Hurricane eMatrix
Hurricane eMatrix » Part I: Summary of Safety and Health Intervention Information from OSHA Situation Reports
Background
During the response and recovery phases to Hurricanes Katrina, Rita and Wilma in 2005 and 2006, OSHA monitored work activities, visited staging areas and work sites, and investigated eighteen work-related deaths. OSHA's workplace monitoring activities were captured and reported in internal Situation Reports (SitReps). The information below summarizes the data contained in the SitReps received from Region 4, including Florida, Alabama, and Mississippi, from August 31, 2005 to March 10, 2006. This report summarizes the 129 SitReps, which contained approximately 4,000 entries that described workers exposed to hazardous situations. The entries describe over 9,500 interventions made by OSHA. Many entries describe multiple interventions. Interventions ranged from providing literature and guidance to individual workers and employers, to having employers remove workers from imminently dangerous situations.
Limitations and Disclaimer
The Matrix does not provide an in-depth analysis of OSHA standards and regulations and cannot address all hazards. It does not increase or diminish any OSHA requirement or employer obligation under those requirements. It is intended as a guide and quick reference for employers and response and recovery workers. The Matrix captures major activities involved in hurricane response and recovery, highlights many of the hazards associated with them, and recommends "best practices." Employers must evaluate the specific hazards associated with the job/operation at the site where the work is being performed.
Employers are responsible for providing a safe and healthful workplace for their workers. OSHA's role is to assure the safety and health of America's workers by setting and enforcing standards; providing training, outreach, and education; establishing partnerships; and encouraging continual improvement in workplace safety and health.
The Hazard Exposure and Risk Assessment Matrix for Hurricane Response and Recovery Work provides a general overview of particular topics related to current OSHA standards. It does not alter or determine compliance responsibilities in OSHA standards or the Occupational Safety and Health Act of 1970, or the equivalent State Plan standards and requirements. Because interpretations and enforcement policy may change over time, you should consult current OSHA/State Plan administrative interpretations and decisions by the Occupational Safety and Health Review Commission and the courts for additional guidance on OSHA compliance requirements. Employers should modify their procedures as appropriate when additional, relevant information becomes available.
Activities Most Frequently Referenced in SitReps
Figure I shows the breakdown of the most commonly noted activities described in these SitReps.
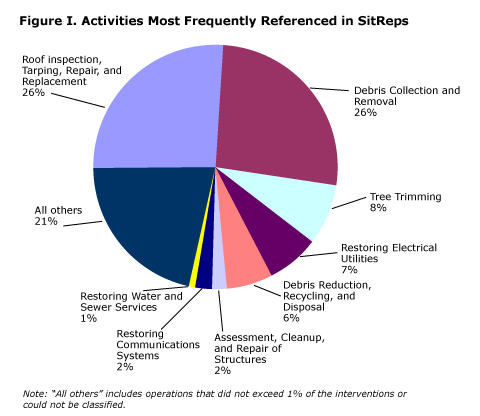
The activities where interventions were conducted most frequently include:
- Roof Inspection, Tarping, and Repair (26%)
- Debris Collection and Removal (26%)
- Tree Trimming (8%)
- Restoring Electrical Utilities (7%)
- Debris Reduction, Recycling, and Disposal (6%)
- Assessment, Cleanup, and Repair of Structures (2%)
- Restoring Communications Systems (2%)
- Restoring Water and Sewer Services (1%)
The following sections organize the information about work site hazards captured in the SitReps submitted by Region 4 (Florida, Alabama, and Mississippi) between August 31, 2005 and March 10, 2006. The information is organized and presented in two ways:
- Hazards most frequently identified in the SitReps for all of the interventions documented.
- Hazards most frequently identified for the each of the eight activities listed above.
The activities and hazards that OSHA documented in the SitReps evaluated generally were not unique to hurricane response and recovery. In many cases, these activities routinely occur in other industrial and occupational settings and the hazards are well recognized by the employers and workers that conduct them. Nevertheless, the information summarized below suggests that many employers either did not properly evaluate hazards and implement controls, or did not require workers to use them. For example, OSHA observed tree clearance crews working in aerial lifts without fall protection. Aerial lifts are used at many work sites to trim trees and fall protection is a required exposure control. OSHA also observed that personal protective equipment (PPE) use was lacking for many recognized hazards. For example, hearing protection was not used during jobs where noise exposures are common such as heavy equipment operations.
