Printing Industry eTool
Printing Industry » Lithography
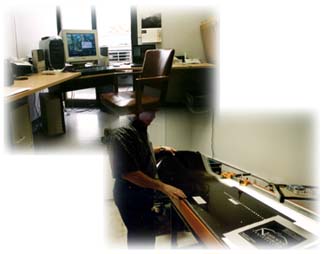
The basic principle of lithography, otherwise known as offset printing, is based on the fact that ink and water don't mix. Early lithographers etched images onto a plate or flat stone, applied ink and transferred the image. Although there are different types (e.g., sheetfed and webfed) and sizes of offset presses, the basic configuration remains the same. When the printing plate is exposed, an ink-receptive coating is activated, creating the image area. On the press, the plate is dampened, first by dampening rollers, then by ink rollers. Ink adheres to the image area and fountain solution sticks to the non-image area. As the cylinders rotate, the image is transferred to the blanket. Paper or another substrate is then placed in contact with the blanket and the image is transferred.
While there are significant variations in the process, this etool attempts to simplify the overall operation into three broad categories. First, pre-press will include everything needed to develop an image from the idea stage to a plate that can be used in a printing press. Second, the press stage will include both sheetfed and webfed processes and will include all tasks from loading raw substrate (usually paper) into the press to the finished product being removed from the press. Finally, finishing and binding will include those processes used to further process the printed material into a finished item.
Potential hazards and possible solutions for the following tasks are covered below.
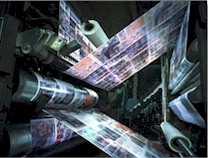
Pre-press
In the modern printing business most pre-press work is done via computer. Images are delivered, checked and edited. The hazards associated with this type of activity are similar to those found in an office environment.
Potential Hazards
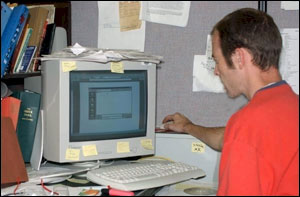

Workers in the prepress area may spend extensive amounts of time at the computer workstation developing content. Workstations that are not properly designed for computer work may cause stressful postures or motions.
-
Prolonged periods of awkward body postures (i.e., tilting the head back, down, or side-to-side) (Figure 1).
-
Repeated motions (i.e., reaching to a mouse). (Figure 1).
-
Contact trauma to the legs or arms from desk surfaces or chair fronts.
-
Glare or monitor washout from poor placement of monitor in relation to windows and other bright light sources (Figure 2).
Possible Solutions
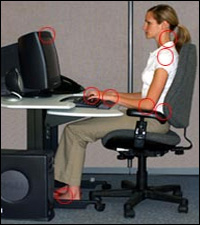
(Roll mouse over text below to highlight specific areas in the image.)
-
Establish a training program so that workers can learn how to set up and periodically adjust their workstations. (Figure 3).
-
Ensure keyboard and mouse are at proper height and position.
-
Provide appropriate computer components and furniture.
- OSHA's Computer Workstations eTool offers assistance for identifying, analyzing and controlling hazards in the following areas:
Platemaking is the process where images are transferred from the computer workstation to a medium that can be used in the printing press. Work is primarily conducted on a light table where designs are transferred to a plate. Finished plates are manually transferred to the printing press.
Potential Hazards
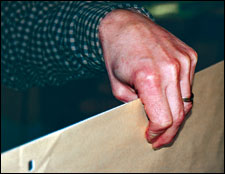

-
Frequent or constant bending and reaching over a large light table to strip film while standing or sitting.
-
Frequent or constant use of a small razor blade, using the thumb and fingers in a pinching grip, for cutting film and masking materials.
-
Frequent or prolonged use of pinch grips or forceful hand gripping to load, carry, or handle film or plates. (Figure 4 and 5).
-
Prolonged periods of standing.
