Lead: Battery Manufacturing eTool
Battery Assembly » Group Burning
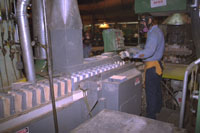
After the plates have been stacked, they are joined with small connecting parts and burned together to form cell elements or groups. This operation is conducted either manually at a burning station or by using an automatic cast-on-strap (COS) machine. The major source of lead exposure in the group burning process comes from lead fumes that workers may inhale during the following operations:
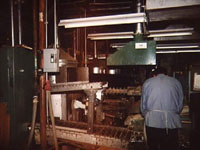
Potential Sources of Exposure
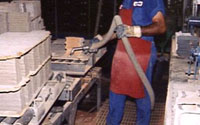
-
Exposure to lead may increase from handling dry plates or moving plates in and out of the workstation.
-
Lead oxide that accumulates on racks, equipment, and floors may become airborne.
-
Lead particles may become airborne when groups are dropped into the cases.
-
Lead particles may become airborne during cleaning and roughing with a wire brush.
-
Increased exposure to lead may occur during drossing or charging the lead pot.
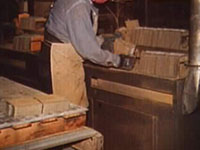
Possible Engineering Controls
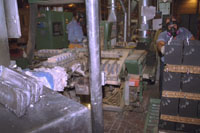
- Install down draft or slot ventilation at the feed end (Figure 3).
- Enclose machine and place in a ventilated room (Figure 4).
-
Provide an access door for maintenance and a small port for drossing and loading the lead pot.
-
Provide local exhaust ventilation at the melting pot, mold heating section, dross pot, lug brush, and the casing areas.
-
Position ventilation slot in the direction of the generated lead particulate, not behind the brush.
-
Install an exhausted semi-enclosure around the brush to help collect particulate entrained in the brush.
-
Install a laminar flow (supplied-air) island above the workstation.
-
Use slot ventilation at burning and group dropping stations.
-
Use an enclosed Lazy Susan for holding the stacked groups for the team stack and burn operations.
-
Place a plastic sheet at the stacking side to control the height of the stacks and prevent cross drafts.
-
Provide an exhaust ventilated enclosure for the lead pot and dross container.
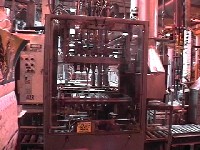
Possible Work Practice Controls
-
Avoid setting torches at excessive temperatures.
-
Tamp plates only over ventilated workstations (Figure 3).
-
Do not bang plates excessively.
-
Use a grating or perforated plate tamping stand.
-
When dropping groups into container, place opening toward exhaust ventilation.
-
Handle groups only with hands; do not lean them against the stomach, chest, or chin.
-
Wear an apron.
-
Maximize the distance between the operators breathing zone and the plates by not stacking assembled groups more than three high.
-
Stand on platform when practical.
-
Keep openings to unventilated enclosures to a minimum.
-
Close access doors to ventilated enclosures.
- Place, do not throw, defective plates into a ventilated scrap barrel.
-
Cover drums with a plastic bag before removing.
-
Provide rubbers or gratings for walking surfaces.
-
Provide adequate PPE, a change of clothes, and shower rooms (see OSHA Lead Requirements for PPE, Housekeeping, and Hygiene Facilities).
-
See Grid Production and Parts Casting for additional possible engineering and work practice controls.
- Maintenance:
-
Ensure that local exhaust ventilation is working properly.
-
Prevent cross drafts.
-
Substitute cooler flames such as air-propane or air-MAP gas for oxy-acetylene.
-
Change torch head to decrease time required for burning.
-
Provide a plastic or glass plate between the breathing zone and the plates.
-
- Housekeeping:
-
Vacuum work stations and adjacent areas to prevent accumulation of oxide dust.
-
Vacuum off each row of plates or groups before use.
-
Vacuum tops of plate trays.
-
Vacuum clean out trays (do not dump them into barrels).
-
Use dust suppression techniques such as keeping floors wet, using dust suppression compounds, or vacuuming.
-
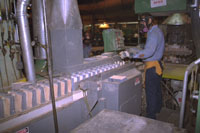
Potential Sources of Exposure
-
Exposure to lead fumes may occur when burning with torches.
-
Exposure to lead may result from moving groups in and out of the workstation and in and out of the burning box.
-
Lead cross contamination can occur between the stacking and the burning stations during the manual group burning process.
-
Lead particles may become airborne when groups are dropped into the cases.
-
Exhaust ports of pneumatic systems may cause settled dust to become airborne.
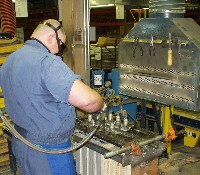
Possible Engineering Controls
- Place the opening toward exhaust ventilation when dropping groups into a container.
-
Use down draft or slot ventilation at the work station.
-
Install a rotating rack so the operator does not need to lean over contaminated racks to reach groups.
- Exhaust the burning box for both fume and dust (Figure 6).
- Use local exhaust ventilation around torch head (Figure 8).
-
Use slot ventilation at burning and group dropping stations.
-
Use a smaller torch tip to lower fume exposure.
-
Use an enclosed Lazy Susan to hold the stacked groups for the stacking and burning operations.
-
Use a laminar flow (supplied-air) island above the operators workstation.
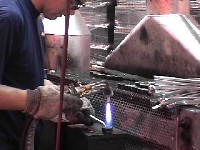
Possible Work Practice Control
-
See Work Practice Controls for Automatic COS Machines.
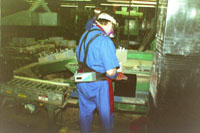
Potential Source of Exposure
-
Exposure to lead may occur while repairing groups.
Possible Engineering and Work Practice Controls
-
Handle groups only with hands (Figure 9).
-
Do not lean groups against the stomach, chest, or chin.
-
Wear an apron.
-
See Battery Repair for addition possible engineering and work practice controls.
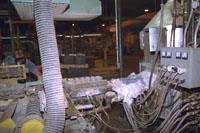
Potential Source of Exposure
-
Lead particulate may become airborne while cleaning molds using compressed air or torches.
Possible Engineering and Work Practice Controls
-
Clean molds using alternative methods, such as vacuuming, that do not produce airborne lead particulate (Figure 10).
- Use local exhaust ventilation around torch head.
-
Use portable side draft or slot ventilation.
Potential Source of Exposure
-
Lead exposure may increase while adjusting and repairing equipment, or during changeovers.
Possible Engineering and Work Practice Controls
-
Ensure that local exhaust ventilation is working properly.
-
Prevent cross drafts.
-
Wear an apron.