Hurricane eMatrix
List of Activity Sheets » Waste debris removal and reduction
Tree Trimming
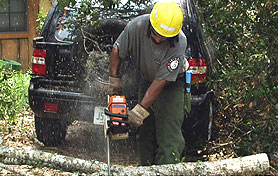
This picture shows actual disaster site work conditions and may not illustrate proper safety and health procedures.
Activity Description
- The hazards outlined in this activity sheet apply to response and recovery workers who are experienced in the use of chain saws and involved in trimming and removing trees using power tools and heavy equipment.
- For some operations or situations (e.g., work zone safety, use of aerial lifts, heavy equipment use) other activity sheets also apply; see related activity sheets below.
- High winds and floodwaters caused extensive damage to trees during Hurricanes Katrina and Rita (2005). Trees and tree limbs blocked roads, fell onto structures, and became tangled in utility lines. Trees must be trimmed or removed when they impede response and recovery efforts, present a safety hazard, or sustained damage that will create a safety hazard in the future. This activity will be necessary for any natural disaster in which damaged trees become a safety hazard.
- Response and recovery workers involved in tree trimming work at heights, gain access by using aerial lifts or by climbing. They then typically use power tools (usually chain saws) to cut branches, limbs, and trunks as necessary. They may also use chippers and related equipment as a preliminary step toward debris reduction. The same workers might be involved in tree felling as necessary to create access and ensure public safety.
- Response and recovery workers conducting this operation may be employed by Federal, State, local, and private employers. Review How to Use This Matrix in the introduction for a discussion of how this information may apply to different workers.
About the Activity Sheet
This activity sheet does not provide an in-depth analysis of OSHA standards and regulations and cannot address all hazards. It does not increase or diminish any OSHA requirement or employer obligation under those requirements. It is intended as a guide and quick reference for employers and response and recovery workers. The Matrix captures major activities involved in hurricane response and recovery, highlights many of the hazards associated with them, and recommends beneficial work practices, personal protective equipment (PPE), and other exposure control methods. Employers must evaluate the specific hazards associated with the job/operation at the site where the work is being performed.
Employers are responsible for providing a safe and healthful workplace for their workers. OSHA's role is to assure the safety and health of America's workers by setting and enforcing standards; providing training, outreach, and education; establishing partnerships; and encouraging continual improvement in workplace safety and health.
The Hazard Exposure and Risk Assessment Matrix for Hurricane Response and Recovery Work provides a general overview of particular topics related to current OSHA standards. It does not alter or determine compliance responsibilities in OSHA standards or the Occupational Safety and Health Act of 1970, or the equivalent State Plan standards and requirements. Because interpretations and enforcement policy may change over time, you should consult current OSHA/State Plan administrative interpretations and decisions by the Occupational Safety and Health Review Commission and the courts for additional guidance on OSHA compliance requirements. Employers should modify their procedures as appropriate when additional, relevant information becomes available.
Activity-Specific Sampling and Monitoring Information
- PPE issues were found at over half the work sites OSHA observed. PPE, including face, head, body, hand, or hearing protection, was either not being worn when needed, or the PPE selected did not provide adequate protection.
- When aerial lifts were used, fall protection was not used or was not used correctly at 75% of the work sites observed.
- Other common concerns included inadequate work zone safety controls, improper use of chainsaws.
- Response and recovery workers operating chain saws, chippers, and heavy equipment are among the groups most likely to experience hazardous noise exposure. Sample results show that individuals using this tree trimming equipment may be exposed to noise above allowable levels (i.e., OSHA's PEL).
- For safety and health monitoring data and sample results, see the Summary of Activity Sampling Data and Safety and Health Monitoring Information.
General Recommendations
Key Engineering Controls and Work Practices. See general recommendations document.
Personal Protective Equipment. The general PPE is recommended for all response/recovery tasks/operations; only the additional PPE that may be needed for a specific hazard is noted below.
