Oil and Gas Extraction
Safety Hazards Associated with Oil and Gas Extraction Activities
Oil and gas well drilling and servicing activities involve many different types of equipment and materials. Recognizing and controlling hazards is critical to preventing injuries and deaths. Several of these hazards are highlighted below. See Standards and Enforcement for more information on evaluation and control requirements.
- Vehicle Collisions
- Struck-By/ Caught-In/ Caught-Between
- Explosions and Fires
- Falls
- Confined Spaces
- Ergonomic Hazards
- High Pressure Lines and Equipment
- Electrical and Other Hazardous Energy
- Machine Hazards
- Planning and Prevention
Vehicle Collisions
Workers and equipment are required to be transported to and from well sites. Wells are often located in remote areas, and require traveling long distances to get to the sites. Highway vehicle crashes are the leading cause of oil and gas extraction worker fatalities. Roughly 4 of every 10 workers killed on the job in this industry are killed as a result of a highway vehicle incident (Census of Fatal Occupational Injuries). The following OSHA and NIOSH documents provide guidance on recognizing and controlling vehicle-related hazards:
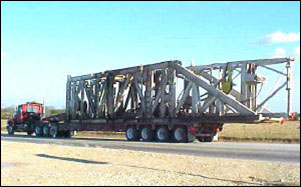
- Motor Vehicle Safety. OSHA Safety and Health Topics Page. Addresses hazards, controls and standards associated with motor vehicles.
- Work Zone Traffic Safety. OSHA QuickCard™ (Publication 3267). Covers traffic safety in brief.
- Fatal Facts, Oil Patch No. 1-2012. Report on a fatality attributable to a vehicle hazard.
- Motor Vehicle Safety. National Institute for Occupational Safety and Health (NIOSH) Workplace Safety & Health Topic. Lists NIOSH publications and current research into occupational motor vehicle safety.
- Work-Related Roadway Crashes: Prevention Strategies for Employers. U.S. Department of Health and Human Services (DHHS), National Institute for Occupational Safety and Health (NIOSH) Publication No. 2004-136, (March 2004). Provides statistics on work-related vehicle accidents and prevention options for employers.
- How to Prevent Fatigued Driving at Work – These fact sheets for employers and workers have information about fatigue and how to stay safe behind the wheel. They are also available in Spanish.
- Oil and Gas Well Drilling and Servicing eTool: Transportation Module. Reviews potential hazards and possible solutions for transporting personnel and equipment, vehicle operation at the well site, and all-terrain vehicles and utility task vehicles.
- Drive Safe. (September 2019). Video developed by Helmerich & Payne to promote safe driving in oil and gas extraction industry.
Struck-By/ Caught-In/ Caught-Between
Three of every five on-site fatalities in the oil and gas extraction industry are the result of struck-by/caught -in/caught-between hazards (OSHA IMIS Database). Workers might be exposed to struck-by/caught-in/caught-between hazards from multiple sources, including moving vehicles or equipment, falling equipment, and high-pressure lines. The following OSHA and NIOSH documents provide guidance on recognizing and controlling these hazards:
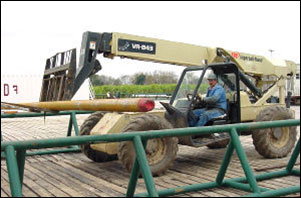
- Crane, Derrick, and Hoist Safety. OSHA Safety and Health Topics Page. Addresses hazards, controls, and standards associated with cranes, derricks, and hoists.
- Struck-By. OSHA's Harwood Grant Training Materials. Covers struck-by hazards in the oil and gas industry.
- OSHA Fatal Facts, Oil Patch No. 2-2012. Report on a fatality attributable to a struck-by hazard.
- OSHA Fatal Facts, Oil Patch No. 3-2012. Report on a fatality attributable to a struck-by hazard.
- Guidelines on the Stability of Well Servicing Derricks. OSHA Directive STD 03-12-003 [PUB 8-1.8], (July 15, 1991).
- Oil Well Derrick Stability: Guywire Anchor Systems. OSHA Technical Manual (OTM), TED 01-00-015 [TED 1-0.15A], (January 20, 1999).
