Shipyard Employment eTool
Cleaning and Other Cold Work >> Cleaning Operations
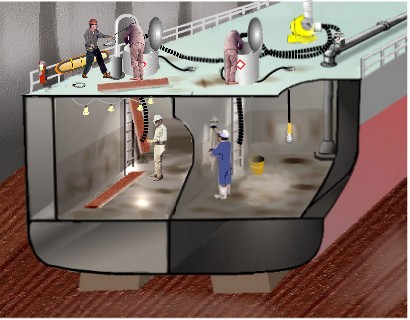
After the spaces are evaluated by the Shipyard Competent Person (SCP), Certified Marine Chemist (CMC), or Certified Industrial Hygienist (CIH), decisions must be made that determine the personnel, equipment, and materials required for the cleaning and cold work. In addition, a hazard assessment must be conducted for selecting appropriate PPE. [29 CFR 1915.152(b)]
Cleaning and cold work exposes workers to potentially hazardous atmospheres, as well as the following hazards:
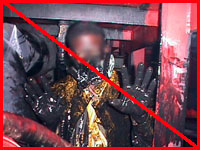
Potential Hazards
Fire and explosions may be caused by:
- Flammable and combustible cleaning solvents such as Methyl Ethyl Ketone (MEK), mineral spirits, and diesel fuel/oil
- Liquids with high flash points (greater than 100º F) applied as a fine mist
- Airborne particulate or dust
- Hydrogen gas generated during cleaning processes
- Reactive cargos such as iron-ore, fertilizer, or incompatible chemicals
- Painting. See Painting and Other Coatings [29 CFR 1915.35]
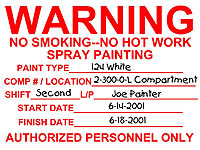
Requirements and Example Solutions
When shipyard operations are capable of producing flammable/combustible atmospheres:
- Rags soaked with solvents must be placed in covered metal containers. [29 CFR 1915.36(a)(3)]
-
No smoking or open flames are allowed. [29 CFR 1915.36(a)(1)]
- Arcing and sparking equipment and tools must not be used. [29 CFR 1915.36(a)(1)]
- Equipment that may generate static electricity such as ventilation systems must be grounded/bonded. [29 CFR 1915.13(b)(11)].
- Explosion-proof lights must be used. [29 CFR 1915.36(a)(4) and 29 CFR 1915.13(b)(9)]
- Adequate ventilation must be maintained (less than 10 percent of LEL). [29 CFR 1915.13(b)(3) and 29 CFR 1915.36(a)(2)]
-
Frequent tests shall be required during cleaning operations to determine if air concentrations are below 10 percent of the LEL. [29 CFR 1915.36(a)(2)]
- The Shipyard Competent Person (SCP) must test the exhaust location to ensure that exhausted vapors do not accumulate to hazardous levels. [29 CFR 1915.13(b)(7), (b)(8), (b)(11), and (b)(12)]
- Suitable fire fighting equipment must be immediately available. [29 CFR 1915.36(a)(6)]
-
Personnel using fire fighting equipment must be instructed in anticipated fire hazards and how to use the equipment. [29 CFR 1915.508] See the Fire Protection: Training page.
- Spills of solvents must be cleaned up immediately. [29 CFR 1915.13(b)(5)]
- For additional requirements, see the Fire Protection chapter.
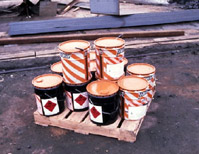
Potential Hazards
Toxic vapors produced by cleaning agents such as freons and trichloroethane may present significant health hazards including oxygen-deficient atmospheres. When used in confined or enclosed spaces these agents produce vapors that are often heavier than air. This can cause displacement of air, reducing oxygen levels, which may be fatal.
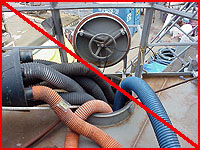
Requirements and Example Solutions
- Ensure adequate ventilation to maintain concentrations below the PEL. [29 CFR 1915.32(a)(2)]
- The Shipyard Competent Person (SCP) may require continual monitoring to determine air concentrations are within the PELs and below IDLH levels. If they are not, additional engineering controls such as ventilation, administrative controls, or PPE such as respirators must be used. [29 CFR 1915.32(a)(3)]
- Airline respirators may be necessary if ventilation is not adequate.