General PPE includes:
- Hard hat for overhead impact or electrical hazards
- Eye protection with side shields
- Gloves chosen for job hazards expected (e.g., heavy-duty leather work gloves for handling debris with sharp edges and/or chemical protective gloves appropriate for chemicals potentially contacted)
- ANSI-approved protective footwear
- Respiratory protection as necessary—N, R, or P95, filtering facepieces may be used for nuisance dusts (e.g., dried mud, dirt and silt) and mold (except mold remediation). Filters with a charcoal layer may be used for odors
Recommendations Specific to Hazards Associated with Tree Trimming
Key Engineering Controls and Work Practices
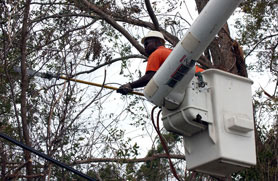
- Limit access/set up controlled access zones
- Inspect trees and limbs for structural weakness before climbing or cutting
- Use safe climbing procedures such as breaking or cutting off dead limbs while climbing, placing hands and feet on separate limbs, and limiting shinning distance to 15 feet
- Use safe work procedures to prevent inadvertent cutting of climbing ropes, lanyards, and safety belts or straps
Additional Personal Protective Equipment
-
Personal fall arrest system including harnesses, lanyards, lifelines, connectors, anchorages, and anchor points (as needed)
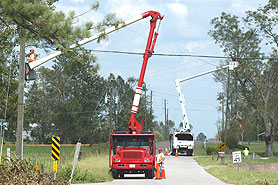
Key Engineering Controls and Work Practices
- See Use of Aerial Lifts activity sheet
- See Heavy Equipment andPowered Industrial Truck Use activity sheet
Additional Personal Protective Equipment
- Hearing protection—see Noise hazard
- When working from an aerial lift, use a body harness that is properly attached (or body belt for tethering or restraint use only) for fall protection
Key Engineering Controls and Work Practices
- See Work Zone Safety and Traffic Control within a Work Area activity sheet
Additional Personal Protective Equipment
-
ANSI/ISEA 107-2004 compliant high visibility safety apparel and headwear
Key Engineering Controls and Work Practices
- Ensure that tree trimming operations to clear electrical lines are performed only by qualified line-clearance tree trimmers. A qualified line-clearance tree trimmer is knowledgeable in the construction and operation of electric power generation, transmission, or distribution equipment involved, along with the associated hazards
- Closely inspect trees for electrical conductors passing through or within reaching distance of workers before beginning tree work
- Consider all electrical power conductors to be energized and not to be directly or indirectly (e.g., through tools, branches, or other equipment) touched
- Assume that electrical lines are energized until proven otherwise. Lines and other conductors may become re-energized without warning as utilities are evaluated and restored after a disaster
- Inspect the work area for downed conductors and do not go near, drive over, or otherwise come in contact with them
- Downed electrical conductors can energize other objects, including fences, water pipes, bushes, trees, and telephone/CATV/fiber optic cables
- Unless deenergized and visibly grounded, maintain proper distance from overhead electrical power lines (at least 10 feet) and/or provide insulating barriers
- Do not approach any gas leaks; if a gas leak is detected, secure spark-producing devices (e.g., engines, tools, electronic, and communications equipment) and evacuate the area until the leak is secured
- Contact utility company to assist in locating, marking, and shutting off/purging utility lines that may pose a hazard or may be impacted; ensure that lines have been purged as needed before beginning work
Additional Personal Protective Equipment
- Hard hat with appropriate ANSI rating for exposure to high voltage, as needed
- Appropriately rated and tested electrician's gloves, as needed
