Lead: Battery Manufacturing eTool
Oxide and Grid Processing » Oxide Production
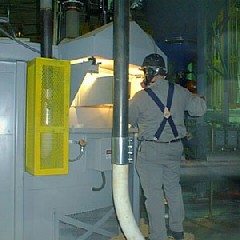
Lead oxide, which is used to create the paste used on the battery plates, is either produced by the Ball Mill Process or the Barton-Like Process. It may also be purchased from an oxide producer (see receiving).
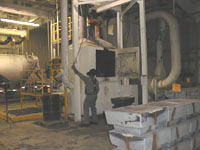
Potential Sources of Exposure
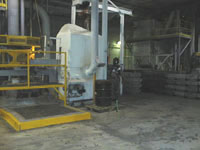
-
Lead dust can become airborne due to improper air flow or exhaust ventilation, which results in "puffing" of lead oxide at the mill inlet.
-
Exposure may occur from handling lead pigs while loading the mill pots or the ball mill.
-
Lead oxide dust may spill or leak from trunnion seals, bearing seals, conveying systems, and transfer points.
-
Exposure to lead may occur when drossing the lead pots during the Barton process (Figure 1) and during maintenance operations that require entry into the pot for cleanout.
-
Lead oxide may leak or spill during drive fitting and transfer operations.
-
Lead exposure may occur while collecting and testing oxide samples.
-
Operators may be exposed to lead oxide while cleaning the oxide production line.
-
Exposure may be due to vehicular traffic in adjacent roadways stirring up oxide.
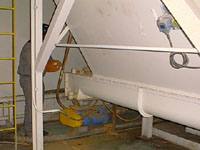
Possible Engineering Controls
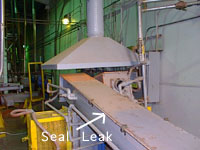
- Use local exhaust ventilation:
- Install a hood enclosure for the lead melting pot.
-
Install a hood enclosure on the dross pot or barrel.
-
Install tightly enclosed conveyer systems with ventilation at transfer stations (Figures 3 and 4).
-
Use exhaust ventilation at the sampling and process test stations (Figure 5).
-
Use exhaust ventilation around the agitator shaft or air intake of the Barton pot.
-
Place a hooded duct in close proximity to the air intake to contain the volume of a "puff" in order to prevent it from entering the workplace.
-
Place local exhaust ventilation around dust generation points.
- Ensure that drum filling operations are ventilated and enclosed.
-
Add a pressure relief valve, vented through a filtering system, to the screw conveyer to vent dust generated during the transfer operation.
- Isolate the process:
-
Separate the operation from the rest of the plant and keep it under negative pressure.
-
Build a positive pressure control room for the operator.
-
-
Use pneumatic conveyers for handling barrels rather than handling them manually.
-
Use automatic sampling instead of manual sampling.
-
Install a vertical classifier ahead of the normal classifier and oxide collection equipment to reduce "puffing" of the Barton Process equipment.
-
Protect or insulate storage tanks from the weather to prevent water condensation on the inside walls.
-
Mechanize the system of feeding lead pots or mills.
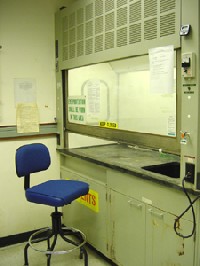
Possible Work Practice Controls
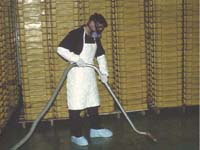
-
Notify supervisor of oxide leaks and perform temporary repairs immediately.
-
Fill drums inside ventilated hoods or enclosures.
-
Wipe down the exterior of drums before transferring them to storage or to other areas.
-
Cap the drums before vacuuming.
-
Prevent lead buildup on the inside perimeter of the pot because it can slough off and cause puffing.
-
Provide adequate PPE, a change of clothes, and shower rooms (see OSHA Lead Requirements for PPE, Housekeeping, and Hygiene Facilities).
- Maintenance:
-
Ensure that the local exhaust ventilation is working properly (Figure 2).
- Develop a written schedule of inspections for oxide mill operators.
-
The schedule should include weekly inspections of equipment such as overhead ducts and rotary valves.
-
-
- Housekeeping:
-
Vacuum all oxide spills immediately with a central vacuum system or a HEPA vacuum.
-
Vacuum equipment surfaces and floors whenever possible during each shift (Figure 6).
-
Use dust suppression compounds in place of water for dust suppression in the mill area to prevent the possibility of oxide fires and the mixing of water and molten lead.
-
Periodically shut down the plant to perform a thorough cleanup of settled dust.
-
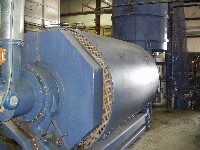
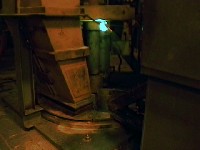