The information summarized below appears to indicate that many employers may not implement recognized work practices or require the use of PPE routinely at work sites. Conditions after a hurricane can create additional risk for many reasons including the loss of basic infrastructure (e.g., power, roads, water, food/hotel service), the large amount of debris in roads and work areas, the large number of response and recovery workers who are not familiar with the area, and the volume and wide range of operations conducted at close range to one another. The use of well-established safety and health work practices and exposure controls is even more critical under these conditions.
OSHA includes recommended exposure controls, including work practices and PPE, for response and recovery operations throughout the Matrix. These exposure controls appear in the General Recommendations document as well as in the individual activity sheets for specific jobs and operations. Employers can include this information in existing and future Job Hazard Analyses and standard operating practices for the activities they perform routinely and those they anticipate performing during future recovery efforts. Employers and response and recovery workers can use this information to improve operations and prepare for future recovery operations, by implementing the recommended work practices, selecting and using recommended PPE, and providing training on how to conduct current operations safely.
Summary of Hazards Most Frequently Observed
This section discusses the hazards most frequently identified during hurricane-related response and recovery activities in Florida, Alabama, and Mississippi, based on keywords identified in SitRep entries. Because OSHA frequently observed work locations where multiple, related hazards were present, there may be significant overlap in the data for the individual hazards identified. For example, in a category where 50% of the entries mention fall hazards and 40% of the entries mention scaffolding, the percentages reported for each hazard overlap because the hazards are related. In addition, only data from Region 4 was analyzed, so the data provided below do not represent OSHA's experience from the entire response and recovery effort. In spite of these two limitations, the data provide a useful catalog of the most common hazards observed during the initial six months of hurricane disaster response and recovery operations. It can be used by employers and response and recovery workers to plan for future disaster response and recovery.
Table I-1 shows the top five hazards observed. As noted above, these hazards are not unique to disaster response and recovery. They are frequently associated with the activities during which they were observed (e.g., work zone safety and tree trimming in a right-of-way near a road). While each hazard is briefly described below, the overall message is that employers should conduct job hazard analyses (JHAs) that address both safety and health hazards, ensure that workers understand the hazards associated with the job, provide the necessary equipment, including PPE, to perform the job safely, and ensure that workers use the controls provided. (OSHA's Website provides additional assistance on developing JHAs.)
Table I-1: Summary of Top Hazards Observed in All Response and Recovery Activities
Description of Hazard or Observation | Approximate Percentages of Sites or Visits |
---|---|
Work zone safety concerns | 40% |
PPE was missing or used improperly | 35% |
Potential fall hazard/inadequate fall protection | 35% |
Risk of being struck-by object, equipment, or vehicle | 20% |
Improper use of aerial lifts | 15% |
- Work zone safety concerns were highest at 40%: Many entries involved tree trimming or electrical line repair on or near roads. The entries often noted inadequate cones and other barriers at a work zone, improper use or lack of traffic control signs (e.g., directional arrows, flaggers with stop/slow signs), workers standing in areas where they were exposed to oncoming traffic, and lack of use of ANSI-approved high-visibility safety apparel such as vests and gloves. Employers need to ensure that workers establish work zones and traffic controls where multiple pieces of heavy equipment, vehicles, and workers are in close proximity. Work zones must be well marked with barriers, cones, signs, and flaggers to provide plenty of warning and appropriate direction to approaching vehicles.
- Improper use or lack of personal protective equipment (PPE) (35%):
- Roughly 65% of the PPE entries reference a lack of face and head protection, or the improper use of PPE. Entries indicated that individuals were not using goggles, hard hats, or face shields when those types of PPE were necessary.
- Other types of PPE commonly mentioned include hand protection (e.g., use of reinforced gloves during the handling of debris or insulating gloves when working around electrical lines), hearing protection, and body protection (e.g., chaps to protect the worker's legs when operating a chainsaw or ANSI-approved high-visibility vests in high traffic areas).
- Approximately 15% of all the entries discussed fall protection use while operating aerial lifts. See next bullet.
