Lead: Battery Manufacturing eTool
Lead: Battery Manufacturing » Maintenance
Maintenance personnel are at risk of exposure to lead fumes and dust during maintenance operations involving equipment that is contaminated with lead. Appropriate PPE should be provided and work practices should be followed when performing maintenance on this equipment. There are recommended engineering and work practice controls to minimize employee exposure in the following situations:
Potential Source of Exposure
-
Maintenance shop personnel may be exposed to lead dust when servicing and handling equipment that is contaminated with lead.
Possible Engineering and Work Practice Controls
-
Decontaminate equipment prior to servicing by vacuum, water spray, or mechanical removal such as scraping or brushing in conjunction with local exhaust ventilation.
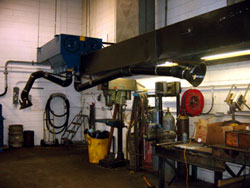
Potential Source of Exposure
-
Exposure to lead may occur when working on contaminated equipment in the maintenance shop. (Figure 1)
Possible Engineering and Work Practice Controls
-
Provide a ventilated work bench.
- Provide exhaust ventilation with HEPA filters.
-
Decontaminate equipment using vacuum, water spray, or mechanical removal such as scraping or brushing in conjunction with local exhaust ventilation.
- Provide low volume and high velocity ventilated hand tools.
- Provide Laminar Flow (Supplied Air) Islands at work stations.
-
Provide wash-up sink for employees in the shop.
-
Keep surfaces free of lead contamination as much as possible.
- Use local exhaust ventilation on torch.
-
Ensure that all shop vacuums are equipped with HEPA filters capable of removing lead.
-
Empty vacuums in a manner that minimizes the reentry of lead into the shop.
A well-designed system and a continuing preventive maintenance program are key in preventing and controlling ventilation system problems.
Elements of a Good Maintenance Program
-
Establish a safe place to file drawings, specifications, fan curves, operating instructions, and other papers generated during design, construction, and testing.
-
Establish a program of periodic inspection.
- The types and frequencies of inspections depend on the operation of the system and other factors.
-
Daily: Visually inspect hoods, ductwork, access and clean-out doors, blast gate positions, hood static pressure, pressure drop across air cleaner, and verbally communicate with users ("How is the system performing today?").
-
Weekly: Check air cleaner capacity, fan housing, pulley belts.
-
Monthly: Check air cleaner components.
-
See Example Checklist.
A quick way to check for settled material in a duct is to take a broomstick and tap the underside of all the horizontal ducts. If the tapping produces a "clean" sheet metal sound, the duct is clear. If the tapping produces heavy, thudding sounds, there may be settled dust in the duct.
-
- The types and frequencies of inspections depend on the operation of the system and other factors.
-
Establish a preventive maintenance program.
-
Certain elements of any ventilation system should be checked on a regular schedule and replaced if found to be defective.
-
See Example Checklist.
-
OSHA Technical Manual: Ventilation Investigation. OSHA (1992), 26 pages. This manual describes the use of supply and exhaust ventilation to control emissions, exposures, and chemical hazards in the workplace.
-
-
Provide worker training.
-
Workers need to be trained about the purpose and functions of the ventilation system. For example, they need to know how to work safely and how to best use the ventilation system. Exhaust hoods do little good if the welder does not know that the hood must be positioned close to the work.
-
-
Keep written records.
-
Maintain written documentation, not only of original installations but also of all modifications as well as problems and resolutions.
-