Evacuation Plans and Procedures eTool
Develop & Implement an Emergency Action Plan (EAP) » Evacuation in or through High Hazard Environments
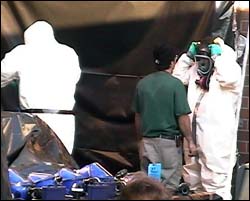
Though this eTool focuses on evacuations for low-hazard businesses, some small businesses may deal with chemicals or substances that could be hazardous during an emergency. In this situation, a prudent employer may provide additional equipment for employees to safely evacuate.
Your employees may need personal protective equipment to evacuate during an emergency. Personal protective equipment must be based on the potential hazards in the workplace. Assess your workplace to determine potential hazards and the appropriate controls and protective equipment for those hazards. Personal protective equipment may include items such as the following:
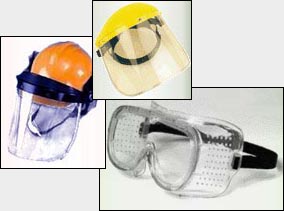
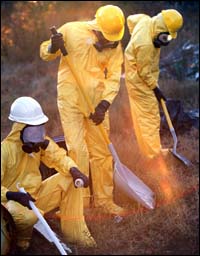
- Safety glasses, goggles, or face shields for eye protection;
- Hard hats and safety shoes for head and foot protection;
- Proper respirators;
- Chemical suits, gloves, hoods, and boots for body protection from chemicals;
- Special body protection for abnormal environmental conditions, such as extreme temperatures; and
- Any other special equipment or warning devices necessary for hazards associated with your worksite.
Consult with health and safety professionals before making any purchases. Respirators selected should be appropriate to the hazards in your workplace, meet OSHA standards' criteria, and be certified by the National Institute for Occupational Safety and Health (NIOSH).
Respiratory protection may be necessary if your employees must pass through toxic atmospheres (such as dust, mists, gases, or vapors) or through oxygen-deficient areas while evacuating. There are four basic categories of respirators for use in different conditions. All respirators must be NIOSH-certified under the current 29 CFR 1910.134. See also OSHA's Small Entity Compliance Guide for Respiratory Protection Standard.
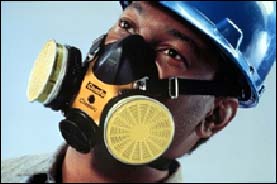
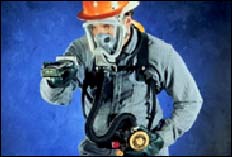
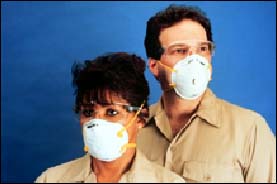