Employers should ensure that the job hazard assessment (JHA) for each response and recovery task identifies the PPE needed for worker protection. Employers must provide properly fitting PPE to workers, train them how to use it, and ensure they use it when performing the task. Employers should use the information in this document and the recommendations in the individual activity sheets to identify job hazards that may require PPE use and to select appropriate PPE for workers.
- Fall hazard/inadequate fall protection (35%): Common examples included using ladders that were not properly secured or that did not extend three feet above the landing; structures such as towers used in debris removal sites or scaffolds that did not have adequate guardrails; and individuals not properly protected from falls when on roofs, handling debris on trucks, or using aerial lifts to trim trees or repair utilities. Entries frequently mentioned lack of or improper use of fall protection equipment (i.e., harnesses, lanyards, connectors, and suitable anchorage points) where such equipment was required. Employers must identify potential fall hazards associated with a task and ensure that these hazards are addressed through controls such as guardrails, a safety monitoring system that includes monitors and warning lines, and/or fall protection equipment.
- Aerial Lifts and Fall Protection: Approximately 15% of all the entries discussed fall protection and other PPE use while operating aerial lifts. Almost all of the entries identified a lack of or improper use of fall protection equipment by operators. Employers need to ensure that workers comply with the requirements of 29 CFR 1926.453 including the use of a properly anchored harness for fall protection (or body belt for tethering or restraint use only). For additional information on the use of aerial lifts, users should see the Use of Aerial Lifts activity sheet.
- Struck-by another object (20%): Hazards mentioned included materials falling from roofs, and materials falling while being moved by heavy equipment such as dump trucks, cranes, or grapplers. Employers need to ensure that appropriate precautions are taken such as securing equipment on elevated surfaces, using spotters around heavy equipment, and precluding workers from entering debris-handling zones are taken. Employers must train workers to recognize and avoid these hazards and wear hard hats where overhead hazards exist.
Summary of the Hazards Observed During Specific Activities
Using information pulled from the same set of SitReps, this section highlights the hazards documented most frequently during the eight hurricane recovery tasks OSHA personnel observed most often:
- Roof Inspection, Tarping, and Repair
- Debris Collection and Removal
- Tree Trimming
- Restoring Electrical Utilities
- Debris Reduction, Recycling, and Disposal
- Assessment, Cleanup, and Repair of Structures
- Restoring Communications Systems
- Restoring Water and Sewer Services
Exposure controls to protect response and recovery workers from the hazards that are common among these activities are identified at the end of this section.
Roof Inspection, Tarping, and Repair
Fatalities associated with this activity: Three worker fatalities occurred during Roof Inspection, Tarping, and Repair activities associated with hurricane response and recovery operations (August 31, 2005 to March 21, 2006). Two people were killed when they, in separate incidents, fell through holes in the roofs they were repairing. A third person died when he fell to the ground.
Hazards documented during this activity:
Table I-2: Hazards Frequently Documented During Hurricane-Related Roof Inspection, Tarping, and Repair Operations
Description of Hazard or Observation | Approximate Percentage of Entries |
---|---|
Fall protection hazards | 80% |
Improper or unsafe use of ladders or scaffolding | 35% |
PPE was missing or used improperly | 30% |
Electrical hazards | 15% |
Table I-2 shows the four hazards most frequently identified in the SitRep entries for Roof Inspection, Tarping, and Repair activities:
- Fall protection hazards (missing harness, improperly used harness, etc.) (80%): Entries noted that safety-monitoring systems were not established and that fall protection (harnesses, lanyards, lifelines, connectors, anchorages, and anchorage points) was not used or was used improperly where such equipment was required.
- Improper/unsafe use of ladders or scaffold (35%): Entries noted that ladders were not tied off (to prevent shifting), where not protected at the base from being struck-by passing traffic, and were not extended three or more feet above the landing surface. Nearly a quarter of the entries in this group discuss scaffolding. Scaffolding entries involved missing guardrails (fall protection (above)), working levels that were not completely planked, and scaffolds that were not braced and secured properly.
- PPE (25%): The PPE specifically noted included inadequate face and head protection.