- Respirators must comply with 29 CFR 1915.154. [29 CFR 1910.134]
- A hazard assessment shall be made to determine the proper selection of respirators. [29 CFR 1915.152(b)]
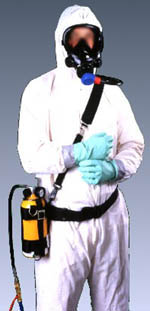
Additional Resources
- Ventilation. See Confined or Enclosed Spaces and Other Dangerous Atmospheres.
- Respiratory Protection. OSHA eTool.
- Inspection procedures for the Respiratory Protection Standard. OSHA Directive CPL 02-00-158, (2014, June 26).
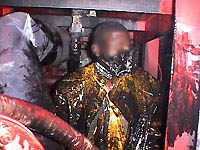
Potential Hazards
Employees working with toxic solvents are at risk if skin and eye contact occurs. Note: Workers should understand the hazards associated with the materials used and contained in the space. This includes training in accordance with the Hazard Communication Standard. [29 CFR 1915.1200]
Hazards include:
- Organ damage by absorption through skin or eye absorption
- Skin or eye irritation
- Defatting of skin
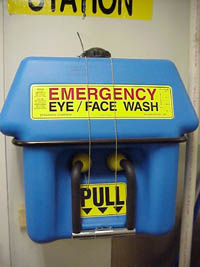
Requirements and Example Solutions
- Use adequate ventilation.Ventilation. See Confined or Enclosed Spaces and Other Dangerous Atmospheres.
- The Shipyard Competent Person (SCP) may require continual monitoring to determine that air concentrations are within the PELs and below IDLH levels. If they are not, additional engineering controls such as ventilation, administrative controls, or PPE such as respirators must be used. [29 CFR 1915.32(a)(3)]
- Spills of hazardous materials must be cleaned up as work progresses. [29 CFR 1915.13(b)(5)]
- Because of the corrosive nature of many of the materials used, suitable facilities for quick drenching or flushing of the eyes and body shall be available. [29 CFR 1910.151(c) and Maritime Labor/Industry Recommendations]
- Washing facilities must be available when working with materials which may be harmful through skin contact. [29 CFR 1915.88(e)]
- Personal hygiene practices must be encouraged, such as washing hands and face before eating, drinking, and smoking. [29 CFR 1915.88(e)(3)]
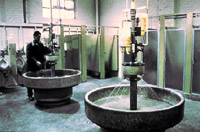
Additional Resources
- Hazard Communication Guidelines for Compliance. OSHA Publication 3111 , (2000).
- Hazard Communication. OSHA Safety and Health Topics Page.
- Fixed or portable eye wash stations/safety showers should meet ANSI Z358.1-1998: Emergency Eye Wash and Shower Equipment.
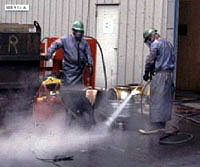
Potential Hazards
Use of high-pressure cleaning equipment may produce high levels of noise, which could lead to hearing loss, and often necessitates a hearing conservation program. An excessively loud operation is:
Use of high-pressure water and steam guns

Requirements and Example Solutions
- Hearing protection. [29 CFR 1910.95(a)]
- Hearing conservation program. [29 CFR 1910.95(c)]
Additional Resources
- Hearing protection. See the PPE Selection: Hearing Protection chapter.
- Occupational Noise Exposure. OSHA Safety and Health Topics Page.
- Noise. OSHA Technical Manual Chapter.
- 29 CFR 1910.95(b)(1), Guidelines for Noise Enforcement; Appendix A. OSHA Directive CPL 02-02-035 [CPL 2-2.35A], (1983, December 19).
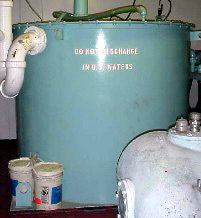
Potential Hazards
Some operations expose employees to biological hazards from sewage and human waste, fungi and molds, and decomposing organic products.
- Collection, holding, and transfer (CHT) tanks, which workers are often required to enter and clean, may contain dangerous, even fatal, levels of hydrogen sulfide or other toxic gases, which are products of decomposing human waste.
- Toxic spores inhaled from fungi and molds growing on grain and lumber may pose an inhalation hazard.
