Hurricane eMatrix
List of Activity Sheets » Waste debris removal and reduction
Debris Collection
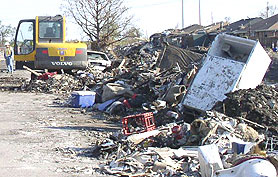
This picture shows actual disaster site work conditions and may not illustrate proper safety and health procedures.
Activity Description
- The hazards outlined in this activity sheet apply to debris collection and removal crews operating dredging, lifting, separating, sweeping, and hauling equipment. Building assessment, cleanup, repair, and demolition operations are covered in two additional activity sheets: "Assessment, Cleanup, and Repair of Structures," and " Building Demolition."
- For some operations or situations (e.g., heavy equipment use, work zone safety) other activity sheets also apply; see related activity sheets below.
- Disasters that result in property damage typically generate large quantities of debris that must be collected and transported for disposal. Debris must be removed from roads and other public areas to provide emergency access and in preparation for subsequent steps toward recovery.
- Debris collection and removal tasks include picking up, clearing, separating, and removing debris. Most of these tasks are typically performed using heavy equipment; however, some manual effort can be necessary at every stage.
- While most debris will be collected from land, after disasters that result in flooding (such as Hurricanes Katrina and Rita, in 2005), debris might need to be removed from water using cranes or dredges to promote drainage, fully restore maritime commerce, and advance recovery efforts.
- Special care is required when collecting and removing materials that are still damp, since wet materials will be heavier than they would have been if dry. Additionally, after a flood, wet materials might be contaminated with any substances that contaminated floodwaters.
- Response and recovery workers conducting this operation may be employed by Federal, State, local, and private employers. Review How to Use This Matrix in the introduction for a discussion of how this information may apply to different workers.
About the Activity Sheet
This activity sheet does not provide an in-depth analysis of OSHA standards and regulations and cannot address all hazards. It does not increase or diminish any OSHA requirement or employer obligation under those requirements. It is intended as a guide and quick reference for employers and response and recovery workers. The Matrix captures major activities involved in hurricane response and recovery, highlights many of the hazards associated with them, and recommends beneficial work practices, personal protective equipment (PPE), and other exposure control methods. Employers must evaluate the specific hazards associated with the job/operation at the site where the work is being performed.
Employers are responsible for providing a safe and healthful workplace for their workers. OSHA's role is to assure the safety and health of America's workers by setting and enforcing standards; providing training, outreach, and education; establishing partnerships; and encouraging continual improvement in workplace safety and health.
The Hazard Exposure and Risk Assessment Matrix for Hurricane Response and Recovery Work provides a general overview of particular topics related to current OSHA standards. It does not alter or determine compliance responsibilities in OSHA standards or the Occupational Safety and Health Act of 1970, or the equivalent State Plan standards and requirements. Because interpretations and enforcement policy may change over time, you should consult current OSHA/State Plan administrative interpretations and decisions by the Occupational Safety and Health Review Commission and the courts for additional guidance on OSHA compliance requirements. Employers should modify their procedures as appropriate when additional, relevant information becomes available.
Activity-Specific Sampling and Monitoring Information
- Work zone safety concerns were found at over half the work sites OSHA observed. Typically work areas were not adequately marked or separated with signs, cones or barricades.
- Other common concerns included PPE issues and workers at risk of being struck by machinery or falling debris. PPE was either not being worn when needed, or the PPE selected did not provide adequate protection.
- Response and recovery workers conducting this activity were among the groups most likely to be exposed to hazardous levels of noise, dust, and crystalline silica. Sample results for these hazards show that individuals collecting and removing debris may be exposed above allowable levels (i.e., OSHA's PEL), particularly when operating machinery and heavy equipment.
- For safety and health monitoring data and sample results, see the Summary of Activity Sampling Data and Safety and Health Monitoring Information.
General Recommendations
Key Engineering Controls and Work Practices. See general recommendations document.
Personal Protective Equipment. The general PPE is recommended for all response/recovery tasks/operations; only the additional PPE that may be needed for a specific hazard is noted below.
