Oil and Gas Well Drilling and Servicing eTool
Servicing » General Services
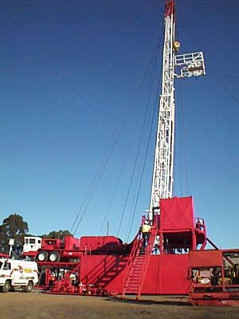
Maintenance activities associated with the well when using a workover/service rig are:
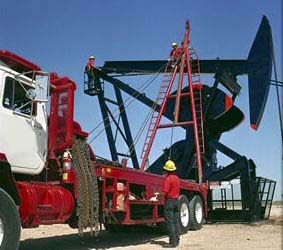
Typically, the horsehead of a pumping unit must be removed to gain access to the wellhead equipment.
Potential Hazards
- Having the unit start up while working on equipment.
- Being struck by counterweights on the pumping unit.
Possible Solution
- Use lockout/tagout, to include mechanically securing the flywheel.
Potential Hazards
- Being struck by dropped horsehead or caught between horsehead and walking beam.
- Getting fingers and hands pinched and caught between tools and/or equipment.
- Being struck by falling tools or equipment.
- Falling from an elevation.
Possible Solutions
- Inspect all slings before use.
- Use tag lines to position the horsehead when removing or lowering and to keep personnel clear of suspended load.
- Use the correct tools for each task.
- Inspect the tools before each use.
- Keep fingers and hands away from pinch points.
- Secure tools from falling and keep the area below clear of personnel.
- Use proper personal protective equipment and fall protection as required.
Additional Information
- Standards. American Petroleum Institute (API).
- RP 54, Occupational Safety for Oil and Gas Well Drilling and Servicing Operations. (March 2007).
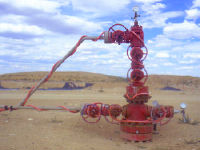
To begin the process, the wellhead must be removed from the casing flange
Potential Hazards
- Being struck by released pressure or flying particles.
- Being struck by the wrench or hammer while removing bolts and fittings.
- Getting caught between wellhead, hydraulic wrenches, and wellhead fittings.
- Getting fingers and hands pinched and caught between flanges or valves.
- Slips, trips, and falls.
- Entering into well cellars.
Possible Solutions
- Stand clear of valves and fittings when removing fitting or bleeding off pressure.
- Check wellhead pressure and bleed pressure off before removal.
- Use the correct tools for each task.
- Inspect the tools before each use.
- Wear appropriate personal protective equipment, including safety glasses.
- Keep fingers and hands away from pinch points.
- Cover open cellars.
- Wear appropriate fall protection.
- Implement a confined space entry program.
#56. Surface Casing
Usually the first casing to be run in a well. This is done after spudding-in so a blowout preventer can be installed before drilling is started.†
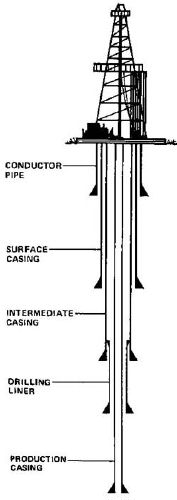
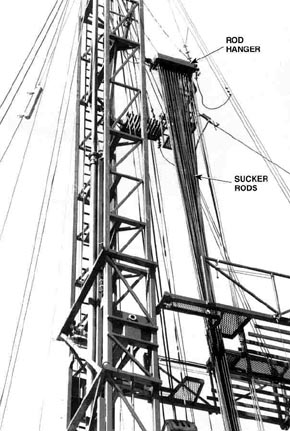
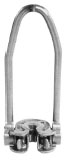
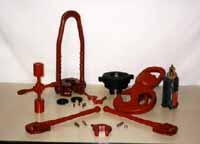
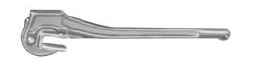

To service, repair, or replace the rods or pump, the sucker rod string must be pulled out of the hole. Pulling rods refers to the process of removing rods from the well. Running rods refers to the process of replacing rods in the well.
Potential Hazard
- Falling from heights.
Possible Solutions
- Wear appropriate fall protection including a full body harness. For Fall Protection guidance, consult:
- 29 CFR 1910.23(c)(1), Fall protection when working from platforms
- 29 CFR 1910.66 Appendix C, Fall protection guidelines
- 29 CFR 1910 Subpart D, Walking-working surfaces
- Never disconnect personal fall arrest systems while working in the derrick.
Potential Hazard
- Getting fingers or hands pinched in or between rod wrenches, rod elevators, power tongs, rod hook, rod transfer, and rod fingers.
Possible Solutions
- Ensure that workers are instructed in proper hand and finger placement when making and breaking rod connections or setting rods on the rod fingers.
- Ensure that workers are instructed in proper latching procedures while pulling and running rods.
Potential Hazard
- Being struck by dropped objects.
Possible Solutions
- Wear appropriate personal protective equipment such as:
- Hard hat
- Work gloves
- Safety-toed footwear
- Use extra caution while people are working overhead.
- Avoid carrying tools while climbing the derrick ladder. Raise tools with a line to any worker above the derrick floor.
- Ensure that all tools and equipment being used are secured with the proper safety lines.
Additional Information
- Standards. American Petroleum Institute (API).
- RP 54, Occupational Safety for Oil and Gas Well Drilling and Servicing Operations. (March 2007).
- TV 304, Rod Wrenching: Safe and Sound. Association of Energy Services Companies (AESC) Training Video.
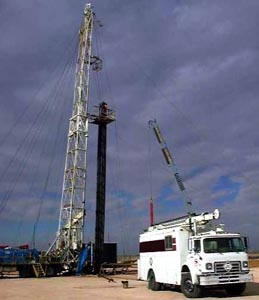
Among the reasons for pulling tubing includes replacing a packer, locating a tubing leak, or plugged tubing.
Raising or Lowering Traveling Block and Elevator
Potential Hazards:
- Being struck by the elevators and traveling block as they are raised or lowered.
- Getting fingers and hands pinched between elevators and tongs or tubing collar.
Possible Solutions:
- Instruct workers to stand clear of tong and slip area when lowering the elevator and traveling block.
- Use handles on elevators as they are descending into place over the tubing.
Latching or Unlatching Elevators onto the Tubing
Potential Hazards:
- Pinching hands or fingers in the elevators.
- Being struck by elevators not securely latched.
Possible Solutions:
- Ensure that workers are instructed in proper latching procedure.
- Inspect and maintain elevators.