Oil and Gas Well Drilling and Servicing eTool
General Safety and Health » Common Wellsite Incidents and Fatalities
Historically the most common incidents and fatalities in the oil patch include the following.
Be aware that the type of work activity being performed will determine the major risks experienced during that activity. For example, when rigging up, the potential of a fire or explosion may be low. However, when drilling or servicing a flowing well, the potential for a fire or explosion will be much higher. The risk of injury or death from struck-by and caught-in hazards is typically going to be high during most phases of well drilling and servicing operations.
Possible Solutions
- Because the risks associated with any job can be distinct and different, prepare and review RAs/HAs/JSAs with workers to address the job-specific hazards and controls of the work activities being performed.
- Follow the possible solutions listed in this eTool for the hazards you will be encountering.
The most frequent causes of preventable incidents and fatalities are discussed in more detail in the following paragraphs.
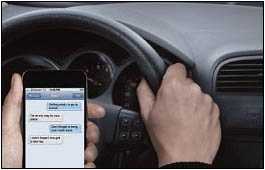
Traffic incidents are the number one cause of fatalities in the upstream oil and gas industry, accounting for almost half of all fatalities. Most of these incidents occur on public roads. Ensure that workers are aware of these hazards and exercise caution when travelling, which often occurs at night, or in bad weather, with heavy loads, on secondary roads, and when a worker is fatigued. See OSHA Oil Patch Fatal Facts, No. 1 – 2012, which involved a double fatality incident where a rig crew was driving home after their work shift.
Major contributors to preventable incidents and fatalities are:
- Not wearing seat belts
- Distractions such as texting and phone calls
- Driving while fatigued
- Driving while under the influence of alcohol or drugs
See the Transportation Module of this eTool for more information concerning the hazards associated with motor vehicles and possible solutions.

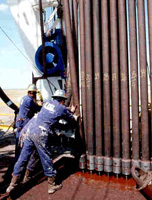
Struck-by, caught-in, and caught-between hazards are the number one cause of fatalities at the well site. Workers might be exposed to struck-by/caught-in/caught-between hazards from multiple sources, including moving vehicles or equipment, falling equipment, and high-pressure lines. The following can help you avoid struck-by, caught-in, and caught-between hazards while on the site.
Possible Solutions
- Wear reflective, high-visibility apparel (including reflective, high-visibility FRC (FRC) when needed) that can be seen by drivers.
- Provide one-way traffic patterns on location.
- Do back-in parking, so that the first move when leaving is moving forward.
- Take time to observe conditions around you that could change.
- Restrict entry of non-essential personnel into the area and ensure that everyone on the task is part of the RA/HA/JSA.
- Avoid standing on or working near heavy equipment, including tubulars, irons, vehicles, and trailers.
- Avoid being under heavy equipment. For example, ensure that floor hands are aware of the condition of wire ropes, slings, blocks, and other parts that could result in falling heavy equipment and tools above them.
- Secure pressurized lines that could whip when loose.
- Establish work zones during high-operating-pressure activities and keep other-than-essential personnel out of these zones.
- Develop a dropped objects program and ensure that all tools/equipment that could fall and strike workers below are secured. For more information and an example of a dropped object program, see ANSI/ISEA 121, American National Standard for Dropped Object Prevention Solutions, as well as Chevron's Dropped Object Prevention Program.
Rig floors, derricks, masts, tanks, and other elevated equipment at well sites often expose workers to falls.
Possible Solutions
- Be aware of the falling hazards when working on the derrick or mast, drilling floor, servicing rig floor, tanks, and other elevated equipment.
- Do not walk backwards.
- Install, inspect, and secure stairs and handrails.
- Instruct workers on proper procedures for using and installing ladders.
- Use only ladders in good repair that do not have missing rungs.
- Do not install stairs with missing or damaged steps. Repair them before installing them.
- Use three-point contact when going up and down stairs and ladders.