- Electrical hazards (15%): Entries noted that workers did not maintain adequate separation distances from uninsulated energized power lines and were not protected from electrical shock when using power tools to repair roofs (e.g., using electrical power tools without the use of ground-fault circuit interrupters). Employers and workers need to ensure that grounding equipment (e.g., insulating blankets) is installed by electric utility personnel or adequate separation distance is maintained when working near power lines. Employers also need to ensure that power tools are protected by ground-fault circuit interrupters (GFCIs) or are double insulated, or need to implement an assured equipment grounding program.
- For additional precautions employers and workers should refer to the Recommendations section and to the Roof Inspection, Tarping, and Repair; and the Restoring Electrical Utilities activity sheets.
Debris Collection and Removal
Fatalities associated with this activity: Two worker fatalities occurred during debris collection and removal activities associated with hurricane response and recovery operations (August 31, 2005 to March 21, 2006). One person was struck by an out-of-control vehicle that entered a properly controlled and well marked work zone. An equipment operator was killed when his tractor overturned into a ditch and pinned him underwater.
Hazards documented during this activity:
Table I-3: Hazards Frequently Documented During Hurricane-Related Debris Collection and Removal Activities
Description of Hazard or Observation | Approximate Percentage of Entries |
---|---|
Work zone safety hazards | 65% |
PPE was missing or used improperly | 40% |
Risk of being struck-by object, equipment, or vehicle | 35% |
Table I-3 shows the three hazards most frequently documented in the SitRep entries for Debris Collection and Removal activities:
- Work zone safety (65%): These typically involved situations where workers were not adequately protected from oncoming traffic or heavy equipment movement. The most common issues mentioned were missing signs or cones.
- PPE-related concerns (40%): The most common concerns documented were lack of face and head protection (e.g., goggles and hard hats), hand protection (e.g., reinforced leather gloves for handling tools and sharp debris), hearing protection, and body protection (e.g., chaps when working with chain saws and ANSI-approved high-visibility vests for use in areas where traffic controls are needed).
- Struck-by hazards (35%): This commonly involved workers not being adequately protected from falling debris during heavy equipment use (e.g., hauling or pushing materials using bulldozers, front-end loaders, or dump trucks). Employers need to ensure that spotters are used when the visibility of heavy equipment operators is restricted and preclude workers from entering areas where debris is handled or can fall from heavy equipment. Workers need to keep a safe distance from heavy machinery, and maintain proper traffic controls near roadways.
- For additional precautions employers and workers should refer to the Recommendations section and to the Debris Collection and the Work Zone Safety and Traffic Control within a Work Area activity sheets.
Tree Trimming
Fatalities associated with this activity: No worker fatalities were reported during tree trimming activities associated with hurricane response and recovery operations (August 31, 2005 to March 21, 2006).
Hazards documented during this activity:
Table I-4: Hazards Frequently Documented During Hurricane-Related Tree Trimming Operations
Description of Hazard or Observation | Approximate Percentage of Entries |
---|---|
PPE was missing or used improperly | 55% |
Work zone safety hazards | 45% |
Chainsaw-related hazards | 30% |
Fall protection used improperly | 20% |
Table I-4 shows the four hazards most frequently documented in the SitRep entries for Tree Trimming operations.
- PPE-related concerns (55%): Entries described situations where PPE was not used, PPE was used improperly, or PPE was available but workers were not required to use it or were not aware that it was necessary. Inadequate face, head, and body protection were noted in over half of the entries; inadequate hand protection and hearing protection were each noted in over one-quarter of the entries.
- Work zone safety (45%): Entries describe issues involving work zone safety concerns with most noting lack of cones or signs.
- Chainsaw-related hazards (30%): Hazards noted included the inadequate training of workers and unsafe operation of chainsaws. Employers need to ensure that workers inspect the saws before use, plan the cut to safely ground the tree or pieces of the tree, and safely use the chain saw by not cutting overhead or moving long distances without engaging the brake.
- Fall protection (20%): Approximately 75% of these fall protection entries involved the lack of or improper use of fall protection equipment while operating aerial lifts.
- For additional precautions employers and workers should refer to the Recommendations section and the Tree Trimming, Work Zone Safety and Traffic Control within a Work Area, and Use of Aerial Lifts activity sheets.