Possible Solutions
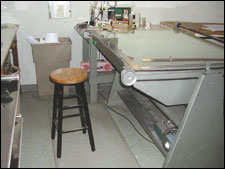
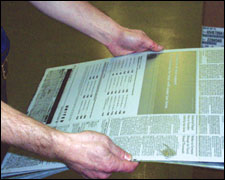
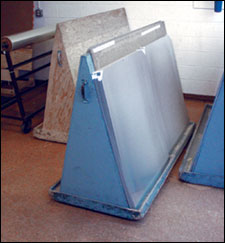
-
Adjust work surface height and angle to minimize forward bending and reaching. Suggested modifications include: (Figure 6).
-
Provide adjustable height and tilt workstations.
-
If workstation is too short, add blocks under the table legs to raise the work surface.
-
Where workstation must be shared between multiple workers, adjust height to accommodate tallest user and provide shorter users with platforms.
-
If provided, seating should be height adjustable.
-
Modify workstation to allow the worker the option to sit or stand or sit/stand.
-
Encourage workers to work while standing up straight and with the elbows in close to the body.
-
It is recommended that workers who are working in a bending body posture for a prolonged period, take frequent micro (one-minute) breaks to change body posture.
-
-
Use a razor tool with an ergonomically designed handle for cutting film. Handle should be bent to minimize wrist bending and should be large enough (1-1/2 to 2-1/2 inches in diameter) to facilitate maximum grip strength. Handle should be coated or textured to reduce slippage in the hand.
-
Design work layout to reduce the distances for hand-carrying film and plates around the prepress area. This will reduce the time and hand strength needed to carry these materials.
-
Hold and carry plates using non-pinch grip postures, whenever possible. (Figure 7).
-
Use a mobile cart to transfer plates from prepress to the press rather than carrying them. (Figure 8).
Press
A sheetfed press prints on individual sheets of paper. Stacks of sheets are placed in a loading area at the front end of the press and are fed into the press one sheet at a time. Bundles of paper are stored on pallets and delivered to the machine with some sort of mechanical device. Workers generally manually move material from supply pallets to the loading area of the press. Workers must use extended reaches and bending to access raw materials for loading machines such as cutters, folders, scoring machines and printing presses. In addition to extending the arms, the worker must often bend at the waist to access loading points.
Potential Hazards
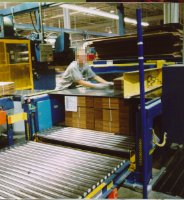
-
Extended reaches, especially with load in hand, increases the risk of shoulder and back overexertion.
-
Bending at the waist, with or without a load in hand, especially with twisting greatly increases the risk of bending hazards. (Figure 9).
-
Considerable finger force must be exerted to lift and control loads being placed into machines. The hazard is greatly increased if the wrist is bent either side-to-side or up-and-down.
Possible Solutions
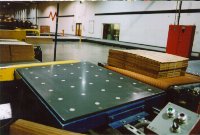
-
Reduce bending and reaching by providing workers with tools or devices for pushing and manipulating the materials.
-
Reduce the force necessary for positioning materials on a horizontal work surface by providing air lift tables. (Figure 10).
-
Tables should be designed and positioned to reduce bending and extended reaches.
-
Add blocks under the table legs to raise the work surface. Where workstation must be shared between multiple workers, adjust height to accommodate tallest user and provide shorter users with platforms.
-
Whenever possible, work surfaces should be no larger than necessary to reduce extended reaches.
-
-
Provide adjustable height workstations.
-
Minimize stack height manually moved at any given time to reduce finger stress.
-
Investigate tilting work surface to minimize wrist bending and reaching.
A webfed press uses large rolls of paper as a feed stock. These are usually stored in an area away from the press and must be transported to the press area. With large rolls, the process is usually mechanized once the roll is at the loading point.
Potential Hazards
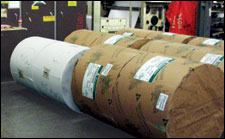
-
Physical strain associated with rolling and turning large rolls during transfer from storage area to press. (Figure 11).
-
Heavy lifting and carrying of the roll shafts or smaller rolls.
-
Forceful exertion required to insert the roll shafts into the core of the roll.
-
Potential contact trauma (e.g., using hand as hammer) if shaft is forced into core.
-
Arm and hand force required to cut cardboard off of rolls with saw blade or utility knife.