- OSHA regulations require that personnel be protected while working at heights. For example, under 29 CFR 1910.28(b)(1)(i), the employer must generally ensure that each employee on a walking-working surface with an unprotected side or edge that is 4 feet (1.2 m) or more above a lower level is protected from falling by guardrail systems, safety net systems, or personal fall arrest systems. Refer to 29 CFR 1910 Subparts D and I for more information.
- Ensure that an auxiliary escape device is installed and required to be used for anyone working on a monkey board, or other work platforms, where emergency escape is needed.
Fires and explosions are another leading cause of fatalities at well sites. The following can help prevent fires and explosions at well sites.
Possible Solutions
- Review the RA/HA/JSA performed before beginning work activities to make sure you are familiar with the fire and/or explosion hazards, and the controls in place.
- Establish barriers, or zones, and stay out of areas that could contain flammable liquids, vapors, and/or gases. These areas include the well head, tanks (including produced fluid tanks), heater-treaters, tanker trucks, hot oilers, and other equipment and lines connected to the process.
- Wear FRC, but DO NOT wear FRC or any other clothing that is soaked in flammable liquids.
- Use lower explosive limit (LEL) monitors/meters and evacuate areas with greater than 10% LEL until it is safe to re-enter.
- Use hot work permits when performing hot work in areas that could contain flammable liquids, vapors, or gases. See the Hot Work section of this eTool for more information.
- Watch for signs of kicks and blowouts resulting from sudden down-hole pressure rises. These releases frequently result in fires and explosions.
For a fire, or flash fire, to occur three conditions must be met (often referred to as the "fire triangle"):
- A fuel must be present
- Oxygen (O2) must be present
- An ignition source must be present
For an explosion to occur, the fire must also be in an enclosed area or space, including inside berms and trenches, or inside other configurations of equipment that tend to trap gases and/or vapors.
For a fire, flash fire, or explosion to occur, the O2 and fuel concentrations must be within the flammable limits (i.e., be within the upper and lower explosive limits) of the material and must be ignited by an energy (ignition) source. Air is almost always the source of O2.
Well Site Fuel Sources
The potential exists for a fuel source to be present at well sites because hydrocarbons are being extracted. In many instances, flammable vapors and gasses build up in enclosed areas such as berms, trenches, and under the rig structure including the cellar. Make every effort to prevent releases of hydrocarbon liquids, gases, and vapors.
Possible Solutions
- Prevent, direct, and/or contain releases through design, installation, inspection, and maintenance of proper equipment and materials.
- Implement procedures and processes, including adequate well control procedures, and install and use equipment (i.e., blowout preventers) to prevent or minimize releases.
- Immediately repair leaks.
- Stop work and/or shut down in a safe manner when a release is possible, is imminent, or has occurred. Re-evaluate the situation (by LEL or other monitoring) before returning to work.
- Kill the well when conditions warrant.
- Keep hatches and other openings on vessels and other equipment closed.
- Install relief devices and flare systems at safe discharge locations.
Ignition Sources
There are many potential sources of ignition for flammable gases and liquids on the well site. Identification and elimination of ignition sources during the RA/HA/JSA is a key to fire and explosion prevention.
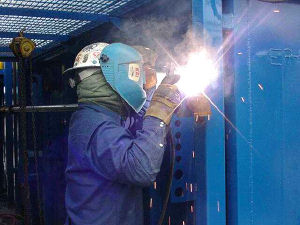
Potential ignition sources include, but are not limited to:
- Flames or sparks from any source, including non-spark-resistant hand tools
- Electric and diesel driven motors
- Internal-combustion engines, including vehicles
- Non-bonded or grounded equipment (producing static charge)
- Smoking
- Welding, cutting, brazing, grinding, or other hot work activities
- Non-intrinsically safe electric power tools
- Non-intrinsically safe cell phones, tablets, lap tops, two-way radios, and other electronic equipment
- Vehicles with catalytic converters
- Portable generators
Mobile engines and motors are ignition sources, but they are often inadequately considered in the oilfield. Refer to the hazard alert, "Fatalities from Ignition of Vapors by Mobile Engines and Auxiliary Motors" for more information.
