injection or absorption of hazardous substances.
To prevent exposure to these well recognized and documented hazards, workers sanitation needs must be met through various means such as providing protective clothing and an adequate number of sanitation facilities, prohibiting eating, drinking, or smoking in contaminated areas, and providing potable drinking water in ample amounts.
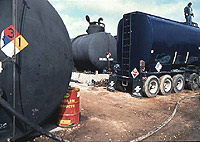
Potential Hazard
Worker illness and injury can be caused by exposure to hazardous substances present in shipyard employment such as garbage, sewage, and toxic substances.
Requirements and Example Solutions
- Facilities, including supplies, must be maintained for employee personal and health needs. Sanitation facilities include potable drinking water, toilet facilities, hand-washing and drying facilities, showers (including quick-drenching or flushing), changing rooms, eating and drinking areas, first aid stations, and on-site medical service areas. Sanitation supplies include: soap, waterless cleansing agents, single-use drinking cups, drinking water containers, toilet paper, and towels.
-
All sanitation facilities, including sewered and portable toilets, must have a determined schedule for servicing, cleaning, and supplying each facility to ensure it is maintained in a clean, sanitary, and serviceable condition (29 CFR 1915.88(a)(2) and (d)(1)(iii)).
- Sanitation facilities, including sewered and portable toilets, must be adequate in number and readily accessible (29 CFR 1915.88(a)(1) and (d)).
- The minimum required number of toilets for each sex, provided in 29 CFR 1915.88(d)(2), are as follows:
- 1 to 15 Employees
- 1 Toilet
- 16 to 35 Employees
- 2 Toilets
- 36 to 55 Employees
- 3 Toilets
- 56 to 80 Employees
- 4 Toilets
- 81 to 110 Employees
- 5 Toilets
- 111 to 150 Employees
- 6 Toilets
- Over 150 Employees
- 1 additional toilet for each additional 40 employees
- When toilets will only be used by men, urinals may be provided instead of toilets, except that the number of toilets in such cases must not be reduced to less than two-thirds of the minimum specified (Note to Table F-2 of §1915.88).
-
When toilet facilities will not be occupied by more than one employee at a time, separate toilets for the opposite sex is not required as long as it can be locked from the inside, and contains at least one toilet (29 CFR 1915.88(d)(1)(ii)(B)).
- Toilet facilities must provide privacy at all times that include each toilet occupying a separate compartment and containing walls or partitions with a door (29 CFR 1915.88(d)(1)(i)).
- Portable toilets are intended for supplemental use; however, where infeasible to provide sewered toilets, or when there is a temporary increase in the number of employees for a short duration of time, these facilities may be provided in meeting the minimum required number of toilets for each sex (29 CFR 1915.88(d)(3)(i)).
- Handwashing facilities must be located at or adjacent to each toilet facility and contain at least one of the following (29 CFR 1915.88(e)(1), (e)(2)(i), and (e)(2)(ii)):
- Hot and cold or lukewarm running water and soap, and clean, single-use hand towels with a sanitary means for disposing of them;
- Hot and cold or lukewarm running water and soap, and clean individual sections of continuous cloth toweling;
- Hot and cold or lukewarm running water and soap, and hand-drying air blower; or
- Waterless skin-cleansing agents.
-
Workers engaged in the application of paints or coatings or in other operations involving hazardous or toxic substances must be trained on the importance of washing their hands and face at the end of the workshift and prior to eating, drinking, or smoking (29 CFR 1915.88(e)(3)).
- Food, beverages, and tobacco products must be prohibited from being consumed or stored in any area where exposure to hazardous or toxic substances is likely (29 CFR 1915.88(h)).
- Changing rooms with privacy for each sex are required when protective clothing is provided to workers to prevent their exposure to hazardous or toxic substances (29 CFR 1915.88(g) and (g)(1)). Separate storage facilities for both street and protective clothes are required (29 CFR 1915.88(g)(2)).
- Potable water must be available in an adequate amount for the health and personal needs of each worker (29 CFR 1915.88(b)(1) and (b)(2)).
- Drinking water made available to workers must be provided from a fountain, a covered container with single-use drinking cups stored in a sanitary receptacle, or single-use bottles. Shared drinking cups, dippers, and water bottles are prohibited (29 CFR 1915.88(b)(3)).
- Non-potable water, which must be clearly marked as "not safe for health or personal use," may be used for purposes such as firefighting and cleaning outdoor premises so long as it does not contain chemicals, fecal matter, coliform, or other substances at levels that may create a hazard for employees (29 CFR 1915.88(c)(1) and (c)(2)).
- When showers are required due to the nature of the work being performed, each facility must provide at least one shower for every 10 workers of each sex. The minimum requirement of at least one shower for each sex also applies for fractions thereof 10 workers (29 CFR 1915.88(f)(1)).
- All showers must be equipped with soap, hot and cold water, and clean towels for each employee who uses the shower (29 CFR 1915.88(f)(2)).
- To prevent the infestation of vermin that may present health and safety hazards for workers, facilities must maintain their property and surrounding areas in a clean manner (29 CFR 1915.88(j)(1)). Such maintenance must include the use of waste receptacles in numbers, sizes, and locations that encourage their use and meet the following specifications (29 CFR 1915.88(i)(1)(iii)):
- Constructed of materials that are corrosion resistant, leak-proof, and easily cleaned or disposable (29 CFR 1915.88(i)(1)(i));
- Equipped with a solid tight-fitting cover (29 CFR 1915.88(i)(1)(ii));
- Emptied often as necessary to prevent overflow, which includes daily servicing for receptacles containing food (29 CFR 1915.88(i)(1)(iv)); and
- Located in areas that do not endanger worker safety and health (29 CFR 1915.88(i)(2) and (i)(3)).
For More Information
- OSHA Fact Sheet entitled, Subpart F – General Working Conditions in Shipyard Employment: Sanitation.
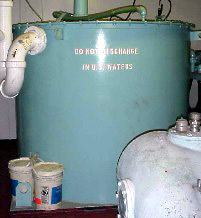
Potential Hazards
Some operations expose employees to biological hazards from sewage and human waste, fungi and molds, and decomposing organic products.
- Collection, holding, and transfer (CHT) tanks, which workers are often required to enter, may contain dangerous, even fatal, levels of hydrogen sulfide or other toxic gases, which are products of decomposing human waste.
- Toxic spores inhaled from fungi and molds growing on grain and lumber may pose an inhalation hazard.
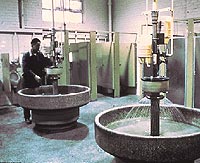
Requirements and Example Solutions
- Employees shall be trained to recognize the potential hazards, use proper work practices, recognize adverse health effects, and understand the physical signs and reactions related to exposures. They shall also be trained to select and use appropriate PPE. [29 CFR 1915.12(d)(2) and 29 CFR 1915.1200]
- Appropriate hygiene practices are required [29 CFR 1915.88]. This includes the following:
- Decontamination (removal of biological matter from PPE and equipment).
- Showers (removal of biological matter from the worker). [29 CFR 1910.141]
- Proper disposal of laundry and coveralls (prevention of exposure to others).
Additional Resources
- Bloodborne Pathogens. OSHA Safety and Health Topics.