Lead: Battery Manufacturing eTool
Plate Processing » Grid Pasting
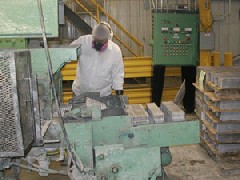
During the pasting process, lead oxide paste is applied to the grid panels in a pasting machine to fill the spaces of the grid. The major source of lead exposure in the pasting process comes from lead oxide in the paste which can become easily airborne once it dries.
Workers may be exposed to lead dust during pasting and take-off operations. Contaminated gloves, clothing, tools, and equipment may also be a source of lead exposure.
- Pasting operations
- Video exposure monitoring: shoveling paste
- Take-Off/Offbearer operations
- Video exposure monitoring: pasting take off
Potential Sources of Exposure
-
Dried paste on equipment and other areas, such as the mixer, cone feeder, paste transfer equipment, paste return belt, pasting machine, floors, and adjacent areas, may become airborne due to equipment vibration or by being disturbed and as described below (Figure 1):
-
Scraping lead oxide off the hopper and exterior of the cone feeder during cleanup and upsets.
-
Inadequate exhaust ventilation on the drying oven.
-
Settled oxide on the housings of rotating drives and motor cooling fans (see Figure 2).
-
Improper handling and disposal of paste accumulated on the floor or other surfaces (see Figure 3).
-
Dried dust on equipment, controls, and gloves during operation of equipment located near the breathing zone.
-
Dried oxide on the floor or other surfaces being disturbed by employees, vehicle traffic, or cross-drafts.
-
Possible Engineering Controls
-
Use a laminar flow (supplied-air) island providing 90-175 feet per minute at the face velocity of the plenum.
-
Use plastic skirting to increase hood efficiency (the skirt prevents induced air from entering the clean air stream).
-
-
Install exhaust ventilation around paste machine feed hopper to prevent dust generation during scraping, cleanup, and operation (see Figure 4).
-
Enclose oven all the way to the floor.
-
The oven or conveyor chain may stir up or re-suspend settled lead oxide dust that may escape through an open door.
-
-
Maintain negative pressure in drying oven ventilation.
-
Ventilation efficiency decreases if oxide is allowed to build up in the bottom of the drying oven.
-
-
Provide a fine water mist for paste return belts to avoid material drying and dispersion (see Figure 5).
-
If this is recycled water, it will become a source of lead in air.
-
Filtered water can be used to wash down pasting if the area is kept wet.
-
-
Use encapsulated motors, if possible, to reduce dust generation.
Possible Work Practice Controls
-
Prohibit cooling fans or open doors and windows, which cause cross drafts or thermals and destroy effectiveness of local exhaust.
-
Keep oven doors closed at all times.
-
Keep breathing zone away from oxide or dry paste.
-
Place machine controls at machine level, not overhead near hopper.
-
-
Provide adequate PPE, change of clothes, and shower rooms (see OSHA Lead Requirements for PPE, Housekeeping, and Hygiene Facilities).
-
Housekeeping:
-
Clean up paste spills immediately.
-
If a paste spill was caused by mechanical problems, report it to a supervisor.
-
-
Shovel paste and dispose of it in ventilated barrels in a manner to minimize airborne dispersion of lead.
-
Clean out oven regularly.
-
Buildup of oxide dust in the oven may cause an imbalance in the ventilation and raise airborne lead concentrates. Note: Water sprayed on a hot oven conveyor belt can be a high source of lead-in-air.
-
-
Use dust suppression techniques such as keeping floors wet, using dust suppression compounds or vacuuming.
-
Using recycled water may increase lead-in-air levels if the water dries. Air bubbles in the water may pop and allow lead to escape into the air.
-
-
Use long handle scrapers or putty knives.
-
Wash-down equipment with water.
-
Control pressure and direction of spray to prevent splash-back.
-
Clean equipment at least once each shift.
-
Coat equipment with a peanut oil and water emulsion to aid adhesion of dry oxide and to facilitate cleanup.
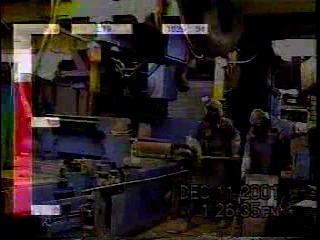
With video exposure monitoring (VEM), worker exposures to lead are monitored and recorded with a direct reading instrument. At the same time, workplace activities are recorded on a videotape. The left hand bar indicates changes in total dust concentrations over time.
As the employee shovels lead paste into the pasting machine hopper, the red bar indicates increasing employee exposure to lead dust.