Also, refer to the Hot Work section below for more information about hot work activities.
Possible Solutions
- Provide spark arrestors for internal-combustion engines.
- Post "NO SMOKING" signs before the job begins wherever a flammable gas or vapor hazard exists.
- Locate "spark producing" equipment or facilities well away from potential hazard areas.
- Prohibit vehicles with catalytic converters from the immediate vicinity of the rig.
- Control vehicle access and parking close to the rig or to other sources of hydrocarbons (e.g., shaker tables or tanks). It should be noted that attempting to move vehicles away from a release has resulted in fires and explosions.
- Prohibit open flames from the vicinity of the rig, considering equipment location such as hot oilers, heater-treaters, propane heaters, burning trash, etc.
- Implement a hot work program at the site.
- Ensure that equipment is properly bonded and/or grounded, including hoses, buckets, and other fluid handling equipment.
- Implement lockout/tagout (LOTO) on equipment that could become an ignition source if energized.
There are many ways to prevent slips, trips, and falls, or to minimize the consequences if they should happen.
Possible Solutions
- Be aware of slipping, tripping, and falling hazards when working on the drilling floor, servicing rig floors, or other platforms.
- Wear PPE that helps prevent slips, trips, and falls. Ensure that safety boots are in good condition with a defined heel and tread.
- Use water-resistant footgear to decrease slip/trip/fall hazards.
- Do not walk backwards.
- Be aware of uneven ground and walking surfaces. Re-level locations as necessary.
- Apply sand or salt during winter conditions to remove snow and ice. Snow can also cover uneven surfaces and obstacles.
- Keep all work areas clean and clear of oil, tools, and debris. (See the Housekeeping section.)
- Use non-skid surfaces where appropriate.
- Keep walkways clean and free of debris and tripping hazards.
- Keep all cords and hoses orderly and clear of walking spaces.
- Cover open cellars.
- Conduct a pre-job inspection to identify hazardous work surfaces, and then eliminate the hazards.
- Keep aisles and passageways clear and in good repair, with no obstruction across, or in aisles, that could create a hazard. Consider installing floor plugs for equipment (so that power cords do not run across pathways) or locate cords overhead.
- See also: 29 CFR 1910 Subpart D.
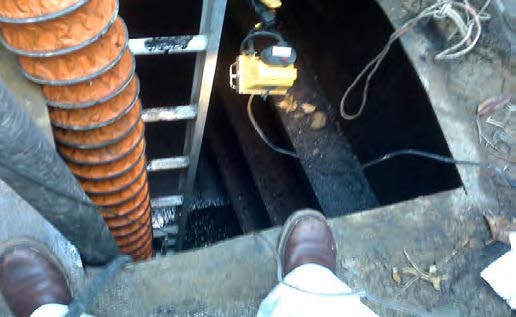
Asphyxiation (lack of O2 to the body) accounts for a surprising number of fatalities at well sites. Well gases, vapors, and volatile compounds (such as hydrogen sulfide (H2S), sulfur dioxide (SO2), carbon dioxide (CO2), carbon monoxide (CO), volatile organic compounds (VOCs), etc.) can come from the well or other sources (e.g., combustion engines). Except for methane, these well gases, vapors, and volatile compounds are heavier than air and therefore settle in low spots around the well. Methane, on the other hand, rises and must be considered when working above open tanks and hatches. The accumulation of gases, vapors, and volatile compounds in confined areas can lead to asphyxiation, which can result in unconsciousness even if the lack of O2 lasts only for a few seconds, followed by death if O2 is not restored quickly.
Possible Solutions
- Perform an atmospheric assessment of the well site and select the proper monitor(s) for the conditions assessed. Air monitors that measure O2 concentration (such as multi-gas meters) are essential for protecting against asphyxiation. For more information about monitor use and capability, see the Multi-Gas Monitors Hazard Alert.
