Laser Hazards
Table of Contents:
- Introduction
- Nonbeam Laser Hazards
- Biological Effects of the Laser Beam
- Laser Hazard Classifications
- Investigational Guidelines
- Control Measures and Safety Programs
- Bibliography
List of Appdendices:
- Appendix III:6-1. FDA-CDRH Requirements for Laser Products
- Appendix III:6-2. FDA-CDRH Federal Laser Product Performance Standard Evaluation Outline
- Appendix III:6-3. The American National Standards Institute (ANSI)
- Appendix III:6-4. Warning Signs
- Appendix III:6-5. Glossary of Laser Terms
The mention of trade names, commercial products, or organizations does not imply endorsement by OSHA or the U.S. Government.
I. Introduction
The term LASER is an acronym for Light Amplification by Stimulated Emission of Radiation. Light can be produced by atomic processes which generate laser light. A laser consists of an optical cavity, a pumping system, and an appropriate lasing medium (Figure III:6-1).

Figure III:6-1. Components of a Laser
A. Optical Cavity
The optical cavity contains the media to be excited with mirrors to redirect the produced photons back along the same general path.
B. Pumping System
The pumping system uses photons from another source as a xenon gas flash tube (optical pumping) to transfer energy to the media, electrical discharge within the pure gas or gas mixture media (collision pumping), or relies upon the binding energy released in chemical reactions to raise the media to the metastable or lasing state.
C. Laser Medium
The laser medium can be a solid (state), gas, dye (in liquid), or semiconductor. Lasers are commonly designated by the type of lasing material employed.
- Solid state lasers have lasing material distributed in a solid matrix, e.g., the ruby or neodymium-YAG (yttrium aluminum garnet) lasers. The neodymium-YAG laser emits infrared light at 1.064 micrometers.
- Gas lasers (helium and helium-neon, HeNe, are the most common gas lasers) have a primary output of a visible red light. CO2 lasers emit energy in the far-infrared, 10.6 micrometers, and are used for cutting hard materials.
- Excimer lasers (the name is derived from the terms excited and dimers) use reactive gases such as chlorine and fluorine mixed with inert gases such as argon, krypton, or xenon. When electrically stimulated, a pseudomolecule or dimer is produced and when lased, produces light in the ultraviolet range.
- Dye lasers use complex organic dyes like rhodamine 6G in liquid solution or suspension as lasing media. They are tunable over a broad range of wavelengths.
- Semiconductor lasers, sometimes called diode lasers, are not solid-state lasers. These electronic devices are generally very small and use low power. They may be built into larger arrays, e.g., the writing source in some laser printers or compact disk players.
D. Wavelength Output
The wavelength output from a laser depends upon the medium being excited. Table III:6-1 lists most of the laser types and their wavelength ouput defined by the medium being excited. Laser use today is not restricted to the laboratory or specialized industries. Table III:6-2 lists some of the major uses of lasers.
Laser type |
Wavelength |
Laser type |
Wavelength |
---|---|---|---|
Argon fluoride (Excimer-UV) |
0.193 |
Helium neon (yellow) |
0.594 |
Krypton chloride (Excimer-UV) |
0.222 |
Helium neon (orange) |
0.610 |
Krypton fluoride (Excimer-UV) |
0.248 |
Gold vapor (red) |
0.627 |
Xenon chloride (Excimer-UV) |
0.308 |
Helium neon (red) |
0.633 |
Xenon fluoride (Excimer-UV) |
0.351 |
Krypton (red) |
0.647 |
Helium cadmium (UV) |
0.325 |
Rohodamine 6G dye (tunable) |
0.570-0.650 |
Nitrogen (UV) |
0.337 |
Ruby (CrAlO3) (red) |
0.694 |
Helium cadmium (violet) |
0.441 |
Gallium arsenide (diode-NIR) |
0.840 |
Krypton (blue) |
0.476 |
Nd:YAG (NIR) |
1.064 |
Argon (blue) |
0.488 |
Helium neon (NIR) |
1.15 |
Copper vapor (green) |
0.510 |
Erbium (NIR) |
1.504 |
Argon (green) |
0.514 |
Helium neon (NIR) |
3.39 |
Krypton (green) |
0.528 |
Hydrogen fluoride (NIR) |
2.70 |
Frequency doubled Nd YAG (green) |
0.532 |
Carbon dioxide (FIR) |
9.6 |
Helium neon (green) |
0.543 |
Carbon dioxide (FIR) |
10.6 |
Krypton (yellow) |
0.568 |
||
Copper vapor (yellow) |
0.570 |
||
Key:
|
TABLE III:6-2. MAJOR CATEGORIES OF LASER USE
- Alignment
- Annealing
- Balancing
- Biomedical
- Cellular research
- Dental
- Diagnostics
- Dermatology
- Ophthalmology
- Surgery
- Communications
- Construction
- Alignment
- Ranging
- Surveying
- Cutting
- Displays
- Drilling
- Entertainment
- Heat treating
- Holography
- Information handling
- Copying
- Displays
- Plate making
- Printing
- Reading
- Scanning
- Typesetting
- Videodisk
- Marking
- Laboratory instruments
- Interferometry
- Metrology
- Plasma diagnostics
- Spectroscopy
- Velocimetry
- Lidar
- Special photography
- Scanning microscopy
- Military
- Distance ranging
- Rifle simulation
- Weaponry
- Nondestructive training
- Scanning
- Sealing
- Scribing
- Soldering
- Welding
II. Nonbeam Laser Hazards
In some laser operations, particularly in the research laboratory, general safety and health guidelines should be considered.
A. Industrial Hygiene
Potential hazards associated with compressed gases, cryogenic materials, toxic and carcinogenic materials and noise should be considered. Adequate ventilation shall be installed to reduce noxious or potentially hazardous fumes and vapors, produced by laser welding, cutting and other target interactions, to levels below the appropriate threshold limit values, e.g., American Conference of Governmental Industrial Hygienists (ACGIH) threshold limit values (TLV's) or Occupational Safety and Health Administration's (OSHA) permissible exposure limits (PEL's).
B. Explosion Hazards
High-pressure arc lamps and filament lamps or laser welding equipment shall be enclosed in housings which can withstand the maximum pressures resulting from lamp explosion or disintegration. The laser target and elements of the optical train which may shatter during laser operation shall also be enclosed.
C. Nonbeam Optical Radiation Hazards
This relates to optical beam hazards other than laser beam hazards. Ultraviolet radiation emitted from laser discharge tubes, pumping lamps and laser welding plasmas shall be suitably shielded to reduce exposure to levels below the ANSI Z 136.1 (extended source), OSHA PEL's, and/or ACGIH TLV's.
D. Collateral Radiation
Radiation, other than laser radiation, associated with the operation of a laser or laser system, e.g., radio frequency (RF) energy associated with some plasma tubes, x-ray emission associated with the high voltage power supplies used with excimer lasers, shall be maintained below the applicable protection guides. The appropriate protection guide for RF and microwave energy is that given in the American National Standard "Safety levels with respect to human exposure to radio frequency electromagnetic fields, 300 kHz to 100 GHz," ANSI C95.1; the appropriate protection guides for exposure to X-ray emission is found in the Department of Labor Occupational Safety and Health Standards, 29 CFR Part 1910.1096 and the applicable State Codes. Lasers and laser systems which, by design, would be expected to generate appreciable levels of collateral radiation, should be monitored.
E. Electrical Hazards
The intended application of the laser equipment determines the method of electrical installation and connection to the power supply circuit (for example, conduit versus flexible cord). All equipment shall be installed in accordance with the National Electrical Code and the Occupational Safety and Health Act. [Additional specific recommendations can be found in Section 7.4 of ANSI Z 136.1 (1993)].
F. Flammability of Laser Beam Enclosures
Enclosure of Class IV laser beams and terminations of some focused Class IIIB lasers, can result in potential fire hazards if the enclosure materials are exposed to irradiances exceeding 10 W/cm2. Plastic materials are not precluded as an enclosure material, but their use and potential for flammability and toxic fume release following direct exposure should be considered. Flame-resistant materials and commercially available products specifically designed for laser enclosures should also be considered.
III. Biological Effects of the Laser Beam
A. Eye Injury
Because of the high degree of beam collimation, a laser serves as an almost ideal point source of intense light. A laser beam of sufficient power can theoretically produce retinal intensities at magnitudes that are greater than conventional light sources, and even larger than those produced when directly viewing the sun. Permanent blindness can be the result.
B. Thermal Injury
The most common cause of laser-induced tissue damage is thermal in nature, where the tissue proteins are denatured due to the temperature rise following absorption of laser energy.
- The thermal damage process (burns) is generally associated with lasers operating at exposure times greater than 10 microseconds and in the wavelength region from the near ultraviolet to the far infrared (0.315 μm-103 μm). Tissue damage may also be caused by thermally induced acoustic waves following exposures to sub-microsecond laser exposures.
- With regard to repetitively pulsed or scanning lasers, the major mechanism involved in laser-induced biological damage is a thermal process wherein the effects of the pulses are additive. The principal thermal effects of laser exposure depend upon the following factors:
- The absorption and scattering coefficients of the tissues at the laser wavelength. See Table III:6-1 for a summary of more common laser types and wavelengths.
- Irradiance or radiant exposure of the laser beam.
- Duration of the exposure and pulse repetition characteristics, where applicable.
- Extent of the local vascular flow.
- Size of the area irradiated.
C. Other
- Other damage mechanisms have also been demonstrated for other specific wavelength ranges and/or exposure times. For example, photochemical reactions are the principal cause of threshold level tissue damage following exposures to either actinic ultraviolet radiation (0.200 μm-0.315 μm) for any exposure time or "blue light" visible radiation (0.400 μm-0.550 μm) when exposures are greater than 10 seconds.
- To the skin, UV-A (0.315 μm-0.400 μm) can cause hyperpigmentation and erythema.
- Exposure in the UV-B range is most injurious to skin. In addition to thermal injury caused by ultraviolet energy, there is the possibility of radiation carcinogenesis from UV-B (0.280 μm - 0.315 μm) either directly on DNA or from effects on potential carcinogenic intracellular viruses.
- Exposure in the shorter UV-C (0.200 μm-0.280 μm) and the longer UV-A ranges seems less harmful to human skin. The shorter wavelengths are absorbed in the outer dead layers of the epidermis (stratum corneum) and the longer wavelengths have an initial pigment-darkening effect followed by erythema if there is exposure to excessive levels. These biological effects are summarized in Table III:6-3.
- The hazards associated with skin exposure are of less importance than eye hazards; however, with the expanding use of higher-power laser systems, particularly ultraviolet lasers, the unprotected skin of personnel may be exposed to extremely hazardous levels of the beam power if used in an unenclosed system design.
