Printing Industry eTool
Printing Industry » Flexography
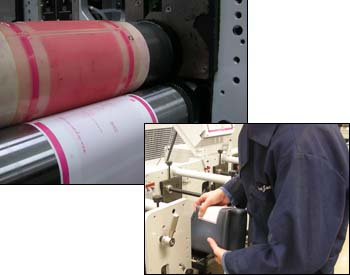
Flexography is a versatile process that can print on a variety of materials of varying sizes. Flexography prints items that we are in contact with daily including cereal boxes, bottle labels, potato chip bags, frozen food bags, corrugated boxes, newspapers and grocery bags.
The flexographic printing process is similar to a rubber stamp and ink pad, but more sophisticated and on a larger scale. Flexography uses a soft, flexible printing plate with a three-dimensional (3D) raised mirror image of the design. Plates are mounted on a cylinder located on a press equipped with anywhere from one to twelve color stations. Ink is placed on the anilox roll, transferred to the plate and from the plate to the substrate.
While there are significant variations in flexography, this module attempts to simplify the overall operation into three broad categories: prepress, press, and post press. First, the prepress section includes everything needed to develop an image, from the idea stage to a plate that can be used on a printing press. The press section includes both web- and sheet-fed processes and incorporates tasks from loading raw substrate into the press, to loading plates, filling inks and removing the finished product from the press. Finally, the post press section includes activities used to further process the printed material into a finished item.
The following identifies potential hazards and possible solutions to reduce the ergonomic hazards within the flexography printing process:
Pre-press
In the modern printing business most prepress work is completed via computer. Images are delivered, checked and edited.
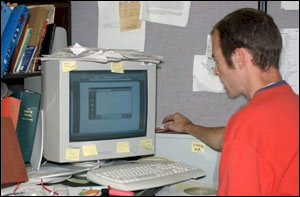
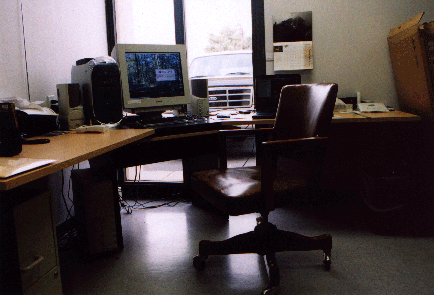
Potential Hazards
The hazards associated with this type of activity are similar to those found in an office environment. Employees in the prepress area may spend extensive amounts of time at the computer workstation developing content. Workstations that are not properly designed for computer work may cause stressful postures or motions.
-
Prolonged periods of awkward body postures (i.e., neck bending, torso twisting, raised shoulders, extended arm) (Figure 1).
-
Repetitive motions (i.e., frequent reaching to a mouse, clicking and dragging) (Figure 1).
-
Contact stress to the legs and/or arms (Figure 1).
-
Glare and poor lighting situations (Figure 2) increase muscle stress, such as eye strain, and encourage awkward postures such as leaning forward to view monitor.
Possible Solutions
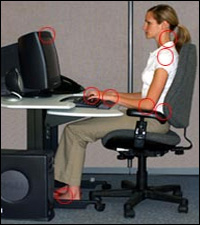
(Roll mouse over text below to highlight specific areas in the image.)
-
Establish a training program so that employees can learn how to set up and periodically adjust their workstations (Figure 3).
-
Ensure keyboard and mouse are at proper height and position.
-
Provide appropriate computer components and furniture.
- OSHA's Computer Workstations eTool offers assistance for identifying, analyzing and controlling hazards in the following areas:
Flexographic platemaking involves transferring images onto photopolymer or rubber printing plates. This transfer may be from photographic negatives or digital computer-to-plate process. Plates can be a variety of sizes depending on the size of the printing press and the requirements of the job. During the platemaking process, plates must be transported between the processor, drying drawers, plate cylinders and storage drawers.
Potential Hazards
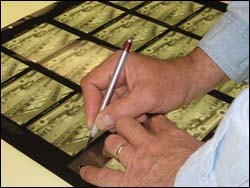
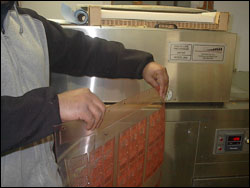

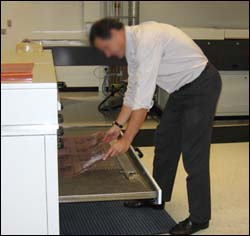
- Frequent or prolonged use of forceful pinch grips to:
- Cut or trim film and masking materials using small- handled knives or film cutters (Figure 4).