Possible Solutions
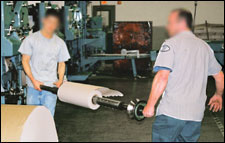
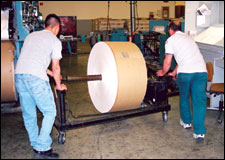
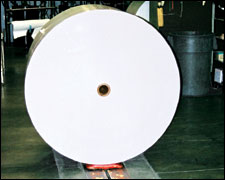
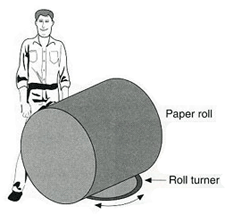
-
Reduce force needed to turn or redirect rolls by providing portable spinning disc or roll turner to position rolls.
-
Always use a 2-person lift for shafts weighing more than 50 pounds if they are to be handled manually. (Figures 12).
-
Eliminate manual carrying of shafts from loading area to staging area by using a 4-wheeled cart with an extended handle and gutter. (Figure 13).
-
Use a roll jack, roll trolley or other mechanical assistance to move rolls. (Figure 13 and 14).
-
Whenever possible, reduce weight of shafts that must be handled manually. For instance, substitute lighter aluminum shafts for steel shafts.
-
Provide an ergonomically designed cutting tool. Handle should be bent to minimize wrist bending and should be large enough (1-1/2 to 2-1/2 inches in diameter) to facilitate maximum grip strength. Handle should be coated or textured to reduce slippage in the hand.
- Provide education and training for workers concerning when manual pushing, pulling, and lifting materials is not appropriate (e.g., generally loads weighing about 50 pounds or push force requiring about 70 pounds).
- Applications Manual for the Revised NIOSH Lifting Equation. US Department of Health and Human Services (DHHS), National Institute for Occupational Safety and Health (NIOSH) Publication No. 94-110, (1994, January).
-
Ergonomic Design for People at Work, Volume 2. Eastman Kodak Company, (1986). Refer to page 380.
-
Minimize manual handling of rolls by designing a track system on a turntable platform on the floor or overhead crane system to mechanically move rolls within facility. (Figure 15).
Finished product from the press can take several forms. It may exit the press as a folded multiple sheet signature or as a single printed sheet. The future use of these products may impact the hazards associated with handling signatures or sheets. Both finished products will be deposited or stacked by the machine at the end of the process. From there they will generally be stacked on pallets or carts and moved to another area for further processing or may be packaged for shipping to another company or plant.
Potential Hazards
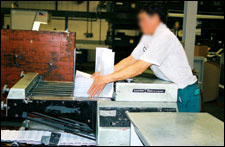
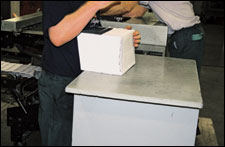
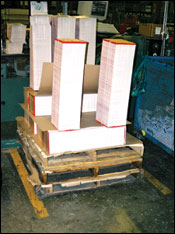
-
Workers use extended reaching across conveyors or other obstacles at the end of the various machines. This hazard is significantly worse if there is a load in the hand while reaching. (Figure 16).
-
Workers exert force with the arms out and away from the body to push bundles down conveyors where they are staged for stacking.
-
Workers may stack materials too high forcing them to use elevated and extended reaches while holding finished product.
-
As the height of materials (paper) lifted increases, the instability of the load increases. This can lead to sudden changes or shifting of the load, which can increase the risk of back or shoulder overexertion. (Figure 18).
-
Reaching to elevated stacks may force workers to bend the wrist to the side while exerting significant finger force.
-
Workers exert considerable physical force often while bending the torso and reaching out and away from the body to move heavy bundles of material from the accumulation areas or conveyors to the carts or pallets.
-
Workers use forceful, repetitive gripping with awkward hand posture to remove bundles from the accumulation areas or conveyors. (Figure 17).
-
Workers may lift heavy bundles of product by a securing strap. This can create a contact trauma to the palm and fingers.