Photobiological spectral domain | Eye effects | Skin effects |
---|---|---|
Ultraviolet C (0.200-0.280 μm) | Photokeratitis | Erythema (sunburn) Skin cancer |
Ultraviolet B (0.280-315 μm) | Photokeratitis | Accelerated skin aging Increased pigmentation |
Ultraviolet A (0.315-0.400 μm) | Photochemical UV cataract | Pigment darkening Skin burn |
Visible (0.400-0.780 μm) | Photochemical and thermal retinal injury | Photosensitive reactions Skin burn |
Infrared A (0.780-1.400 μm) | Cataract, retinal burns | Skin burn |
Infrared B (1.400-3.00 μm) | Corneal burn Aqueous flare IR cataract |
Skin burn |
Infrared C (3.00-1000 μm) | Corneal burn only | Skin burn |
IV. Laser Hazard Classifications
A. Introduction
- The intent of laser hazard classification is to provide warning to users by identifying the hazards associated with the corresponding levels of accessible laser radiation through the use of labels and instruction. It also serves as a basis for defining control measures and medical surveillance.
- Lasers and laser systems received from manufacturers are required by federal law, 21 CFR Part 1000, to be classified and appropriately labeled by the manufacturer. It should be stressed, however, that the classification may change whenever the laser or laser system is modified to accomplish a given task.
- It should also be stressed that an agency such as the Food and Drug Administration's Center for Devices and Radiological Health (FDA/CDRH) does not "approve" laser systems for medical use. The manufacturer of the laser system first classifies the laser and then certifies that it meets all performance requirements of the Federal Laser Product Performance Standard (FLPPS). The forms submitted by the manufacturer to FDA/CDRH are reviewed for technical accuracy, omissions, and errors. If none are found, the manufacturer is notified only that the submission appears to be complete. Therefore, all lasers and laser systems that are manufactured by a company, or purchased by a company and relabeled and placed into commerce, or incorporated into a system and placed into commerce, shall be classified.
B. Laser Hazard Classes
- Virtually all of the U.S. domestic as well as all international standards divide lasers into four major hazard categories called the laser hazard classifications. The classes are based upon a scheme of graded risk. They are based upon the ability of a beam to cause biological damage to the eye or skin. In the FLPPS, the classes are established relative to the Accessible Emission Limits (AEL) provided in tables in the standard. In the ANSI Z 136.1 standard, the AEL is defined as the product of the Maximum Permissible Exposure (MPE) level and the area of the limiting aperture. For visible and near infrared lasers, the limiting aperture is based upon the "worst-case" pupil opening and is a 7 mm circular opening.
- Lasers and laser systems are assigned one of four broad Classes (I to IV) depending on the potential for causing biological damage. The biological basis of the hazard classes are summarized in Table III:6-4.
-
Class I: cannot emit laser radiation at known hazard levels (typically continuous wave: cw 0.4 μW at visible wavelengths). Users of Class I laser products are generally exempt from radiation hazard controls during operation and maintenance (but not necessarily during service).
Since lasers are not classified on beam access during service, most Class I industrial lasers will consist of a higher class (high power) laser enclosed in a properly interlocked and labeled protective enclosure. In some cases, the enclosure may be a room (walk-in protective housing) which requires a means to prevent operation when operators are inside the room.
- Class I.A.: a special designation that is based upon a 1000-second exposure and applies only to lasers that are "not intended for viewing" such as a supermarket laser scanner. The upper power limit of Class I.A. is 4.0 mW. The emission from a Class I.A. laser is defined such that the emission does not exceed the Class I limit for an emission duration of 1000 seconds.
- Class II: low-power visible lasers that emit above Class I levels but at a radiant power not above 1 mW. The concept is that the human aversion reaction to bright light will protect a person. Only limited controls are specified.
- Class IIIA: intermediate power lasers (cw: 1-5 mW). Only hazardous for intrabeam viewing. Some limited controls are usually recommended.
NOTE: There are different logotype labeling requirements for Class IIIA lasers with a beam irradiance that does not exceed 2.5 mW/cm2 (Caution logotype) and those where the beam irradiance does exceed 2.5 mW/cm2 (Danger logotype).
- Class IIIB: moderate power lasers (cw: 5-500 mW, pulsed: 10 J/cm2 or the diffuse reflection limit, whichever is lower). In general Class IIIB lasers will not be a fire hazard, nor are they generally capable of producing a hazardous diffuse reflection. Specific controls are recommended.
- Class IV: High power lasers (cw: 500 mW, pulsed: 10 J/cm2 or the diffuse reflection limit) are hazardous to view under any condition (directly or diffusely scattered) and are a potential fire hazard and a skin hazard. Significant controls are required of Class IV laser facilities.
-
Applies to |
Hazards |
|||||||
---|---|---|---|---|---|---|---|---|
Class |
UV |
VIS |
NIR |
IR |
Direct ocular |
Diffuse ocular |
Fire |
|
I |
X |
X |
X |
X |
No |
No |
No |
|
IA |
-- |
X† |
-- |
-- |
Only after 1000 sec |
No |
No |
|
II |
-- |
X |
-- |
-- |
Only after 0.25 sec |
No |
No |
|
IIIA |
X |
X†† |
X |
X |
Yes |
No |
No |
|
IIIB |
X |
X |
X |
X |
Yes |
Only when laser output is near Class IIIB limit of 0.5 Watt |
No |
|
IV |
X |
X |
X |
X |
Yes |
Yes |
Yes |
|
Key:
|
C. How to Determine the Class of Lasers During Inspection
- The classification of a laser or laser product is, in some instances, a rather detailed process. It can involve determination of the AEL, measurement of the laser emission, measurement/determination of the emission pulse characteristics (if applicable), evaluation of various performance requirements (protective housing, interlocks, etc.) as specified by the FLPPS and/or ANSI standards.
-
It should be stressed that classification is a required specification provided by the laser manufacturer and the label that specifies the class is found in only one location on the laser product. The class of the laser will be specified only on the lower left-hand corner (position three) of the warning logotype label.
The logotype is the rectangular label that has the laser "sunburst" symbol and the warning statement of CAUTION (Class II and some Class IIIA) or DANGER (some Class IIIA, all Class IIIB and Class IV). This label will also have the type of laser designated (HeNe, Argon, CO2, etc.) and the power or energy output specified (1 mW CW/MAX, 100 mJ pulsed, etc.).
- Class I lasers have no required labeling indicating the Class I status. Although the FLPPS requires no classification labeling of Class I lasers it does require detailed compliance with numerous other performance requirements (i.e., protective housing, identification and compliance labeling, interlocking, etc.)
D. ANSI Z 136.2 Optical Fiber Service Group Designations
- Optical Fiber Communication Systems (OFCS) and the associated optical test sets use semiconductor lasers or LED transmitters that emit energy at wavelengths typically in the range from 0.650 to 1.20 μm into the light-guide fiber-optic cables.
- All OFCS are designed to operate with the beam totally enclosed within the fiber-optic and associated equipment and, therefore, are always considered as Class I in normal operation.
- The only risk for exposure would occur during installation and service when light-guide cables are disconnected or during an infrequent accidental cable break.
- Under the requirements of the ANSI Z 136.2 (1988) Standard "For the Safe Use of Optical Fiber Communication Systems Utilizing Laser Diode and LED Sources," Optical Fiber Communication Systems (OFCS) are assigned into one of four service group (SG) designations: SG1, SG2, SG3a, SG3b, depending on the potential for an accessible beam to cause biological damage.
- The service group designations relate to the potential for ocular hazards to occur only during accessible beam conditions. This would normally occur only during periods of service to a OFCS. Such designations apply only during periods of service in one of the following four service groups:
- Service Group 1: An OFCS that is SG1 has a total output power that is less than the Accessible Emission Limit (AEL) for Class I and there is no risk of exceeding the Maximum Permissible Irradiance (MPI) when viewing the end of a fiber with a microscope, an eye-loupe or with the unaided eye.
- Service Group 2: An OFCS is SG2 only if wavelengths between 0.400 and 0.700 μm are emitted and is potentially hazardous if viewed for more than 0.25 second. (Note: At present there are virtually no OFCS's that operate in this wavelength range.)
- Service Group 3A: A SG 3A OFCS is not hazardous when viewed with the unaided eye and is hazardous only when viewed with a microscope or an eye-loupe.
- Service Group 3B: OFCS that meet none of the above criteria are designated as SG 3B.
V. Investigational Guidelines
A. Requirements of Laser Standards
In the United States, several organizations concern themselves with laser safety. These organizations include the American National Standards Institute (ANSI); the Center for Devices and Radiological Health (CDRH) of the Food and Drug Administration (FDA); the Department of Labor's Occupational Safety and Health Administration (OSHA); and the Council of Radiation Control Program Directors (CRCPD). Several state governments and the CRCPD have developed a model state standard for laser safety.
-
OSHA Regulatory Practice. At the present time, OSHA does not have a comprehensive laser standard, though 29 CFR 1926.54 is applicable to the construction industry. A standard for personal protective equipment (Subpart I) may apply in some cases.
The construction standard 29 CFR 1926.102(b)(2), for eye and face protection, states that "employees whose occupation or assignment requires exposure to laser beams shall be furnished suitable laser safety goggles which will protect for the specific wavelength of the laser and be of optical density (O.D.) adequate for the energy involved."
OSHA citations are issued by invoking the general duty clause or, in some cases, Subpart I. In such cases, the employers are required to revise their reportedly unsafe work place using the recommendations and requirements of such industry consensus standards as the ANSI Z 136.1 Standard. See also Table III:6-8.
-
Specific and Model State Laser Regulations. A few states currently have laser regulations. Requirements are generally concerned with the registration of lasers and the licensing of operators and institutions. Physician-used and other medical lasers are generally exempt from state requirements.
The complexity of state laser regulations may change in the future pending adoption of the "Suggested State Regulation for Lasers" promulgated through the Conference of Radiation Control Program Directors. This model state standard has been adopted in part, for example, by Arizona and Florida. Several other states have enacted some form of regulation. Table III:6-5 summarizes state regulations.
TABLE III:6-5. SUMMARY OF CURRENT STATE LASER REGULATIONS State Department Regulation Alaska Environmental Conservation Title 18, Article 7 Arizona† Radiation Regulatory Agency Arkansas Division of Radiation Control Emergency Management Act 460 Florida† Department of Health & Rehabilitative Services Non-Ionizing Chapter: 10D-89 Georgia Department of Public Health Chapter: 290-5-27 Illinois Department of Nuclear Safety Chapter: 111 ½ Massachusetts Department of Public Health 105 CMR 21 Montana Health & Environmental Services 92-003 New York Department of Labor Code Rule 50 Pennsylvania Environmental Resources Chapter: 203, Title 25 Texas Department of Health Radiation Control Act Parts 50, 60, 70 Washington Labor & Industry Chapter 296-62-WAC † Using CRCPD "Model State" laser standard as basis. - FDA Center for Devices and Radiological Health Performance Requirements.
