Lead: Secondary Lead Smelter eTool
Engineering Controls » Process Controls
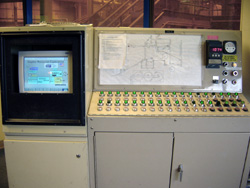
Process control systems, which include artificial intelligence based on preset algorithms, are sometimes used for controlling lead smelter operations. Those systems can minimize system upsets, which may result in lead emissions. They provide graphical user interfaces (GUI) that show real-time information, such as when a process fails. The process control system can also store data that can be retrieved and manipulated, and provide automated reporting.
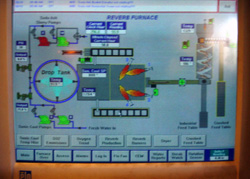
The graphical user interface (Fig. 1) shows the process in real-time with user-friendly graphics. These graphics may be as simple as a block diagram or as complex as digital photographs. The user interface not only displays pictures of the process but can also use process data to show real-time or historical trends of process points. Alarms are provided to notify the operator when intervention is required.
The programmable logic controller (PLC) is a local, stand-alone computer that is hard wired to process points such as limit switches and temperature probes. It runs logic based on information from input devices (e.g., switches, analog devices, or information received from the user interface) and compares it to a program in its memory. The PLC then makes decisions and provides commands to field devices (e.g., starting and stopping motors). If communication between the user interface and the PLC is lost, the PLC will run the process autonomously based on the last information received from the user interface and its programming.
The database is where all data collected from the user interface and PLCs is stored. This data can be used in a number of ways:
- It can be retrieved and trends analyzed to help identify how the process runs under certain conditions.
- It can be retrieved and put into report formats that can be shown on a computer screen, automatically printed out, or e-mailed to selected recipients.
In short, reports that were once collected and collated by hand can now be created automatically. This both saves time and decreases the likelihood for human error.
Waste water treatment chemical feed
Chemicals are fed into a wastewater stream, which helps keep the stream at a pH of 10. A pH probe sends its readings to the PLC that monitors the process. The PLC then takes this reading and applies it to its logic tables to determine whether to add more chemicals, and if adding, how much to add. This keeps the waste stream at a pH of 10 and limits chemical wasting due to over feeding.
Furnace exhaust
Instruments monitor furnace exhaust emissions and send their readings to the PLC. Decisions are then made by the PLC based on its logic tables:
- whether to add a chemical,
- open and close dampers,
- alarm the process control computer,
- or even send a message to the supervisor's pager.
This allows for a timely response by operations personnel to prevent unwanted releases from being vented to the atmosphere.