Note: This example illustrates VEM can be used for determining sources of employee exposure. Other sources can be determined by using VEM sampling for a full work shift.
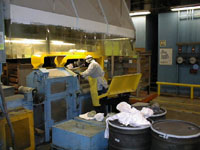
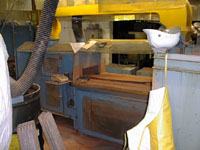
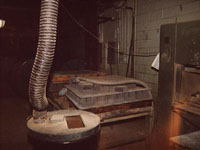
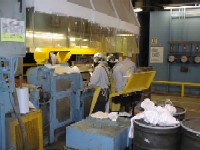
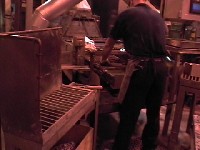
Potential Sources of Exposure
-
Lead oxide dust may become airborne:
-
From handling dry plates or moving plates in and out of the workstation.
-
From the buildup of dust on equipment, racks, and floor.
-
When workers brush plate lugs during parting.
-
When workers improperly handle or dispose of scrap plates and oxide from catch tray.
-
From inadequate capture velocity for tamping plates.
-
From upset conditions or while clearing jam-ups in equipment.
-
From dried oxide on contaminated gloves, clothing, shoes, and tools.
-
Possible Engineering Controls
-
Place scrap plates into a ventilated barrel or box and dispose of them properly (see Figure 8). When designing and building local exhaust ventilation keep flexible tubing to a minimum.
-
Place a slot or down draft ventilation at take off station.
-
Provide properly designed exhaust ventilation for the workstation.
-
Provide exhaust between oven and take-off workstation to prevent dust contamination generated from existing plates and conveyor chains.
-
Provide ventilated lug brush.
-
Use exhaust ventilated plate racks if it is shown by air sampling to be a contributor to exposure.
-
Break plates inside of hood or over ventilated tamping stand.
-
Evaluate the technical feasibility of robotics or automatic plate catching.
-
Use dust suppression techniques such as using dust suppression compounds, or vacuuming, where practical.
-
Provide a clear plastic plate between the operators breathing zone, and the conveyor and tamping stand. Enclose the process, if possible to minimize the ventilation requirements.
-
Install a piece of Plexiglas across the front of the hood to increase hood efficiency and prevent possible contaminated air from being induced into the operator's breathing zone while allowing the operator to see clearly.
-
Use a laminar flow (supplied-air) island at workstation.
-
Ventilate the testing station.
-
Note: Industrial batteries may require ventilation that is not always necessary for SLI batteries. This includes rack ventilation, a ventilated lug breaking station and a directed air system through the operator's breathing zone.
Possible Work Practice Controls
-
Wash shoes or leave shoe coverings in the pasting department to avoid transport of lead throughout the plant, or provide a shoe cleaning station.
-
Vacuum table, equipment, and racks to prevent accumulations of oxide.
-
Use dust suppression techniques such as keeping floors wet, using dust suppression compounds or vacuuming.
-
Using recycled water may increase lead-in-air levels if the water dries. Air bubbles in the water may pop and allow lead to escape into the air.
-
-
Provide adequate PPE, a change of clothes, and shower rooms (see OSHA Lead Requirements for PPE, Housekeeping, and Hygiene Facilities).
-
Brush toward the hood ventilation when brushing lugs, the edge of the panels, or the plates to remove adhering oxide.
-
Cover ventilated barrels or boxes with a plastic bag before moving it, or if a wax-coated cardboard box is used, close, and remove to storage.
-
Do not store plates on ventilated tamping stands.
-
Do not break plates on a metal plate or solid board.
-
Prohibit cooling fans or open doors and windows that cause cross drafts or thermals and destroy the effectiveness of local exhaust.
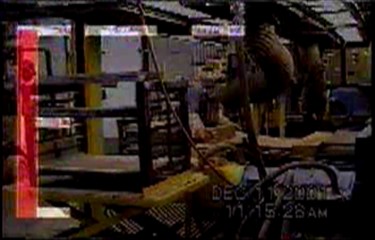
With video exposure monitoring (VEM), worker exposures to lead are monitored and recorded with a direct reading instrument. At the same time, workplace activities are recorded on a videotape. The left hand bar indicates changes in total dust concentrations over time.
As the employee removes plates from the pasting machine and brushes the edges of the plates, the red bar indicates increasing employee exposure to lead dust.
Note: This example illustrates how VEM can be used for determining sources of employee exposure. Other sources of employee lead exposure can be determined by using VEM sampling for a full work shift.