- The CDRH of the Department of Health and Human Services was chartered by Congress to standardize the manufacture of lasers in interstate commerce after August 2, 1976. CDRH also has the responsibility for enforcing compliance with the medical devices legislation. All manufacturers of surgical lasers must obtain premarket approval of their devices through the CDRH.
- FDA sanctions the exploratory use of lasers for specific procedures through a process known as an Investigational Device Exemption (IDE). Approval of an IDE permits the limited use of a laser expressly for the purpose of conducting an investigation of the laser's safety and effectiveness. Once an IDE has been prepared and approved by the CDRH, the manufacturer may then actively market the laser for that specific medical or surgical procedure.
- The FDA/CDRH Federal Laser Product Performance Standard (FLPPS) regulates the manufacturer of commercial laser products, not the user. The standard does not contain specific design specifications, but is a conceptual, performance standard which the designer of laser products must consider. The intent is to insure laser product safety.
- FLPSS is applicable to lasers or laser systems sold by a company within or imported into the U.S. In some cases it can also apply when a laser or laser system is transferred within a company for internal use within the U.S. The compliance procedure requires implementation of the procedures and requirements as set forth in the U.S. Federal Laser Product Performance Standard: 21 CFR Part 1000 [parts 1040.10 and 1040.11].
- Under the requirements of the FLPPS, the manufacturer is first required to classify the laser as either a Class-I, Class-II, Class-I.A., Class-IIIA, Class-IIIB, or Class-IV laser product and then to certify (by means of a label on the product) as well as submit a report demonstrating that all requirements (performance features) of the compliance standard are met. Specific performance features include:
- protective housing;
- protective housing warning labels and logotype labels;
- product identification label and certification statement;
- safety interlocks;
- emission indicator;
- remote interlock connector;
- key control;
- beam attenuator;
- specification of control locations;
- viewing optic limitations;
- scanning beam safeguards; and
- manual reset of beam cutoff.
- FDA/CDRH performance requirements are tabulated in Appendix III:6-1. An outline to assist in evaluating FLPPS laser system performance requirements is included in Appendix III:6-2.
- The American National Standard Institute (ANSI). An American National Standard implies a consensus of those substantially concerned with its scope and provisions. These standards are intended as a guide for manufacturers, consumers, and the general public. However, there is no inherent requirement for any person or company to adhere to an ANSI standard. Compliance is voluntary unless specifically required by an organization. For example, the U.S. Department of Energy requires adherence to the ANSI Z 136.1 by their staff as well as by all contractor organizations. Appendix III:6-3 summarizes ANSI Standards applicable to laser safety.
B. Laser Exposure Limits
At present either the FDA criteria for medical lasers or the following ANSI standards can be useful in evaluating laser safety.
- FDA Long-Term Exposure Limits. The FDA/CDRH Federal Laser Product Performance Standard (FLPPS) assumes a linearly additive biological effect for exposures to visible light between 10 and 10^4 seconds (2.8 hours). The standard accepts that a cumulative radiant energy exposure of 3.85 millijoules (mJ) will not cause a biological effect. Hence a 10-second total accumulated exposure corresponds to an average power entering a 7-mm aperture of 385 microwatts (μW). For an exposure of 10^4 seconds, the average power would be 0.385 μW. In the FLPPS, the power level of 0.385 μW is referred to as the Class I Accessible Emission Limit (AEL) for a visible CW laser.
- ANSI Z 136.1, Long-Term Exposure Limits
- The ANSI Z 136.1 (1993) standard is a "user" standard and therefore provides maximum permissible exposure (MPE) limits. These were derived by normalizing the power (or pulse energy) data derived from biological research studies relative to a defined limiting aperture. For example, in the visible and near-infrared spectra, the limiting aperture is based upon the diameter of a fully dilated pupil of the human eye, 7 mm. The area of a 7-mm pupil is 0.385 cm2. Hence, the irradiance limit for long-term ocular exposure is computed by dividing the AEL value of 0.385 μW by the area of the limiting aperture of 0.385 cm2. This yields the worst-case MPE value of 1.0 μW/cm2 for long-term exposure in the wavelength range of 0.400 to 0.550 um.
- The ANSI Z 136 and FDA/CDRH allowable-exposure limits for CW lasers (Class I limits) are essentially identical for wavelengths between 0.400 and 0.550 μm. The ANSI limits are, however, more relaxed for wavelengths between 0.550 and 1.40 μm. ANSI recognizes a decreased biological hazard in the red and infrared regions that is not recognized by the CDRH.
- The ANSI Z 136 MPE level for a very long term exposure by a helium-neon laser is, in fact, seventeen times greater than the CDRH standard. In the 1976 revision, ANSI Z 136 introduced the correction factor CB which has a value of 17.5 at the 0.633-μm HeNe laser wavelength, and, thus, permitted a radiant exposure of 185 mJ/cm2 accumulated exposure for times from T1 = 453 seconds to 104 seconds, and about 18 w/cm2 (7 w in a 7-mm limiting aperture) for continuous operation of exposure durations exceeding 104 seconds.
- ANSI Z 136.1, Repetitively Pulsed Exposures
- The ANSI Z 136 standard requires a decrease in the maximum permissible exposure (MPE) for scanned or repetitive-pulse radiation as compared to continuous-wave radiation for pulse repetition frequencies (PRF) in the general range of 1000-15000 Hz. Because of pulse additivity, scanned or repetitively pulsed radiation with repetition rates less than 15 KHz have lower retinal damage threshold levels than CW radiation of comparable power.
- The ANSI Z 136 Standard includes a reduction factor of the threshold for each of the single pulses based on biological data that are not yet well explained by any theory. The FDA/CDRH standard does not recognize this repetitive-pulse correction factor. However, some experts envision the possibility of a repetitively pulsed laser which is Class I by the FDA/CDRH standard could be rated Class II or even Class IIIB by the ANSI Z 136 standard.
- The ANSI standard requires that multiple-pulse (scanning) lasers operating from 1 to 15,000 Hz have a correction to the single pulse MPE. The correction factor is determined by taking the fourth root of the total number of pulses (N) in a pulse train. Then, the correction factor is calculated such that the MPE radiant exposure or integrated radiance of an individual pulse within the train is reduced by a factor N-¼.
- ANSI Z 136.1, Maximum Permissible Exposure Limits
- A summary of Maximum Permissible Exposure (MPE) limits for direct ocular exposures for some of the more common lasers is presented in Table III:6-6. For further information on MPE values, refer to the ANSI Z 136.1 "Safe Use of Lasers" Standard.
- The information in Table III:6-6 provides the MPE value for different lasers operating for different overall exposure times. The times chosen were:
- 0.25 second: The human aversion time for bright-light stimuli (the blink reflex). Thus, this becomes the "first line of defense" for unexpected exposure to some lasers and is the basis of the Class II concept.
- 10 seconds: The time period chosen by the ANSI Z 136.1 committees represents the optimum "worst-case" time period for ocular exposures to infrared (principally near-infrared) laser sources. It was argued that natural eye motions dominate for periods longer than 10 seconds.
- 600 seconds: The time period chosen by the ANSI Z 136.1 committees represents a typical worst-case period for viewing visible diffuse reflections during tasks such as alignment.
- 30,000 seconds: The time period that represents a full 1-day (8-hour) occupational exposure. This results from computing the number of seconds in 8 hours; e.g.: 8 hours × 60 minutes/hour × 60 seconds/minute = 28,800 seconds. Rounded off, it becomes 30,000 seconds.
- The "safety" exposure limits (MPE's) in Table III:6-6 are expressed in irradiance terms (W/cm2) that would be measured at the cornea. Note that they vary by wavelength and exposure time.
Wave- |
-------------- MPE level (W/cm2) -------------- |
||||
---|---|---|---|---|---|
Laser type |
(μm) |
0.25 sec |
10 sec |
600 sec |
30,000 sec |
CO2 (CW) |
10.6 |
--- |
100.0 × 10-3 |
--- |
100.0 × 10-3 |
Nd: YAG (CW) |
1.33 |
--- |
5.1 × 10-3 |
--- |
1.6 × 10-3 |
Nd: YAG (CW) |
1.064 |
--- |
5.1 × 10-3 |
--- |
1.6 × 10-3 |
Nd: YAG (Q-switched) |
1.064 |
--- |
17.0 × 10-6 |
--- |
2.3 × 10-6 |
GaAs (Diode/CW) |
0.840 |
--- |
1.9 × 10-3 |
--- |
610.0 × 10-6 |
HeNe (CW) |
0.633 |
2.5 × 10-3 |
--- |
293.0 × 10-6 |
17.6 × 10-6 |
Krypton (CW) |
0.647 |
2.5 × 10-3 |
|
364.0 × 10-6 |
28.5 × 10-6 |
Argon (CW) |
0.514 |
2.5 × 10-3 |
--- |
16.7 × 10-6 |
1.0 × 10-6 |
XeFl (Excimer/ CW) |
0.351 |
--- |
--- |
--- |
33.3 × 10-6 |
XeCl (Excimer/ CW) |
0.308 |
--- |
--- |
--- |
1.3 × 10-6 |
† Source: ANSI Z 136.1 (1993) |
C. Laser Hazard Computations
- NHZ Definition, Use, and Values
- The Nominal Hazard Zone (NHZ) describes the space within which the level of direct, reflected, or scattered radiation during normal operation exceeds the MPE. The NHZ associated with open-beam Class IIIB and Class IV laser installations can be useful in assessing area hazards and implementing controls.
- It is often necessary in some applications where open beams are required (e.g., industrial processing, laser robotics, surgical uses) to define the area where the possibility exists for potentially hazardous exposure. This is done by determining the NHZ. Consequently, persons outside the NHZ boundary would be exposed below the MPE level and are considered to be in a non-hazardous location.
- The NHZ boundary may be defined, for example, by direct beams (intrabeam) and diffusely scattered laser beams, as well as beams transmitted from fiber optics and/or through lens arrays. The NHZ perimeter is the envelope of MPE exposure levels from any specific laser installation geometry.
- The purpose of an NHZ evaluation is to define that space where control measures are required. This is an important factor since, as the scope of laser uses has expanded, controlling lasers by total enclosure in a protective housing or interlocked room is limiting and, in many instances, an expensive overreaction to the real hazards. The following factors are required in NHZ computations:
- laser power or energy output;
- beam diameter;
- beam divergence;
- pulse repetition frequency (prf) (if applicable);
- wavelength;
- beam optics and beam path; and
- maximum anticipated exposure duration.
