Grocery Warehousing eTool
Grocery Warehousing » Work Practice
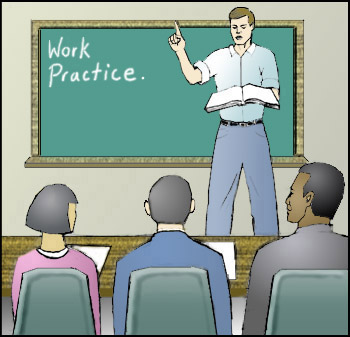
Management and staff employees should be aware of good work practices that minimize the possibility of injury. Items such as the patterns for pallet unloading, break schedules, training, or the number of hours worked can greatly influence the potential for injury.
Potential Hazards
Selectors encounter many racking situations in the typical warehouse and often depalletize in ways that expose them to unnecessary stressors. Depalletizing is where material is removed from a pallet where it has been stacked, usually in multiple layers. There are two common techniques of depalletizing (layer-by-layer and pyramiding) and either technique may be used depending on racking and product types.
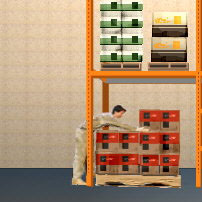
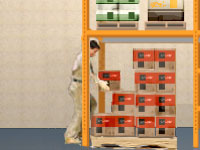
-
In a layer-by-layer technique selectors remove all cases from one layer before the cases from the next layer are removed (Figure 1). This technique requires employees to reach to the back of a palletized load and pull an item forward. This process moves the load closer to the body prior to lifting, but it can also create back and shoulder hazards if cases are extremely large or heavy. Also, weak or small handles, stacks above shoulder height, or cases that do not slide easily can stress the shoulder, back, and possibly the knee during reaching and pulling motions.
-
In the pyramiding technique cases are removed in a diagonal pattern from the top front to the rear back (Figure 2). This technique is preferred when weight, size, and handle types are like those mentioned above. In these situations the employee can limit forward reaching and pulling by moving closer to the load and lifting the closest container, often leaving the remaining stack in a pyramid shape. Pyramiding is not suggested if the pallet is unstable or in an area with little clearance space for employees. Many of the new racking systems, such as the push-back model, are elevated on slides and tightly packed into a pick slot. These configurations limit stability and accessibility, forcing employees to reach considerable distances across empty portions of the pallet to access and lift loads. Even lighter loads can create considerable stress to the shoulder, back, and knee when held away from the body.
Possible Solutions
-
An evaluation of each racking situation should be performed either by management or by a trained employee to determine the least stressful method of depalletizing. An appropriate selection should consider the nature of the load, the weight of the load, and the type of racking system used.
- Employees should generally use a layer-by-layer technique in push-back racking systems where employee access is limited, and pyramiding creates longer reach distances. Examples best suited for layer-by-layer depalletizing are:
- Boxed product, preferably with handles or cutouts
- Lighter boxes that slide fairly easily
-
Product stacked below shoulder height (measured with the pallet on the rack)
- A layer-by-layer approach can be made easier using the following methods:
- Use a hook to pull product from the back of pallets, allowing the arm to stay closer to the body, and reducing stress to the shoulder
- Order product, such as bagged produce, with slip sheets between the layers to facilitate sliding
- Order produce in boxes rather than bags. Boxes are easier to slide than bagged product and boxes are usually packaged in smaller quantities so the overall package is lighter
-
Place a slip sheet made of low friction material on partially emptied layers to facilitate sliding of product from the back of the pallet
- Pyramiding on a push-back system may be acceptable for lighter product such as toilet tissue or styrofoam plates. Product on push-back systems should be stacked low enough so reaches above head height are not required.
- Pyramiding may be acceptable for heavier items or items that do not slide easily, such as bagged onions, if the pallet is placed on the floor or another solid support that provides adequate access and the pallet itself does not present a hazard if walked on to provide easier access. Plastic pallets will provide a better base than wood slat pallets.
- For lighter loads stacked above shoulder height, it may be possible to use a combined approach. The top layers can be pulled down the sides in a controlled fall using the pyramid technique. When stack height drops below shoulder level, product can be removed in a layer-by-layer fashion.
