Woodworking eTool
Woodworking » Rotary and Reciprocating Movements
All machines operate by rotating or reciprocating motion or by a combination of these motions. Reciprocating movement is back-and-forth or up-and-down motion. Rotary cutting and shearing mechanisms, rotating wood stock, flywheels, shaft ends, and spindles all rotate. Rotating action is hazardous regardless of the speed, size, or surface finish of the moving part.
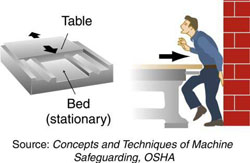
-
Rotating parts and shafts, such as stock projecting from the chuck of a lathe, can catch hair or clothing and draw the operator in. This can seriously mangle or crush the operator.
-
Operators can be struck by a projecting bolt or key.
-
Rotating parts and stock can force an arm or hand into a dangerous position, breaking bones and lacerating or severing a hand or other parts of a limb.
-
Operators can be caught and crushed by reciprocating movement when the moving part approaches or crosses a fixed part of the machine (Fig. 1).
Engineering Controls
Machine Guarding - Guards are now standard equipment on most woodworking machines. If you purchase a machine that does not come equipped with a guard, install one. Contact the manufacturer of the machine to see if appropriate guard(s) are available for the equipment. If not, use this guide to help you determine the appropriate guard to install. Because woodworking equipment is dangerous, guards should always be designed and installed by technically competent and qualified persons. In addition, it is always a good idea to have the equipment manufacturer review proposed guard designs to ensure that the guard will adequately protect employees and allow safe operation of the equipment.
There are many ways to guard machines. The type of operation, size or shape of stock, work being performed on the material, method of handling, and production requirements are some of the factors that help determine the appropriate safe-guarding method for an individual machine. All moving machine parts that may cause injury must be safeguarded. This includes the point of operation, the power transmission apparatus, and rotary or reciprocating parts. Table 1 describes three types of machine guards commonly used on woodworking machinery: fixed, adjustable, and self-adjusting.
To be effective, a guard should prevent employees from contacting the dangerous parts of the machines, and it should be secure. This is not always possible, as in the case of the radial arm saw. Regardless, workers should not be able to easily bypass, remove, or otherwise tamper with the guard. In protecting the worker, however, the guard must not create additional hazards, nor prevent the worker from performing the job.
Make sure that guards are in working order and that they are appropriate and practical for the machinery. Guards must have adequate strength to resist blows and strains and should be constructed to protect operators from flying splinters and machine parts such as broken saw teeth, cutting heads, and tools.
The Rough Mill and Production sections provide more detailed information on methods of machine guarding (including construction of guards), and guard types for specific woodworking machines.
Additional methods for safeguarding machines include guarding by location or distance, feeding methods, and appropriate placement of controls. However, none of these methods should replace machine guards. It is always important to provide a guard or barrier that prevents access to the danger area. Table 2 describes these other safeguarding methods.
Work Practice Controls
Train workers on machine use and allow only trained and authorized workers to operate and maintain the equipment. Workers should understand the purpose and function of all controls on the machine, should know how to stop the equipment in an emergency, and should be trained on the safety procedures for special set-ups.
Operator training should include hazards associated with the machine, how the safeguards protect the worker from these hazards, under what circumstances the guard may be removed (usually just for maintenance), and what to do if the guard is damaged or not functioning properly.
Employees should be able to demonstrate their ability to run the machine with all safety precautions and mechanisms in place.
Frequently inspect equipment and guards. Ensure that: (1) the operator and machine are equipped with the safety accessories suitable for the hazards of the job, (2) the machine and safety equipment are in proper working condition, and (3) the machine operator is properly trained. Document the inspections and keep the records. Documentation should identify the machine, inspection date, problems noted, and corrective action taken. Noting problems helps to ensure that corrective action will be taken, that operators on all shifts will be made aware of any potential danger, and that any pattern of repeat problems on a particular machine can be detected and resolved as early as possible.
Use equipment only when guards are in place and in working order. A worker should not be allowed to operate a piece of woodworking equipment if the guard or any other safety device, return device, spreader, anti-kickback fingers apparatus, guard on in-running rolls, or gauge or rip fence is not functioning properly. When guards cannot be used (during rabbeting or dadoing, for instance), you must provide combs, featherboards, or suitable jigs for holding the stock.
Never leave a machine unattended in the "on" position. Make sure that workers know never to leave a machine that has been turned off but is still coasting.
Maintain proper housekeeping. Workers have been injured by tripping and then falling onto the blades of saws. You must keep floors and aisles in good repair and free from debris, dust, protruding nails, unevenness, or other tripping hazards. Do not use compressed air to blow away chips and debris. Make sure you have a non-slip floor.
Do not allow workers to wear loose clothing or long hair. Loose clothing or long hair can be easily caught up in rotating parts.
Use appropriate personal protective equipment.