- Position or move film while on the platemaker (a 52" x 80" plate can weigh in excess of 35 pounds).
-
Lift and carry the plate between workstations (Figure 5).
- Frequent or prolonged torso bending to:
- Reach over large platemaker tables or processors (Figure 6).
- Place plates into or retrieve plates from processors trays or storage drawers (Figure 7).
Possible Solutions
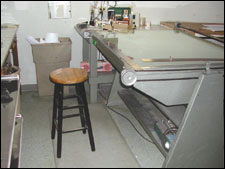
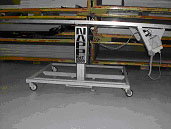
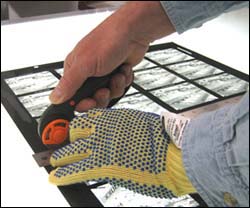
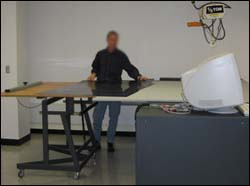
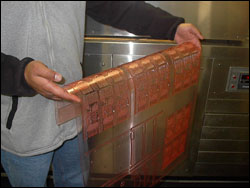

- Adjust work surface height and angle to minimize forward bending and reaching. Suggested modifications include: (Figures 8 and 9)
- Provide adjustable height and tilt tables. Workstations should be adjustable for either sitting or standing heights.
- Add blocks under the table legs to raise the work surface, if workstation is too low. Adjust height to accommodate tallest users and provide shorter users with platforms when workstation is shared.
- Provide height adjustable seating.
- When standing body position is required, encourage employees to adjust workstation and material so that work can be done while standing up straight, with the elbows in close to the body.
-
Take frequent micro (one-minute) breaks to change body posture and rest when working in a bending body posture for a prolonged period.
-
Use a larger-retractable razor tool with an ergonomic handle for cutting film. This reduces the likelihood of hand cuts and muscle stress from constantly gripping a small razor blade (Figure 10). Ideally, the handle should allow the user's fingers and the palm of the hand to maintain a "C" shaped posture. Tool handles should be rounded about 1-1/2" in diameter and made of non-slip material.
-
Keep cutter blades sharp at all times to reduce the amount of hand force required when cutting film.
-
Design work area to reduce the distance and time necessary to hand-carry film and plates around the prepress area.
-
Use a fully adjustable (height and angle) transfer cart or table on wheels which allows the operator to easily move large, bulky plates from one step of the platemaking process to the next without physically lifting the plate (Figure 11).
-
Carry flexo plates by draping them over hands or fingers instead of using a pinch grip (Figure 12).
-
Use a plate exposure unit designed to allow the operator 360 degree access to the plate (Figure 13). Because "clam shell" exposure units are hinged at the back, they can only be accessed from the front. Consequently, the operator has to lean further into the equipment.
Press
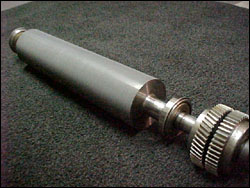
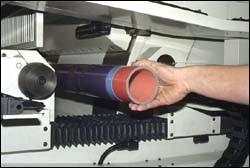
Flexo presses utilize rollers, sleeves, and cylinders to complete the printing process. Operators have to tend to, remove, transport, or store many of these press components. These tasks may require lifting of heavy weight, often in awkward postures, especially on older machines where there is little attention given to accessibility.
Anilox rolls (Figure 14) are engraved ink-metering rollers used on flexographic printing presses. They are typically ceramic coated steel rolls of considerable size and weight. A doctor blade spreads ink which has been applied to the Anilox roll, to create a controlled film across the surface of the roll. Ink is then transferred which. prints the image onto the substrate.
Anilox sleeves are used as an alternative to anilox rolls. Also ceramic coated, they are hollow and slide over steel cylinders which remain on the press.
Printing plates are mounted on plate cylinders. For narrow web applications lighter plates may be mounted on plate cylinders either on or off the press. On wide web applications where the plate may weigh several hundred pounds, mounting is generally done off the machine where access is improved. Plate cylinders are seldom removed from corrugated presses except for maintenance. The plates for this application are mounted on mylar and attached in the press.
Plate sleeves (Figure 15) are hollow cylindrical plates that are fitted over a plate cylinder. This makes cylinders lighter and easier to manipulate in wide web and uninterrupted printing processes.