Restoring Electrical Utilities
Fatalities associated with this activity: Three worker fatalities occurred during electrical utility restoration associated with hurricane response and recovery operations (August 31, 2005 to March 21, 2006). One person was struck by a 75-foot utility pole that fell when it was being positioned with a forklift. One person was electrocuted when he contacted a live 110-volt line that he was attaching to a house. One person suffered fatal burns when the electrical system being restored became energized, exploded, and caused a flash fire.
Hazards documented during this activity:
Table I-5: Hazards Frequently Documented During Hurricane-Related Electrical Utility Restoration Operations
Description of Hazard or Observation | Approximate Percentage of Entries |
---|---|
Work zone safety hazards | 40% |
PPE was missing or used improperly | 20% |
Fall hazards | 25% |
Shock or electrocution hazard | 25% |
Table I-5 shows the four hazards documented most frequently in SitRep entries for Electrical Utilities Restoration operations.
- Work zone safety (40%): Entries describe issues involving work zone safety concerns with most noting lack of cones or signs.
- PPE concerns (20%): Face/head protection and hand protection were each mentioned in approximately one-quarter of the PPE entries.
- Fall hazards (25%): Over half of these entries involved aerial lifts, while another quarter involved improper use of ladders or scaffolds. The aerial lift hazard most frequently noted was the lack or improper use of fall protection equipment by workers in aerial lifts; most often this involved workers who did not properly anchor their fall protection equipment when working from an aerial lift. Ladder and scaffold hazards most frequently involved ladders that could shift because they were not properly tied off at the top or did not have their bases protected from being struck by passing traffic.
- Shock or electrocution hazards (25%): Commonly referenced observations included inadequate protection from contact with live electrical equipment during repairs including an improper use of insulating and grounding equipment and electrically protective PPE. Only 1910.269 qualified workers shall conduct electrical power restoration activities. Ensure that power lines are deenergized whenever possible. In addition, install temporary grounds to protect workers against inadvertent energizing of power lines. Use insulating protective equipment and PPE as needed around power lines.
- For additional precautions employers and workers should refer to the Recommendations section and to the Restoring Electrical Utilities, Work Zone Safety and Traffic Control within a Work Area, and the Use of Aerial Lifts activity sheets.
Debris Reduction, Recycling, and Disposal
Fatalities associated with this activity: Two worker fatalities occurred during debris reduction, recycling, and disposal activities associated with hurricane response and recovery operations (August 31, 2005 to March 21, 2006). One person was killed when he was struck by a bulldozer at a debris reduction site. One operator was killed when his excavator rolled down the debris pile he was working on.
Table I-6: Hazards Frequently Documented During Hurricane-Related Debris Reduction, Recycling, and Disposal Activities
Description of Hazard or Observation | Approximate Percentage of Entries |
---|---|
PPE was missing or used improperly | 50% |
Work zone safety hazards | 45% |
Fall hazards | 15% |
Table I-6 shows the three hazards documented most frequently in the SitRep entries for Debris Reduction, Recycling, and Disposal activities.
- PPE concerns (50%): The most common issues involved lack of required hard hats (mentioned in over half of the entries on PPE) and inadequate respiratory protection and hearing protection (each referenced in one-quarter of the entries for this group).
- Work zone safety (45%): These hazards are consistent with the large amounts of heavy equipment used at locations that handle debris.
- Fall hazards (15%): Specific SitRep entries described individuals standing on top of large piles of debris (often in truck beds) without fall protection equipment and workers in observation towers with inadequate hand and guardrails.
- For additional precautions employers and workers should refer to the Recommendations and to the Debris Reduction, Recycling, and Disposal and the Work Zone Safety and Traffic Control within a Work Area activity sheets.
Assessment, Cleanup, and Repair of Structures
Fatalities associated with this activity: Two worker fatalities occurred between August 31, 2005 to March 21, 2006 during the assessment, cleanup, and repair of structures damaged by the hurricanes. One worker received an electrical shock when the knife he was using contacted a power line and he fell 18 feet. Another worker was killed when he was struck by a falling security gate that was damaged during a hurricane.
