Lead: Secondary Lead Smelter eTool
Raw Materials Processing » Battery Breaking and Separating
The most common raw material at a secondary lead smelter is used automotive batteries. Batteries are typically unloaded by hand from trailers, conveyors, or from pallets. The batteries are then prepared for smelting by draining the acid and separating the plates, rubber, plastic containers, and sludge.
This section discusses the primary sources of lead exposure and controls that minimize lead exposure during the battery breaking and separating process.
Note: Exposure to corrosive acids can lead to serious burns and injuries. Required personal protective equipment must take acid exposure into account. Eye washes and emergency flushing facilities must also be provided.
The four most common processes for breaking automotive batteries are:
- High speed saw
- Slow speed saw
- Shear
- Whole battery crushing
The use of saws and shears involves cutting the tops off of the batteries, then dumping the contents of the battery. The whole battery crushing process involves crushing the entire battery in a crusher, shredder or hammermill, and separating the components by gravity separation.
Potential Sources of Exposure
-
The operation of battery saws, shears, crushers (hammermills), and shredders may release mists containing lead, which may dry and release lead dust if disturbed.
-
Shredded or crushed battery components may fall to the ground and release lead-containing materials.
- Vibrating equipment with lead- contaminated surfaces may cause reentrainment of lead dust.
Possible Engineering and Work Control Practices
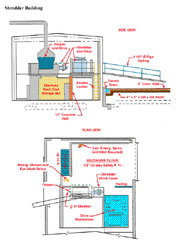
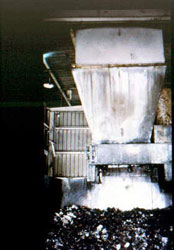
- Provide properly designed local exhaust hoods with local exhaust ventilation for saws, shears, shredders, and crushers (hammermills) to control lead emissions. (Fig. 1).
- Provide enclosure and local exhaust ventilation for shredded battery conveyor and transfer points.
- Provide a supplied air island or a temperature-controlled, positive-pressure, filtered supplied clean air room.
-
Automate the process with slow speed saws to cut off the tops of batteries. Slow speed saws emit less lead dust and acid mist than high speed saws.
-
Provide curtains or shields on battery- breaking equipment to contain mists and liquid droplets containing lead particulate.
-
Use wet suppression techniques to control exposure levels during cutting and sawing operations.
-
Provide adequate make-up air.
-
If it is determined through source identification sampling that lead dust is coming from mobile equipment or is coming from adjacent areas, reevaluate material handling patterns and work practices and isolate the area through barriers and provide ventilation as needed.
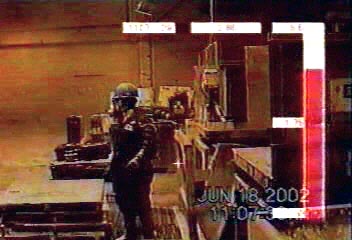
With video exposure monitoring (VEM), worker exposures to lead are monitored and recorded with a direct reading instrument. At the same time, workplace activities are recorded on a videotape. The right hand bar indicates changes in total dust concentrations over time.
As the employee charges battery feed material to a battery crusher, the increasing red bar indicates that employee exposure may be from settled dust becoming airborne after dropping the pallet; or acid mist and particulate may be escaping the ventilated battery crusher. Additional area samples may be collected at the inlet to the crusher and adjacent to the pallet to determine which is the predominate source.
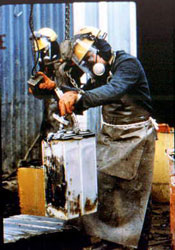
Industrial batteries, used to power mobile electric equipment or for other industrial uses, are periodically purchased for raw material by most secondary smelters. Many of these batteries have steel cases which require removal by cutting the case open with a cutting torch, a hand-held gas powered saw, or other equipment that can separate the case from its contents (Fig. 2).
Potential Sources of Exposure
-
For manual cutting or breaking operations, acid mist containing lead may be emitted which may dry and release lead dust if disturbed.
-
Automated operations using crushers may release lead containing mist that may dry and release lead dust if disturbed.
-
Vibrating equipment with lead contaminated surfaces may cause reentrainment of lead dust.
-
Cutting industrial battery cases open with a torch may result in exposures to airborne lead.