Potential Hazards
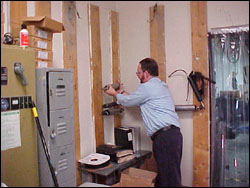
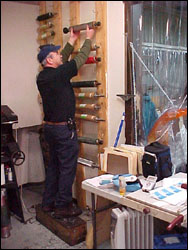
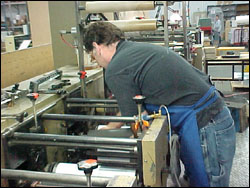
-
Use of extended reaches (which may be above shoulder or head level) to place or remove heavy cylinders/rolls from or onto storage racks. Additionally, these reaches may be required when placing cylinders/rolls into the press (Figures 16 and 17).
-
Repetitive and forceful lifting utilizing awkward postures such as torso bending and twisting to manually place or remove cylinders/rolls from rack or press (Figure 18).
-
Strain of the hand and fingers may occur when gripping and lifting cylinders when the cylinders size is too large for good hand coupling.
-
Rolls, sleeves or plates may be too heavy for individuals to manually lift.
Possible Solutions
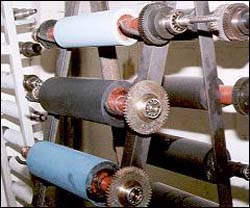
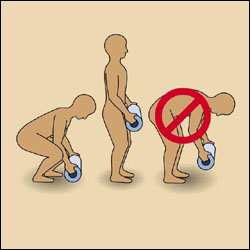
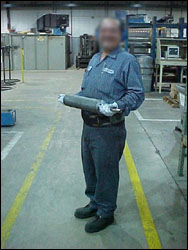
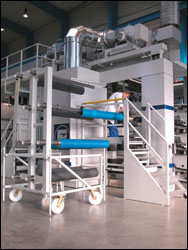
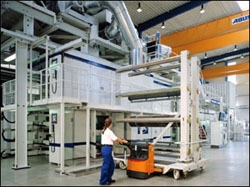
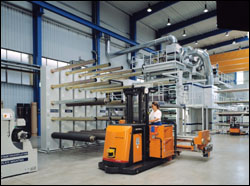
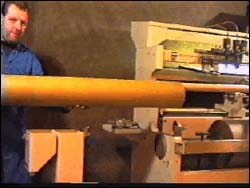
-
Consider the design and placement of storage systems and cleaning equipment. Storage systems should be close at hand, easy to access, and at a comfortable working height. The floor area surrounding the storage systems should be kept clear of debris, finished labels, roll stock, ink buckets, etc. to prevent tripping and improve access.
-
Use storage racks that are at the ergonomically correct height (usually between knee and shoulder height), easily accessible and minimize bending and reaching (Figure 19). Do not store rolls under work benches.
-
Keep work objects or materials close to the body when lifting or carrying (Figures 20 and 21).
- Reduce the weight of items to be lifted by:
-
Whenever possible, solid steel rolls should be phased out in favor of lighter weight, thin-walled hollow steel anilox rolls. They can reduce the weight of anilox rolls by as much as 2/3. A 19" solid steel anilox roll weighing 90 pounds can be replaced with a thin-walled, hollow steel roll weighing only 35 pounds.
-
Other ways to lighten rolls include manufacturing from aluminum, aluminum tube with steel journals, or carbon fiber with steel journals.
These products will significantly reduce the rolls’ weight, but may increase the cost and may require additional care when cleaning or resurfacing.
-
- Ensure that engineering and administrative controls are implemented for handling rolls that are heavier than about 50 pounds or which can not be handled in close to the body at about waist height, including:
- Overhead gantry or pivot cranes to lift rolls from machines or racks.
- Fork lifts or pallet trucks to lift, lower, and transport rolls or racks.
-
Multiple employees working together to perform lifts of heavy objects.
-
Reduce anilox roll changes by standardizing process specifications. For example, running jobs which can use anilox rolls with the same specifications will require fewer roll changes.
- Use carts or integrated systems to minimize manual handling of sleeves or rolls.
- Provide a roll stand that mechanically lifts and positions rolls (Figure 22).
- Provide a cart or floor tram (Figure 23) to move large cylinders. Once manually moved in front of the printing press, the cylinder cart is coupled to a motorized positioning device that automatically moves the cart to the locations that are required for deinstalling and installing the hardware.
