Oil and Gas Well Drilling and Servicing eTool
General Safety and Health » Safety and Health Program
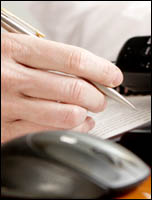
When work activities have been identified, contractors are selected by the operator for the work to be performed. Select the right contractors to ensure that the work is done right and with attention to personnel safety and health.
Possible Solutions
It is important for operators to develop systems to vet service contractors. See American Petroleum Institute Recommended Practice (API RP) 76, Contractor Safety Management for Oil and Gas Drilling and Production Operations for more information on the contractor selection process
- Once vetted and selected, perform a needs assessment or gap analysis to identify gaps between the operator's safety and health management system and the contractors' systems.
- Develop and implement an action plan to close the gaps and align the systems. This is frequently referred to as "bridging the contractors."
- Ensure that this action plan results in communication with, and training of, workers in the field.
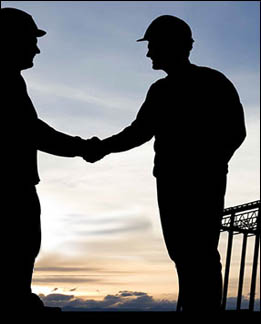
Most well operations include multiple contractors performing specific jobs associated with the overall operation. Keeping contractors aware of the whole operation, and coordinating efforts, will improve work performance and worker safety and health.
Possible Solutions
- Work together with contractors to ensure that their safety and health management systems align with the operator's requirements.
- Ensure that contractors are pulled into, and participate in, the job planning and risk assessment steps as early as possible.
- Ensure that work rules and procedures are clearly communicated and make it clear to contractors that they are expected to live by these rules to avoid confusion and conflicting rules.
- As the job proceeds, regular communication is critical to avoid contractor overlap and conflict. Therefore, facilitate coordination and cooperation through regular toolbox talks (often referred to as tailgates) or other routine meetings.
- Daily tailgates with all on-site contractors can help coordinate activities. Include in each tailgate a discussion of any unusual hazards that the contractors might encounter that day. This is becoming more important as multi-well and simultaneous operations increase.
- When conditions and/or job scope change, ensure that contractors stop the job. Work together to adequately address and communicate the new conditions and hazards. Ensure that all contractors agree with change(s) in operations.
Drilling and servicing operations begin with planning of operations to be performed at the well site. Include safety and health considerations in this planning stage and throughout the operations.
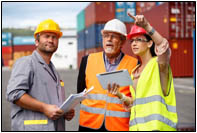
Possible Solutions
- Ensure that site planning addresses safety and health issues, including (but not limited to):
- Considering the hazards associated with multiple contractors involved in simultaneous operations. (Operations typically involve multiple contractors).
- Considering the hazards associated with working on or around roads and walkways, ensuring the placement of heavy machinery in safe locations, and using equipment appropriate for the work conditions and operations to be performed.
- Locating and properly addressing the hazards associated with flammable storage tanks, chemicals, exhausts, flares, and so forth.
- Reviewing control system, alarm, and emergency shutdown adequacy and functionality.
- As the various phases of operations are planned, discuss and update the status of risk assessments (RAs), hazard analyses (HAs), job safety analyses (JSAs), operating procedures, worker training, emergency services and response, as well as other safety and health considerations.
Extensive and in-depth analysis at the initial planning stage helps ensure a safe and successful job is completed.
Very little is routine about well site operations. The lay of the land, the site geology, the formation properties, the operations to be performed, the equipment selected for use, the experience of the crews, the weather, and many other factors create risks and hazards to consider and assess before work begins.
Possible Solutions
- Well operations are made up of many jobs happening together in an environment that needs to be assessed. An RA or HA of the entire operation is important to ensure that all safety and health hazards associated with the specific well operations being performed at the site are considered.
- As well, RAs, HAs, and JSAs are valuable tools for specific jobs. Use RAs/HAs/JSAs consistently throughout well site operations. Employers and workers together make a good RA/HA/JSA team. Ensure that the RAs/HAs/JSAs are not templates that discuss only the general hazards of a job. Address the step-specific hazards and controls of the tasks to be performed. See Sample JSA module.
- Since work is seldom routine, obstacles encountered and changing conditions may result in changes to job tasks as the operation proceeds. Ensure that workers stop work when this happens and work together to reassess the risks and hazards. Preventable incidents frequently happen because the job changed but the hazards and risks were not adequately reassessed.
Most drilling and servicing companies have work rules and procedures for typical operations that they perform. Whether written or not, ensure that workers are informed of, and understand, these rules and procedures for their own safety and health.
Possible Solutions
- Review and update the rules and procedures, and communicate them to workers, before each job. Because each operation may be a little different, use a management of change (MOC) process, when needed. See API RP 76 for more information about the MOC process.
- Deviations from procedures because of unique conditions or situations at the well site often lead to unforeseen consequences. Ensure that workers do not feel that they will be terminated, docked, or otherwise punished for stopping work when they believe their safety or health is at risk. Stop work to assess the new or changing conditions and develop a modified operation plan or procedure to help prevent undesirable consequences.
