Hurricane eMatrix
List of Activity Sheets » Operation-specific sheets
Heavy Equipment and Powered Industrial Truck Use
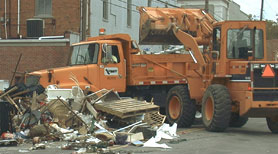
This picture shows actual disaster site work conditions and may not illustrate proper safety and health procedures.
Activity Description
- This activity sheet is for heavy equipment operators and their supervisors. It should be used in conjunction with the activity sheet for the activity in which the heavy equipment is being used (building demolition, utility restoration). Additionally, operators of cranes and aerial lifts should also refer to the precautions outlined in the activity sheets for those operations.
- For some operations or situations other activity sheets also apply; see related activity sheets below.
- As a result of Hurricanes Katrina and Rita (2005), water, sand, and sludge have impacted streets and buildings causing many to become structurally unsound and in need of demolition or repair.
- To help restore the affected communities, many pieces of heavy equipment (bulldozers, backhoes, front-end loaders, dump trucks, and powered industrial trucks (PITs), such as fork lifts) will be used.
- While operators should be familiar with the proper use of such equipment, this activity sheet is provided to advise operators of common controls for hazards likely to be encountered.
- Response and recovery workers conducting this operation may be employed by Federal, State, local, and private employers. Review How to Use This Matrix in the introduction for a discussion of how this information may apply to different workers.
About the Activity Sheet
This activity sheet does not provide an in-depth analysis of OSHA standards and regulations and cannot address all hazards. It does not increase or diminish any OSHA requirement or employer obligation under those requirements. It is intended as a guide and quick reference for employers and response and recovery workers. The Matrix captures major activities involved in hurricane response and recovery, highlights many of the hazards associated with them, and recommends beneficial work practices, personal protective equipment (PPE), and other exposure control methods. Employers must evaluate the specific hazards associated with the job/operation at the site where the work is being performed.
Employers are responsible for providing a safe and healthful workplace for their workers. OSHA's role is to assure the safety and health of America's workers by setting and enforcing standards; providing training, outreach, and education; establishing partnerships; and encouraging continual improvement in workplace safety and health.
The Hazard Exposure and Risk Assessment Matrix for Hurricane Response and Recovery Work provides a general overview of particular topics related to current OSHA standards. It does not alter or determine compliance responsibilities in OSHA standards or the Occupational Safety and Health Act of 1970, or the equivalent State Plan standards and requirements. Because interpretations and enforcement policy may change over time, you should consult current OSHA/State Plan administrative interpretations and decisions by the Occupational Safety and Health Review Commission and the courts for additional guidance on OSHA compliance requirements. Employers should modify their procedures as appropriate when additional, relevant information becomes available.
General Recommendations
Key Engineering Controls and Work Practices. See general recommendations document.
Personal Protective Equipment. The general PPE is recommended for all response/recovery tasks/operations; only the additional PPE that may be needed for a specific hazard is noted below.
General PPE includes:
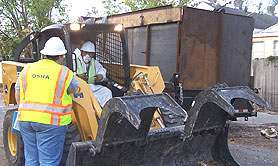
This picture shows actual disaster site work conditions and may not illustrate proper safety and health procedures.
- Hard hat for overhead impact or electrical hazards
- Eye protection with side shields
- Gloves chosen for job hazards expected (e.g., heavy-duty leather work gloves for handling debris with sharp edges and/or chemical protective gloves appropriate for chemicals potentially contacted)
- ANSI-approved protective footwear
- Respiratory protection as necessary—N, R, or P95, filtering facepieces may be used for nuisance dusts (e.g., dried mud, dirt and silt) and mold (except mold remediation). Filters with a charcoal layer may be used for odors
Recommendations Specific to Hazards Associated with Heavy Equipment and Powered Industrial Truck Use
Key Engineering Controls and Work Practices
- See Work Zone Safety and Traffic Control within a Work Area activity sheet
Additional Personal Protective Equipment
- ANSI/ISEA 107-2004 compliant high visibility safety apparel and headwear
Key Engineering Controls and Work Practices
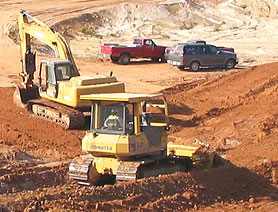
- All vehicles must have:
- A service brake system, an emergency brake system, and a parking brake system
- Working headlights, tail lights, and brake lights
- An audible warning device (horn)
- Intact windshield with working windshield wipers
- Ensure that all operators have been trained on the equipment they will use
- Check vehicles at the beginning of each shift to ensure that the parts, equipment, and accessories are in safe operating condition. Repair or replace any defective parts or equipment prior to use
- Do not operate vehicle in reverse with an obstructed rear view unless it has a reverse signal alarm capable of being heard above ambient noise levels or a signal observer indicates that it is safe to move
- Vehicles loaded from the top (e.g., dump trucks) must have cab shields or canopies to protect the operator while loading
- Ensure that vehicles used to transport workers have seats, with operable seat belts, firmly secured and adequate for the number of workers to be carried
- Equipment should have roll-over protection and protection from falling debris hazards as needed