- Note that the ANSI Z 136 MPE value is required in all NHZ calculations. Examples of NHZ calculations can be found in the appendix of ANSI Z 136.1 (1993). In addition, computer software is also available to assist in the computations for NHZ, optical densities of protective eye wear, and other aspects of laser hazard analysis.
-
NHZ Example Summary. The intrabeam (direct) hazard for a Nd:YAG laser extends from 792 meters to 1410 meters, depending upon whether a 10-second or 8-hour criterion is used, as summarized in Table III:6-7. Similarly, with a lens on the laser, the hazard for a Nd:YAG laser exists over a range from 6.3 meters to 11.3 meters. The diffuse reflection zone for this laser type is, however, markedly smaller, 0.8 meter to 1.4 meters. Nonetheless, the analysis suggests that operating personnel and support staff close to the laser still need eye protection even for diffuse reflections.
Other calculations are also presented in Table III:6-7 for a 500-Watt CO2 and a 5-Watt argon laser. Note that the NHZ's do not vary for the CO2 laser (because the MPE values are nearly identical for 10-second and 8-hour criteria). Also note that the diffuse reflection NHZ's are very small except for the 8-hour criterion for the argon laser. In most cases, 0.25 second can be used with visible lasers unless intentional staring is required or intended.
TABLE III:6-7. NHZ DISTANCE VALUES FOR VARIOUS LASERS ----- Hazard range (meters) -----
Laser type Exposure
criteriaDiffuse Lens-on-laser Direct Nd:YAG
100 Watt
1.064 µm8 hours
10 seconds1.4
0.811.3
6.31410
792CO2
500 Watt
10.6 µm8 hours
10 seconds0.4
0.45.3
5.3309
390Argon
5.0 Watt
0.488 µm8 hours
0.25 seconds12.6
0.251.7 x 103
33.325.2 x 103
240Laser criteria used for NHZ distance calculations: Laser parameter Nd-YAG CO2 Argon Wavelength (μm) 1.064 10.6 0.488 Beam power (Watts) 100.0 500.0 5.0 Beam divergence (mrad) 2.0 2.0 1.0 Beam size at aperture (mm) 2.0 20.0 2.0 Beam size at lens (mm) 6.3 30.0 3.0 Lens focal length (mm) 25.4 200.0 200.0 MPE for 8 hours (w/cm2) 1.6 x 103 1.0 x 105 1.0 MPE for 10 seconds (w/cm2) 5.1x103 1.0 x 105 --- MPE for 0.25 second (w/cm2) --- --- 2.5 x 103
D. Intrabeam Optical Density Determination
- Based upon these typical exposure conditions, the optical density required for suitable filtration can be determined. Optical density (OD) is a logarithmic function defined by:
EQUATION III:6-1. OPTICAL DENSITY
OD = log10 H0/MPE
where:
H0 = Anticipated worst-case exposure (J/cm2 or W/cm2)
Maximum permissible exposure level expressed in the same units as H0 -
Based upon the worst case exposure conditions outlined above, one can determine the optical density recommended to provide adequate eye protection for this laser. For example, the minimum optical density at the 0.514 µm argon laser wavelength for a 600-second direct intrabeam exposure to the 5-watt maximum laser output can be determined as follows:
Where:
f = 5 Watts
MPE = 16.7 W/cm2 (using 600-second criterion)
d = 7 mm (worst-case pupil size)Computing the worst-case exposure H0:
H0 = [Power/Area] = f/A = 4f/ pd2
H0 = [(4)(5.0)/ p(0.7)2]
H0 = 12.99 W/cm2Substitution gives:
OD = log10 [(12.99)/(16.7 x 10-6)]
OD = 5.9 -
The most conservative approach would be to choose an 8-hour (occupational) exposure. In this case, the optical density at 0.514 µm is increased to OD = 7.1 for a 5.0-watt intrabeam exposure because the 8-hour (30,000 §) MPE is reduced to 1.0 x 10-6 W/cm2. The OD values for various lasers, computed for various appropriate exposure times, are presented in Table III:6-8. It should be stressed these values are for intrabeam viewing (worst case) only. Viewing Class IV diffuse reflections (such as during alignment tasks) require, in general, less OD. These should be determined for each situation and would be dependent upon the laser parameters and viewing distance.
TABLE III:6-8. OPTICAL DENSITIES FOR PROTECTIVE EYEWEAR FOR VARIOUS LASER TYPES Laser type and power(μm) Wavelength (μm) --- Optical density for exposure durations ---
0.25 § 10 § 600 § 30,000 § XeCl
50 Watts0.308a -- 6.2 8.0 9.7 XeFl
50 Watts0.351a -- 4.8 6.6 8.3 Argon
1.0 Watts0.514 3.0 3.4 5.2 6.4 Krypton
1.0 Watt0.530 3.0 3.4 5.2 6.4 Krypton
1.0 Watt0.568 3.0 3.4 4.9 6.1 HeNe
0.005 Watt0.633 0.7 1.1 1.7 2.9 Krypton
1 Watt0.647 3.0 3.4 3.9 5.0 GaAs
50 mW0.840c -- 1.8 2.3 3.7 Nd: YAG
100 Watt1.064a -- 4.7 5.2 5.2 Nd: YAG
(Q-switch)b1.064a -- 4.5 5.0 5.4 Nd: YAG
50 Watts1.33a -- 4.4 4.9 4.9 CO2
1000 Watts10.6a -- 6.2 8.0 9.7 a. Repetitively pulsed at 11 Hertz, 12-nanosecond pulses, 20 mJ/pulse.
b. OD for UV and FIR beams computed using a 1-mm limiting aperture, which presents a "worst-case" scenario. All visible and NIR computations assume a 7-mm limiting aperture.
c. Nd:YAG operating at a less-common 1.33 μm wavelength.
NOTE: All OD values determined using MPE criteria of ANSI Z 136.1 (1993).
VI. Control Measures and Safety Programs
The specific control measures specified in the ANSI Z 136.1 standard are summarized in Table III:6-9. The details of these controls are outlined the following sections.
Control measures |
------------------ Class ----------------- |
|||||
---|---|---|---|---|---|---|
I | IA | II | IIIA | IIIB | IV | |
Protective housing | X | X | X | X | X | X |
Without protective housing |
-- LSO shall establish alternate controls -- |
|||||
Interlocks on protective housing | a | a | a | X | X | X |
Service access panel | b | b | b | b | b | X |
Key switch master | _ | _ | _ | _ | • | X |
Viewing portals | _ | _ | ◊ | ◊ | ◊ | ◊ |
Collecting optics | _ | _ | ◊ | ◊ | ◊ | ◊ |
Totally open beam path | _ | _ | _ | _ | X | X |
Limited open beam path | _ | _ | _ | _ | X | X |
Remote interlock connector | _ | _ | _ | _ | • | X |
Beram stop or attenuator | _ | _ | _ | • | • | X |
Activation warning system | _ | _ | _ | _ | • | X |
Emission delay | _ | _ | _ | _ | _ | • |
Class IIIB laser controlled area | _ | _ | _ | _ | X | _ |
Class IV laser controlled area | _ | _ | _ | _ | _ | X |
Laser outdoor controls | _ | _ | _ | _ | X | X |
Temporary laser controlled area | b | b | b | b | _ | _ |
Remote firing & monitoring | _ | _ | _ | _ | _ | • |
Labels | _ | X | X | X | X | X |
Area posting | _ | _ | • | • | X | X |
Administrative & procedural controls | _ | X | X | X | X | X |
Standard operating procedures | _ | _ | _ | _ | • | X |
Output emission limitations | _ | _ | _ |
--LSO determines-- |
||
Education and training | _ | _ | _ | X | X | X |
Authorized personnel | _ | _ | _ | _ | X | X |
Alignment procedures | _ | _ | X | X | X | X |
Eye protection | _ | _ | _ | _ | • | X |
Spectator control | _ | _ | _ | _ | • | X |
Service personnel | b | b | b | b | X | X |
Laser demonstration | _ | _ | X | X | X | X |
Laser fiber optics | _ | _ | X | X | X | X |
Key:
X = Shall. |
A. Control Measures: Overview
- There are four basic categories of controls useful in laser environments. These are engineering controls, personal protective equipment, administrative and procedural controls, and special controls. The controls to be reviewed here are based upon the recommendations of the ANSI Z 136.1 standard.
- Important in all controls is the distinction between the functions of operation, maintenance, and service. First, laser systems are classified on the basis of level of the laser radiation accessible during operation. Maintenance is defined as those tasks specified in the user instructions for assuring the performance of the product and may include items such as routine cleaning or replenishment of expendables. Service functions are usually performed with far less frequency than maintenance functions (e.g., replacing the laser resonator mirrors or repair of faulty components) and often require access to the laser beam by those performing the service functions. The safety procedures required for such beam access during service functions should be clearly delineated in the laser product's service manual.
B. Laser Safety Officer (LSO)
- The LSO has the authority to monitor and enforce the control of laser hazards and effect the knowledgeable evaluation and control of laser hazards. The LSO administers the overall laser safety program where the duties include, but are not limited to, items such as confirming the classification of lasers, doing the NHZ evaluation, assuring that the proper control measures are in place and approving substitute controls, approving standard operating procedures (SOP's), recommending and/or approving eye wear and other protective equipment, specifying appropriate signs and labels, approving overall facility controls, providing the proper laser safety training as needed, conducting medical surveillance, and designating the laser and incidental personnel categories.
- The LSO should receive detailed training including laser fundamentals, laser bioeffects, exposure limits, classifications, NHZ computations, control measures (including area controls, eye wear, barriers, etc.), and medical surveillance requirements.
- In many industrial situations, the LSO functions will be a part-time activity, depending on the number of lasers and general laser activity. The individual is often in the corporate industrial hygiene department or may be a laser engineer with safety responsibility. Some corporations implement an internal laser policy and establish safety practices based upon the ANSI Z 136.1 standard as well as their own corporate safety requirements.
C. Class I, Class II, Class I.A., and Class IIIA Lasers.
Accident data on laser usage have shown that Class I, Class II, Class I.A., and Class IIIA lasers are normally not considered hazardous from a radiation standpoint unless illogically used.
D. Beam Path Controls
There are some uses of Class IIIB and Class IV lasers where the entire beam path may be totally enclosed, other uses where the beam path is confined by design to significantly limit access and yet other uses where the beam path is totally open. In each case, the controls required will vary as follows:
- Enclosed (Total) Beam Path
- Perhaps the most common form of a Class I laser system is a high-power laser that has been totally enclosed (embedded) inside a protective enclosure equipped with appropriate interlocks and/or labels on all removable panels or access doors. Beam access is prevented, therefore, during operation and maintenance.