- Most important: Follow and enforce the rules and procedures. Although at times this may be unpopular or uncomfortable to do, remind others (e.g., your employer, your workers, fellow workers, contractors, and operators) that the rules and procedures exist to ensure the safety and success of the job.
New workers, and even seasoned employees, need to be made aware of the operations to be performed, the hazards that may be encountered, and the steps required to safely perform the job.
Possible Solutions
- When the operator, contractor, supervisors, and/or foremen can't adequately train their workers, assign someone else to do so. The hazards at well sites are too significant to rely on the "school-of-hard-knocks" or the "learning-by-experience" methods.
- Training can be performed in many ways, with the quality of the training often dependent upon the method used and the worker's method of learning. Some people can learn by hearing or reading alone. Others are best trained by seeing, touching, and then practicing. Many oilfield workers are hands-on personnel who will be trained best by seeing, touching, and practicing.
- As part of the contractor vetting process, include an assessment of the contractor's use of safety and health management systems (see API RP 76), how their workers are trained, and how the worker's skills and knowledge are evaluated.
- Well site operations are seldom routine, and jobs and/or conditions change. When workers encounter situations that are new or have not been done by the workers before, ensure that the workers stop. Help the workers go through new steps while evaluating the hazards and risks and ensure that the workers get the training needed to do the job safely and adequately.
- Train what you do. Do what you train.
Include in any safety and health management program a process for reporting incidents and injuries, with an emphasis on preventing retaliation. More incidents of the same kind can be prevented only if they are known. Unless workers feel free to report incidents, they may not receive adequate medical attention; and worker injuries, equipment damage, and further incidents can occur with increased severity if not reported promptly. Reporting near misses and near hits prevents incidents from happening in the first place.
Possible Solutions
- Ensure that rules for incident and near miss/near hit reporting are well established and understood. Include reporting of near misses and/or near hits in the safety management system.
- Encourage workers to report near misses/near hits.
- Eliminate incentives or policies that discourage reporting. Develop a culture where workers do not fear reprisals for reporting incidents and near miss/near hits.
- Report incidents to supervisors as soon as possible.
- Ensure that supervisors respond to these reports promptly. Work in the oil patch proceeds quickly. A timely investigation and corrective actions can help prevent additional incidents and injuries and reduce their frequency and severity.
- Consistent tracking of near misses/near hits serves as a leading indicator that can suggest improvements needed to prevent incidents from occurring.
- Ensure that investigations of incidents and near misses/near hits are conducted by employees knowledgeable of the site conditions and processes. Share investigation findings with all parties on site and at other operator/contractor well sites.
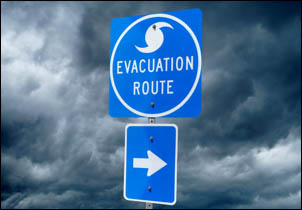
The severity and seriousness of emergency events can be significantly reduced when the employer has a well-implemented emergency response/action plan.
Possible Solutions
- Ensure that this plan includes, among other provisions, provisions for emergency evacuation, first aid and medical treatment, fire extinguishers, trained responders (if workers are designated as responders), weather events, threats from workers or from outside, security measures, and other emergency situations that could arise. (See 29 CFR 1910.38).
- Train workers on how to immediately respond to emergencies. A quick and adequate response can reduce the severity of many emergencies and can protect workers from injury. It is important that employers contact local emergency response entities and ascertain their response capabilities, equipment, and estimated site response times.
- It is also important that employers ensure they have the capability to keep access to the site available to emergency responders during inclement weather conditions, such as clearing of snow drifts.
- Where eye or body wash stations are required, ensure they are capable of operation during cold weather conditions.
- Conduct drills frequently to practice the plan. Hold a review after the drill to identify gaps and areas for improvement.
- Keep an emergency contact list. Ensure the list is kept up to date and reviewed frequently.
Housekeeping is everyone's responsibility. Preventable incidents often occur due to housekeeping issues.
Possible Solutions
- Ensure that personal workspace is as neat and clean as possible.
- Keep aisles, exits, and passageways open and clear.
- Pick up tools and other equipment that could fall from heights or become tripping hazards. Secure tools and other equipment that could drop from elevated surfaces, such as from tables, shelves, beams, tongs, platforms, etc.
- Ensure that flooring is adequate for the work environment. Use anti-slip flooring where slippery surfaces could occur.
- Clean up spills and fix leaks promptly and use proper disposal methods for the material being disposed.
- Install warning signs at walking surface height changes and at blind spots.
- Store combustible materials only in amounts needed and away from incompatible materials. Refer to safety data sheets (SDSs) for proper storage.
- Ensure proper labeling of chemical containers.
- Be cognizant of storing flammable materials where ignition sources could be present.
- Return unused chemicals to the vendor or dispose of unused chemicals properly when the job is complete.
- Dispose of trash, including used personal protective equipment (PPE), properly in designated trash cans or other designated dispensers/containers.
- Secure trash openings with lids to prevent scattering (for example, by wind) or pilfering (for example, by wildlife).