- Non-conductive clothing, as needed
Key Engineering Controls and Work Practices
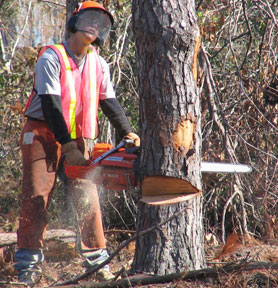
- Before starting, check controls, chain tension, bolts, and handles to ensure proper function and adjustment
- Start the saw on the ground or on another firm support with the brake engaged
- Plan the cut; watch for objects under tension; use extreme care to bring objects safely to the ground. Plan where the object will fall; ensure that the fall area is free of hazards; avoid felling an object into other objects; and ensure that a clear retreat path is provided
- Look for nails, spikes, or other metal objects before cutting
- Clear away dirt, debris, small tree limbs, and rocks from the chain saw's path
- Keep hands on handles and maintain secure footing
- To control or prevent chain saw kickback, push-back, and pull-in, use saws that reduce these dangers through chain breaks, low kickback chains, etc.; do not use the saw's tip and keep any tip guards in place
- Do not cut directly overhead
- Shut off/release throttle prior to retreating
- Shut off or engage chain saw brake when carrying a saw more than 50 feet or crossing hazardous terrain
Additional Personal Protective Equipment
- Chaps
- Hearing protection—see Noise hazard
- Eye protection appropriate for additional impact hazard
- Fall protection, as necessary—see Fall hazard
Key Engineering Controls and Work Practices
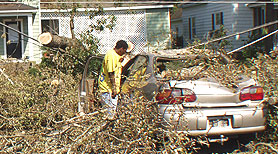
- Limit access/set up controlled access zones
- During trimming, keep non-essential response and recovery workers at least 20 feet beyond expected drop zones during trimming
- During felling, designate work area so that trees cannot fall into an adjacent occupied work area. Adjacent occupied work areas should be at least two tree lengths from the tree being felled (allow more if it is reasonably foreseeable that the tree might roll or slide)
- Always plan a clear path of retreat before cutting
- Determine the felling direction and how to deal with forward, back, and/or side lean
- Determine the proper hinge size to safely guide the tree in its fall
- If tree is broken and under pressure, make sure you know which way the pressure is going. If not sure, make small cuts to release some of the pressure before cutting up the section
- Be careful of young trees that other trees have fallen against; they act like spring poles and can propel back
- If you have to cut a dead tree, be careful: the top could break off
- If possible, avoid felling trees into other trees or objects; branches and objects may get thrown back toward the tree cutter
Key Engineering Controls and Work Practices
- Do not wear loose-fitting clothing
- Follow the manufacturer's guidelines and safety instructions
- Guard the feed and discharge ports
- Prevent opening of access doors and covers until the drum or disc has completely stopped
- Prevent detached chippers from sliding or rolling by chocking the trailer wheels
- Maintain a safe distance (2 to 3 log lengths) between the chipper operator and other work/individuals
- Never reach into the equipment while it is operating
- Use a lockout system when servicing or maintaining (e.g., "unjamming") chipping equipment
Additional Personal Protective Equipment
- Eye and face protection appropriate for additional impact hazard
- Hand protection for cut- and abrasion-control
- Hearing protection—see Noise hazard
Key Engineering Controls and Work Practices
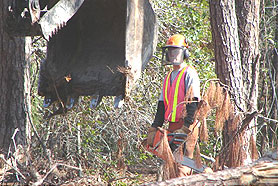
- Use ground-fault circuit interrupters (GFCIs) or double insulated power tools, or implement an assured equipment grounding program
- Inspect power tool condition (including any cords) and verify operation of safety features before use
- Do not use equipment that is defective, such as equipment with inoperable safety switches, missing guards, frayed/cut cords etc.
