Scaffolding eTool
Scaffolding » Planking
According to Federal labor statistics, more scaffold incidents are attributed to planking giving way than any other cause. Additionally, almost 25% of workers receive no safety training for erecting scaffolds and installing work platforms.
The planking portion of OSHA's Scaffolding eTool is intended to address the need for specific and accurate information about arguably the single most critical scaffolding component: The lumber from which platforms are made.
Scaffold-grade lumber is meant to withstand forces not imposed on ordinary, construction-grade wood (which is only two-thirds the capacity of scaffold-grade). Using construction-grade lumber on a scaffold platform not only violates OSHA standards, but is also an unsafe practice and an invitation to a deadly incident.
The quality of scaffold-grade lumber is measured by:
- The number of rings per inch (6 or more).
- The slope of the grain (1 inch to the side for every 16 inches along the length of the board for Douglas Fir, 1/14 for Southern Pine).
- The number of defects, such as knots and notches.
Solid sawn wood used for scaffold planks should follow the grading rules of a recognized lumber grading association or an independent lumber inspection agency, and be identified by that agency or association's grade stamp (see examples below).
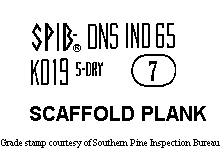
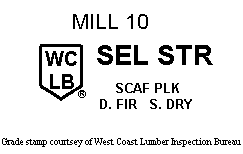
Such organizations and their grading rules must be certified by the Board of Review of the American Lumber Standard Committee, per the U.S. Department of Commerce.
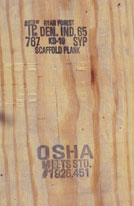
OSHA does not inspect lumber; therefore, any scaffold planking stamped "OSHA Approved" is, at best, misleading, and should not be assumed to meet the standard on the basis of that stamp alone. An inspection agency can claim that its product meets OSHA requirements. (Figure 3) However, because a scaffold plank may still be in service long after the grade stamp on it has faded, workers should pay attention to the quality and condition of the planking, whether it bears a stamp or not.
As wood ages and reacts to usage, it will begin to show checks, splits and notches. These will vary in degree depending on the loads a plank has carried, the weather it has been exposed to, how long it has been in use, etc.
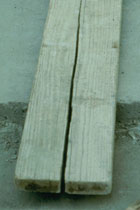
Planks with splits (cracks that go clear through the wood) more than a few inches in length should not remain in service, as they may no longer maintain the necessary load-bearing capacity.
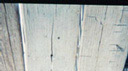
Planks with checks (cracks that are on the surface only and do not go clear through the wood) should be watched, as the checks may develop into splits over time.
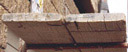
Notches (small checks on the ends of a plank) should also be watched over time, as they can lengthen and deepen until they become splits.
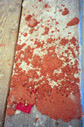
Scaffold planks that have accumulated layers of paint, plaster, etc. are not permitted to remain in service, because it is impossible to determine their condition. Dangerous splits may be hidden underneath these coatings. [29 CFR 1926.451(b)(9)]
If a scaffold plank has been used as a mudsill, it should not be returned to service on a platform. Moisture from standing water, as well as point-loading from the scaffold legs, may have weakened it, making it unable to bear the weight that will be placed on it.
The span of a scaffold plank is the distance it runs between supports. The longer the span, the more deflection (bend) it will have, and therefore, the less its load-bearing capacity will be. For 2 x 10 (nominal) or 2 x 9 (rough) solid sawn wood planks, allowable spans for a given load are shown in the table below:
Maximum Intended Load |
Maximum Permissible Span Using Full Thickness Lumber |
Maximum Permissible Span Using Nominal Thickness Lumber |
---|---|---|
25 lbs./square foot |
10 feet |
8 feet |
50 lbs./square foot |
8 feet |
6 feet |
75 lbs./square foot |
6 feet |
-- |
Because nominal thickness lumber is not cut to its exact dimensions, nominal 2 x 10 is really more like 1½ x 9¼. As a result, it does not have the same load-bearing capacity of full thickness lumber.
For fabricated planks and platforms, maximum spans are to be recommended by the manufacturer based on the following table:
Rated Load Capacity |
Intended Load |
---|---|
Light-duty |
25 lbs. per square foot applied uniformly over the entire span area |
Medium-duty |
50 lbs. per square foot applied uniformly over the entire span area |
Heavy-duty |
75 lbs. per square foot applied uniformly over the entire span area |
One-person |
250 lbs. placed at the center of the span (total 250 lbs.) |
Two-person |
250 lbs. placed 18 inches to the left and right of the center of the span (total 500 lbs.) |
Three-person |
250 lbs. placed at the center of the span and 250 lbs. placed 18 inches to the left and right of the center of the span (total 750 lbs.) |
To assure that scaffold planking remains within its safe load-bearing capacity, it may not be allowed to deflect more than 1/60th of its span between supports. [29 CFR 1926.451(f)(16)] The table below shows how little deflection that is.
Span of Plank Between Supports |
Calculation |
Maximum Permissible Deflection |
---|---|---|
10 feet |
120 inches/60 inches |
2 inches |
7 feet |
84 inches/60 inches |
1⅜ inches |
5 feet |
60 inches/60 inches |
1 inch |
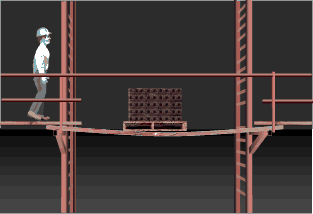
Figure 8. Animation. Illustrates the danger posed to workers by planking that has been overloaded.
Workers should be aware of deflection because it can indicate when a platform is overloaded, and a competent person should not allow employees to occupy a platform that exceeds the 1/60th ratio. The animation below illustrates the danger posed to workers by planking that has been overloaded.