Table I-7: Hazards Frequently Documented During Hurricane-Related Assessment, Cleanup, and Repair of Structures
Description of Hazard or Observation | Approximate Percentage of Entries |
---|---|
Fall hazards | 60% |
Improper use of ladders and/or scaffolds | 50% |
PPE was missing or used improperly | 30% |
Risk of being struck-by object, equipment, or vehicle | 25% |
Table I-7 shows the four hazards documented most frequently in the SitRep entries for Assessment, Cleanup, and Repair of Structures.
- Fall Protection/Fall Hazards (60%): Entries in this group cited fall hazards or improper use of fall protection controls or equipment.
- Ladder and Scaffolding Use (50%): Many of these entries mention not properly protecting the ladder from shifting by tying it off, inadequately protecting a ladder's base from being struck by passing traffic, and not extending that ladder three or more feet above the landing surface. Scaffolding entries involved workers not adequately protected from falls by guardrails, and scaffolds without proper planking and adequate support.
- PPE issues (30%): Face and head protection (such as goggles and hard hats) were cited in around 80% of the entries in this group; hand protection was cited in roughly 25% of these entries.
- Struck-by hazards (25%): Entries noted workers at risk for being struck-by objects such as construction materials.
- For additional precautions, employers and workers should refer to the Recommendations section and to the Assessment, Cleanup, and Repair of Structures activity sheet.
Restoring Communications Systems
Fatalities associated with this activity: Two worker fatalities occurred between August 31, 2005 and March 21, 2006 during the repair of communication systems damaged by hurricanes. One cable television repairman was electrocuted when he contacted a live electrical line three feet above the cable line he was working on. Another telecommunications worker was found dead near a ladder that was placed against a telephone pole.
Table I-8: Hazards Frequently Documented During Hurricane-Related Communication System Restoration Activities
Description of Hazard or Observation | Approximate Percentage of Entries |
---|---|
Work zone safety hazards | 55% |
Hazards associated with use of aerial lifts | 40% |
Fall hazards | 25% |
PPE was missing or used improperly | 10% |
Table I-8 shows the four hazards most frequently documented in the SitRep entries for the Restoration of Communication Systems.
- Work zone safety (55%): Hazards involved situations where workers were not adequately protected from oncoming traffic. The most common issues mentioned were missing signs or cones.
- Use of Aerial Lifts (40%): Over half of these entries noted the lack or improper use of fall protection equipment by workers in aerial lifts. Most often this involved workers who did not properly anchor their fall protection equipment when working from an aerial lift.
- 25% of all entries for this activity discuss potential fall hazards or lack of fall protection. Almost all of these entries involve the improper use of fall protection equipment during use of aerial lifts.
- PPE issues (10%): The PPE hazard most frequently noted included improper face and head protection (e.g., goggles and hard hats) and hand protection.
- For additional precautions employers and workers should refer to the Recommendations section and to the Restoring Communications Systems, Work Zone Safety and Traffic Controls within a Work Area, and the Use of Aerial Lifts activity sheets.
Restoring Water and Sewer Services
Fatalities associated with this activity: No worker fatalities were reported during water and sewer service restoration operations associated with hurricane response and recovery operations (August 31, 2005 to March 21, 2006).
Hazards documented during this activity:
Table I-9: Hazards Frequently Documented During Hurricane-Related Sewer and Water Service Restoration Activities
Description of Hazard or Observation | Approximate Percentage of Entries |
---|---|
Work zone safety hazards | 50% |
Hazards of working in trenches or excavations | 40% |
PPE was missing or used improperly | 30% |
Table I-9 shows the four hazards most frequently documented in the SitRep entries for Sewer and Water Service Restoration.
- Work zone safety (50%): Entries most often noted lack of cones or signs.
- Trench/excavation hazards (40%) while accessing the water or sewer lines. Trenching hazards associated with water and sewer system restoration included cave-in hazards (mentioned in nearly half of these entries) and exit/egress issues (mentioned in over one-quarter of these entries). Employers need to ensure that trenches are properly protected from cave-in and must have a competent person inspect trenches before workers are allowed to enter them and periodically thereafter.
- PPE concerns (30%): Over half of the entries note inadequate face and head protection and over a quarter noted a lack of hearing protection when this protection was required. Inadequate foot protection (e.g., lack of waterproof boots when needed) was also discussed in several of these entries.