- Such a completely enclosed system, if properly labeled and properly safeguarded with protective housing interlocks (and all other applicable engineering controls), will fulfill all requirements for a Class I laser and may be operated in the enclosed manner with no additional controls for the operator.
- It should be noted that during periods of service or maintenance, controls appropriate to the class of the embedded laser may be required (perhaps on a temporary basis) when the beam enclosures are removed and beam access is possible. Beam access during maintenance or service procedures will not alter the Class I status of the laser during operation.
- Limited Open Beam Path
- It is becoming an accepted work practice, particularly with industrial materials-processing lasers, to build an enclosure that completely surrounds the laser-focusing optics and the immediate area of the workstation. Often a computer-controlled positioning table is located within this enclosure. The design often allows a gap of less than one quarter of an inch between the bottom of the enclosure and the top of the material to be laser processed. Such a design enables the part to be laser cut or welded to move while the laser delivery optics remain stationary.
- Such a system might not meet the stringent "human access" requirements of the FLPPS for a Class I laser, but the real laser hazards are well confined. Such a design provides what can be called a limited open beam path. In this situation, the ANSI Z 136.1 standard recommends that the LSO shall conduct a laser hazard analysis and establish the extent of the NHZ.
- In many system designs, (such as described above), the NHZ will be extremely limited, and procedural controls (rather than elaborate engineering controls) will be sufficient to ensure safe use. In many cases, the laser units may be reclassified by the LSO as Class I under the specifications of the ANSI Z 136 standard.
- Such an installation will require a detailed standard operating procedure (SOP). Training is also needed for the system operator commensurate with the class of the embedded laser.
- Protective equipment (eye protection, temporary barriers, clothing and/or gloves, respirators, etc.) would be recommended, for example, only if the hazard analysis indicated a need or if the SOP required periods of beam access such as during setup or infrequent maintenance activities. Temporary protective measures for service can be handled in a manner similar to the service of any embedded Class IV laser.
- Totally Unenclosed Beam Path. There are several specific application areas where high power (Class IIIB and Class IV) lasers are used in an unenclosed beam condition. This would include, for example, open industrial processing systems (often incorporating robotic delivery), laser research laboratory installations, surgical installations, etc. Such laser uses will require that the LSO conduct a hazard analysis and NHZ assessment. Controls are chosen to reflect the magnitude of hazards associated with the accessible beam.
E. Laser-Controlled Area.
When the entire beam path from a Class IIIB or Class IV laser is not sufficiently enclosed and/or baffled to ensure that radiation exposures will not exceed the MPE, a "laser-controlled area" is required. During periods of service, a controlled area may be established on a temporary basis. The controlled area will encompass the NHZ. Those controls required for both Class IIIB and Class IV installations are as follows:
- Posting with Appropriate Laser Warning Signs
- Class IIIA (beam irradiance 2.5 mW/cm2), Class IIIB and Class IV lasers: Require the ANSI DANGER sign format: white back-ground, red laser symbol with black outline and black lettering (see Appendix III:6-4). Note that under ANSI Z 136.1 criteria, area posting is required only for Class IIIB and Class IV lasers.
- Class II or Class IIIA areas (if area warning is deemed unnecessary by the LSO): All signs (and labels) associated with these lasers (when beam irradiance for Class IIIA does not exceed 2.5 mW/cm2) use the ANSI CAUTION format: yellow background, black symbol and letters.
- During times of service and other times when a temporary laser-controlled area is established, an ANSI NOTICE sign format is required: white background, red laser symbol with blue field and black lettering. This sign is posted only during the time when service is in progress. Examples of area warning signs and logotype designs are given in Appendix III:6-4.
- Operated by Qualified and Authorized Personnel. Training of the individuals in aspects of laser safety is required for Class IIIB and Class IV laser installations.
- Transmission from Indoor Controlled Area. The beams shall not, under any circumstances, be transmitted from an indoor laser-controlled area unless for specific purposes (such as testing). In such cases, the operator and the LSO must assure that the beam path is limited to controlled air space.
F. Class IV Laser Controls--General Requirements
Those items recommended for Class IIIB but required for Class IV lasers are as follows:
- Supervision directly by an individual knowledgeable in laser safety.
- Entry of any noninvolved personnel requires approval.
- A beam stop of an appropriate material must be used to terminate all potentially hazardous beams.
- Use diffusely reflecting materials near the beam, where appropriate.
- Appropriate laser protective eye wear must be provided all personnel within the laser controlled area.
- The beam path of the laser must be located and secured above or below eye level for any standing or seated position in the facility.
- All windows, doorways, open portals, etc., of an enclosed facility should be covered or restricted to reduce any escaping laser beams below appropriate ocular MPE level.
- Require storage or disabling of lasers when not in use.
G. Entryway Control Measures (Class IV)
In addition, there are specific controls required at the entryway to a Class IV laser controlled area. These can be summarized as follows:
- All personnel entering a Class IV area shall be adequately trained and provided proper laser protective eye wear.
- All personnel shall follow all applicable administrative and procedural controls.
- All Class IV area and entryway controls shall allow rapid entrance and exit under all conditions.
- The controlled area shall have a clearly marked "Panic Button" (nonlockable disconnect switch) that allows rapid deactivation of the laser.
Class IV areas also require some form of area and entryway controls. In the past, doorway interlocking was customary for Class IV installations. The ANSI Z 136 Standard now provides four options that allow the LSO to provide an entryway control suited for the installation. The options include:
- Nondefeatable Entryway Controls. A nondefeatable control, such as a magnetic switch built into the entryway door which cuts the beam off when the door is opened, is one option. In this case, training is required only for those persons who regularly work in the laser area.
- Defeatable Entryway Controls
- Defeatable controls may be used at an entryway, for example, during long-term testing in a laser area. In this case the controls may be temporarily made inactive if it is clearly evident that there is no hazard at the point of entry. Training is required for all personnel who may frequently require entry into the area.
- Such defeatable controls shall be designed to allow both rapid egress by the laser personnel at all times and admittance to the laser controlled area in an emergency condition. A readily accessible "panic button" or control/disconnect switch shall be available for deactivating the laser under such emergency conditions.
- Under conditions where the entire beam path is not completely enclosed, access to the laser-controlled area shall be limited only to persons wearing proper laser protective eye wear when the laser is capable of emitting a beam. In this case, all other optical paths (for example, windows) from the facility shall be covered or restricted in such a way as to reduce the transmitted intensity of the laser radiation to levels at or below the MPE for direct irradiation of the eye.
- Procedural Entryway Controls. A blocking barrier, screen, or curtain that can block or filter the laser beam at the entryway may be used inside the controlled area to prevent the laser light from exiting the area at levels above the applicable MPE level. In this case, a warning light or sound is required outside the entryway that operates when the laser is energized and operating. All personnel who work in the facility shall be appropriately trained.
- Entryway Warning Systems. In order to safely operate a Class IV laser or laser system, a laser warning system shall be installed as described:
- A laser activation warning light assembly shall be installed outside the entrance to each laser room facility containing a Class IV laser or laser system.
- In lieu of a blinking entryway warning, the entryway light assembly may alternatively be interfaced to the laser in such a manner that a light will indicate when the laser is not operational (high voltage off) and by an additional light when the laser is powered up (high voltage applied) but not operating and by an additional (flashing) light when the laser is operating.
A laser warning sign shall be posted both inside and outside the laser-controlled area.
H. Temporary Laser-Controlled Area
Should overriding interlocks become necessary during periods of special training, service, or maintenance, and access to Class IIIB or Class IV lasers is required, a temporary laser-controlled area shall be devised following specific procedures approved by the LSO. These procedures shall outline all safety requirements necessary during such operation.
Such temporary laser-controlled areas, which by nature will not have the built-in protective features as defined for a laser-controlled area, shall nevertheless provide all of the safety requirements for all personnel, both within and without the temporary laser-controlled area during periods of operation when the interlocks are defeated.
I. Administrative and Procedural Controls
-
Standard Operating Procedures. One of the more important of the administrative and procedural controls is the written Standard Operating Procedure (SOP). The ANSI Z 136.1 standard requires an SOP for a Class IV laser and recommends SOP's for Class IIIB lasers.
The key to developing an effective SOP is the involvement of those individuals who operate, maintain and service the equipment under guidance of the LSO. Most laser equipment comes with instructions for safe operation by the manufacturers; however, sometimes the instructions are not well suited to a specific application due to special use conditions.
- Alignment Procedures. Many laser eye accidents occur during alignment. The procedures require extreme caution. A written SOP is recommended for all recurring alignment tasks.
- Limitations on Spectators. Persons unnecessary to the laser operation should be kept away. For those who do enter a laser area with unenclosed Class IIIB or Class IV beam paths, appropriate eye protection and instruction is required.
- Protective Equipment. Protective equipment for laser safety generally means eye protection in the form of goggles or spectacles, clothing, and barriers and other devices designed for laser protection.
- Laser Protective Eyewear and Clothing
- Eye-protection devices designed to protect against radiation from a specific laser system shall be used when engineering controls are inadequate to eliminate the possibility of potentially hazardous eye exposure (i.e., whenever levels of accessible emission exceed the appropriate MPE levels.) This generally applies only to Class IIIB and Class IV lasers. All laser eye wear shall be clearly labeled with OD values and wavelengths for which protection is afforded.
- Skin protection can best be achieved through engineering controls. If the potential exists for damaging skin exposure, particularly for ultraviolet lasers (0.200-0.400 m), then skin covers and or sun-screen creams are recommended. For the hands, gloves will provide some protection against laser radiation. Tightly woven fabrics and opaque gloves provide the best protection. A laboratory jacket or coat can provide protection for the arms. For Class IV lasers, flame-resistant materials may be best.
- In general, other controls should serve as primary protection rather than depending on employees to use protective eye wear. Many accidents have occurred when eye wear was available but not worn. This may be because laser protective eye wear is often dark, uncomfortable to wear, and limits vision.
- Laser Barriers and Protective Curtains
- Area control can be effected in some cases using special barriers specifically designed to withstand either direct or diffusely scattered beams. The barrier will be described with a barrier threshold limit (BTL): the beam will penetrate the barrier only after some specified exposure time, typically 60 seconds. The barrier is located at a distance from the laser source so that the BTL is not exceeded in the worst-case exposure scenario.
- Currently available laser barriers exhibit BTL's ranging from 10 to 350 W/cm2 for different laser wavelengths and power levels. An analysis conducted in a manner similar to the NHZ evaluations described previously can establish the recommended barrier type and installation distances for a given laser. It is essential that the barrier also not support combustion or be itself consumed by flames during or following a laser exposure.