Possible Solutions
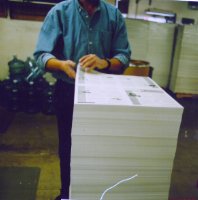
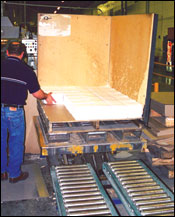
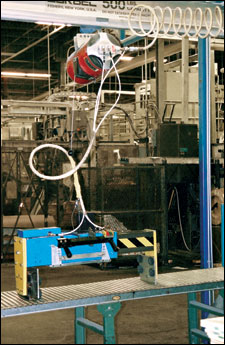
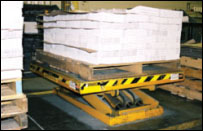
-
Whenever possible, remove all impediments between the worker and the load to be lifted. The load should be close enough to be lifted while keeping the elbows in close to the torso.
- During all lifting operations optimize bundle size and weight for 1-person lifting. Generally, bundled packages should not weigh more than about 50 pounds. Pick up several lighter loads. Avoid moving material over long distances. (Figure 19).
-
Applications Manual for the Revised NIOSH Lifting Equation. US Department of Health and Human Services (DHHS), National Institute for Occupational Safety and Health (NIOSH) Publication No. 94-110, (January 1994).
-
- Gloves should be provided if bundles are to be lifted by straps or other securing devices.
-
If gloves are used, they should be appropriately sized. If too small, gloves may constrict hand movement. If too large, excess material may gather in the palm.
-
-
Instruct workers to lift bundles by placing the hands under the load instead of grabbing securing straps.
-
Adjust the height of the loading area or provide a platform for the worker to stand on so the bundles are slightly below waist height of the worker. This will provide optimal leverage for the worker to lift and stage bundles. (Figure 20).
-
Use an overhead crane or hoist system to lift and stack bundles onto pallets. (Figure 21).
-
Locate pallets adjacent to the conveyor to minimize the distance of lifting and carrying bundles.
-
Position pallets on an adjustable-height surface to allow for matching the height of the bundles on the conveyor. This may allow bundles to slide directly onto the pallet with minimal lifting and will reduce forward bending. (Figure 22).
-
Add a turntable device for the pallet to be placed on. This will allow workers to constantly turn and reposition the pallet to minimize extended reaches.
-
Consider job rotation among employees to reduce lifting effort.
-
Provide training to employees on proper lifting techniques. This includes:
-
Keeping the load close to the body.
-
Bending the knees and keeping the back straight.
-
Pivoting the feet and not twisting the back.
-
Only lifting an amount of product that will allow workers to maintain comfortable hand posture and grip distances. Wrists should be straight with no bending either up or down or to the side. The hand should maintain the shape of a "C" with the thumb and fingers between 1.5 and 3 inches apart.
-
Finishing and Binding
Product that comes from the printing process must often be further processed before it can proceed to the bindery for final assembly. This process generally involves accessing material from a cart or pallet and manually lifting it to the loading end of a machine such as a folder or cutting table.
Potential Hazards
-
Workers bend at the waist to access items. Raw materials often arrive on pallets which are typically a few inches above the floor or machine access or discharge areas may be too low. (Figures 23, 24 & 25).
-
As the amount of materials (paper) increases, the worker's grip span also must increase. This causes gripping of the materials to be more difficult. An increased grip span is a risk factor for hand overexertion.
-
Workers who have the option to lift as much or as little material as they desire may lift heavier loads than necessary, particularly if they are under tight time constraints.
-
"Fanning" the raw, stock paper requires the use of awkward hand and wrist postures, such as wrist bending and forearm rotation, while exerting significant finger force. This task is needed to help separate sheets and to realign the leading edge of stacked material to facilitate orderly feeding into subsequent processes. This task increases the risk of overexertion of the muscles and tendons of the hand, wrist and forearm. (Figure 26, 27 and 28).
-
Small, repetitive manipulations are required continuously through the feeding process to ensure that all stock is properly aligned. Small tools used for this process can require wrist bending and forceful pinch grips with the fingers. This task increases the risk of developing injuries to the muscles and tendons of the hand, and wrist. (Figure 29 and 30).
