Hurricane eMatrix
List of Activity Sheets » Community support and public health services
Removing Human and Animal Remains
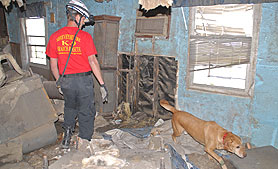
This picture shows actual disaster site work conditions and may not illustrate proper safety and health procedures.
Activity Description
- This activity sheet outlines the hazards that apply to any response and recovery worker involved in recovering human remains and transferring them to a mortuary service facility for identification. It also applies to those who handle and dispose of animal remains after a natural disaster.
- For some operations or situations (e.g., permit-required confined space entry, heavy equipment use) other activity sheets also apply; see related activity sheets below.
- After any natural disasters, like Hurricanes Katrina and Rita (2005), that involve loss of life, human and animal remains must be removed from the site and transferred to an appropriate location.
- Human remains are recovered from the disaster site and transferred to an approved facility that provides mortuary services. Response and recovery workers typically recover human remains by manually transferring them to a body bag and stretcher. This activity occurs early in the recovery process, but will continue as long as deceased victims continue to be found.
- Animal remains are collected and disposed of using an appropriate method (typically burying or incineration). Animal remains are typically transferred manually or with assistance from heavy equipment.
- Mass disposal of animal remains should occur as soon as time and resources allow; this will help ensure that the animal remains stay intact and response and recovery workers will have less contact with body fluids.
- Response and recovery workers might need to shift debris, work in water, or enter enclosed areas to access remains. However, some hazards originally present at the recovery site during initial search-and-rescue activities can be stabilized or abated (e.g., downed power lines deenergized) before remains are recovered
- Response and recovery workers conducting this operation may be employed by Federal, State, local, and private employers. Review How to Use This Matrix in the introduction for a discussion of how this information may apply to different workers.
About the Activity Sheet
This activity sheet does not provide an in-depth analysis of OSHA standards and regulations and cannot address all hazards. It does not increase or diminish any OSHA requirement or employer obligation under those requirements. It is intended as a guide and quick reference for employers and response and recovery workers. The Matrix captures major activities involved in hurricane response and recovery, highlights many of the hazards associated with them, and recommends beneficial work practices, personal protective equipment (PPE), and other exposure control methods. Employers must evaluate the specific hazards associated with the job/operation at the site where the work is being performed.
Employers are responsible for providing a safe and healthful workplace for their workers. OSHA's role is to assure the safety and health of America's workers by setting and enforcing standards; providing training, outreach, and education; establishing partnerships; and encouraging continual improvement in workplace safety and health.
The Hazard Exposure and Risk Assessment Matrix for Hurricane Response and Recovery Work provides a general overview of particular topics related to current OSHA standards. It does not alter or determine compliance responsibilities in OSHA standards or the Occupational Safety and Health Act of 1970, or the equivalent State Plan standards and requirements. Because interpretations and enforcement policy may change over time, you should consult current OSHA/State Plan administrative interpretations and decisions by the Occupational Safety and Health Review Commission and the courts for additional guidance on OSHA compliance requirements. Employers should modify their procedures as appropriate when additional, relevant information becomes available.
General Recommendations
Key Engineering Controls and Work Practices. See general recommendations document.
Personal Protective Equipment. The general PPE is recommended for all response/recovery tasks/operations; only the additional PPE that may be needed for a specific hazard is noted below.