-
Provide a programmable floor tram controlled by laser and inductive cable. This may be used to transport sleeves and cylinders between different work areas such as mounter proofer, storage area and transfer station (Figure 24).
- Replace heavy plate cylinders with lighter weight (5-10 pounds) air sleeve cylinders (Figure 25). This minimizes heavy lifting and awkward postures by letting machinery and forced air do the work.
- Process includes the following steps: applying air to the plate cylinder; slide off current sleeve (with plates still mounted); slide on new sleeve with the plates for the next job; and remove air source to affix the sleeve in place.
Press ink must be stored, transported, mixed, and loaded into presses before the printing process can begin. Ink is purchased in large volumes ranging from 5 gallons to 1000 liters (about 300 gallons). Smaller volumes may be poured and mixed manually. Larger volumes that weighing in excess of 10 pounds must be dispensed using pumps and manually put in place. After the ink is mixed it is placed into containers (usually kits) which are transported to the press on carts or pallets. Once at the press, ink may be pumped from the kit to the ink fountain. Smaller volumes may be manually poured.
Potential Hazards
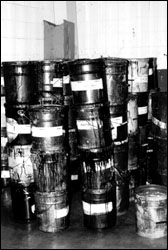
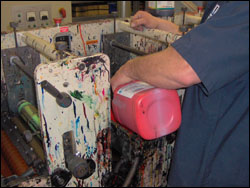
-
Forward bending to reach low locations or reaching overhead to retrieve ink containers from pallets, shelving or stacks (Figure 26).
-
Force needed to lift or move (may include use of hand truck) heavy ink containers and drums (50 to 600 pounds).
-
Force needed to lift and set heavy pumps and lids (more than 10 pounds).
-
Awkward bending of the wrist when pouring ink into ink fountains or containers (Figure 27).
Possible Solutions
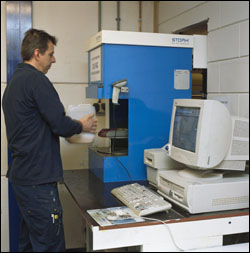
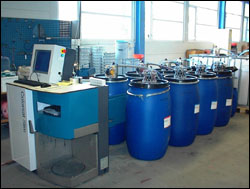
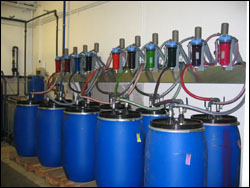
-
Order supplies or repackage ink in the smallest containers practical to reduce heavy lifting where mixing and pouring must be done manually (Figure 28).
-
Use a height adjustable pushcart to retrieve and transport multiple containers from storage.
-
Use mechanical assistance, such as a forklift or barrel dolly, to move heavy items.
-
Use automated ink dispensing systems which pump ink from large drums into kits (Figure 29).
-
Use fixed ink dispensing systems that can be mechanically lowered over drums or use pumps that are mounted nearby instead of manually lifting and positioning ink pumps onto drums of ink (Figure 30).
-
Minimize awkward wrist postures by using two hands to support containers during pouring.
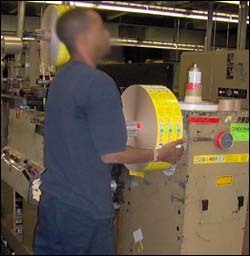
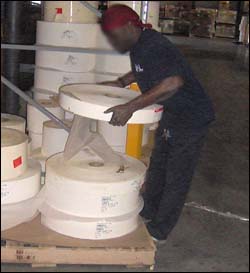
Web presses print on rolls of substrate including paper, film and foil. The finished product is generally collected on another large rolls at the end of the press. Rolls must be loaded onto and removed from the press.
Potential Hazards
-
Forceful and repetitive gripping is used to grasp and move rolls between the supply pallets and press feed areas.
-
Forceful and repetitive gripping is used to grasp and remove finished rolls for further processing.
-
Heavy lifting and physical strain while manually moving rolls between the press or pallets (Figure 31).
-
Forward bending to lift substrate rolls from lower areas of supply pallets (Figure 32).
-
Forward bending to stack rolls of finished product on pallets.
Possible Solutions
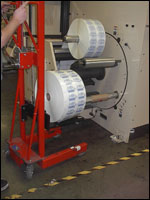
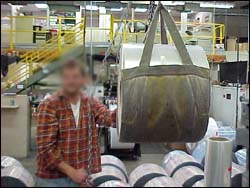
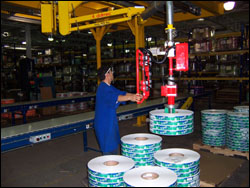
-
Keep elbows close to your body when manipulating heavy rolls to reduce physical strain.