Relevant OSHA standards applicable to these hazards include:
- Eye and face protection 1910.133
- Head protection 1910.135
- Foot protection 1910.136
- Hand protection 1910.138
- Handling materials - General 1910.176
- Powered industrial trucks 1910.178 App A
- Crawler locomotive and truck cranes 1910.180
- Slings 1910.184
- Machinery and machine guarding 1910 Subpart O
- General requirements for all machines 1910.212
- Mechanical power-transmission apparatus 1910.219
Relevant industry practice documents applicable to these hazards include:
- AESC Guidelines on the Stability of Well Servicing Derricks
- API RP 4G Maintenance and Use of Drilling and Well Servicing Structures
- API RP 8B Inspection, Maintenance, Repair, and Remanufacture of Hoisting Equipment
- API RP 53 Blowout Prevention Equipment Systems for Drilling Operations
- API RP 54 Recommended Practice for Occupational Safety for Oil and Gas Well Drilling and Servicing Operations
- API RP 74 Recommended Practice for Occupational Safety for Onshore Oil and Gas Production Operations
- ANSI/ASSE Z41, Personal Protection - Protective Footwear
- ANSI/ASSE Z89.1, Requirements for Industrial Head Protection
Explosions and Fires
Workers in the oil and gas industries face the risk of fire and explosion due to ignition of flammable vapors or gases. Flammable gases, such as well gases, vapors, and hydrogen sulfide, can be released from wells, trucks, production equipment or surface equipment such as tanks and shale shakers. Ignition sources can include static, electrical energy sources, open flames, lightning, cigarettes, cutting and welding tools, hot surfaces, and frictional heat. The following OSHA and NIOSH documents provide guidance on recognizing and controlling these hazards:
- Prevention of Fatalities from Ignition of Vapors by Mobile Engines and Auxiliary Motors. OSHA and National STEPS Network and NIOSH Alliance, (June 2017). A hazard alert on how to prevent fires and explosions caused by ignition of vapors by motorized equipment during drilling, servicing, and production operations.
- Well Site Ignition Sources. OSHA's Oil and Gas Drilling and Servicing eTool. Lists sources of ignition at well sites and possible controls.
- Hot Work, Fire, and Explosive Hazards. OSHA's Oil and Gas Drilling and Servicing eTool. Covers hazards associated with performing hot work at oil and gas well sites.
- Potential Flammability Hazard Associated with Bulk Transportation of Oilfield Exploration and Production (E&P) Waste Liquids. OSHA Safety and Health Information Bulletin, (March 24, 2008). Alerts oil and gas facilities about the flammability of oilfield waste liquids.
- Static Electricity Buildup in Plastic Pipe. OSHA Hazard Information Bulletin, (September 30, 1988). Addresses the potential for static electricity to ignite flammable gas.
- Fire Safety. OSHA Safety and Health Topics Page.
- OSHA Fatal Facts, Oil Patch No. 5-2012. Report on a fatality attributable to a flash fire from crude oil vapors.
- Hot Work in Oilfields. OSHA and National STEPS Network and NIOSH Alliance, (September 2016). A hazard alert on how to prevent fatalities associated with hot work on oilfield tanks, tankers and related equipment.
Relevant standards from OSHA, other federal agencies, and national consensus organizations, and OSHA letters of interpretation applicable to these hazards, include:
- Flammable liquids 1910.106
- Storage and handling of liquefied petroleum gases 1910.110
- Fire protection 1910 Subpart L
- Guidance on handling cases developed pursuant to the FRC enforcement policy memorandum [1910.132; 1910.132(a)], OSHA Letter of Interpretation, (December 18, 2012).
- Clarification of term "Active Hydrocarbon Zone" as it relates to the oil and gas well drilling operations; and the need to use FRC (flame-resistant clothing) when performing drilling operations [1910.132; 1910.132(a); 1910.106; 1910.119], OSHA Letter of Interpretation, (October 19, 2010).
- Enforcement Policy for Flame-Resistant Clothing in Oil and Gas Drilling, Well Servicing, and Production-Related Operations. [1910.132; 1910.132(a); 1910.132(d)], OSHA Letter of Interpretation, (March 19, 2010).