- Laser Protective Eyewear and Clothing
J. Engineering Controls
Engineering controls are normally designed and built into the laser equipment to provide for safety. In most instances, these will be included on the equipment (provided by the laser manufacturer) as part of the "performance requirements" mandated by the FLPPS. Specifics on some of the more important engineering controls recommended in the ANSI Z 136.1 standard are detailed as follows:
- Protective Housing. A laser shall have an enclosure around it that limits access to the laser beam or radiation at or below the applicable MPE level. A protective housing is required for all classes of lasers except, of course, at the beam aperture. In some cases, the walls of a properly enclosed room area can be considered as the protective housing for an open beam laser. Such a "walk-in" enclosure can also be a FDA/CDRH Class I provided that controls preclude operation with personnel within the room (viz.: pressure sensitive floor-mat switches, IR sensors, door interlocks, etc.)
- Master Switch Control. All Class IV lasers and laser systems require a master switch control. The switch can be operated by a key or computer code. When disabled (key or code removed), the laser cannot be operated. Only authorized system operators are to be permitted access to the key or code. Inclusion of the master switch control on Class IIIB lasers and laser systems is also recommended but not required.
- Optical Viewing System Safety. Interlocks, filters, or attenuators are to be incorporated in conjunction with beam shutters when optical viewing systems such as telescopes, microscopes, viewing ports, or screens are used to view the beam or beam-reflection area. For example, an electrical interlock could prevent laser system operation when a beam shutter is removed from the optical system viewing path. Such optical filter interlocks are required for all except Class I lasers.
- Beam Stop or Attenuator. Class IV lasers require a permanently attached beam stop or attenuator which can reduce the output emission to a level at or below the appropriate MPE level when the laser system is on "standby." Such a beam stop or attenuator is also recommended for Class IIIA and Class IIIB lasers.
- Laser Activation Warning System. An audible tone or bell and/or visual warning (such as a flashing light) is recommended as an area control for Class IIIB laser operation. Such a warning system is mandatory for Class IV lasers. Such warning devices are to be activated upon system start-up and are to be uniquely identified with the laser operation. Verbal "countdown" commands are an acceptable audible warning and should be a part of the SOP.
- Service Access Panels. The ANSI Z 136.1 standard requires that any portion of the protective housing that permits direct access to an embedded Class IIIB or Class IV laser (intended for removal only by service personnel) must have either an interlock or require a tool in the removal process. If an interlock is used and is defeatable, a warning label indicating this fact is required on the housing near the interlock. The design shall not allow replacement of a removed panel with the interlock in the defeated condition.
The FDA/CDRH Federal Laser Product Performance Standard requires warning labels on removable protective housing panels under all conditions.
- Protective Housing Interlock Requirements
- Interlocks, which cause beam termination or reduction of the beam to MPE levels, must be provided on all panels intended to be opened during operation and maintenance of all Class IIIA, Class IIIB, and Class IV lasers. The interlocks are typically electrically connected to a beam shutter. The removal or displacement of the panel closes the shutter and eliminates the possibility of hazardous exposures.
- Under the requirements of the ANSI Z 136 Standard, for embedded Class IIIB and Class IV lasers only, the interlocks are to be "fail-safe." This usually means that dual, redundant, electrical series-connected interlocks are associated with each removable panel.
- Adjustments or procedures during service on the laser shall not cause the safety interlocks to become inoperative or the laser radiation outside a Class I laser protective housing to exceed the MPE limits, unless a temporary laser-controlled area is established. The interlocking requirements under the FLPPS are detailed and summarized in .Appendix III:6-2.
- Remote Interlock Connector. All Class IV lasers or laser systems must have a remote interlock connector to allow electrical connections to an emergency master disconnect ("panic button") interlock or to room, door or fixture interlocks. When open circuited, the interlock shall cause the accessible laser radiation to be maintained below the appropriate MPE level. The remote interlock connector is also recommended for Class IIIB lasers.
K. Laser Use Without Protective Housing (All Classes)
In some circumstances, such as during the manufacture of lasers and during research and development, operation of an unenclosed laser or laser system may become necessary. In such cases, the LSO shall determine the hazard and ensure that controls are instituted appropriate to the class of maximum accessible emission to ensure safe operation. Such controls may include but are not limited to:
- access restriction;
- eye protection;
- area controls;
- barriers, shrouds, beam stops, etc.;
- administrative and procedural controls; and
- education and training.
L. Optical Fiber (Light Wave) Communication Systems (OFCS)
- Under normal operation such systems are completely enclosed (Class I) with the optical fiber and optical connectors forming the enclosure. During installation or servicing, or when an accidental break in the cable occurs, the system can no longer be considered enclosed. If engineering controls limit the accessible emission to levels below the applicable MPE (irradiance), no controls are necessary. If the accessible emission is above the MPE, the following requirements shall apply:
- Only authorized trained personnel shall be permitted to perform service on light wave transmission systems if access to laser emission is required.
- Only authorized trained personnel shall be permitted to use the laser test equipment (Optical Loss Test Set, Optical Time Domain Reflectometer, etc.) during installation and/or service.
- All unauthorized personnel shall be excluded from the immediate area of access to laser radiation during service and installation when there is a possibility that the system may become energized. The immediate area shall be considered a temporary laser-controlled area.
- Staring into the end of any broken, severed, or unterminated optical fiber or cable shall be avoided.
- The end of any broken, severed, or unterminated optical fiber shall not be viewed with unfiltered optical instruments (microscopes, telescopes, etc.) An exception to this is the use of indirect image converters such as an infrared image converter or closed-circuit television system for verification that a fiber is not energized.
- During a splicing operation (either installation or service), if it is required that the ends of the fiber be examined with an eye-loupe for a satisfactory cut, only an eye-loupe containing an appropriate filter shall be used. If a fusion splicer is used, the appropriate operating safety procedures shall be rigidly adhered to.
VII. Bibliography
American National Standards Institute, American National Standard for the Safe Use of Lasers: ANSI Z 136.1 (1993), Laser Institute of America, New York, NY (1993).
American National Standards Institute, American National Standard for the Safe Use of Optical Fiber Communication Systems Utilizing Laser Diode and LED Sources: ANSI Z 136.2 (1988), Laser Institute of America, Orlando, Florida, 1988.
American National Standards Institute, American National Standard for the Safe Use Lasers in the Health Care Environment: ANSI Z 136.3 (1988), Laser Institute of America, Orlando, Florida, 1988.
Food and Drug Administration: Regulations for the Administration and Enforcement of the Radiation Control for Health and Safety Act of 1968 (Lasers), Center for Devices and Radiological Health, Food and Drug Administration (DHHS), 21 CFR Chapter 1, 1968.
Food and Drug Administration: Performance Standard for Laser Products, Center for Devices and Radiological Health, Food and Drug Administration (DHHS), 50 CFR 161: 33682-33702, 1985.
Food and Drug Administration: Compliance Guide for Laser Products, Center for Devices and Radiological Health, Food and Drug Administration (DHHS), FDA 86-8260.
Doyle, Daryl and Kokasa, John, Laser Processing of Kevlar: Hazardous Chemical By-products, Proceedings of ICALEO, Laser Institute of America, Toledo, Ohio, 1986.
Rockwell, R. James, Jr., Ed., Laser Safety Training Manual - Sixth Edition, Rockwell Associates, Inc., Cincinnati, Ohio, 1989.
Sliney, David H. and Wolbarsh, Myron L., Safety With Lasers and Other Optical Sources. New York, Plenum, 1980.
Rockwell, R. James, Jr., "Ensuring safety in laser robotics," Lasers and Applications, 3(11): 65-69, November 1984.
Rockwell, R. James, Jr., "Fundamentals of Industrial Laser Safety." In Industrial Laser Annual Handbook, M. Levitt and D. Belforte, Eds. Penn Well Books, Tulsa, Okla., pp. 131-148, 1986.
Laser Institute of America, "Safety information on electrical hazards," Laser News, Laser Inst. of America, 6(5): 8-14, September 1984.
Doyle, D.J. and Kokosa, J.M., "Hazardous By-Products of Plastics Processing with Carbon Dioxide Lasers." In: Laser Welding, Machining and Materials Processing: C. Albright, Ed. Proceedings of ICALEO, IFS LTD., Bedford, U.K., pp. 201-203, 1985.
Rockwell, R. James, Jr. and Moss, C.E., "Optical radiation hazards of laser welding processes, part I: Nd:YAG laser," The Journal of The American Industrial Hygiene Association, 44(8): 572-579, August 1983.
Rockwell, R. James, Jr. and Moss, C.E., "Optical radiation hazards of laser welding processes, part II: carbon dioxide laser," The Journal of The American Industrial Hygiene Association, 50(8): 419-427, August 1989.
Rockwell, R. James, Jr., "Laser accidents: are they all reported and what can be learned from them?" Journal of Laser Applications, Laser Institute of America, Toledo, Ohio, pp. 53-57,October 1989.
Underwriters Laboratories Inc., UL 1740: Standard for Industrial Robots and Robotic Equipment. Underwriters Laboratories Inc. Northbrook, Ill., 1995.