General PPE includes:
- Hard hat for overhead impact or electrical hazards
- Eye protection with side shields
- Gloves chosen for job hazards expected (e.g., heavy-duty leather work gloves for handling debris with sharp edges and/or chemical protective gloves appropriate for chemicals potentially contacted)
- ANSI-approved protective footwear
- Respiratory protection as necessary—N, R, or P95, filtering facepieces may be used for nuisance dusts (e.g., dried mud, dirt and silt) and mold (except mold remediation). Filters with a charcoal layer may be used for odors
Recommendations Specific to Hazards Associated with Removing Human and Animal Remains
Key Engineering Controls and Work Practices
- Limit access/set up controlled access zones until stability and structural integrity is known
- Ensure that a competent person inspects building and floors before entry to perform work. A competent person is able to recognize existing and predictable hazardous conditions and has the authority to take prompt corrective measures to eliminate the hazardous conditions
- Install temporary structural support (shoring, bracing) adequate to protect workers
Key Engineering Controls and Work Practices
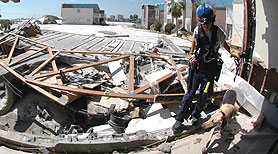
- Remove or secure objects (glass, structural members) that may fall while workers work under them
- Use debris netting, sidewalk sheds, canopies, or catch platforms to reduce hazards from falling objects
- Assess the presence, contents, and condition of tanks and equipment that might contain hazardous chemicals, gases, or flammable materials. If the condition of tanks or equipment is suspect, avoid disturbing them
- Use air monitoring equipment to determine if the contents of the tanks or equipment are creating a hazardous atmosphere (e.g., flammable, combustible, corrosive, toxic, or oxygen-deficient). When necessary, provide additional controls (e.g., forced ventilation, respiratory protection)
- Test and purge tanks and equipment that may be impacted by work operations
Key Engineering Controls and Work Practices
- Assume that electrical lines are energized until proven otherwise. Lines and other conductors may become re-energized without warning as utilities are evaluated and restored after a disaster
- Inspect the work area for downed conductors and do not go near, drive over, or otherwise come in contact with them
- Downed electrical conductors can energize other objects, including fences, water pipes, bushes, trees, and telephone/CATV/fiber optic cables
- Unless deenergized and visibly grounded, maintain proper distance from overhead electrical power lines (at least 10 feet) and/or provide insulating barriers
- Do not approach any gas leaks; if a gas leak is detected, secure spark-producing devices (e.g., engines, tools, electronic, and communications equipment) and evacuate the area until the leak is secured
- Contact utility company to assist in locating, marking, and shutting off/purging utility lines that may pose a hazard or may be impacted; ensure that lines have been purged as needed before beginning work
Key Engineering Controls and Work Practices
- Follow universal precautions, including washing any areas of the body or clothing that become contaminated with blood or bodily fluids
- Wash hands with soap and water every time gloves are removed. In the absence of soap and water, use an alcohol-based hand cleaner after glove removal. However, wash hands with soap and water as soon as feasible
- Do not wear PPE or clothing that has been damaged or has been penetrated by body fluids
- Report injuries and exposures to body fluid to supervisor
- Decontaminate equipment before reuse; do not reuse gloves or other disposable PPE
Additional Personal Protective Equipment
- Fluid-proof gloves (e.g., latex, nitrile, rubber). Cover with heavy-duty work gloves if potential for cuts and abrasions (e.g., moving debris)
- Protective clothing appropriate for preventing blood penetrating to underlying skin/clothing
Key Engineering Controls and Work Practices
- Inspect ladders for cracked, broken, or defective parts before use
- Do not exceed the load rating of ladders—remember that load ratings include people, tools, and equipment
- Set up ladders on stable surfaces
- Set extension or straight ladders at a 75 degree angle from the ground (1/4 foot back for every foot of rise) and provide 3 feet above an upper landing surface to ease climbing onto/descending from height