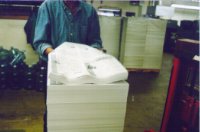
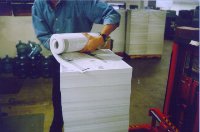
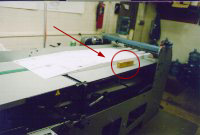
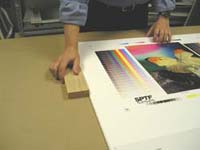
Possible Solutions
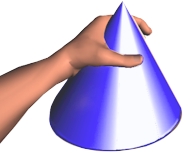
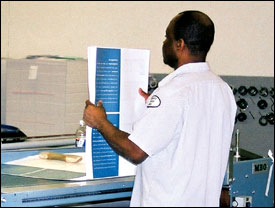
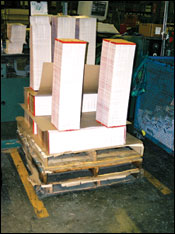
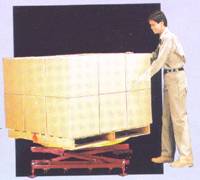
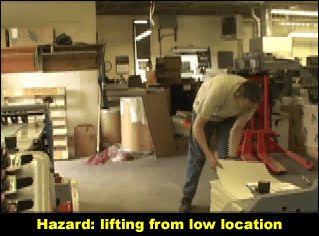
-
Determine how much material (paper) can be safely and effectively handled at one time. This will change depending on the type, weight, and size of paper used. The following will provide some guidance when making these determinations.
-
Maintain hand postures that provide maximal finger force. Generally, the hand span should be about 1.75 to 2.25 inches for maximum finger exertion and the hand should be in the shape of a "C". (Figure 31).
- Limit the amount of product that is lifted at one time to reduce the finger force exerted. Some recommendations for repetitive tasks that require pinch grips and that include force should be limited to about 2 to 4 pounds of force. Note: It takes about 2 pounds of force to hold a 12 oz. soda can and about 5 pounds of force to fully open a small binder clip. (Figure 32).
-
Ergonomic Design for People at Work, Volume 2. Eastman Kodak Company, (1986). Refer to page 255.
-
-
Ensure that the hand is maintained in a neutral posture where it is not bent either up or down or to either side. Bending the wrist reduces the amount of force that can be safely exerted by the fingers.
-
-
Provide a height- and tilt- adjustable table so employees can maintain neutral body posture while performing this task.
-
Educate all employees about the risks associated with performing tasks using awkward postures and forceful finger exertions. Supervisors must be educated in these principles since they need to ensure that workers perform tasks in the proper manner and they must evaluate proposed solutions to ensure that they do not introduce other risks on the job.
-
Whenever possible, elevate the pallets to minimize bending:
-
This can be achieved by simply placing loaded pallets on top of several empty pallets to raise the height of the raw materials. Secure the pallets to reduce the risk of falling materials. Do not stack above shoulder height. (Figure 33).
-
A height-adjustable lift table or cart could be used to keep the load close to waist level. This is particularly effective when the materials are stacked so high that most lifts cannot be performed with the arms in close to the torso.
-
-
Minimize reaching by keeping the load in close to the body. Some height-adjustable tables also rotate. This allows the load to be positioned close to the body by simply turning the pallet. (Figure 34).
-
Train employees in proper lifting techniques (Figure 35), such as:
-
Do not bend forward at the waist.
-
Keep the arms in close to the body.
-
Do not twist the torso while lifting.
-
-
Determine how much material (paper) can be safely and effectively moved at one time. Develop guidelines for employees and include these with job-specific ergonomic training for this task. A visual guide, such as a small red ruler placed next to the stack of raw materials will provide a visual check to remind employees not to grasp too much material at one time.
-
Provide a ramp-up period for new and returning employees so that they can gradually condition themselves to full operational production.
Signatures must be manually loaded in collating machines for assembly into a finished product. Signatures will be lifted from a pallet or cart and placed into a feed pocket.
Potential Hazards
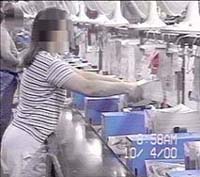
-
Twisting and bending at the same time to lift signatures from pallets or carts.
-
Excessive hand and finger exertion to fan signatures.
-
Extended and elevated reaches and forward bending to place the signatures into the pocket. (Figure 36).
