Oil and Gas Well Drilling and Servicing eTool
General Safety » Hot Work
Hot work is any work that involves burning, welding, cutting, brazing, soldering, grinding, using fire- or spark-producing tools, or other work that produces a source of ignition. Welding and cutting operations are common to drilling and servicing operations.
Require hot work permits in areas where hazardous materials are stored and cannot be removed, or in areas where flammable atmospheres could exist. It is important for the employer to have a hot work program that covers hot work requirements, including permits.
Hazards with hot work are most frequently related to Fire and Explosion Hazards and Welding, Cutting, Brazing and Grinding Hazards; but also be aware that exposure to welding arcs and welding fumes can result in serious and disabling long-term health injuries. Refer to the hazard alert on hazards of hot work on oilfield equipment for more information.
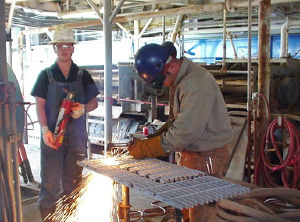
Tanks, containers, and other equipment (such as barrels, drums, bulk containers, separators, heater/treaters, vacuum trucks, storage tanks, frac tanks, flowback tanks, interconnecting pipes, produced water tanks and tankers, confined spaces where gases or vapors can accumulate, etc.) at the well site and at treatment facilities require periodic repair that often includes hot work. Workers performing hot work are exposed to the risks of fires and explosions from ignition of flammable or combustible materials in the workspace. Most tanks and equipment on site (even produced water tanks and tanker trucks) have contained hydrocarbons. Empty tanks, drums, and containers are a concern because they can easily contain enough residue to produce a flammable atmosphere in the headspace. Refer to the U.S. Chemical Safety and Hazard Investigation Board (CSB) bulletin Seven Key Lessons to Prevent Worker Deaths During Hot Work in and Around Tanks for additional information.
Possible Solutions
- All hot work is potentially hazardous. Perform an RA/HA/JSA to determine where the hazards exist. Recognize and understand the job and the hazards of hot work and follow safe work practices to prevent fires and explosions.
- Follow hot work procedures and permits as written. Skipping steps can lead to serious injuries. If a procedure needs to be modified, follow the MOC process, as recommended in API RP 76.
- Fatalities often occur because hot work practices are not followed. Don't assume that vapors or gases cannot be present in empty equipment. Perform periodic or continuous monitoring to ensure LELs for flammable vapors are zero or remain low.
- Ensure all vessel and equipment isolation practices are followed to prevent exposure to residual hydrocarbons.
- Follow LOTO procedures.
- Always test for flammable gases and vapors in the work area before starting any hot work. Potentially hazardous areas include, but are not limited to, barrels, drums, bulk containers, well heads, fuel tanks, mud pits, tank batteries (permanent or temporary), gas separators, oil heater/treaters, tanker vacuum trucks, produced water tanks and tankers, frac tanks, flowback tanks, interconnecting pipes, or confined spaces where gases or vapors can accumulate.
- Perform hot work well away from all sources of flammable vapors.
- If you are uncertain about potential risks or have questions, stop the job and ask… It could save your life!
- To reduce the risks of a fire or explosion, it is important for EMPLOYERS to:
- Communicate to contractors and employees the hazards and controls of all fluids at the wellsite. For example, contractors and employees may not recognize a fire or explosion hazard exists with many fluids that contain residual concentrations of hydrocarbons. However, these residuals can build up in tank, or truck, headspaces, as well as in “empty” tanks, drums, and other containers. Fluid haulers may also require respirators when changing filters, or when gauging.
- Develop SDSs for produced fluids at the well site and communicate the hazards of these fluids to contractors and employees.
- Provide PPE and training on the proper use and limitations of the PPE.
- Establish safe work practices for hot work, confined spaces work, LOTO, and line breaking.
- Make sure tanks are isolated, thoroughly cleaned, vented to safe areas, and tested for LEL before beginning hot work.