- Prior to permitting construction equipment or vehicles onto an access roadway or grade, verify that the roadway or grade is constructed and maintained to safely accommodate the equipment and vehicles involved
- Do not modify the equipment's capacity or safety features without the manufacturer's written approval
- Where possible, do not allow debris collection work or other operations involving heavy equipment under overhead lines
Key Engineering Controls and Work Practices
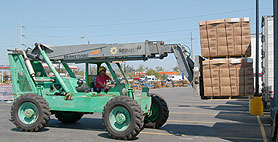
- Only handle loads within the rated capacity of the truck
- Use rough-terrain trucks where conditions warrant their use
- Carry loads low
- When necessary, travel in reverse so the driver/operator has a clear view of the path of travel
- Ascend or descend grades slowly; when ascending or descending grades in excess of 10 percent, loaded trucks should be driven with the load positioned upgrade
- Ensure that forklifts/PITs are not modified without the written approval of the manufacturer
- When left unattended, ensure that the load-engaging means are fully lowered, controls are neutralized, power is shut off, and brakes are set
- Maintain a safe distance from edges, including those of ramps and platforms
- Ensure that dockboards or bridgeplates are capable of withstanding the load imposed and that they are properly secured before the vehicle is slowly and carefully driven over it
- Only use safety platforms approved by the manufacturer when lifting personnel. Ensure that the lifting platform is firmly secured to the lifting carriage and/or forks before lifting personnel
Key Engineering Controls and Work Practices
- Do not overload vehicles
- Ensure that loads are balanced and are fully contained within the vehicle. Trim loads, where necessary, to ensure loads do not extend beyond the sides or top of the vehicle
- Cover and secure loads before moving the vehicle
Key Engineering Controls and Work Practices
- Stay upwind of or away from dust-generating activities, and in particular those involving crystalline silica-containing materials like concrete, brick, tile, drywall, mortar, sand, or stone. When inhaled, the fine crystalline silica particles contained in the dust can become lodged deep in the lung, which can lead to silicosis and other respiratory illnesses
- Use water spray or mist to suppress dust generation, especially during operations that may create a lot of dust, such as cutting or sawing silica-containing materials, jack hammering, impact drilling, using heavy equipment, and demolishing structures
- Avoid using compressed air for cleaning surfaces
- Sample worker exposures to silica during dust-generating activities
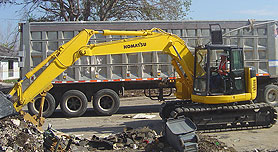
Additional Personal Protective Equipment
- At a minimum, use respirators with N, R, or P95 filters for work with crystalline silica-containing materials (e.g., concrete, brick, tile, mortar). The use of N, R, or P100 filters may provide additional protection. Higher levels of respiratory protection may be needed for some operations (e.g., cutting concrete, sandblasting, mixing concrete)
- N, R, or P95 respirators may be used for nuisance dusts (e.g., dried mud, dirt, or silt) and mold (except mold remediation). Filters with a charcoal layer may be used for odors
Key Engineering Controls and Work Practices
- Use heavy equipment with enclosed, temperature-controlled cabs, when available
- Place generators, compressors, and other noisy equipment at a distance or behind a barrier when possible
Additional Personal Protective Equipment
- Hearing protection when working around potential noise sources and when noise levels exceed 90 dBA. A useful "rule of thumb"—if you cannot hold a conversation in a normal speaking voice with a person who is standing at arms length (approximately 3 feet), the noise level may exceed 90 dBA
Key Engineering Controls and Work Practices
- Ensure that ignition sources are at least 25 feet away from fueling areas
- Prohibit smoking in fueling areas
- Ensure that vehicles are attended while being fueled
Key Engineering Controls and Work Practices
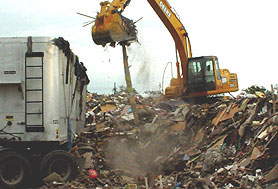
- If hazardous chemical containers are found or leaking materials are detected:
- Do not use spark-producing devices (e.g., engines, tools, electronic, and communications equipment) in the immediate area
- Take self-protective measures (i.e., move to a safe distance upwind) and contact hazardous material response personnel for evaluation/removal before continuing work in the area
Additional Personal Protective Equipment
- Evaluate the need to revise protective clothing, respirator, and glove selection
Select any of the following potential hazards that can be associated with this activity in order to access relevant recommendations in the general recommendations document:
- Environmental hazards
Additional Medical Needs
- Follow medical guidance and precautions outlined in the general recommendations document
Additional Training Needs
- Follow general site- and task-specific training guidelines as outlined in the general recommendations document
- OSHA heavy equipment-specific training requirements
- Personnel operating Powered Industrial Trucks (PITs) must be able to operate them safely and must demonstrate this competency by completing the training and evaluation requirements in 29 CFR 1910.178(l)
Related Activity Sheets
Other Resources and References
- 29 CFR 1926 Subpart O, Motor vehicles, mechanized equipment, and marine operations. OSHA.
- 29 CFR 1926.251, Rigging equipment for material handling. OSHA Standard.
- 29 CFR 1910.178, Powered industrial trucks. OSHA Standard.
- Powered Industrial Trucks. OSHA Safety and Health Topics Page.
- 29 CFR 1910.134, Respiratory protection. OSHA Standard.
- Respiratory Protection. OSHA Safety and Health Topics Page.
- NIOSH Respirator Selection Logic 2004. Centers for Disease Control and Prevention (CDC).
- Manual on Uniform Traffic Control Devices (MUTCD). U.S. Department of Transportation, Federal Highway Administration.