-
Wrist bending while exerting finger force to hold and place stack of signatures into the pocket.
Possible Solutions
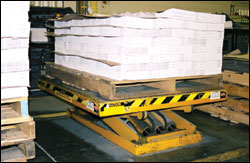
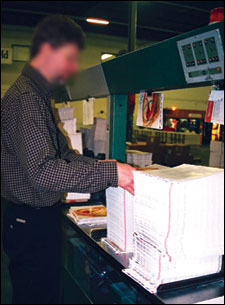
-
Locate pallets so that they are accessible from all sides so that horizontal reaching beyond 15 inches is minimized.
-
Elevate loads by placing pallets on platforms or palletizers to minimize bending to retrieve signatures. (Figure 37).
-
Provide training to employees on proper lifting techniques. This includes:
-
Keeping the load close to the body. Pull bundles close to the body before lifting them. (Figure 38).
-
Bending the knees and keeping the back straight.
-
Pivoting the feet to face the load and not twisting the back when lifting.
-
-
Install platform for shorter workers so that they can work at elbow height.
-
Consider job rotation to reduce exposure time to tasks that require repetitive lifting.
-
Provide a stream feeder to load signatures in pockets. These devices load material in a vertical alignment that minimizes wrist bending. Additionally, the loading height is lower so that elevated reach postures are minimized.
Some small jobs or rework jobs will be hand collated. This task involves placing all signatures in stacks around the worker. The worker then assembles the document by manually selecting each item from the appropriate pile. The finished document is then prepared for further processing.
Potential Hazards
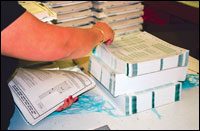
-
Repeated reaching to stacks to access individual signatures. (Figure 39).
-
Repeated elevated reaches to access stacks of materials if the table height is too high.
-
Repeated pinching with the thumb and fingers to pick up papers.
-
Standing for a prolonged period of time.
-
Neck and torso bending to view materials and reach stacks if tables are too low.
Possible Solutions

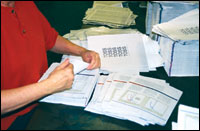
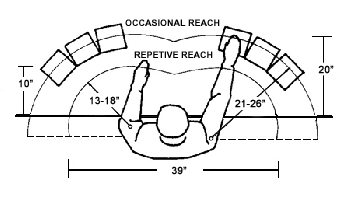
-
Wear a rubber tip on the end of the finger picking up papers for easy retrieval and reduced finger force. Use an office product that coats the finger with a sticky substance for ease in retrieving papers.
-
Provide a mat for the worker to stand on or have the worker wear shoe insoles to improve comfort when standing or walking.
-
Stack of materials should be placed within the employee's reach. Stacks should be arranged within easy reach; workers should be able to reach stacks without fully pulling the arm away from the body. (Figure 40, 41 and 42).
-
Adjust the work height to minimize neck and torso bending. A fully adjustable table will allow workers to change work surface heights easily as the heights of the stacks are reduced. Workers should adjust workstation height so that they can stand straight and keep the elbows close to the body while performing the task. (Figure 40).
-
Consider the option of a sit/stand stool to allow the worker the ability to change postures.
-
Provide a footrest when standing in one place to allow the worker the ability to alternate feet and thereby improve blood circulation.
-
Consider job modification or rotation to reduce the exposure time to this task.
-
Automate collating tasks whenever possible.
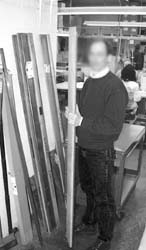
Paper may be purchased that is bigger than what is needed for a particular job or a finished job may need to be trimmed before it is processed further. These tasks are performed on a cutting table and will involve loading, aligning, and removing product as well as replacing blades.
Potential Hazards
-
Frequent wrist bending and fingering to fan the paper or signature for inserting.
-
Repeated use of awkward hand and arm postures with finger force to jog and fan product prior to placing it in the cutter.
-
Awkward hand and arm postures with finger force if inappropriate tools are used to align stacks as they are fed into the cutter.
-
Bending and reaching to lift while handling heavy cutting blades which can weigh up to 50 lbs. (Figure 43).