- Employees should generally use a layer-by-layer technique in push-back racking systems where employee access is limited, and pyramiding creates longer reach distances. Examples best suited for layer-by-layer depalletizing are:
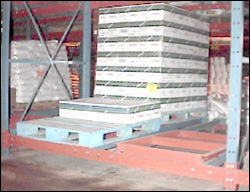
-
If a push back system is to be used with a pyramiding technique, equip it with a positive lock mechanism such that the pallet is held firmly in place and can not be pushed backward if an employee steps on it. This will allow employees to place one foot on the pallet to improve access and limit reaches. These postures will still not be acceptable for heavy product such as most meat items.
-
Tag slots as to what type of technique should be used and train employees about both the tagging system and selecting techniques.
- Develop systems so employees keep product that has to be lifted closer to the body, minimizing reaches and torso bending
- Utilize a turntable in bays so pallets can be rotated to ensure that the product is close to the aisle prior to lifting
- Create space around palletized loads so employees can access product from the side keeping it close to the body prior to lifting
- Develop a product re-orientation process for unloading using the pyramiding technique. The turning process should turn the pallet around 180 degrees to improve access. This will place the empty portion of the pallet at the back of the slot and place product closer to the aisle. This can be done by replenishing personnel during the stocking process or by a designated individual assigned to this task.
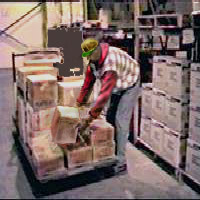
Potential Hazard
-
Selectors tend to reach across the pallet with a load in the hand (Figure 4) rather than walk around a pallet. This prevents keeping the load close to the body and adds significant stress to the shoulders and upper back.
Possible Solutions
-
Factor proper work practice into pick times. Time limits should not force employees to use shortcuts like reaching across a pallet instead of walking around the pallet for better access.
-
Provide training to Selectors so they understand the importance of performing tasks using proper ergonomic techniques.
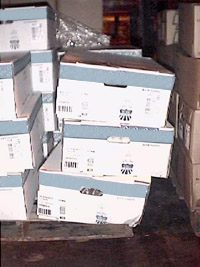
Potential Hazards
- Even experienced Selectors will come upon situations where they must perform unexpected exertions. This can happen when:
- A box weighs more than expected.
- The box falls apart (Figure 5), creating the need to perform quick and unexpected actions to save the load.
- Boxes stick together and additional force is needed to separate the boxes.
- Poor footing or slippage causes the load to be supported in an unexpected or awkward posture.
- Quick motions occur while holding the load.
Possible Solutions
-
Tag slots with case weights. This can be accomplished by noting the case weight on the slot in clear and easily read terms, or by color coding the slot to indicate the hazard. For example, the area in front of the slot can be marked with a red marker to indicate those areas where the heaviest product is stored.
-
Request that the suppliers pack product in sturdy cases, appropriate for the environment.
-
Clean all areas in the stocking aisles to avoid slipping. Workers should be educated on the importance of appropriate footwear.
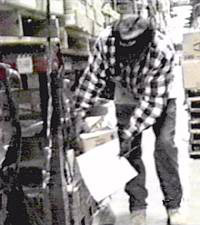
Potential Hazards
-
Stickers are placed on boxes after they are selected. Often an employee holds the sticker sheet while selecting and lifting product. If employees hold these sheets while performing lifting tasks (Figure 6), their contact with the box is reduced. This can lead to slippage and unexpected exertions, which increase the chance of injury to the back and shoulders.
-
One hand may exert more force than the other, which can lead to uneven weight distribution. This increases the chance of injury to the back. The chance of straining the tendons of the hand or forearm is also increased.
Possible Solutions
-
Use a sticker dispenser that can be worn around the employee's waist. This device will allow Selectors to use both hands when lifting product.
-
Provide a clipboard on the pallet jack to hold the sticker sheets rather than having employees hold the sheets in their hand while lifting.
Potential Hazard
-
Selectors may work through their break periods if production standards are set too high. Breaks are very important in heavy, physical work. Without periodic rest periods, the body may not have adequate time to rest and recuperate. Selectors who consistently work through their breaks are at a greater risk of musculoskeletal disorders (MSDs), accidents, and reduced quality of work due to operating at higher fatigue levels.
Possible Solutions
-
Work rates that require Selectors to pick orders rapidly will benefit the company, in the short run, by reducing the number of Selectors hired. However, these benefits may be lost due to higher injury rates if work standards exceed the capabilities of individuals. A competent work-time consultant can survey work tasks and recommend an appropriate work rate.