Appendix III:6-1. FDA/CDRH Requirements for Laser Products
Requirements |
----------- Class1 ----------- |
|||||
---|---|---|---|---|---|---|
I | IA | II | IIIA | IIIB | IV | |
Performance (all laser products) | ||||||
Protective housing | R2 | R2 | R2 | R2 | R2 | R2 |
Safety interlock | R3,4 | R3,4 | R3,4 | R3,4 | R3,4 | R3,4 |
Location of controls | _ | R | R | _ | R | R |
Viewing optics | R | R | R | R | R | R |
Scanning safeguard | R | R | R | R | R | R |
Performance (laser systems) | ||||||
Remote control connector | _ | _ | _ | _ | R | R |
Key control | _ | _ | _ | _ | R | R |
Emission indicator | _ | _ | R | R | R10 | R10 |
Beam attenuator | _ | _ | R | R | R | R |
Reset | _ | _ | _ | _ | _ | R13 |
Performance (specific purpose products) | ||||||
Medical | S | S | S | S8 | S8 | S8 |
Surveying, leveling, alignment | S | S | S | S | NP | NP |
Demonstration | S | S | S | S | S11 | S11 |
Labeling (all laser products) | ||||||
Certification and identification | R | R | R | R | R | R |
Protective housing | D5 | R5 | R5 | R5 | R5 | R5 |
Aperture | _ | _ | R | R | R | R |
Class warning | _ | R6 | R7 | R9 | R12 | R12 |
Information (all lasers) | ||||||
User information | R | R | R | R | R | R |
Product literature | _ | R | R | R | R | R |
Service information | R | R | R | R | R | R |
Key:
|
||||||
Notes:
|
Appendix III:6-2. FDA/CDRH Federal Product Performance Standard Evaluation Outline
LASER EMISSIONS DESCRIPTION: | ||||||
---|---|---|---|---|---|---|
Type: | ||||||
CLASSIFICATION DESIGNATION: | ||||||
Class I | [ ] | Class IIIA | [ ] | |||
Class IIA | [ ] | Class IIIB | [ ] | |||
Class II | [ ] | Class IV | [ ] | |||
PERFORMANCE REQUIREMENTS: | PRESENT: | |||||
[YES] | [NO] | |||||
Protective Housing -- All Classes -- 1040.10(f)(1) | [ ] | [ ] | ||||
Safety Interlocks -- All Classes -- 1040.10(f)(2) NOTE: requirements are dependent on class of internal radiation Nondefeatable Interlocks Defeatable Interlocks |
[ ] [ ] |
[ ] [ ] |
||||
Remote Interlock Connector -- Classes IIIB & IV -- 1040.10(f)(3) | [ ] | [ ] | ||||
Key Control -- Classes IIIB & IV -- 1040.10(f)(4) | [ ] | [ ] | ||||
Emission Indicator -- Classes II, III, & IV -- 1040.10(f)(5) Class II & IIIA: no delay -- 1040.10(f)(5)(i) Class IIIB & IV: with delay -- 1040.10(f)(5)(ii) |
[ ] [ ] |
[ ] [ ] |
||||
Indicators on laser and controls, if separated by more than 2 meters. NOTE: Class IIA is exempt. |
[ ] | [ ] | ||||
Beam Attenuator -- Classes II, III & V -- 1040.10(f)(6) | [ ] | [ ] | ||||
Location of Controls -- Classes IIA, II, III & IV -- 1040.10(f)(7) | [ ] | [ ] | ||||
Viewing Optics -- All Classes -- 1040.10(f)(8) | [ ] | [ ] | ||||
Scanning Safeguard -- All Classes -- 1040.10(f)(9) | [ ] | [ ] | ||||
Manual Reset Mechanism -- Class IV -- 1040.10(f)(10) | [ ] | [ ] | ||||
LABEL REQUIREMENTS: | PRESENT: | |||||
[YES] | [NO] | |||||
Certification Label -- All Classes -- 1010.2 | [ ] | [ ] | ||||
Identification Label -- All Classes -- 1010.3 | [ ] | [ ] | ||||
Class Designation and Warning Label -- All Classes except Class I -- 1040.10(g)(1,2,& 3) |
[ ] | [ ] | ||||
Radiation Output Information (Position 2 on label) -- Classes II, III & IV -- 1040.10(g)(4) NOTE: Class IIA is exempt. |
[ ] | [ ] | ||||
Aperture Label -- Classes II, III & IV -- 1040.10(g)(5) NOTE: Class IIA is exempt. |
[ ] | [ ] | ||||
Noninterlocked Protective Housing Labels (i.e. service panels) -- All Classes -- 1040.10(g)(6) |
[ ] | [ ] | ||||
Defeatably Interlocked Protective Housing Labels -- 1040.10(g)(7) | [ ] | [ ] | ||||
Warning for Invisible Radiation (wherever applicable - all labels) -- 1040.10(g)(8) | [ ] | [ ] | ||||
Positioning of Labels -- 1040.10(g)(9) | [ ] | [ ] | ||||
Label Specifications -- 1040.10(g)(10) | [ ] | [ ] | ||||
INFORMATION REQUIREMENTS: | PRESENT: | |||||
[YES] | [NO] | |||||
User Information -- 1040.10(h)(1) | [ ] | [ ] | ||||
Operator & Maintenance Instructions -- (h)(1)(i) | [ ] | [ ] | ||||
Statement of Parameters -- (h)(1)(ii) | [ ] | [ ] | ||||
Label Reproductions -- (h)(1)(iii) | [ ] | [ ] | ||||
Listing of Controls, Adjustments, and Procedures, including Warnings -- (h)(1)(iv) | [ ] | [ ] | ||||
Service Information -- 1040.10(h)(2)(ii) | [ ] | [ ] |
Appendix III:6-3. The American National Standards Institute (ANSI)
An American National Standard implies a consensus of those substantially concerned with its scope and provisions. These standards are intended as a guide to aid the manufacturer, the consumer and the general public. There is, however, no inherent requirement for anyone or any company to adhere to an ANSI standard. Compliance is voluntary unless specifically required by some alliance. For example, the Federal Department of Energy requires adherence to the ANSI Z 136.1 by their internal staff as well as all contractor organizations. At present, the following ANSI standards can be useful in laser safety matters:
ANSI Z 136.1 (1993): "FOR THE SAFE USE OF LASERS"
This is the master or "parent" standard in the Z 136 series. Originally published in 1973, this standard has gone through revisions in 1976, 1980, 1986, and 1993. Revisions are currently being considered by the committee for the next publication which should occur in 1991.
The Z 136.1 (1993) standard includes the basis of laser hazard assessment including the Nominal Hazard Zone (NHZ) concept and measurements, establishes Maximum Permissible Exposure (MPE) limits based on bioeffects of the eye and skin, introduces a general classification scheme, specifies the recommended control measures, outlines suggested medical surveillance practice, specifies training requirements and recommends practices for other (nonbeam) concerns.
ANSI Z 136.2 (1988): "FOR THE SAFE USE OF OPTICAL FIBER COMMUNICATION SYSTEMS UTILIZING LASER DIODE AND LED SOURCES"
This ANSI Standard provides guidance for the safe use of optical fiber communications systems (OFCS) utilizing laser diodes and/or LED sources by defining control measures for each of four service group (SG) classifications. This concept eliminates measurements and/or calculations. The standard is limited to OFCS that emit at power levels at or below 0.5 W.
The Z 136.2 standard addresses the same general topics as the base Z 136.1 standard. The significant variation between the two standards lies in the definition of a Maximum Permissible Irradiance (MPI) value based upon a 5 mm limiting aperture in the visible and near-infrared spectral regions. This is in contrast to the larger 7mm limiting aperture used in this spectral region in the ANSI Z 136.1 Standard.
ANSI Z 136.3 (1988): "FOR THE SAFE USE OF LASERS IN HEALTH CARE FACILITIES"
The ANSI Z 136.3 Standard provides guidance for the safe use of lasers for diagnostic and therapeutic uses in health care facilities. The publication includes an extensive appendix that details suggested practice in fourteen medical subspecialty areas. (Although the appendix is not technically a part of the standard.)
Major emphasis is included on the associated hazard topics of airborne contaminants ("plume") and electrical and fire hazards. The information in the base of the standard has been kept less mathematical and refers the reader frequently to the ANSI Z 136.1 Standard if such detail is needed. Summary charts provide information on MPE and NHZ values. Control measures are identical, in most cases, to the master standards, with items special to medical laser systems (foot pedals, output calibration, QC and safety audits, etc.) given additional coverage.
ANSI/NFPA 70-1990: THE NATIONAL ELECTRICAL CODE - 1990 HANDBOOK
The fifth edition of the National Electrical Code Handbook is based on the new edition of The National Fire Protection Association's NFPA-70, The National Electrical Code. This document, authored by the NFPA's Electrical Code Committee, is unquestionably the most authoritative and comprehensive document on electrical safety and addresses the topic from both a fire and electrocution point of view. The Handbook includes the complete text of the Code provisions along with explanations. It provides a basis for safety procedures for all electrical hazards associated with lasers.
ANSI Z 87.1 (1989): "PRACTICE FOR OCCUPATIONAL AND EDUCATIONAL EYE AND FACE PROTECTION"
This ANSI standard is included in this listing mainly because a high percentage of industrial facilities require that the eye protection used in their plants meet the ANSI Z 87 requirements. In the past, this basically referred to the "drop ball test" in which a 1-inch diameter ball weighing 2.4 ounces and dropped 50 inches must not fracture the protective lens.
The new Z 87.1 (1989) requires a high-velocity impact test wherein small (1/4 in) diameter steel balls weighing 0.04 ounces are projected at high velocity at the protective filter. In addition, there is a high-mass impact test in which a 1-inch diameter, pointed, heat-treated steel projectile (30-degree cone) that weighs 17.6 ounces is dropped at specified distances. These new requirements place far more stringent performance requirements on safety eye wear.
Appendix III:6-4. Warning Signs
Figure III:6-2. Caution
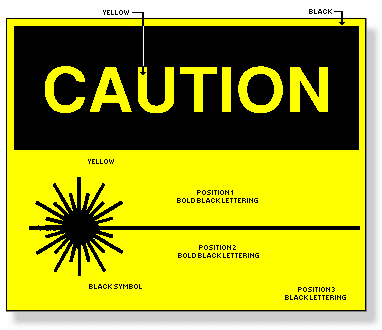
Figure III:6-3. Danger
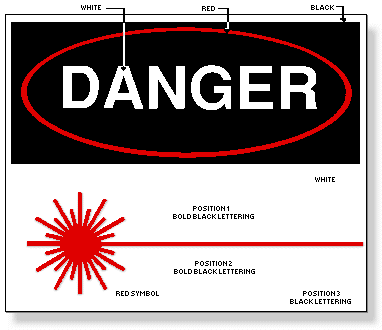
Figure III:6-4. Laser Repair Notice
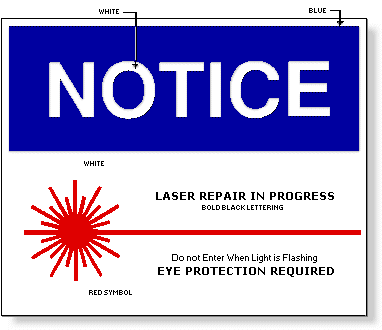
Appendix III:6-5. Glossary of Laser Terms
- Absorb
- To transform radiant energy into a different form, with a resultant rise in temperature.
- Absorption
- Transformation of radiant energy to a different form of energy by the interaction of matter, depending on temperature and wavelength.
- Accessible Emission Level
- The magnitude of accessible laser (or collateral) radiation of a specific wavelength or emission duration at a particular point as measured by appropriate methods and devices. Also means radiation to which human access is possible in accordance with the definitions of the laser's hazard classification.
- Accessible Emission Limit (AEL)
- The maximum accessible emission level permitted within a particular class. In ANSI Z 136.1, AEL is determined as the product of accessible emission Maximum Permissible Exposure limit (MPE) and the area of the limiting aperture (7 mm for visible and near-infrared lasers).
- Aperture
- An opening through which radiation can pass.
- Argon
- A gas used as a laser medium. It emits blue-green light primarily at 448 and 515 nm.
- Attenuation
- The decrease in energy (or power) as a beam passes through an absorbing or scattering medium.
- Aversion Response
- Movement of the eyelid or the head to avoid an exposure to a noxious stimulant, bright light. It can occur within 0.25 seconds, and it includes the blink reflex time.
- Beam
- A collection of rays that may be parallel, convergent, or divergent.