- Train workers to stay out of confined spaces such as tanks, cellars, pits, and so forth, where vapors and gases can replace air. Make sure to comply with the requirements of 29 CFR 1910.146, Permit-Required Confined Spaces, before and during confined space entries. Do not enter a confined space if not in compliance, or if acceptable entry conditions do not exist.
Be aware of a serious health concern at thief hatches and manholes on tanks and tankers. Workers who open hatches or manholes can be asphyxiated or can become unconscious from toxic hydrocarbon vapors escaping the hatch or manhole. Those working for extended times on tanks with open hatches or manholes can also be harmed. When performing these activities, wear air-supplied respirators. For more information, see the Tank Hazard Infographic and the National Institute for Occupational Safety and Health, NIOSH-OSHA Hazard Alert titled "Health and Safety Risks for Workers Involved in Manual Tank Gauging and Sampling at Oil and Gas Extraction Sites."
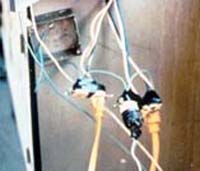
Electrocutions occur most frequently due to lack of awareness of the electrical hazards present, improper training, and use of inappropriate equipment, including inappropriate PPE.
Possible Solutions
- Identify electrical hazards on the RA/HA/JSA and ensure that they are adequately addressed.
- Watch for overhead energized lines when transporting equipment to and from the well-site, and when climbing or operating/raising tall equipment – especially during rig up and rig down operations.
- Watch for bare lines, as well as lines where insulation has worn through.
- Watch for ground-based energized lines. These lines are often subject to vehicle and foot traffic, resulting in damage to the insulation. Inspect all protective covers to ensure they are in sound condition.
- Do not work around electrical lines or equipment when you, or the area, is wet. Conditions can often be wet on and around the rig, which increases the risk of electrical shock, even at a distance from the electrical source.
- Watch for fallen lines, and for whether any fallen lines are in contact with water or conductive metal equipment.
- Do not work on energized lines or equipment unless you are a trained, qualified electrician working under a live electrical work permit, and using the right tools and PPE (including electrical protective equipment).
- Follow appropriate requirements for deenergizing lines and equipment. (e.g., LOTO, 29 CFR 1910.147, or applicable requirements for deenergizing lines and equipment under 29 CFR 1910.269). Confirm that there is no electrical energy present before working on electrical lines and potentially energized equipment.
- Perform routine inspections of electrical lines and equipment to ensure that they have not been damaged.
- Route electrical lines away from access ways, vehicle travel routes, and away from water unless designed or protected for that application.
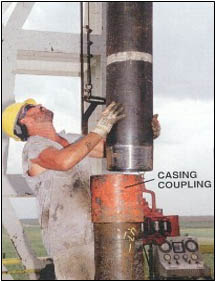
Strains and sprains are a frequent result of work with heavy and awkward loads at well sites. Injuries may not be fatal but can lead to long-term health issues if not prevented or properly treated.
Possible Solutions
- Complete an ergonomic assessment to identify potentially high-frequency, repetitive, or high-severity activities.
- Identify ergonomic hazards on the RA/HA/JSA and ensure that they are adequately addressed.
- Use mechanical lifting aids and equipment, and limit manual lifting of heavy equipment.
- When manual lifting is required, use proper lifting techniques (e.g., knees bent with back straight).
- Use proper hand and body positioning.
- Limit jerking actions when lifting. Jerking actions often result in sudden load increases that can result in strain and sprain injuries to the body.
- Practice proper hand placement and use of pullback (tail) ropes.
- Seek assistance when moving awkward and heavy equipment, such as irons, guards, and covers.
- Use proper stance and slip-lifting techniques. Slips typically have three handles and should be lifted jointly (i.e., with more than one person).
- Avoid prolonged repetitive motions that wear down the body. For those jobs that require repetitive motions, consider frequent rotation of personnel.
Refer to the NIOSH Ergonomics and Musculoskeletal topic page for more information.