Possible Solutions
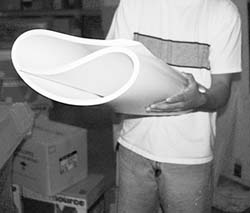
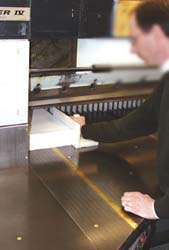
-
Elevate pallets of materials to minimize the amount of forward bending. This could be accomplished by:
-
Adjustable height palletizers.
-
Using carts with raised beds to transport materials to the cutter.
-
Placing pallets of materials on a stack of empty pallets.
-
-
Minimize the amount of finger force by using a trifold technique to move large sheets of stock from supply areas to the cutter. This allows the stock to be carried using a open hand cradling posture rather than pinch grips. (Figure 44).
-
Utilize an automated air assist table to reduce the force needed to slide stacks of stock around the cutting table. The material rides on a sheet of air similar to an air hockey, table greatly reducing the force needed to push stock.
-
Provide an automated jogging table to minimize hand manipulations.
-
Develop a clean and wax policy for the cutting table to ensure that the working surface is clear of scraps and dirt and that the surface is properly waxed to decrease the force required to move product around the machine by reducing the coefficient of friction. This essentially makes the horizontal surface slicker so that it is easier to push materials from place to place.
-
Use a blocking tool with a handle that allows the worker to maintain a straight wrist while pushing paper into position beneath the blade. (Figure 45).
-
Minimize the amount of reaching and lifting to remove scrap by placing the scrap bins adjacent to the cutter. Placing the bins on wheels will also minimize the amount of pushing and lifting which must be performed.
-
Use a 2-person lift when changing the blades to reduce the amount of weight lifted.
-
Avoid postures such as bending and reaching when handling heavy blades. Bending and reaching allows leverage to increase the hazard created by lifting heavy objects.
-
Consider using an elevator and knife stand to eliminate manually lifting and maneuvering heavy knives. This kind of stand can be positioned to support the weight while the blade is being detached from the rest of the apparatus and then can be used to mechanically lower the blade for replacement or maintenance. The reverse of this operation will allow for mechanical support during installation.
Products are generally palletized at the conclusion of the printing or collating process. They are stacked and often secured (either plastic wrapped, boxed, or bound with strapping) and then manually moved from the end of the press or collating machine to a pallet. This process is usually performed even if the materials are to be used within the same plant.
Potential Hazards
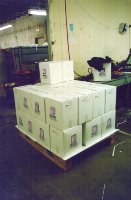
-
Workers reach out in front of the body to access and pull heavy materials from stackers or conveyors and to place heavy materials at the far side of pallets.
-
Workers often bend and twist to place finished materials onto pallets located at floor height. The height of material on the bottom of the pallet is typically only a few inches above the floor. (Figure 46).
-
Product is often packaged in volumes that create a significant hazard due to their weight (>50 pounds).
Possible Solutions
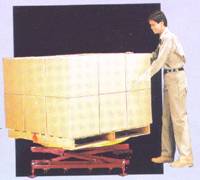
-
Whenever possible, elevate the pallets used for receiving processed materials to minimize bending.
-
The loading pallet can be placed on top of several empty pallets to raise the loading height. Secure the pallets to improve the stability of this arrangement and take care to ensure that palletized material is not stacked above about mid-chest height if this method is used.
-
Use height-adjustable lift tables to keep the load close to waist level. Some height-adjustable tables also rotate (Figure 47). This enables the worker to position the load close to the body by turning the pallet.
-
-
Ensure that there is sufficient room around the pallet so that workers do not need to reach across the pallet to place loads.
- Restrict the size of loads that are banded or packaged to limit the weight. Generally, loads should be limited to no more than about 40 to 50 pounds.
-
Applications Manual for the Revised NIOSH Lifting Equation. US Department of Health and Human Services (DHHS), National Institute for Occupational Safety and Health (NIOSH) Publication No. 94-110, (January 1994).
-
-
Reduce the number of lifts by using take-away conveyors (roller or powered) to move finished materials to the next processing station instead of palletizing and then depalletizing the load.