-
Ergonomic improvements may not justify an increase in pick rates. The benefits of reduced risk could easily be lost if rates are increased because the task appears to be easier.
-
Incorporate a work ramp-up (break-in) period for new hires. Work rates set for experienced Selectors may be too high for those that are new to Selecting work. It is common practice to allow a gradual ramp-up work rate for new hires that increases production over several weeks, or until employees can work at the same pace as experienced workers.
Potential Hazard
-
Working overtime, especially when the overtime is performed as an extension of the normal workday, may overexert employees by exceeding their capabilities.
Possible Solutions
-
Minimize overtime if at all possible. Provide part-time staff for peak periods.
-
Schedule overtime on off-days instead of extending the regular work shift. This will allow a period of recovery between shifts when employees may recuperate.
-
Assign overtime on a volunteer basis as much as possible.
Potential Hazard
-
Selectors are on their feet for long periods of time, possibly an entire shift. The leg muscles continually support the body, which can cause fatigue. Employees work on hard concrete surfaces, which can create contact trauma or tendon and muscle problems if proper footwear is not worn.
Possible Solutions
-
Educate employees about proper footwear. Shoes with solid support, flex at the ball of the foot, and adequate padding will maintain foot support and provide shock absorption against foot strike while walking on hard concrete surfaces
-
Provide employees with padded shoe inserts that support the foot and cushion against foot strike.
-
Shoes with non-skid soles are also important, particularly where surfaces are potentially slippery.
Potential Hazard
-
Without a medical management program, the presence of musculoskeletal disorders (MSDs) will probably be underestimated. With reduced awareness of MSDs, symptoms may go undetected until they become disabling injuries. Injured employees are less likely to get timely and appropriate care and restricted duty programs may not be established or utilized if proper medical management is not in place.
Possible Solutions
-
Consult with a medical specialist who has experience in and is familiar with work-related musculoskeletal disorders (MSDs). This person may be a physician, a nurse, or other healthcare provider that is familiar with causes of musculoskeletal injuries. They should be allotted time to track injury trends, coordinate injured employee's visits to healthcare facilities, interact with the treating physicians, and interact with the ergonomic committee regarding return-to-work activities and restricted work jobs. This person can also act as the principle contact person for Workers Compensation issues, and the liaison between management, healthcare and employees.
-
A relationship should be developed with a local medical clinic if an on-site specialist is not an option. It is imperative that the healthcare professionals be familiar with the type of tasks the employees perform. This will assist in diagnosis and the return-to-work process after an injury. If a clinic is used, it is important to have a responsible party on-site to act as a liaison with the medical provider
-
A return-to-work program should be developed for placement of injured workers into jobs consistent with their medical restrictions. A well constructed plan allows employees to return to work sooner and increases the chance that they will eventually return to their original job. The challenge of such a plan is to develop and categorize jobs within a facility that do not violate the restrictions given by the physician. Care should be taken to develop such a program in cooperation with any worker's unions, medical staff and contractors.
-
Symptoms should be reported as soon as they start to develop. Early reporting can help address potential problems before they become serious and costly lost-time injuries.
Potential Hazard
-
Newly hired employees may not recognize ergonomic hazards or understand effective techniques used to minimize these hazards.
Possible Solutions
-
Provide general ergonomics training and work-task specific training at the time of new-hire orientation. Explain risk factors and proper work techniques to minimize these hazards.
-
Provide appropriate video tapes of proper work practice for employees to review on a regular basis. In addition to regularly scheduled refresher training, injured employees should be retrained regarding ergonomic risks pertinent to their injuries.
-
Provide Post Incident Refresher Training after injuries:
-
The time immediately after employees are injured where they are usually more receptive to safety related training. Employees should be reintroduced to a full refresher of pertinent training topics once they are stabilized and can return to the work-site. The experiences of some warehouses have been that employees are more receptive to the message of safety training once they have been injured. They now understand that it can happen to them and that there is a way to help minimize these hazards. Once this new attitude is established these employees often become a very forceful messenger for the safety training message.
-
-
Provide new employees with a mentor that can provide insights on the proper and most efficient methods to perform their tasks.
-
Explain the medical management system to new-hires. It is important for employees to understand how to report an injury and how the company prefers its employees to seek medical attention. This can expedite assistance, reduce costs, and improve lines of communication.