General PPE includes:
- Hard hat for overhead impact or electrical hazards
- Eye protection with side shields
- Gloves chosen for job hazards expected (e.g., heavy-duty leather work gloves for handling debris with sharp edges and/or chemical protective gloves appropriate for chemicals potentially contacted)
- ANSI-approved protective footwear
- Respiratory protection as necessary-N, R, or P95, filtering facepieces may be used for nuisance dusts (e.g., dried mud, dirt and silt) and mold (except mold remediation). Filters with a charcoal layer may be used for odors
Recommendations Specific to Hazards Associated with Debris Collection
Key Engineering Controls and Work Practices
- Limit clean up operations to one side of the road at a time
- See Work Zone Safety and Traffic Control within a Work Area activity sheet
Additional Personal Protective Equipment
-
ANSI/ISEA 107-2004 compliant high visibility safety apparel and headwear
Key Engineering Controls and Work Practices
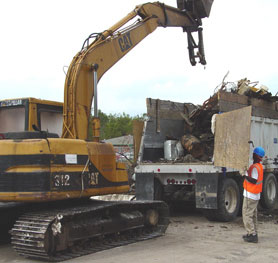
- Where possible, do not allow collection work to be done with heavy equipment under overhead lines
- Inspect debris piles before using equipment to pick them up and ensure that there are no obstructions (e.g., fire hydrants, water meters, etc) underneath that may pose a hazard
- See Heavy Equipment and Powered Industrial Truck Use activity sheet
- See Crane Use activity sheet
- See Use of Aerial Lifts activity sheet
Additional Personal Protective Equipment
- Hearing protection-see Noise hazard
- When working from an aerial lift, use a body harness that is properly attached (or body belt for tethering or restraint use only) for fall protection
Key Engineering Controls and Work Practices
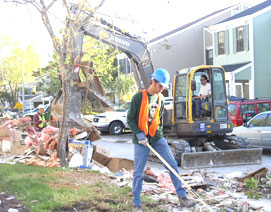
- Assume that electrical lines are energized until proven otherwise. Lines and other conductors may become reenergized without warning as utilities are evaluated and restored after a disaster
- Inspect the work area for downed conductors and do not go near, drive over, or otherwise come in contact with them
- Downed electrical conductors can energize other objects, including fences, water pipes, bushes, trees, and telephone/CATV/fiber optic cables
- Unless deenergized and visibly grounded, maintain proper distance from overhead electrical power lines (at least 10 feet) and/or provide insulating barriers
- Do not approach any gas leaks; if a gas leak is detected, secure spark-producing devices (e.g., engines, tools, electronic, and communications equipment) and evacuate the area until the leak is secured
- Contact utility company to assist in locating, marking, and shutting off/purging utility lines that may pose a hazard or may be impacted; ensure that lines have been purged as needed before beginning work
Key Engineering Controls and Work Practices
- Do not overload vehicle
- Ensure loads are balanced and are fully contained within the vehicle. Trim loads, where necessary, to ensure loads do not extend beyond the sides or top of the vehicle
- Cover and secure the load before moving vehicle
Key Engineering Controls and Work Practices
- Take frequent rest breaks when lifting heavy or water-laden objects
- See general recommendations document
Key Engineering Controls and Work Practices
- See Diving and Diver-Support Operations activity sheet
- See Deep-Water Work/Boating Operations activity sheet
- Do not allow workers to pass fore, aft, over, between, and around barge decks unless there is a walkway or another means for safe passage
- Provide fall protection if individuals must stand at an outboard or inboard edge without sufficient bulwark, rail, coaming, or other protection
Additional Personal Protective Equipment
- Personal floatation device-see Working on or over water
Key Engineering Controls and Work Practices
- Use grappling poles to retrieve floating objects; take caution around floating barrels and drums, which could release hazardous substances if punctured
- Use buoys to mark underwater locations of submerged materials
- Use additional protections, such as a life-saving skiff and a ring buoy, as appropriate
Additional Personal Protective Equipment
- Coast Guard-approved Type I or II personal floatation devices
- Watertight boots with steel toe and insole
Key Engineering Controls and Work Practices
- Before starting, check controls, chain tension, bolts, and handles to ensure proper function and adjustment
- Start the saw on the ground or on another firm support with the brake engaged
- Plan the cut; watch for objects under tension; use extreme care to bring objects safely to the ground. Plan where the object will fall; ensure that the fall area is free of hazards; avoid felling an object into other objects; and ensure that a clear retreat path is provided
- Look for nails, spikes, or other metal objects before cutting
- Clear away dirt, debris, small tree limbs, and rocks from the chain saw's path
- Keep hands on handles and maintain secure footing
- To control or prevent chain saw kickback, push-back, and pull-in, use saws that reduce these dangers through chain breaks, low kickback chains, etc.; do not use the saw's tip and keep any tip guards in place
- Do not cut directly overhead
- Shut off/release throttle prior to retreating
- Shut off or engage chain saw brake when carrying a saw more than 50 feet or crossing hazardous terrain
Additional Personal Protective Equipment
- Chaps
- Hearing protection-see Noise hazard
- Eye protection appropriate for additional impact hazard
- Fall protection, as necessary-see General Recommendations
Key Engineering Controls and Work Practices
- Use ground-fault circuit interrupters (GFCIs) or double insulated power tools, or implement an assured equipment grounding program
- Inspect power tool condition (including any cords) and verify operation of safety features before use
- Do not use equipment that is defective, such as equipment with inoperable safety switches, missing guards, frayed/cut cords etc.