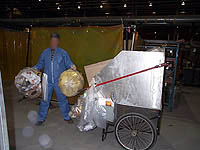
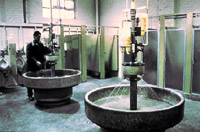
Requirements and Example Solutions
- Employees shall be trained to recognize the potential hazards, use proper work practices, recognize adverse health effects, and understand the physical signs and reactions related to exposures. They shall also be trained to select and use appropriate PPE. [29 CFR 1915.12(d)(2) and 29 CFR 1915.1200]
- Personal hygiene practices must be encouraged, such as: [29 CFR 1915.88]
- Decontamination (removal of biological matter from PPE and equipment)
- Showers (removal of biological matter from the worker) [29 CFR 1915.88(f)]
- Proper disposal of laundry/coveralls (prevention of exposure to others)
- The Maritime/Labor Industry recommends having a Bloodborne Pathogen program.
Additional Resources
- Bloodborne Pathogens and Needlestick Prevention. OSHA Safety and Health Topics Page.
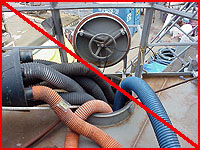
Potential Hazards
When working in confined or enclosed spaces workers may become trapped and unable to exit due to:
- Improperly located equipment.
- Ventilation ducts and hoses running through the opening.
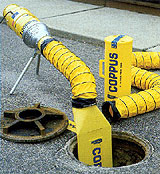
Requirements and Example Solutions
- When employees work in confined spaces or enclosed spaces with limited access, the access must not be blocked or impeded by ventilation ducts, hoses or other equipment. [29 CFR 1915.76(b)(2)]
- More than one means of access must be provided where practical. [29 CFR 1915.76(b)(1)]
- Additional openings should be provided for ducts, hoses, and other equipment.
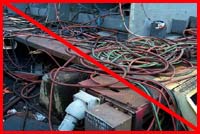
Potential Hazards
Workers performing surface preparation are exposed to slippery working surfaces and tripping hazards.
- Slipping off oily and greasy ladders
- Slipping and falling on oily decks.
- Tripping over equipment, hoses, and vessel structures.
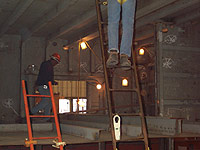
Requirements and Example Solutions
- Spills shall be cleaned up immediately. [29 CFR 1915.13(b)(5) and 29 CFR 1915.91]
- Visual Inspection will be conducted. See Confined or Enclosed Spaces and Other Dangerous Atmospheres.
- Adequate Illumination will be provided. See General Working Conditions.
- Housekeeping as described in 29 CFR 1915.91 will be maintained.
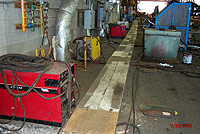

Potential Hazards
Fall hazards are a leading cause of shipyard fatalities. Shipyard employees are often required to work in dangerous environments that may include fall hazards. Accidents involving elevation equipment such as ladders, scaffolds, and aerial lifts are often serious, even fatal.
High-Pressure Cleaning
- Surges from drops in pressure in the hose line may throw a worker from the work surface
- Cleaning can create static electricity. This may shock the worker and result in a fall
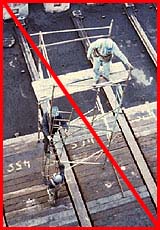
Deck Openings and Edges
- Falls from deck openings
- Falls into open holes
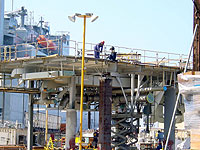
Scaffolds
- Falls from ladders
- Falls from scaffolds
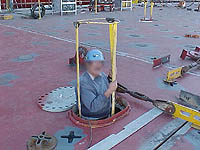
Requirements and Example Solutions:
High-Pressure Cleaning
- Cleaners must be protected by proper fall protection. [29 CFR 1915.34(c)(3)(v)]
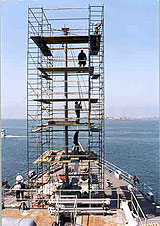
Guarding of Deck Openings and Edges
- Openings and deck edges must be guarded. [29 CFR 1915.73]
- Flush manholes and other small openings must be guarded after opening. [29 CFR 1915.73(b)]
- Fall protection (harness with lanyard) must be used during the installation of guards on large openings and deck edges. [29 CFR 1915.73(d)]
- Openings must be guarded or planked when floor plates or gratings (e.g. bilges, engine rooms, pump rooms, machinery spaces) are removed. [29 CFR 1915.73(f)]
Fall Protection for Scaffold Work
- Guardrails or other appropriate fall protection must be used when working on scaffolds 5 feet above surfaces. [29 CFR 1915.71(j)]
- Fall protection must be used during the installation of guards on scaffolds. [29 CFR 1915.73(d)]
- Maritime Labor/Industry recommends that personal fall protection including lanyards and harnesses be used and secured during installation of guardrails as well as erection and dismantling of scaffolds.
