Grocery Warehousing eTool
Grocery Warehousing » Transport Techniques
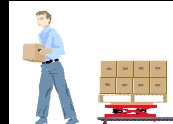
Employees usually move materials through the warehouse on pallet jacks. A pallet is placed on the Pallet Jack and merchandise is removed from a storage area called a slot or pick bin, then placed on the pallet. Many of these loads, especially in refrigerated or freezer warehouses, are extremely heavy. Weights upwards of 80 to 100 pounds are not uncommon.
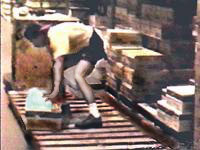
Potential Hazards:
-
Employees repeatedly bend forward at the waist to place boxes on the lowest level of pallets (Figure 1).
-
The heaviest units are placed on the bottom layer for stability. This work process requires employees to lift the heaviest loads using the worst body postures.
Possible Solutions:
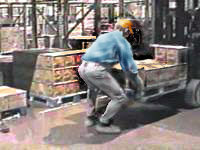
-
Raise the height of the bottom level to allow employees to keep the load close to the body (Figure 2). This will minimize bending of the torso.
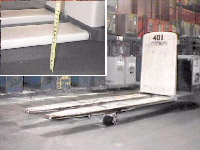
-
Provide height-adjustable picking equipment (Figure 3) so loads can be maintained at a height that minimizes bending at the waist. This pallet jack raises up to 10 inches, while many others raise eight inches or less.
-
Educate employees about the hazards of bending while moving heavy loads. Ensure the use of proper lifting techniques.
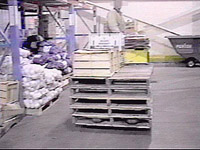
-
Stack extra empty pallets on the pallet jack to elevate the bottom of the load (Figure 4).
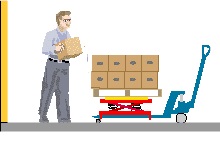
-
Place a palletizer on the forks of the pallet jack to keep product at waist height (Figure 5).
-
When possible, utilize power equipment rather than manual to reduce ergonomic stresses.
Back Belts:
-
The effectiveness of back belts in reducing the risk of back injury among heal workers remains unproven. If workers falsely believe they are protected when wearing belts, they may attempt to lift more than they would without a belt. This poses a risk of injury to the worker (See Back Belts: Do They Prevent Injury? US Department of Health and Human Services (DHHS), National Institute for Occupational Safety and Health (NIOSH) Publication No. 94-127).
Potential Hazards:
-
Over long periods of time the solid rubber wheels of pallet jacks and forklifts can develop flat spots resulting in unstable loads and poor handling. Employees can experience stress to the hands and arms from difficulty in steering and stopping.
-
Worn floors create ruts and bumps.
Possible Solutions:
-
Provide periodic maintenance of pallet jacks and fork lifts so they can operate with the minimum amount of hand, arm, and finger force.
-
Provide training to Selectors so they recognize the early signs of mechanical breakdown. This will allow them to report problems or difficulties with the machine before the problems lead to injury.
-
Keep floors well maintained (e.g. no ruts or bumps) to reduce force when using manual materials handling equipment and whole body vibration/shock from driven equipment.
For more information, refer to the following:
- Powered Industrial Trucks (Forklifts Trucks). OSHA Safety and Health Topics Page.