-
Use a lift or other mechanical assistance to remove rolls from turrets, conveyor belts and pallets (Figures 33 and 34).
- Use a lift to maneuver rolls of stock and finished product (Figure 35).
-
Using lifts may benefit overall efficiency and quality by increasing the number of finished rolls a packer can safely handle. This may also eliminate unnecessary carrying and manual transferring reducing the potential for damage to finished rolls.
-
-
Design a track system where rolls can be positioned on a turntable platform and pushed along the track into position.
-
Provide education and training on use of safe body mechanics when pushing, pulling and lifting materials.
Some presses print on individual pieces of flat stock such as corrugated board. Pressmen working with stacks of flat stock are exposed to a number of potential ergonomic hazards when loading or unloading a press. Sheets can be large, heavy and awkward to handle.
Potential Hazards
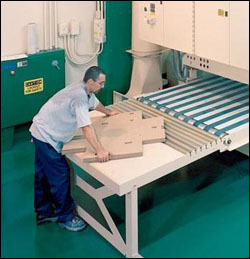
- Forceful and repetitive gripping using elongated grip may be required to:
- retrieve stock from supply pallets and transport to press loading area, and
-
to move finished product stacks for further processing.
-
Use of extended reaches (which may be above shoulder or head level) to retrieve or place stock from tall piles.
-
Torso bending to place or retrieve stock from low locations such as pallets on the floor or tables (Figure 36).
-
Extended reaching and torso bending to feed stock into press.
Possible Solutions
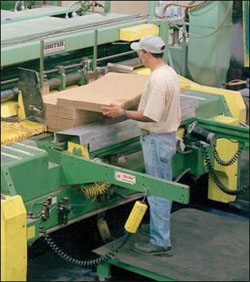

-
Provide employees with tools to minimize reaching and bending, including push bars for pushing and manipulating materials.
-
Minimize elevated reaches (which may be above shoulder or head level) to stock, controls or feed area by using platforms to raise employees to proper height (Figure 37).
- Generally a stack should be limited to no more than about 1-1/2 to 2-1/2 inches. This is easier on the back and minimizes the finger force that must be exerted. Encourage employees to lift and carry less material more frequently rather than heavier loads less often.
-
Consider using visual markers such as lines drawn on a stack of materials to suggest to employees the amount of material to be handled at one time.
-
-
Use height adjustable carts (Figure 38) to transport stock to and from the printer. Adjust the height of the cart to be the same height as the press feed and discharge so that stock can slide on and off without the employee having to reach and lift.
-
Provide palletizers or scissors lift at the press so that stock can be unloaded and loaded at a proper height. These devices keep the height of a load at about waist height by raising the height as supply is removed from the pallet.
-
Do not stack items in tall stacks that require elevated reaches.
- Use a waist mounted belt to support the bottom edge of the substrate sheets (corrugated material). This should minimize bending and twisting keeping the load at waist height and directly in front of the body. Forceful pinch grips are minimized because weight is supported by the belt.
- Pull the sheets from the table or stack to the beltline, support the bottom edge against the belt, then lift the sheet up using the belt as a pivot point and transport to the new location.
Post Press
Depending on customer specifications, printed products may be packed, banded or sheaved, or palletized before it is shipped. Bundled product can be heavy and loading may be from near ground level to above head height. The product may be slick and require excess finger force to keep product in stacks. After a load has been prepared on a pallet, it is generally wrapped with plastic to maintain its integrity during transit.
Potential Hazards
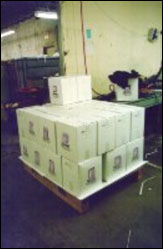
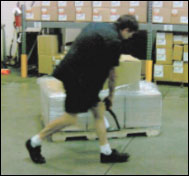
- Torso bending, twisting and reaching out and away from the body to:
- Grab bundles on the conveyor before they arrive.
- Place items on pallets. The height of material on the bottom of the pallet is typically only a few inches above the floor (Figure 39).
-
Manually wrap plastic around bottom of the pallets while supporting the plastic wrap dispenser (Figure 40).
- Forceful, repetitive gripping to:
- Retrieve printed materials from press.
- Load materials onto pallets or into boxes.
