Lead: Battery Manufacturing eTool
Oxide and Grid Processing » Oxide Conveyance and Classification
Certain material transporting operations call for mechanical conveyance. Common conveyance methods used in battery manufacturing facilities include:
Classification separates the oxide particles by size, allowing only particles within the desired size range to the paste mixing operation.
Pneumatic conveying systems use air to transfer lead oxide from one point to another via pipes.
Potential Sources of Exposure
-
Leaking equipment.
-
Damaged bags in bin vent or baghouse.
Possible Engineering and Work Practice Controls
-
Repair leaks and replace bags immediately.
-
Use self-adhesive neoprene gaskets at all joints to provide a dust-tight seal.
Belt conveying systems use belts to transport lead oxide material.
Potential Source of Exposure
- Lead dust may be emitted from open conveyor systems:
-
At the receiving end.
-
At the discharge end.
-
At the underside of conveyor.
-
From spillage along the conveyor belt.
-
Possible Engineering and Work Practice Controls
-
Provide an enclosed conveying system, such as a screw or pneumatic conveyor, in place of an open conveyor belt where possible.
- Totally enclose and exhaust ventilate the conveyor from loading to transfer points.
-
Provide an exhaust ventilated enclosure at the conveyor loading and unloading points to minimize dust emissions.
-
Provide a trough belt and conveyor skirting to minimize spillage.
-
Provide a baffle to ensure the unloading of conveyor at transfer point.
-
Provide a belt scraper at the discharge end to dislodge dust particles that may adhere to the belt surface.
-
Provide access doors to conveyor and transfer point enclosures to facilitate maintenance, wash down, and other activities.
-
Use top-hinging doors for inspection to prevent spillage of leaded material.
-
Provide drains and sumps in conveyor trench to collect wash water and mud.
-
Provide hose bibs for manually washing the conveyor equipment.
- Wet down floors to suppress dust generation.
- Note: If wet lead oxide gets into a storage tank, it could lead to an oxide fire. Do not use water in areas with lead oxide silos or storage bins. Also keep water away from molten lead as explosions may result.
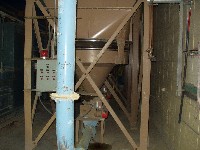
Tubular drag link conveying systems consist of disc-shaped flights attached to a chain inside a tubular housing. The chain is driven by a motor connected to a drive sprocket. Hoppers located above holes in the housing, feed material into the conveyor; holes cut in the bottom of the housing form the outlet.
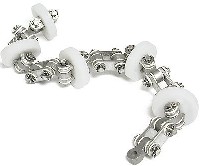
Potential Source of Exposure
- Lead dust may be emitted from open conveyor systems at:
-
The receiving end.
-
The discharge end.
-
Leaking flange connections.
-
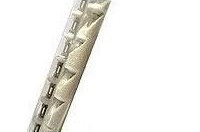
Possible Engineering and Work Practice Controls
-
Provide a preventive maintenance program to maintain system integrity.
-
Adjust the takeup (usually located near the drive sprocket) regularly to remove slack in the chain caused by stretching.
-
Inspect the chain and flights periodically for material buildup and wear.
-
Replace chain and flight components through the inspection opening to avoid dismantling the conveyor.
-
- Totally enclose and exhaust ventilate the conveyor from loading to transfer points.
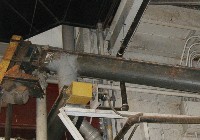
Potential Sources of Exposure
-
Lead dust may be emitted from leaking screw conveyors and at discharge points.
Possible Engineering and Work Practice Controls
-
Enclose screw conveyor systems that transport leaded materials.
-
Enclose and exhaust ventilate screw conveyor transfer points.
-
Maintain cover gaskets and repair leaks immediately.
-
Establish a preventive maintenance program for all lead handling processes and equipment.
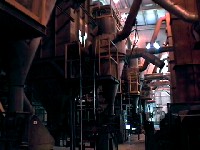
Air classification equipment (cones or cyclones) operate by applying opposing air flows and centrifugal forces to the oxide material. By balancing the two forces, the heavier particles spiral out and down where they are collected, and finer particles flow up to the top, where they may be passed to another cyclone with finer classification capability. Through this process, the desired particle size distribution is obtained.
Potential Sources of Exposure
-
Leaking equipment.
Possible Engineering and Work Practice Controls
-
Provide a preventive maintenance program to maintain system integrity.