- Provide calibrated air monitoring equipment and procedures.
- Continuously monitor for O2 and LELs during hot work.
- Establish safe work practices for thawing frozen lines, hoses, valves, and equipment.
- Recognize and eliminate ignition sources.
- Ground and bond equipment.
- Use fire blankets, curtains, and shields to protect surrounding areas and workers.
- Provide and train on an emergency action plan that includes fires and explosions associated with hot work.
- Ensure properly equipped fire watches are used when performing hot work.
- Train workers on safe hot work practices and procedures and verify competency.
- Periodically audit hot work practices and procedures to ensure that the practices and procedures remain up to date and are effectively protecting workers.
-
It is important for EMPLOYEES to:
- Follow employer's work practices and procedures.
- Use proper grounding and bonding.
- Obtain appropriate hot work permits before beginning work.
- Review hot work permit/audit procedures with supervisors and have them sign off.
- Attend hazardous communication training – know the contents and hazards of the tanks and other equipment on which you work.
- Be aware of potential ignition sources (e.g., burning, welding, cutting, brazing, soldering, grinding, using fire- or spark-producing tools, propane torches, open flames, cigarettes, sparks from tools or metal objects, static charge, cell phones, radios, or performing any work that produces a source of ignition).
- Remove combustible materials from the work area before beginning hot work.
- Use required PPE.
- Use air monitoring devices and heed all alarms.
- Follow company procedures for incident and near miss/near hit reporting, as well as for emergencies and evacuations.
Eye damage can occur when workers are exposed to flashes and arcs created during welding, arc cutting, gouging, and other activities that produce high energy light, which, if viewed, is similar to looking directly at the sun. Breathing welding fumes can result in harmful exposure to several metals, including hexavalent chromium and manganese, and other hazardous air contaminants, depending on the materials used in the welding rods/wires and in the base metal(s).
Possible Solutions
- Know the materials being used before work begins.
- Use the correct protective lens for the application. Refer to 29 CFR 1910.252(b)(2).
- Provide respiratory protection and require its use when needed. Refer to NIOSH standards and to 29 CFR 1910.134 for selection of the proper respiratory protection.
- Sample for fumes, gases, and other possible air contaminants created by the hot work activities, and properly control and protect workers from these hazards.
- Perform work in a well-ventilated area.
- Mechanical ventilation and/or respiratory protection may be needed, depending on the hazard review.
- Equipment placed close to each other can create hazards similar to a confined space. Evaluate such situations to determine whether to add mechanical ventilation.
- Use fire blankets, curtains, and shields to protect personnel in surrounding areas, as well as personnel who are walking by the hot work area.
At times, hot work can occur in confined spaces or may require LOTO to isolate the potential hazards (such as fuels, ignition sources, and other sources of energy. It is important for employers and employees to review and make sure that all hazards are adequately addressed.
Possible Solutions
- If hot work is to be conducted in a permit-required confined space, use a confined space permit in conjunction with the hot work permit to control conditions in the confined space. See 29 CFR 1910.146.
- Use LOTO to isolate known fuel, ignition, and other energy sources from the area. See 29 CFR 1910.147.
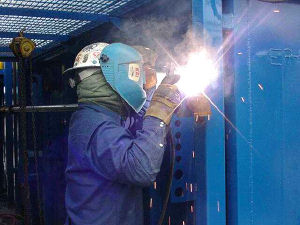
Injuries and illnesses can be caused by welding, cutting, brazing, or grinding activities, which can result in exposure to welding fumes and weld shielding gases, cutting torch fumes and gases (including CO), UV light, sparks, noise, or skin injury. Carefully monitor portable welding enclosures for sufficient ventilation.
Possible Solutions
- Inspect the work area to ensure that all fuel and ignition sources are isolated by shielding, clearing the area, LOTO, or soaking flammable material with water, etc.
- Remove flammable and combustible materials from around the area.
- After the proper hazard assessment, ensure that the required PPE is used. For example, wear equipment such as a face shield, leather welder's vest, and gauntlet gloves.