- OSHA's Flammable and Combustible Liquids Standard, 29 CFR 1910.106 related to pressure vessels used at oil and gas extraction/production facilities. OSHA Letter of Interpretation, (July 17, 2006).
- Applicability of 29 CFR 1910.119 Process Safety Management (PSM) Standard to the Manufacture of Explosives Required Under 29 CFR 1910.109(k)(2) . OSHA Letter of Interpretation, (November 8, 1995).
- Bureau of Alcohol, Tobacco, Firearms and Explosives 27 CFR 555, Commerce in Explosives.
- NFPA 1 Fire Code
- NFPA 10 Standard for Portable Fire Extinguishers
- NFPA 30 Flammable and Combustible Liquids Code
- NFPA 2112 Standard on Flame-Resistant Garments for Protection of Industrial Personnel Against Flash Fire
- NFPA 2113 Standard on Selection, Care, Use, and Maintenance of Flame-Resistant Garments for Protection of Industrial Personnel Against Flash Fire
Relevant industry practice documents applicable to these hazards include:
- API 53 Blowout Prevention Equipment Systems for Drilling Operations
- API 54 Recommended Practice for Occupational Safety for Oil and Gas Well Drilling and Servicing Operations
- API 67 Oilfield Explosives Safety
- API 74 Recommended Practice for Occupational Safety for Onshore Oil and Gas Production Operations
- API 500 Classification of Locations for Electrical Installations at Petroleum Facilities Classified as Class I, Division 1 and Division 2
- IADC Hot Work Hazard Recognition
Falls
Workers might be required to access platforms and equipment located high above the ground. OSHA requires fall protection to prevent falls from the mast, drilling platform, and other elevated equipment. The following OSHA and NIOSH documents provide guidance on recognizing and controlling this hazard:
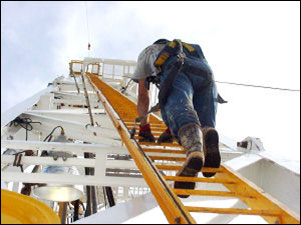
- Fall Protection. OSHA Safety and Health Topics Page. Addresses fall control and specific standards for general industry and construction.
- Falls. OSHA's Harwood Grant Training Materials. Covers sources of slips, trips, and fall hazards in the oil and gas industry.
- Walking and Working Surfaces and Fall Protection. OSHA's Harwood Grant Training Materials. Covers slips, trips, and fall hazards in the oil and gas industry and associated OSHA standards.
- OSHA Fatal Facts, Oil Patch No. 4-2012. Report on a fatality attributable to this hazard.
- Fall Injuries Prevention in the Workplace. National Institute for Occupational Safety and Health (NIOSH) Workplace Safety & Health Topic. Lists NIOSH publications and current research into occupational fall prevention.
- Occupational Fatalities Resulting from Falls in the Oil and Gas Extraction Industry, United States, 2005–2014. Centers for Disease Control and Prevention (CDC) Morbidity and Mortality Weekly Report (MMWR), (April 28, 2017).
Relevant OSHA and national consensus standards applicable to this hazard include:
- Walking-working surfaces 1910 Subpart D
- Powered platforms, manlifts and vehicle-mounted work platforms 1910 Subpart F
- ANSI/ASSE Z359.1, Safety Requirements for Personal Fall Arrest Systems, Subsystems and Components
Relevant industry practice documents applicable to this hazard include:
- IADC (International Association of Drilling Contractors) Working at Height
- API 54 Recommended Practice for Occupational Safety for Oil and Gas Well Drilling and Servicing Operations
- API 74 Recommended Practice for Occupational Safety for Onshore Oil and Gas Production Operations
Confined Spaces
Workers are often required to enter confined spaces such as petroleum and other storage tanks, mud pits, reserve pits and other excavated areas, sand storage containers, and other confined spaces around a wellhead. Safety hazards associated with confined space include ignition of flammable vapors or gases. Health hazards include asphyxiation and exposure to hazardous chemicals. Confined spaces that contain or have the potential to contain a serious atmospheric hazard must be classified as permit-required confined spaces, tested prior to entry, and continuously monitored. The following OSHA and NIOSH documents provide guidance on recognizing and controlling this hazard:
- Confined Spaces. OSHA Safety and Health Topics Page. Addresses specific standards for the general industry and shipyard employment.