- Use non-conductive ladders (e.g., fiberglass) and exercise extreme caution when working near power lines
- Secure ladders that can be displaced by work activities; consider barricades at the base to keep traffic away
Key Engineering Controls and Work Practices
- See Work Zone Safety and Traffic Control within a Work Area activity sheet
Additional Personal Protective Equipment
- ANSI/ISEA 107-2004 compliant high visibility safety apparel and headwear
Key Engineering Controls and Work Practices
- See Heavy Equipment and Powered Industrial Truck Use activity sheet
Additional Personal Protective Equipment
- Hearing protection—see Noise hazard
Key Engineering Controls and Work Practices
- Use buoys to mark underwater locations of submerged materials
- Use additional protections, such as a lifesaving skiff and a ring buoy, as appropriate
- Ensure that all divers and support teams follow the Diving and Diver-Support Operations activity sheet
- See Deep-Water Work/Boating Operations activity sheet as needed
Additional Personal Protective Equipment
- Coast Guard-approved Type I or II personal floatation devices
- Watertight boots with steel toe and insoles
Key Engineering Controls and Work Practices
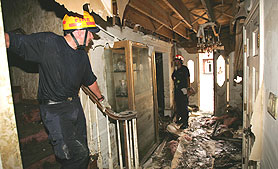
- Limit access/set up controlled access zones
- Use fall protection systems: guardrails, safety nets, or fall arrest systems
- Cover or guard holes and openings as soon as they are created. Covers must support two times the weight (body, equipment, materials) that may be imposed
Additional Personal Protective Equipment
- Personal fall arrest system including harnesses, lanyards, lifelines, connectors, anchorages, and anchor points (as needed)
Key Engineering Controls and Work Practices
- Confined spaces have limited means of entry or exit, are large enough to bodily enter, and may contain physical (e.g., mechanical, electrical, hydraulic, pneumatic energy; engulfment hazards; inwardly converging surfaces) or atmospheric hazards (e.g., atmospheres that are oxygen-deficient or oxygen-enriched, contain or may contain flammable gas, vapor or mist, airborne combustible dust, toxic substances, or any other atmosphere that is immediately dangerous to life or health). Examples include storage tanks, process vessels, bins, boilers, vaults, ventilation or exhaust ducts, sewers, tunnels, pipelines, and pits more than 4 feet in depth
- Hurricane-related events might introduce hazards or potential hazards into confined spaces. For example, a space might have a potential to contain a hazardous atmosphere due to the presence of decomposing organic matter, to the use of hazardous chemicals in the space, or to the performance of operations in the space, such as welding, cutting, or burning, that may create a hazardous atmosphere. Additional precautions must be taken to make the space safe for entry
- Evaluate the need for entry (i.e., placing any body part into the space)
- If entry is required, see Entry into Confined Spaces activity sheet
Key Engineering Controls and Work Practices
- Stay upwind of or away from dust-generating activities, and in particular those involving crystalline silica-containing materials like concrete, brick, tile, drywall, mortar, sand, or stone. When inhaled, the fine crystalline silica particles contained in the dust can become lodged deep in the lung, which can lead to silicosis and other respiratory illnesses
- Use water spray or mist to suppress dust generation, especially during operations that may create a lot of dust, such as cutting or sawing silica-containing materials, jack hammering, impact drilling, using heavy equipment, and demolishing structures
- Avoid using compressed air for cleaning surfaces
- Sample worker exposures to silica during dust-generating activities
- Limit contact or disturbance of surfaces containing visible mold growth
Additional Personal Protective Equipment
- At a minimum, use respirators with N, R, or P95 filters for work with crystalline silica-containing materials (e.g., concrete, brick, tile, mortar). The use of N, R, or P100 filters may provide additional protection. Higher levels of respiratory protection may be needed for some operations (e.g., cutting concrete, sandblasting, mixing concrete)
- N, R, or P95 respirators may be used for nuisance dusts (e.g., dried mud, dirt, or silt) and mold (except mold remediation). Filters with a charcoal layer may be used for odors
