Woodworking eTool
Woodworking » Point of Operation
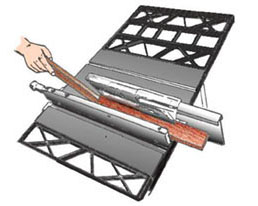
The point of operation is the place where work is performed on the material. This is where the stock is cut, shaped, bored, or formed. Most woodworking machines use a cutting and/or shearing action.
-
Employees can be injured if their hands get too close to the blade, particularly when working on small pieces of stock. The size of the piece dictates that the operator's hand be close to the blade. Accidents can occur when stock unexpectedly moves or when a worker's hand slips.
-
Stock can get stuck in a blade and actually pull the operator's hands into the machine.
-
Employees can be injured if the machine or its guard is not properly adjusted or maintained. An improperly adjusted radial saw, for example, might not return to its starting position after making a cut.
-
If the machine has controls that are not recessed or remote, and the equipment is accidentally started, a worker's hands may be caught at the point of operation.
-
Contact also can occur during machine repair or cleaning if care is not taken to de-energize the machine - that is, if lockout/tagout procedures are not followed.
-
An employee may be injured if he or she reaches in to clean a saw or remove a piece of wood after the saw has been turned off, but is still coasting or idling. Also, saw blades often move so fast that it can be difficult to determine whether they are moving. This is especially a problem under fluorescent lighting.
Engineering Controls
-
Machine Guarding - Guards are now standard equipment on most woodworking machines. If you purchase a machine that does not come equipped with a guard, install one. Contact the manufacturer of the machine to see if appropriate guard(s) are available for the equipment. If not, use this guide to help you determine the appropriate guard to install. Because woodworking equipment is dangerous, guards should always be designed and installed by technically competent and qualified persons. In addition, it is always a good idea to have the equipment manufacturer review proposed guard designs to ensure that the guard will adequately protect employees and allow safe operation of the equipment.
-
There are many ways to guard machines. The type of operation, size or shape of stock, work being performed on the material, method of handling, and production requirements are some of the factors that help determine the appropriate safe-guarding method for an individual machine. All moving machine parts that may cause injury must be safeguarded. This includes the point of operation, the power transmission apparatus, and rotary or reciprocating parts. Table 1 describes three types of machine guards commonly used on woodworking machinery: fixed, adjustable, and self-adjusting.
-
To be effective, a guard should prevent employees from contacting the dangerous parts of the machines, and it should be secure. This is not always possible, as in the case of the radial arm saw. Regardless, workers should not be able to easily bypass, remove, or otherwise tamper with the guard. In protecting the worker, however, the guard must not create additional hazards, nor prevent the worker from performing the job.
-
Make sure that guards are in working order and that they are appropriate and practical for the machinery. Guards must have adequate strength to resist blows and strains and should be constructed to protect operators from flying splinters and machine parts such as broken saw teeth, cutting heads, and tools.
-
The Rough Mill and Production sections provide more detailed information on methods of machine guarding (including construction of guards), and guard types for specific woodworking machines.
-
Additional methods for safeguarding machines include guarding by location or distance, feeding methods, and appropriate placement of controls. However, none of these methods should replace machine guards. It is always important to provide a guard or barrier that prevents access to the danger area. Table 2 describes these other safeguarding methods.
Work Practice Controls
-
Use appropriate equipment for the job. Workers can be seriously injured if they do not use the correct equipment for a job. Use machines only for work within the rated capacity specified by the machine manufacturer. Use the correct tools on a given machine. For example, when using a circular saw, use the correct blade for the required cutting action. Similarly, you must only mount blades, cutter heads, or collars on machine arbors that have been accurately sized and shaped to fit these parts.
-
Train workers on machine use and allow only trained and authorized workers to operate and maintain the equipment. Workers should understand the purpose and function of all controls on the machine, should know how to stop the equipment in an emergency, and should be trained on the safety procedures for special set-ups. Operator training should include hazards associated with the machine, how the safeguards protect the worker from these hazards, under what circumstances the guard may be removed (usually just for maintenance), and what to do if the guard is damaged or not functioning properly. Employees should be able to demonstrate their ability to run the machine with all safety precautions and mechanisms in place.
-
Frequently inspect equipment and guards. Ensure that: (1) the operator and machine are equipped with the safety accessories suitable for the hazards of the job, (2) the machine and safety equipment are in proper working condition, and (3) the machine operator is properly trained. Document the inspections and keep the records. Documentation should identify the machine, inspection date, problems noted, and corrective action taken. Noting problems helps to ensure that corrective action will be taken, that operators on all shifts will be made aware of any potential danger, and that any pattern of repeat problems on a particular machine can be detected and resolved as early as possible.
-
Use equipment only when guards are in place and in working order. A worker should not be allowed to operate a piece of woodworking equipment if the guard or any other safety device, return device, spreader, anti-kickback fingers apparatus, guard on in-running rolls, or gauge or rip fence is not functioning properly. When guards cannot be used (during rabbeting or dadoing, for instance), you must provide combs, featherboards, or suitable jigs for holding the stock.
-
Provide employees with push sticks or other hand tools so that their hands are away from the point of operation when they work on small pieces of stock. A push stick is a strip of wood or block with a notch cut into one end that is used to push short or narrow lengths of material through saws (Fig. 1). Using push sticks keeps stock from tipping and prevents the operator's fingers from coming in contact with blades.
-
Use a brush or stick to clean sawdust and scrap from a machine. Never allow your employees to clean a saw with their hands or while the machine is running.
-
Never leave a machine unattended in the "on" position. Make sure that workers know never to leave a machine that has been turned off but is still coasting.
-
Maintain proper housekeeping. Workers have been injured by tripping and then falling onto the blades of saws. You must keep floors and aisles in good repair and free from debris, dust, protruding nails, unevenness, or other tripping hazards. Do not use compressed air to blow away chips and debris. Make sure you have a non-slip floor.
-
Never saw freehand. Always hold the stock against a gauge or fence. Freehand sawing increases the likelihood of an operator's hands coming in contact with the blade.
-
Use appropriate personal protective equipment.