- Permit-Required Confined Spaces in General Industry. OSHA QuickCard™ (Publication 3214). Covers confined space entry in brief.
- Confined Space. OSHA's Harwood Grant Training Materials. Covers confined space entry in the oil and gas extraction industry.
- Permit-Required Confined Space Entry. OSHA's Harwood Grant Training Materials. Covers confined space entry in the oil and gas extraction industry.
- Confined Spaces. National Institute for Occupational Safety and Health (NIOSH) Workplace Safety & Health Topic. Lists NIOSH publications and current research into confined spaces.
Relevant OSHA and national consensus standards applicable to this hazard include:
- Permit-required confined spaces 29 CFR 1910.146
- ANSI/ASSE Z117.1 Safety Requirements for Confined Spaces
- NFPA 326 Standard for Safeguarding of Tanks and Containers for Entry, Cleaning, or Repair
Relevant industry practice documents applicable to this hazard include:
- API 1615 Safe Entry and Cleaning of Petroleum Storage Tanks, Planning and Managing Tank Entry from Decommissioning Through Recommissioning
Ergonomic Hazards
Oil and gas workers might be exposed to ergonomics-related injury risks, such as lifting heavy items, bending, reaching overhead, pushing and pulling heavy loads, working in awkward body postures, and performing the same or similar tasks repetitively. Risk factors and the resulting injuries can be minimized or, in many cases, eliminated through interventions such as pre-task planning, use of the right tools, proper placement of materials, education of workers about the risk, and early recognition and reporting of injury signs and symptoms. The following OSHA and NIOSH documents provide guidance on recognizing and controlling these hazards:
- Strains and Sprains. OSHA's Oil and Gas Well Drilling and Servicing eTool. Lists solutions for preventing strains and sprains in the oil and gas industry.
- Ergonomics. OSHA Safety and Health Topics Page. Covers related standards and guidelines for preventing ergonomic injury.
- Ergonomics and Musculoskeletal Disorders. National Institute for Occupational Safety and Health (NIOSH) Workplace Safety & Health Topic. Lists NIOSH publications and current research into ergonomics.
High Pressure Lines and Equipment
Workers might be exposed to hazards from compressed gases or from high-pressure lines. Internal erosion of lines might result in leaks or line bursts, exposing workers to high-pressure hazards from compressed gases or from high-pressure lines. If connections securing high-pressure lines fail, struck-by hazards might be created. The following OSHA documents provide guidance on recognizing and controlling these hazards:
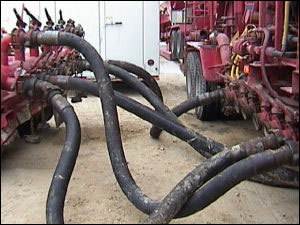
- Compressed Gas and Equipment. OSHA Safety and Health Topics Page. Reviews standards and hazard-control measures associated with compressed gas and equipment.
- Pressure Vessels. OSHA Safety and Health Topics Page. Reviews standards and hazard-control measures associated with pressurized tanks and containers.
Relevant industry practice documents applicable to these hazards include:
- API 53 Blowout Prevention Equipment Systems for Drilling Operations
- API 54 Recommended Practice for Occupational Safety for Oil and Gas Well Drilling and Servicing Operations
- API 59 Recommended Practice for Well Control
- API 74 Recommended Practice for Occupational Safety for Onshore Oil and Gas Production Operations
- IADC Guide to Blowout Prevention
- IADC Blowout and Well Control Handbook
- IADC Well Control for the Man on the Rig
- IADC Well Control for the Rig-Site Drilling Team
- IADC Well Control Manual
Electrical and Other Hazardous Energy
Workers might be exposed to uncontrolled electrical, mechanical, hydraulic, or other sources of hazardous energy if equipment is not designed, installed, and maintained properly. Further, administrative controls such as operating procedures must be developed and implemented to ensure safe operations. The following OSHA and NIOSH documents provide guidance on recognizing and controlling these hazards:
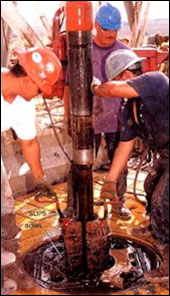
- Control of Hazardous Energy (Lockout/Tagout). OSHA Safety and Health Topics Page. Reviews general industry standards, explains lockout/tagout concepts, and provides guidance on developing a lockout/tagout program.