- Ground power tools properly
- Avoid standing in wet areas when using portable power tools
Additional Personal Protective Equipment
- Hearing protection—see Noise hazard
- Hand protection for cut- and abrasion-control and vibration dampening
- Eye protection appropriate for additional impact hazard
Key Engineering Controls and Work Practices
- Place chipper, generators, and other noisy equipment at a distance or behind a barrier when possible
Additional Personal Protective Equipment
- Hearing protection when working around potential noise sources and when noise levels exceed 90 dBA. A useful "rule of thumb"—if you cannot hold a conversation in a normal speaking voice with a person who is standing at arms length (approximately 3 feet), the noise level may exceed 90 dBA
Key Engineering Controls and Work Practices
- Inspect ladders for cracked, broken, or defective parts before use
- Do not exceed the load rating of ladders—remember that load ratings include people, tools, and equipment
- Set up ladders on stable surfaces
- Set extension or straight ladders at a 75 degree angle from the ground (1/4 foot back for every foot of rise) and provide 3 feet above an upper landing surface to ease climbing onto/descending from height
- Use non-conductive ladders (e.g., fiberglass) and exercise extreme caution when working near power lines
- Secure ladders that can be displaced by work activities; consider barricades at the base to keep traffic away
Key Engineering Controls and Work Practices
- See general recommendations document
- Train response and recovery workers on hazardous plant recognition
- Keep rubbing alcohol accessible because it can be used to remove oily resin
Additional Personal Protective Equipment
- Gloves, long pants, and long-sleeved shirts when contact with poisonous plants possible
- Use a barrier cream formulated to protect against poison ivy/oak
Key Engineering Controls and Work Practices
- If hazardous chemical containers are found or leaking materials are detected:
- Do not use spark-producing devices (e.g., engines, tools, electronic, and communications equipment) in the immediate area
- Take self-protective measures (i.e., move to a safe distance upwind) and contact hazardous material response personnel for evaluation/removal before continuing work in the area
Additional Personal Protective Equipment
- Evaluate the need to revise protective clothing, respirator, and glove selection
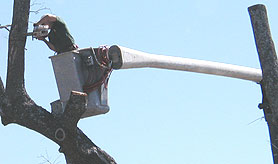
Select any of the following potential hazards that can be associated with this activity in order to access relevant recommendations in the general recommendations document:
Additional Medical Needs
- Follow medical guidance and precautions outlined in the general recommendations document
Additional Training Needs
- Follow general site- and task-specific training guidelines as outlined in the general recommendations document
- Train workers on the fall protection systems that they will use
- Train workers who will perform tree trimming in the skills needed for their job. Use 29 CFR 1910.266(i) – Logging as a reference guide for tree trimming operations
- Ensure that workers who will be trimming near electrical lines are also trained in electrical safety as required by 29 CFR 1910.269 - Electric power generation, transmission, and distribution
Related Activity Sheets
- Debris Collection
- Debris Reduction, Recycling, and Disposal
- Heavy Equipment and Powered Industrial Truck Use
- Work Zone Safety and Traffic Control within a Work Area
- Use of Aerial Lifts
Other Resources and References
- 29 CFR 1926.266, Logging Operations. OSHA.
- 29 CFR 1910.269, Electric Power Generation, Transmission, and Distribution. OSHA.
- 29 CFR 1926.251, Rigging Equipment for Material Handling. OSHA.
- 29 CFR 1926.453, Aerial Lifts. OSHA.
- 29 CFR 1910.178, Powered Industrial Trucks. OSHA.
- 29 CFR 1926 Subpart I, Hand and power tools. OSHA.
- 29 CFR 1926 Subpart X, Ladders. OSHA.
- Tree Trimming Safety. OSHA Fact Sheet, (2006).
- Preventing Falls and Electrocutions During Tree Trimming. National Institute for Occupational Safety and Health (NIOSH), (1992).
- Chipper Machine Safety. OSHA Quick Card, (2007).
- Working Safely with Chain Saws. OSHA Fact Sheet, (2005).
- Using Aerial Lifts. OSHA Fact Sheet, (2005).
- Working Safely with Electricity. OSHA Fact Sheet (Publication 3942), (2018).
- Working Safely Around Downed Electrical Wires. OSHA Fact Sheet (Publication 3941), (2018).
- Portable Ladder Safety Tips. OSHA Quick Card, (2005).