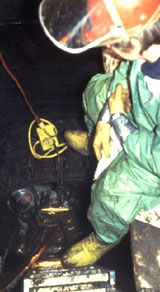
Potential Hazards
Extreme environmental hazards include temperature, humidity, and air movement within the work area. A combination of PPE use, heat producing equipment, work activity, and environmental conditions can cause temperature-related illnesses.
Heat related illnesses include:.
- Heat Stress
- Heat Stroke
- Heat Cramps
- Dehydration
Cold related illnesses include:.
- Hypothermia
- Frost Bite
Additional Resources
- OSHA Technical Manual (OTM). OSHA Directive TED 01-00-015 [TED 1-0.15A], (1999, January 20). Identifies heat stress as part of the evaluation process in the following:
- Heat Stress. Contains useful sections on the signs and symptoms of heat stress, sampling methods, control suggestions, and guidelines for investigating heat stress in the workplace.
- Occupational Heat Exposure. OSHA Safety and Health Topics Page.
Example Solutions:
The following are recommended for heat-related illnesses:
- Plenty of fluids
- Frequent breaks
- Ice vest
- Shaded or cooled break areas
- Ventilation
- Awareness training
It is recommended that the following be implemented to prevent cold related illnesses:
- Appropriate insulated PPE
- Warming areas for breaks
- Conduct awareness training
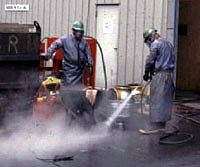
Potential Hazards
The use of high pressure equipment may expose the operator and other workers to the following hazards:
- Contact with high-pressure steam, water, or air streams from cleaning equipment
- Contact by uncontrolled high-pressure hoses
- Contact with steam, water, or air leaks from high-pressure equipment
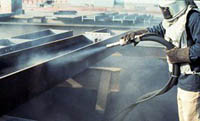
Injuries associated with these hazards include:
- Loss of body parts such as fingers, hands, etc.
- Lacerations
- Burns
- Loss of sight
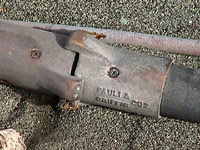
Requirements and Example Solutions
- Steam guns must be insulated to prevent heat burns to the operator. [29 CFR 1915.33(e)]
- Appropriate PPE shall be used. [29 CFR 1915.152]
- Access to the area should be controlled.
- Hoses and connections should be inspected before use.
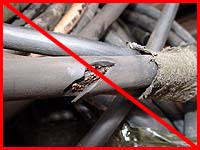
Potential Hazards
Employees who work with or around electrical equipment in wet or damp locations have an increased risk of getting shocked or electrocuted due to:
- Exposed energized electrical parts
- Open lighting parts
- Damaged insulation on power cords
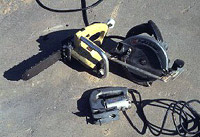
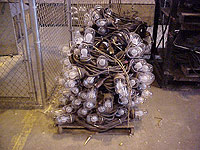
Requirements and Example Solutions
- Portable electrical tools must be grounded or double insulated. [29 CFR 1915.132(a)]
- Temporary lighting must be grounded. [29 CFR 1915.92(c)]
- Power and lighting cables must be inspected by a person competent to evaluate electrical hazards. (Note: This is not the Shipyard Competent Person). [29 CFR 1915.36(a)(5)]
- All electrical tools or equipment should undergo a visual inspection prior to use.
- All portable electric hand tools and temporary lighting systems should use Ground Fault Circuit Interrupters (GFCI).
- Electrical tools and equipment should correspond with the requirements of the job.
- Electrical equipment and tools should be used with proper circuit protection for the voltage and amperage used.
- Only qualified electricians should attempt repair of electrical tools and equipment in use.
- A Ground Assurance Program should be in place for all electrical tools and equipment used including:
- Records of tools inspected and repaired
- Records of electrical boxes inspected and repaired
- Records of electrical extension cords inspected and repaired
- Recall of records of the above
- The requirements of the Ground Assurance Program should be performed on a regular basis.