- Use cotton, denim, or FRC clothing, as appropriate.
- Provide UV shielding for arc welding.
- Inspect welding and cutting equipment (e.g., arc or gas welding/burning equipment) before use.
- Test gas torches, gauges, and hoses for leaks.
- Use and review a hot work permit.
- Ensure the availability of adequate fire watch/fire protection equipment.
- Ensure adequate ventilation from toxic welding and cutting fumes, with attention to portable welding enclosures, and areas where pieces of equipment are close to each other.
- Consider use of a hot wire anemometer to measure ventilation.
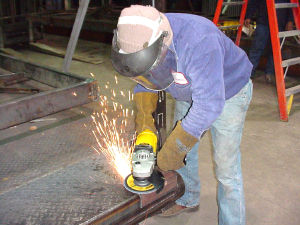
Toxic gases can accumulate in the area – particularly within a confined space. A hazardous atmosphere also exists in O2-deficient (atmospheric concentration of less than 19.5 percent) or O2-enriched areas (atmospheric concentration of more than 23.5 percent).
Possible Solutions
- Ventilate toxic metal fumes using mechanical ventilation, particularly if entering a confined space, such as inside of mud tanks, water tanks, oil tanks, frac tanks, flowback tanks, hoppers, sumps, pits, cellars, etc.
- Where a confined space contains, or has a potential to contain (among other things), a toxic, flammable, or O2-deficient atmosphere, use a written confined-space permit system to document (among other things) authorization to enter, the work to be performed, and the results of the gas monitoring. Both hot work and confined space entry permits may be required for welding, cutting or brazing within a confined space. See 29 CFR 1910.146.
Grinding results in sparks, flying metal filings or grinding wheel pieces, etc., and thereby creates the potential for eye and skin injuries. Fingers or hands can be caught in the grinding wheel, resulting in amputations or severe lacerations. Grinding wheels can fly apart and strike employees, if wheels are improperly sized or if the grinder speed does not match the wheel. A portable grinder can also strike a worker if the wheel catches on the piece being ground and causes a kickback.
Possible Solutions
- Perform an RA/HA/JSA to determine the best work practices and required PPE.
- Ensure that the proper PPE is being used at the work site. For example: wear a face shield, safety glasses, leather gloves, steel-toed shoes, etc.
- Wear cotton, denim, or FRC clothing, as appropriate.
- Remove flammable materials from around the area.
- Inspect grinding equipment before use.
- Ensure that tool guards, deflectors, and other safety devices are properly attached.
- Review the hot work permit.
- Ensure the availability of adequate fire watch/fire protection equipment.
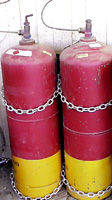
Gas cylinders contain gases, or liquefied gases, at high pressures. Inspect and maintain these cylinders to prevent rupture. Stop angle valves are located on top of these cylinders and have been known to break off if the cylinder is dropped or improperly handled. This can sometimes result in toxic exposures, fires, and/or explosions with the cylinder taking off like a rocket. They are also heavy and awkward to handle. Falling or rolling injuries have occurred from improper gas cylinder storage.
Possible Solutions
- Store full and empty cylinders separately. Also store all cylinders in an upright position, chained in separate racks, and with valve caps installed. Only remove the valve cap when the cylinder is in use.
- Close valves at the cylinders when work is completed or not being performed (such as before breaks, lunch, and at the end of shifts).
- Before transporting, remove gauges and regulators, and always install protective valve caps.
- Store cylinders in a dry, well-ventilated location.
- Avoid storing flammable substances in the same area as gas cylinders.
- Avoid storing cylinders of O2 within 20 feet of cylinders containing flammable gases or separate them by a fire-rated wall.
- Follow 29 CFR 1910 Subpart H - Hazardous Materials.
- Consult Compressed Gas Association (CGA) and Department of Transportation (DOT) standards and regulations, and regularly check for revisions.