- Ground power tools properly
- Avoid standing in wet areas when using portable power tools
Additional Personal Protective Equipment
- Hearing protection-see Noise hazard
- Hand protection for cut- and abrasion-control and vibration dampening
- Eye protection appropriate to the impact hazard
Key Engineering Controls and Work Practices
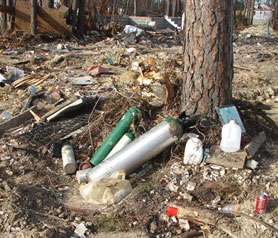
- If intact hazardous chemical containers are found with debris:
- Segregate them from the waste stream before continuing work in the area
- Store/stack containers securely so that they will not break or fall and so that they are clear of vehicular traffic and heavy equipment
- If broken or leaking hazardous chemical containers are found with debris:
- Take self-protective measures (i.e., move to a safe distance upwind) and contact hazardous material response personnel for evaluation/removal before continuing work in the area
- Do not use spark-producing devices (e.g., engines, tools, electronic, and communications equipment) in the immediate area
- Mark the location of the chemical container. Use a float/buoy for locations near or on water
Additional Personal Protective Equipment
-
Evaluate the need to revise protective clothing, respirator, and glove selection
Key Engineering Controls and Work Practices
- If material that may contain asbestos is found with debris, contact a supervisor/hazardous material personnel for evaluation/removal before continuing work in the area. Thermal system insulation (formed or spray-on) is the asbestos-containing materials (ACM) of greatest concern for response and recovery worker exposure. Other materials that may contain asbestos include: vinyl floor tile, home siding and shingles, transite (including cement piping), flame retardant materials (e.g., gloves, curtains), and roof flashing
- See general recommendations document
Additional Personal Protective Equipment
-
Based on the initial exposure assessment, select a respirator and protective clothing for visual inspection, sampling, and subsequent abatement work
Key Engineering Controls and Work Practices
- Remove flammable and combustible materials from the area
- Do not perform "hot work" such as welding, cutting, or burning in areas where flammable, combustible, corrosive, or toxic substances are being used, stored, or may otherwise be present
- Maintain a fire watch during all hot work until material has cooled
- Ensure fire extinguishers and extinguishing agents are available in the immediate area
- Provide natural, exhaust, or forced ventilation to control exposure to the metal fumes and other contaminants being generated (e.g., generator exhaust)
- Ensure that pipes and other vessels are purged of hazardous materials
- Identify building materials that will be welded, cut, or burned and that may contain lead, such as painted surfaces and pipes. Test materials and provide exposure controls identified in 29 CFR 1926.62 as necessary; see the lead hazard in the general recommendations document
Additional Personal Protective Equipment
- Gloves and protective clothing for the activity being performed
- At a minimum, filtered lenses and face-protection as appropriate for the activity being performed
- Respiratory protection based on anticipated exposure to metal fumes, including lead
Key Engineering Controls and Work Practices
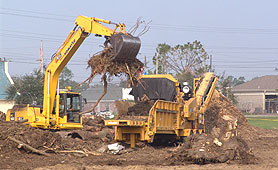
- Do not wear loose-fitting clothing
- Follow the manufacturer's guidelines and safety instructions
- Guard the feed and discharge ports
- Prevent opening of access doors and covers until the machinery has completely stopped
- Prevent trailer-mounted machinery from sliding or rolling by chocking trailer wheels
- Maintain a safe distance between the machine operations and other work/individuals. This area should be free of nonessential equipment, vehicles, and personnel
- Never reach into the equipment while it is operating
- Use a lockout system when servicing or maintaining (e.g., "unjamming") chipping equipment
Additional Personal Protective Equipment
-
Hearing protection-see Noise hazard