- Beam Diameter
- The distance between diametrically opposed points in the cross section of a circular beam where the intensity is reduced by a factor of e-1 (0.368) of the peak level (for safety standards). The value is normally chosen at e-2 (0.135) of the peak level for manufacturing specifications.
- Beam Divergence
- Angle of beam spread measured in radians or milliradians (1 milliradian = 3.4 minutes of arc or approximately 1 mil). For small angles where the cord is approximately equal to the arc, the beam divergence can be closely approximated by the ratio of the cord length (beam diameter) divided by the distance (range) from the laser aperture.
- Blink Reflex
- See aversion response.
- Brightness
- The visual sensation of the luminous intensity of a light source. The brightness of a laser beam is most closely associated with the radio-metric concept of radiance.
- Carbon Dioxide
- Molecule used as a laser medium. Emits far energy at 10,600 nm (10.6 μm).
- Closed Installation
- Any location where lasers are used which will be closed to unprotected personnel during laser operation.
- CO2 Laser
- A widely used laser in which the primary lasing medium is carbon dioxide gas. The output wavelength is 10.6 μm (10600 nm) in the far infrared spectrum. It can be operated in either CW or pulsed.
- Coherence
- A term describing light as waves which are in phase in both time and space. Monochromaticity and low divergence are two properties of coherent light.
- Collimated Light
- Light rays that are parallel. Collimated light is emitted by many lasers. Diverging light may be collimated by a lens or other device.
- Collimation
- Ability of the laser beam to not spread significantly (low divergence) with distance.
- Continuous Mode
- The duration of laser exposure is controlled by the user (by foot or hand switch).
- Continuous Wave (CW)
- Constant, steady-state delivery of laser power.
- Controlled Area
- Any locale where the activity of those within are subject to control and supervision for the purpose of laser radiation hazard protection.
- Diffuse Reflection
- Takes place when different parts of a beam incident on a surface are reflected over a wide range of angles in accordance with Lambert's Law. The intensity will fall off as the inverse of the square of the distance away from the surface and also obey a Cosine Law of reflection.
- Divergence
- The increase in the diameter of the laser beam with distance from the exit aperture. The value gives the full angle at the point where the laser radiant exposure or irradiance is e-1 or e-2 of the maximum value, depending upon which criteria is used.
- Embedded Laser
- A laser with an assigned class number higher than the inherent capability of the laser system in which it is incorporated, where the system's lower classification is appropriate to the engineering features limiting accessible emission.
- Emission
- Act of giving off radiant energy by an atom or molecule.
- Enclosed Laser Device
- Any laser or laser system located within an enclosure which does not permit hazardous optical radiation emission from the enclosure. The laser inside is termed an "embedded laser."
- Energy (Q)
- The capacity for doing work. Energy is commonly used to express the output from pulsed lasers and it is generally measured in Joules (J). The product of power (watts) and duration (seconds). One watt second = one Joule.
- Excimer "Excited Dimer"
- A gas mixture used as the active medium in a family of lasers emitting ultraviolet light.
- Fail-safe Interlock
- An interlock where the failure of a single mechanical or electrical component of the interlock will cause the system to go into, or remain in, a safe mode.
- Gas Discharge Laser
- A laser containing a gaseous lasing medium in a glass tube in which a constant flow of gas replenishes the molecules depleted by the electricity or chemicals used for excitation.
- Gas Laser
- A type of laser in which the laser action takes place in a gas medium.
- Helium-Neon (HeNe) Laser
- A laser in which the active medium is a mixture of helium and neon. Its wavelength is usually in the visible range. Used widely for alignment, recording, printing, and measuring.
- Infrared Radiation (IR)
- Invisible electromagnetic radiation with wavelengths which lie within the range of 0.70 to 1000 μm. These wavelengths are often broken up into regions: IR-A (0.7-1.4 μm), IR-B (1.4-3.0 μm) and IR-C (3.0-1000 μm).
- Intrabeam Viewing
- The viewing condition whereby the eye is exposed to all or part of a direct laser beam or a specular reflection.
- Irradiance (E)
- Radiant flux (radiant power) per unit area incident upon a given surface. Units: Watts per square centimeter. (Sometimes referred to as power density, although not exactly correct).
- Laser
- An acronym for light amplification by stimulated emission of radiation. A laser is a cavity with mirrors at the ends, filled with material such as crystal, glass, liquid, gas or dye. It produces an intense beam of light with the unique properties of coherency, collimation, and monochromaticity.
- Laser Accessories
- The hardware and options available for lasers, such as secondary gases, Brewster windows, Q-switches and electronic shutters.
- Laser Controlled Area
- See Controlled Area.
- Laser Device
- Either a laser or a laser system.
- Laser Medium (Active Medium)
- Material used to emit the laser light and for which the laser is named.
- Laser Rod
- A solid-state, rod-shaped lasing medium in which ion excitation is caused by a source of intense light, such as a flash lamp. Various materials are used for the rod, the earliest of which was synthetic ruby crystal.
- Laser Safety Officer (LSO)
- One who has authority to monitor and enforce measures to control laser hazards and effect the knowledgeable evaluation and control of laser hazards.
- Laser System
- An assembly of electrical, mechanical and optical components which includes a laser. Under the Federal Standard, a laser in combination with its power supply (energy source).
- Lens
- A curved piece of optically transparent material which, depending on its shape, is used to either converge or diverge light.
- Light
- The range of electromagnetic radiation frequencies detected by the eye, or the wavelength range from about 400 to 760 nm. The term is sometimes used loosely to include radiation beyond visible limits.
- Limiting Aperture
- The maximum circular area over which radiance and radiant exposure can be averaged when determining safety hazards.
- Maintenance
- Performance of those adjustments or procedures specified in user information provided by the manufacturer with the laser or laser system, which are to be performed by the user to ensure the intended performance of the product. It does not include operation or service as defined in this glossary.
- Maximum Permissible Exposure (MPE)
- The level of laser radiation to which a person may be exposed without hazardous effect or adverse biological changes in the eye or skin.
- Nd:Glass Laser
- A solid-state laser of neodymium:glass offering high power in short pulses. A Nd-doped glass rod used as a laser medium to produce 1064 nm light.
- Nd:YAG Laser
- Neodymium:Yttrium Aluminum Garnet. A synthetic crystal used as a laser medium to produce 1064 nm light.
- Neodymium (Nd)
- The rare earth element that is the active element in Nd:YAG laser and Nd:Glass lasers.
- Nominal Hazard Zone (NHZ)
- The nominal hazard zone describes the space within which the level of the direct, reflected or scattered radiation during normal operation exceeds the applicable MPE. Exposure levels beyond the boundary of the NHZ are below the appropriate MPE level.
- Optical Cavity (Resonator)
- Space between the laser mirrors where lasing action occurs.
- Optical Density
- A logarithmic expression for the attenuation produced by an attenuating medium, such as an eye protection filter.
- Optical Fiber
- A filament of quartz or other optical material capable of transmitting light along its length by multiple internal reflection and emitting it at the end.
- Optical Pumping
- The excitation of the lasing medium by the application of light rather than electrical discharge.
- Optical Radiation
- Ultraviolet, visible, and infrared radiation (0.35-1.4 μm) that falls in the region of transmittance of the human eye.
- Output Power
- The energy per second measured in watts emitted from the laser in the form of coherent light.
- Power
- The rate of energy delivery expressed in watts (Joules per second). Thus: 1 Watt = 1 Joule x 1 §
- Protective Housing
- A protective housing is a device designed to prevent access to radiant power or energy.
- Pulse
- A discontinuous burst of laser, light or energy, as opposed to a continuous beam. A true pulse achieves higher peak powers than that attainable in a CW output.
- Pulse Duration
- The "on" time of a pulsed laser, it may be measured in terms of milliseconds, microseconds, or nanoseconds as defined by half-peak-power points on the leading and trailing edges of the pulse.
- Pulsed Laser
- Laser which delivers energy in the form of a single or train of pulses.
- Pump
- To excite the lasing medium. See Optical Pumping or Pumping.
- Pumped Medium
- Energized laser medium.
- Pumping
- Addition of energy (thermal, electrical, or optical) into the atomic population of the laser medium, necessary to produce a state of population inversion.
- Radiant Energy (Q)
- Energy in the form of electromagnetic waves usually expressed in units of Joules (watt-seconds).
- Radiant Exposure (H)
- The total energy per unit area incident upon a given surface. It is used to express exposure to pulsed laser radiation in units of J/cm2.
- Reflection
- The return of radiant energy (incident light) by a surface, with no change in wavelength.
- Refraction
- The change of direction of propagation of any wave, such as an electromagnetic wave, when it passes from one medium to another in which the wave velocity is different. The bending of incident rays as they pass from one medium to another (e.g., air to glass).
- Resonator
- The mirrors (or reflectors) making up the laser cavity including the laser rod or tube. The mirrors reflect light back and forth to build up amplification.
- Ruby
- The first laser type; a crystal of sapphire (aluminum oxide) containing trace amounts of chromium oxide.
- Scanning Laser
- A laser having a time-varying direction, origin or pattern of propagation with respect to a stationary frame of reference.
- Secured Enclosure
- An enclosure to which casual access is impeded by an appropriate means (e.g., door secured by lock, magnetically or electrically operated latch, or by screws).
- Semiconductor Laser
- A type of laser which produces its output from semiconductor materials such as GaAs.
- Service
- Performance of adjustments, repair or procedures on a non-routine basis, required to return the equipment to its intended state.
- Solid Angle
- The ratio of the area on the surface of a sphere to the square of the radius of that sphere. It is expressed in steradians (sr).
- Source
- The term source means either laser or laser-illuminated reflecting surface, i.e., source of light.
- Tunable Laser
- A laser system that can be "tuned" to emit laser light over a continuous range of wavelengths or frequencies.
- Tunable Dye Laser
- A laser whose active medium is a liquid dye, pumped by another laser or flash lamps, to produce various colors of light. The color of light may be tuned by adjusting optical tuning elements and/or changing the dye used.
- Ultraviolet (UV) Radiation
- Electromagnetic radiation with wavelengths between soft X-rays and visible violet light, often broken down into UV-A (315-400 nm), UV-B (280-315 nm), and UV-C (100-280 nm).
- Visible Radiation (light)
- Electromagnetic radiation which can be detected by the human eye. It is commonly used to describe wavelengths in the range between 400 nm and 700-780 nm.
- Wavelength
- The length of the light wave, usually measured from crest to crest, which determines its color. Common units of measurement are the micrometer (micron), the nanometer, and (earlier) the Angstrom unit.
- YAG
- Yttrium Aluminum Garnet, a widely used solid-state crystal composed of yttrium and aluminum oxides and a small amount of the rare earth neodymium.