- Lack of cleanliness in doghouses can, on occasion, make movement in the doghouse restricted and congested.
Always maintain this area to ensure that the driller can quickly access information and controls as needed. - Maintain all doghouses, including those in remote locations, in a clean and orderly condition.
- See also: 29 CFR 1910.22 and 29 CFR 1910.176.
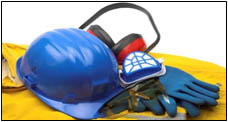
Provide, use, and maintain PPE in a sanitary and reliable condition whenever it is necessary to protect workers from hazardous conditions. Train workers that use PPE on how to use and care for it (among other things). See 29 CFR 1910.132. Failure to specify and use the right PPE has resulted in many needless incidents.
Possible Solutions
- Perform a PPE hazard assessment to determine if hazards are present, or are likely to be present, which necessitate the use of PPE for specific operations. Select, and have each affected employee use, appropriate PPE (such as hard hats, eye protection, safety shoes, work gloves, personal fall protection, and special-purpose PPE for activities such as hot work, working at heights, and electrical work) that will protect them from the hazards identified in the hazard assessment. See 29 CFR 1910.132(d).
- Although many employers have a corporate or general PPE program in place, assess the hazards at each work site to ensure that the PPE is adequate for that site. Reassess PPE requirements if changes occur at the site because hazards may also change.
- Ensure contractor PPE is also appropriate and in good condition.
- Require high-visibility wear in any areas where employees have potential exposure to vehicle traffic, including high-visibility, flame-resistant clothing (FRC) when needed.
-
Training is critical so that workers understand the hazards and the reasons for use of the PPE, as well as the proper use and care of the PPE.
- When falling object hazards are possible, ensure that workers wear American National Standards Institute (ANSI) approved hardhats, safety glasses, and steel-toed shoes.
- Gloves fit for the specific purpose are usually needed because of heavy equipment, impact hazards, slick and oily surfaces, and other site hazards.
- Require fall protection when working at heights on rigs (see the Slips, Trips and Falls section for more information.)
- Require FRC in any areas where flash fire hazards could be present or where a RA/HA/JSA has indicated that they should be used. To properly maintain flame-resistant integrity, follow the manufacturer's recommendations for washing and care.
- Require respirators in areas where a toxic atmosphere could be present, or when effective engineering controls are not feasible to prevent atmospheric contamination. See 29 CFR 1910.134.
- To select an appropriate respirator:
- Conduct an exposure assessment to determine the type and amount of hazardous exposure.
- Consider the factors that can influence respirator selection, such as job site and worker characteristics.
- Understand the assigned protection factors.
- Know the various kinds of respirators and their relevant characteristics.
- Refer to the Respiratory Protection eTool and to the PPE Hazards and Solutions Safety and Health Topics Page for more information.
- Training on, among other topics, the proper care, use, and storage of respirators is essential to worker protection. (See 29 CFR 1910.134(k)).
- Implement appropriate cartridge change-out schedules to ensure that workers' PPE is providing the required protection.
- Ensure appropriate fit-testing of respirators before use. Ensure workers do not wear tight fitting respirators if they have facial hair that comes between the sealing surface of the facepiece and the face, or that interferes with valve function, or if the workers have any condition that interferes with the face-to-facepiece seal or valve function. See 29 CFR 1910.134(g)(1). In such cases, facial hair will have to be removed or another type of respirator will have to be selected.
- In situations where exposure to air contaminant hazards is possible (e.g., where toxic or flammable atmospheres could exist), area monitors and/or personal monitors can provide workers with an early warning of the hazards. Most monitoring devices have limitations and selecting the right monitors for the expected conditions is important when addressing the assessed hazards.
-
Ensure electrical PPE and other electrical protective equipment is available and used appropriately to reduce the risk of exposure to electrical hazards. See OSHA standards covering protection from electrical hazards for more information about the appropriate design and use of electrical protective equipment (e.g., 29 CFR 1910.137, 29 CFR 1910 Subpart S, 29 CFR 1910.269), as well as relevant consensus standards (e.g., National Fire Protection Association (NFPA) 70E).
- Provide special PPE for hot work activities. See the Hot Work section below for more information.
Establishing a safety and health management system, as part of the company's overall safety and health program, is an essential tool for any employer. For further guidance, see the following resources.
- Recommended Practices for Safety and Health Programs,
- Oil and Gas Extraction Safety and Health Topics Page, or
- Contact your workers' compensation insurance provider.
OSHA Consultation Services offers no-cost and confidential occupational safety and health services to small- and medium-sized businesses in all 50 states, the District of Columbia, and several U.S. territories, with priority given to high-hazard worksites. Consultants from state agencies or universities work with employers to identify workplace hazards, provide advice for compliance with OSHA standards, and assist in establishing and improving safety and health programs. On-Site Consultation Services are separate from OSHA's enforcement efforts and do not result in penalties or citations.
Many of OSHA's Safety and Health Topic Pages can help when considering hazards to be included in a Safety and Health Management System.