- Hazardous Energy. OSHA's Harwood Grant Training Materials. Covers control of hazardous energy in the oil and gas industry.
- Lockout/Tagout. OSHA's Harwood Grant Training Materials. Covers control of hazardous energy and lockout/tagout procedures in the oil and gas industry.
- Electrical Safety. National Institute for Occupational Safety and Health (NIOSH) Workplace Safety & Health Topic. Lists NIOSH publications and current research into occupational electrical safety.
Relevant OSHA and national consensus standards applicable to these hazards include:
- The control of hazardous energy (lockout/tagout) 1910.147
- Typical minimal lockout procedures 1910.147 Appendix A
- Electrical 1910 Subpart S
- NFPA 70 National Electrical Code®
Relevant industry practice documents applicable to this hazard include:
- API 53 Blowout Prevention Equipment Systems for Drilling Operations
- API 54 Recommended Practice for Occupational Safety for Oil and Gas Well Drilling and Servicing Operations
- API 74 Recommended Practice for Occupational Safety for Onshore Oil and Gas Production Operations
Machine Hazards
Oil and gas extraction workers may be exposed to a wide variety of rotating wellhead equipment, including top drives and Kelly drives, drawworks, pumps, compressors, catheads, hoist blocks, belt wheels, and conveyors, and might be injured if they are struck by or caught between unguarded machines. The following OSHA and NIOSH documents provide guidance on recognizing and controlling these hazards:
- Barrier Guard for Drawworks Drum at Oil Drilling Sites. OSHA Hazard Information Bulletin, (July 13, 1995). Highlights the need for barrier guards for drawworks drums to prevent caught-between hazards at oil drilling sites.
- Caught-Between. OSHA's Harwood Grant Training Materials. Covers sources of caught-between hazards at oil and gas drilling sites.
- Machine Guarding. OSHA's Harwood Grant Training Materials. Covers principles of machine guarding in the oil and gas industry and associated OSHA standards.
- Machine Safety. National Institute for Occupational Safety and Health (NIOSH) Workplace Safety & Health Topic. Lists NIOSH publications and current research into occupational machine safety.
Relevant OSHA and national consensus standards applicable to these hazards include:
- Machinery and machine guarding 1910 Subpart O
- Hand and portable powered tools and other hand-held equipment 1910 Subpart P
Relevant industry practice documents applicable to these hazards include:
- API 54 Recommended Practice for Occupational Safety for Oil and Gas Well Drilling and Servicing Operations
- API 74 Recommended Practice for Occupational Safety for Onshore Oil and Gas Production Operations
- API 11ER Guarding of Pumping Units. (ANSI/API RP 11ER-1992) (includes Supplement 1, July 1, 1991).
- IADC Hand Safety & Injury Prevention for the Oil and Gas Industry
Planning and Prevention
For process-specific and task-specific hazards and controls, see OSHA's Oil and Gas Well Drilling and Servicing eTool. The eTool identifies common hazards and possible solutions to reduce incidents that could lead to injuries or deaths. Each drilling and servicing company should have its own safety program:
- Know the hazards. Evaluate the hazards at the worksite. Many companies within the oil and gas industry use the Job Safety Analysis Process (also referred to as a JSA, Job Hazard Analysis, or JHA) to identify hazards and find solutions.
- Establish ways to protect workers, including developing and implementing safe practices for:
- Confined space; excavations
- Chemical handling; exposure
- Chemical storage
- Electrical work
- Emergency response
- Equipment/machine hazards
- Fall protection
- Fire protection
- Hot work, welding, flame cutting operations
- Personal protective equipment use
- Power sources (lockout/tagout provisions, safe distance from power lines)
- Working in the heat, long shifts
- Provide personal protective equipment (PPE). When engineering controls alone cannot protect worker overexposure to chemicals, noise, or other hazards, the employer must provide PPE.
- Communicate the hazards, and train workers.
- Have a plan for contractor safety and training.