Key Engineering Controls and Work Practices
- Maintain barge decks and other work surfaces in a safe condition
- See general recommendations document
Key Engineering Controls and Work Practices
- Place generators, compressors, shaker-separators, and other noisy equipment at a distance or behind a barrier when possible
Additional Personal Protective Equipment
-
Hearing protection when working around potential noise sources and when noise levels exceed 90 dBA. A useful "rule of thumb"-if you cannot hold a conversation in a normal speaking voice with a person who is standing at arms length (approximately 3 feet), the noise level may exceed 90 dBA
Key Engineering Controls and Work Practices
- Stay upwind of or away from dust-generating activities, and in particular those involving crystalline silica-containing materials like concrete, brick, tile, drywall, mortar, sand, or stone. When inhaled, the fine crystalline silica particles contained in the dust can become lodged deep in the lung, which can lead to silicosis and other respiratory illnesses
- Use water spray or mist to suppress dust generation, especially during operations that may create a lot of dust, such as cutting or sawing silica-containing materials, jack hammering, impact drilling, using heavy equipment, and demolishing structures
- Avoid using compressed air for cleaning surfaces
- Sample worker exposures to silica during dust-generating activities
- Limit contact or disturbance of surfaces containing substantial visible mold growth
Additional Personal Protective Equipment
- At a minimum, use respirators with N, R, or P95 filters for work with crystalline silica-containing materials (e.g., concrete, brick, tile, mortar). The use of N, R, or P100 filters may provide additional protection. Higher levels of respiratory protection may be needed for some operations (e.g., cutting concrete, sandblasting, mixing concrete)
- N, R, or P95 respirators may be used for nuisance dusts (e.g., dried mud, dirt, or silt) and mold (except mold remediation). Filters with a charcoal layer may be used for odors
Key Engineering Controls and Work Practices
- Confined spaces have limited means of entry or exit, are large enough to bodily enter, and may contain physical (e.g., mechanical, electrical, hydraulic, pneumatic energy; engulfment hazards; inwardly converging surfaces) or atmospheric hazards (e.g., atmospheres that are oxygen-deficient or oxygen-enriched, contain or may contain flammable gas, vapor or mist, airborne combustible dust, toxic substances, or any other atmosphere that is immediately dangerous to life or health). Examples include storage tanks, process vessels, bins, boilers, vaults, ventilation or exhaust ducts, sewers, tunnels, pipelines, and pits more than 4 feet in depth
- Hurricane-related events might introduce hazards or potential hazards into confined spaces. For example, a space might have a potential to contain a hazardous atmosphere due to the presence of decomposing organic matter, to the use of hazardous chemicals in the space, or to the performance of operations in the space, such as welding, cutting, or burning, that may create a hazardous atmosphere. Additional precautions must be taken to make the space safe for entry
- Evaluate the need for entry (i.e., placing any body part into the space)
- If entry is required, see Entry into Confined Spaces activity sheet
Key Engineering Controls and Work Practices
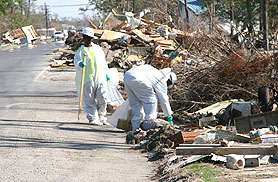
- Segregate and store incompatible chemicals separately. For example, store solvents and oxidizers (e.g., peroxides) separately, and acids and caustics separately
- Secure compressed gas cylinders and ensure that they are stored properly when not in use (regulators off and valve caps on when not in use; separate oxygen and fuel gas by 20 feet or using a non-combustible barrier (5 ft high, fire-resistant rating of at least ½ hour))
- Store chemicals in containers approved and designed for chemical storage and mark all storage locations