-
To hold rolls of plastic wrap while wrapping around pallets.
-
Bundles transported between press and pallet may be too heavy or too bulky to lift.
-
Physical stress associated with positioning large plastic wrap rolls into automatic wrapping machines.
-
Repeated lifting of wooden pallets weighing between 40 and 70 pounds may cause stress to the lower back, arms, elbows and shoulders.
- Prolonged periods of standing to:
- Feed presses.
- Collect and palletize finished product.
-
Wrap and pack product.
-
Awkward hand and arm postures to place materials in packing box.
-
Repetitive hand and arm motions are required when sealing packages using handheld tape gun.
Possible Solutions
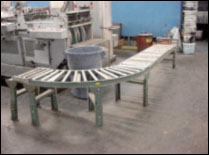
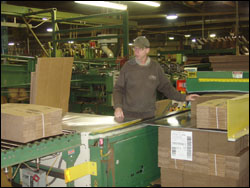
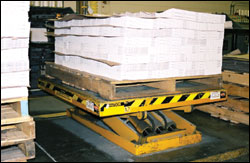
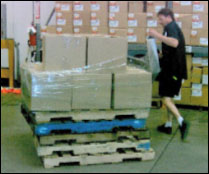
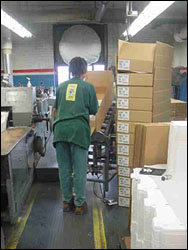
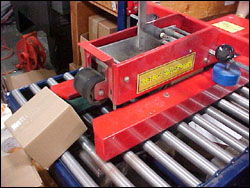
- Eliminate or minimize manual material handling by:
- Using mechanical means, including hoists, lift tables, and stackers.
- Using carts to transport product from one location to another. Push instead of pull whenever possible.
-
Use conveyors to move materials directly to the next step or process without palletizing (Figure 41).
- Conveyor should be coordinated with press (at equal height) to allow material transfer with minimal lifting.
- Materials should be slightly below waist height and close to the employees body at the unloading end of the conveyor (Figure 42). This will allow the employee to lift and stage loads without bending or reaching.
- If conveyors are too high, use of a platform will allow shorter employees to work at proper height.
- Elevate the pallets used for receiving processed materials to minimize bending by:
- Using height-adjustable lift devices to keep the load close to waist level. Some height-adjustable devices also rotate. This enables the employee to position the load close to the body by turning the pallet (Figure 43).
- Using a forklift to position pallets off the floor and at a matching height adjacent to the conveyor.
- Placing pallets on a platform that positions the load close to waist level.
-
Placing the pallet on several other empty pallets to raise the height. Secure the lower pallets to increase the stability of the stack (Figure 44).
-
Optimize load size and weight for one-person lifting. Generally, a load should not weigh in excess of 40 pounds.
-
Use a wedge, provide adjustable packing stands, or build a table at an angle so that the box opening is tilted toward the loader and improves access to box interior (Figure 45).
-
Consider using boxes with one removable side.
-
Minimize twisting of torso when loading between conveyor and pallet. Move the feet to face the load instead of twisting. Place box or pallet close to conveyor.
-
Use automated taping, banding or wrapping machine (Figure 46).
-
Use rolls that weigh as little as possible to minimize the lifting hazard if manual plastic wrapping must be performed.
-
Consider the use of an automatic pallet wrapper and an automatic strapping machine to reduce repetitive motions and awkward postures (Figure 47).
-
Use lighter, plastic pallets. Plastic pallets can weigh half of what a wood pallet weighs. The employees of both the company and the customer will benefit from the reduction in weight being lifted (Figure 48).
-
Provide anti-fatigue mats and/or sit/stand stools (Figure 49).
-
Change the handling method to lowering instead of lifting, if possible. Ensure proper lifting techniques are used even when lowering.
-
Consider job modification or rotation to reduce the exposure time for these tasks.
- Train on proper lifting techniques.
- Keep back straight.
- Keep elbows in close to the body.
- Lift with your legs.
- Get firm grip.
- Do not twist back.
- Move load smoothly
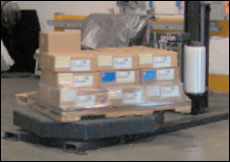
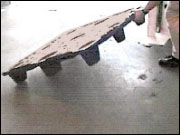
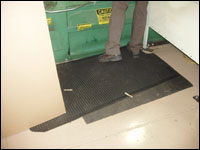