Woodworking eTool
Specific Finishing Equipment » Shapers
Woodworking shapers are machines that are most commonly used to shape the edges of stock. Cutting occurs by hand feeding stock against a vertical rotating cutter mounted on a spindle. Some machines have multiple spindles. The cutter has multiple cutting edges and rotates at 7200 to 10,000 RPM. Stock may be fed from any direction. Guide pins hold the stock for curved shaping and fences hold it for straight line shaping.
Operator Involvement
The operator is required to hand-feed and manipulate the stock against the cutter and to keep the stock flat on the table. The type of work being done is better described as hand crafting rather high-speed cutting.
-
Point of operation - Contact with the cutter head may occur, particularly if holding devices are not used.
Possible Solutions:
Engineering Controls
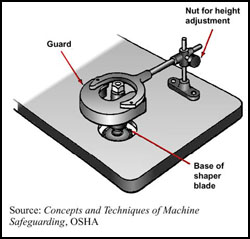
-
As shown in Fig. 1, enclose the spindle with an adjustable guard or cage [29 CFR 1910.213(m)(1)]. For straight-line shaping, the fence frame should include the guard. The fence should contain as small an opening as possible for the knives, and should extend at least 18 inches on either side of the spindle. Split adjustable fences are useful for guarding when the entire edge of the stock is to be shaped.
-
Mount a ring guard around the cutting bit to reduce contact with the bit.
Work Practices
-
Use templates, jigs, and fixtures to distance the operator's hands from the point of operation. Featherboards may be clamped to the fence for straight line shaping.
-
Tool projection - Knives may be flung if the cutter head is unbalanced.
Possible Solutions
Engineering Controls
-
Use a safety collar to minimize the potential for tool projection.
Work Practices
-
Maintain the knives. Make sure they are precision-ground to apply uniform pressure. Make sure the knives are balanced and fit properly [29 CFR 1910.213(s)(2)].
-
Train operators to listen for "chatter," which indicates that knives are out of balance. To start the machine, operators should apply the power in a series of short starts and stops to slowly bring the spindle to operating speed.
-
Kickbacks - Stock may be thrown back at the operator after being caught by the cutter head.
Possible Solutions
Engineering Controls
-
Ensure that double-spindle shapers have a starting and stopping device for each spindle [29 CFR 1910.213(m)(3)].
Work Practices
-
Cut in the opposite direction of the spindle's rotations.
-
Flying chips - Wood chips and splinters may be thrown by the cutting action of the knives.
Possible Solutions
Work Practices
-
Maintain the knives. Make sure they are precision-ground to apply uniform pressure. Make sure the knives are balanced and fit properly [29 CFR 1910.213(s)(2)].
-
In-running nip points - Clothing, hair, or hands may be caught by and pulled into the in-running rolls of the automatic feed.
Possible Solutions
Engineering Controls
-
Guard automatic feed rollers [29 CFR 1910.213(b)(7)].
Potential Hazard
-
Operating controls are mounted on the front of the machine about waist high. This could allow incidental starting.