- Store and handle hazardous materials in areas with natural or forced ventilation; do not store or handle in low-lying areas
- Isolate, secure and identify storage areas
- Prohibit smoking near storage areas
- Keep ignition sources at least 25 feet away from storage areas
- Ensure that fire extinguishers and extinguishing agents are available in the immediate area
- Bond and ground containers before dispensing flammable liquids. Reference 29 CFR 1926.152(e)(2)
Additional Personal Protective Equipment
- Gloves made of material that will protect user from chemicals handled
- Face shield or goggles with indirect venting. If a face shield is selected, eye protection must be worn under the face shield
- Coveralls or apron resistant to chemicals being handled
- Disposable boot covers resistant to the chemicals being handled
- A respirator and cartridges specific for chemical, as necessary
Key Engineering Controls and Work Practices
- Reduce the exposure to splash or aerosolized liquid hazards by limiting the number of people in the area and having those in the area stay upwind of water discharge areas
- Ensure that good hygiene, especially hand washing, is practiced before eating, drinking, and smoking. If clean water is not available, use an alternative such as hand sanitizer or sanitizing wipes
- Ensure that cuts and bruises are protected from contact with contaminated water
- Clean areas of the body that come in contact with contaminated water with soap and water, hand sanitizer, or sanitizing wipes
- If divers are involved, ensure divers and their equipment are appropriately decontaminated (fresh water shower/rinse at minimum) upon completion of dive operations-see Diving and Diver-Support Operations activity sheet
Additional Personal Protective Equipment
- Goggles if routinely working near splashing floodwater
- N, R, or P95 respirators may be necessary for exposure to contaminated water that may become aerosolized
- Watertight boots with steel toe and insoles
- Waterproof gloves for contact with contaminated water
Key Engineering Controls and Work Practices
-
If found, contact public health/mortuary personnel for removal
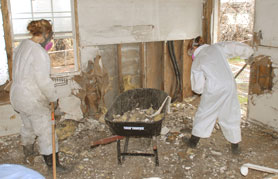
Select any of the following potential hazards that can be associated with this activity in order to access relevant recommendations in the general recommendations document:
Additional Medical Needs
-
Follow medical guidance and precautions outlined in the general recommendations document
Additional Training Needs
-
Follow general site- and task-specific training guidelines as outlined in the general recommendations document
Related Activity Sheets
- Building Demolition
- Assessment, Cleanup, and Repair of Structures
- Debris Reduction, Recycling, and Disposal
- Vehicle Removal and Salvage
- Sand/Sludge Removal
- Diving and Diver-Support Operations
- Deep-Water Work/Boating Operations
- Entry into Confined Spaces
- Heavy Equipment and Powered Industrial Truck Use
- Work Zone Safety and Traffic Control within a Work Area
- Crane Use
- Use of Aerial Lifts
Other Resources and References
- 29 CFR 1926.106, Working Over or Near Water. OSHA
- 29 CFR 1926.251, Rigging Equipment for Material Handling. OSHA.
- 29 CFR 1926.550, Cranes. OSHA.
- 29 CFR 1910.178, Powered Industrial Trucks. OSHA.
- 29 CFR 1910.134, Respiratory Protection. OSHA.
- 29 CFR 1910.1001, Asbestos in General Industry. OSHA.
- 29 CFR 1926.1101, Asbestos in Construction. OSHA.
- Cleanup Hazards. OSHA Fact Sheet, (2005).
- Storm, Flood and Hurricane Response. National Institute for Occupational Safety and Health (NIOSH) Workplace Topic.
- Respiratory Protection. OSHA Safety and Health Topics Page.
- NIOSH Respirator Selection Logic. Centers for Disease Control and Prevention, (2004).
- Working Safely with Chain Saws. OSHA Fact Sheet, (2005).
- Working Safely Around Downed Electrical Wires. OSHA Fact Sheet (Publication 3941), (2018).
- Hand Hygiene and Protective Gloves in Hurricane-Affected Areas. OSHA Fact Sheet, (2005).
- Manual on Uniform Traffic Control Devices (MUTCD). U.S. Department of Transportation, Federal Highway Administration.