- For additional precautions employers and workers should refer to the Recommendations section and to the Restoring Water and Sewer Services, Work Zone Safety and Traffic Controls within a Work Area, and the Trenches and Excavations activity sheets.
Additional Hurricane Response and Recovery Fatality Information
There were four worker fatalities between August 31, 2005 to March 21, 2006 associated with hurricane response and recovery activities that are not described above.
- Two worker fatalities that occurred during the Removal of Floodwaters from Structures and Initial Entry into Previously Flooded Areas. These fatalities occurred on the same date and at the same location when the workers were overcome by hydrogen sulfide gas during removal of water from a confined space.
- Two additional fatalities occurred during Heavy Equipment and Powered Industrial Truck Use. One person was struck by a truck that flipped over on top of him after he got out of the vehicle, which he had parked on soft mulch. One person was crushed when the jack he was using to lift the trailer slipped, causing the truck's bumper to fall on his head. Four heavy equipment fatalities are discussed in the debris reduction, recycling, and disposal; debris collection and removal; and the restoring electrical utilities sections.
Exposure Controls for Activity-Specific Hazards
This section only addresses the hazards noted above that are common among the eight activities highlighted. The Matrix includes detailed, hazard-specific recommendations for engineering controls, work practices, and additional PPE in the individual activity sheets.
- Work Zone Safety: Work zone safety precautions and traffic control procedures are necessary to protect response and recovery workers performing tasks adjacent to or in roadways, and within a work site where heavy equipment and vehicles are operating near others. In both cases individuals are at risk of being struck, either by on-coming traffic or by vehicles and heavy equipment moving around the site. After a hurricane, much of the recovery work requires accessing structures, utilities, or debris from roadways. Most recovery operations require the use of heavy equipment. For this reason, the Matrix includes an activity sheet on Work Zone Safety and Traffic Controls within a Work Area, which includes engineering controls, work practices, and additional PPE that employers must implement and require the use of to protect workers. In general, employers must:
- Ensure that workers understand the importance of establishing traffic controls.
- Mark work zones with needed barriers, cones, signs, and/or flaggers to provide plenty of warning and appropriate direction to approaching vehicles.
-
Within work sites, establish a traffic control pattern, mark work zones with cones, barricades, and signs, and ensure that heavy equipment operators stay alert and are aware of other equipment and personnel near them and their direction of travel.
- Fall Hazards and Fall Protection: Fall hazards and exposure controls, including engineering controls, work practices, and PPE, are highlighted in the individual activity sheets in this Matrix. Employers should review the individual activity sheets for the operation their workers are anticipated to perform and identify potential fall hazards. In general, employers must:
- Address fall hazards through controls such as guardrails, a safety monitoring system including monitors and warning lines, and/or fall protection equipment.
- If fall protection equipment is required, train workers to understand where this equipment is required and how to use it properly.
-
Where workers will use aerial lifts, provide them with fall protection equipment that meets the requirements of 29 CFR 1926.453 and instruct them how to use the equipment and anchor themselves to the bucket.
- PPE: Head, eye, hand, and foot protection was required for most of the activities response and recovery workers performed during hurricane response and recovery operations. In many cases the PPE was not provided or its use was not enforced. The Matrix identifies the head, hand, eye, and foot protection recommended for all activities in the disaster response and recovery area in the General Recommendations section of the Matrix. The Matrix also identifies additional PPE for specific hazards in the individual activity sheets. In general, employers must:
- Assess the need for PPE, and select the PPE that will protect an worker performing the job
- Ensure that PPE is available and sized for the worker
- Train workers when and how to use required PPE
-
Enforce the use of PPE when it is required
- Ladders and Scaffolding: This equipment was used frequently to access structures, roofs, trees, etc., and to work from to complete inspection, repair and other tasks at elevated locations. The Matrix includes the improper use of ladders and scaffolds as a hazard in many of the individual activity sheets and highlights engineering controls, work practices, and PPE in each. In general, employers must:
- Ensure that ladders are properly secured, protected, and always extend three feet above landings
- Ensure that scaffolding is secured, properly planked, and has guardrails installed when needed. Scaffolding must also be inspected by a competent person prior to use.