Key Engineering Controls and Work Practices
- Place generators, compressors, and other noisy equipment at a distance or behind a barrier when possible
Additional Personal Protective Equipment
- Hearing protection when working around potential noise sources and when noise levels exceed 90 dBA. A useful "rule of thumb"—if you cannot hold a conversation in a normal speaking voice with a person who is standing at arms length (approximately 3 feet), the noise level may exceed 90 dBA
Key Engineering Controls and Work Practices
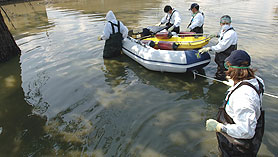
- Reduce the exposure to splash or aerosolized liquid hazards by limiting the number of people in the area and having those in the area stay upwind of water discharge areas
- Ensure that good hygiene, especially hand washing, is practiced before eating, drinking, and smoking. If clean water is not available, use an alternative such as hand sanitizer or sanitizing wipes
- Ensure that cuts and bruises are protected from contact with contaminated water
- Clean areas of the body that come in contact with contaminated water with soap and water, hand sanitizer, or sanitizing wipes
- If divers are involved, ensure divers and their equipment are appropriately decontaminated (fresh water shower/rinse at minimum) upon completion of dive operations—see Diving and Diver-Support Operations activity sheet
Additional Personal Protective Equipment
- Goggles if routinely working near splashing floodwater
- N, R, or P95 respirators may be necessary for exposure to contaminated water that may become aerosolized
- Watertight boots with steel toe and insoles
- Waterproof gloves for contact with contaminated water
Key Engineering Controls and Work Practices
- Report any contact with blood or body fluids to your supervisor
- See general recommendations document
Key Engineering Controls and Work Practices
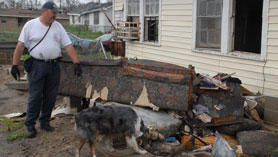
- If hazardous chemical containers are found or leaking materials are detected:
- Do not use spark-producing devices (e.g., engines, tools, electronic, and communications equipment) in the immediate area
- Take self-protective measures (i.e., move to a safe distance upwind) and contact hazardous material response personnel for evaluation/removal before continuing work in the area
Additional Personal Protective Equipment
- Evaluate the need to revise protective clothing, respirator, and glove selection
Select any of the following potential hazards that can be associated with this activity in order to access relevant recommendations in the general recommendations document:
Additional Medical Needs
- Follow medical guidance and precautions outlined in the general recommendations document
- Hepatitis B vaccinations must be made available to workers likely to contact blood and body fluids
Additional Training Needs
- Follow general site- and task-specific training guidelines as outlined in the general recommendations document
- Workers who may be exposed to blood or other potentially infected materials (OPIM) must be provided with initial and annual training on bloodborne pathogens and the employer's exposure control plan, in accordance with 29 CFR 1910.1030(g)
Related Activity Sheets
- Search and Rescue
- Diving and Diver-Support Operations
- Deep-Water Work/Boating Operations
- Entry into Confined Spaces
- Heavy Equipment and Powered Industrial Truck Use
- Work Zone Safety and Traffic Control within a Work Area
Other Resources and References
- 29 CFR 1910.1030, Bloodborne Pathogens. OSHA Standard.
- 29 CFR 1926.106, Working Over or Near Water. OSHA Standard.
- Handling of human remains from natural disasters. US Army Public Health Command (USAPHC), (July 18, 2011).
- Interim Health Recommendations for Workers who Handle Human Remains After a Disaster. Centers for Disease Control and Prevention (CDC).
- Traumatic Incident Stress: Information for Emergency Response Workers. US Department of Health and Human Services (DHHS), National Institute for Occupational Safety and Health (NIOSH) Publication No. 2002-107, (October 2001).
- Bloodborne Pathogens. OSHA Fact Sheets, (2011).
- Cleanup Hazards. OSHA Fact Sheet, (2005).
- General Decontamination. OSHA Fact Sheet, (2005).
- Respiratory Protection. OSHA Safety and Health Topics Page.
- NIOSH Respirator Selection Logic 2004. US Department of Health and Human Services (DHHS), National Institute for Occupational Safety and Health (NIOSH) Publication No. 2005-100, (October 2004).