Possible Engineering and Work Control Practices
- Provide side draft ventilation and a turntable at the cutting station to control any mist being generated.
- Provide properly designed local exhaust hoods with local exhaust ventilation for crushers to control lead emissions.
- Provide enclosure and local exhaust ventilation for shredded battery conveyor and transfer points.
- Provide a supplied air island or a temperature-controlled, positive-pressure, filtered supplied clean air room.
-
Provide an automatic or semi-automatic means for opening battery cases.
-
Provide curtains or shields on battery breaking equipment to contain mist and liquid droplets containing lead particulate.
-
Provide adequate make-up air.
-
Use wet suppression techniques to prevent lead from drying on equipment surfaces.
-
If it is determined through source identification sampling that lead dust is coming from mobile equipment or is coming from adjacent areas, reevaluate material handling patterns and work practices and isolate the area through barriers and provide ventilation as needed.
After the automotive batteries have been "broken", the lead-bearing material must be separated from the case material. The three most widely used techniques for accomplishing this task are:
The "manual" technique is not used by many secondary lead smelters. After the battery passes through the saw or shear, an employee manually dumps the "groups" or lead-bearing material into a pile and places the case and top of the battery into another pile or conveyance system.
Potential Sources of Exposure
-
Splashes of lead-laden liquid may dry on equipment and adjacent surfaces and become airborne through reentrainment or physical disturbance.
-
Lead-laden acid mist may be created from the physical dumping of batteries.
-
Acid mist may be generated by the saw or shear, which is located in close proximity to the dumping station.
Potential Engineering and Work Practice Controls
- Provide enclosure and local exhaust ventilation for conveyor loading and discharge points to maintain adequate capture velocity.
- Provide enclosure and local exhaust ventilation for conveyor.
- Provide supplied air island or temperature-controlled, positive-pressure, filtered supplied air control room.
- Vacuum surfaces using HEPA filtered portable or central vacuum systems.
-
Provide barriers and shields to stop splashes of mists and liquid droplets containing lead particulate.
-
Wash down building walls and fixed equipment with water.
-
Provide additional dilution or make-up air ventilation.
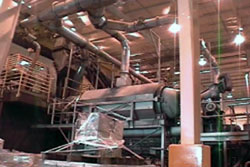
A "tumbler" is a device in which batteries are placed after the tops have been sawed or sheared off to separate the battery plates from the cases. Ribs inside the tumbler dump the groups as it slowly rotates. Groups fall through the slots in the tumbler while the cases are conveyed to the far end and are collected as they exit. Plastic and rubber battery cases and tops are further processed after being separated from the lead-bearing material (Fig. 3).
Potential Sources of Exposure
- Splashes of lead-laden liquid may dry on equipment and adjacent surfaces and become airborne through reentrainment or physical disturbance.
Possible Engineering and Work Practice Controls
- Provide enclosure and local exhaust ventilation for tumbler and loading and discharge points (Fig. 3).
- Provide enclosure and local exhaust ventilation for discharge points of adjacent crushers which may contribute to employee exposure.
- Provide supplied air island or temperature-controlled, positive-pressure, filtered supplied air control room.
- Vacuum surfaces using HEPA filtered portable or central vacuum systems.
-
Provide additional dilution or make-up air ventilation.
-
Wash down building walls and fixed equipment with water.
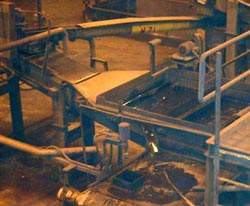
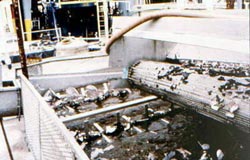
The "sink/float process" is used by the majority of secondary smelters (Fig. 4). The "sink/float process" is typically combined with the hammermill or crushing process for battery breaking. Battery pieces, both lead-bearing and cases, are placed in a series of tanks filled with water. Lead-bearing material sinks to the bottom of the tanks and is removed by screw conveyor or drag chain while the case material floats and is skimmed off the tank's surface (Fig. 5). This operation should not lead to significant employee exposure.
If employees are exposed above the OSHA PEL, additional air sampling should be performed to determine sources of exposure.
Potential Source of Exposure
-
Splashes of lead-laden liquid may dry on equipment and adjacent surfaces and become airborne through reentrainment or physical disturbance.
Potential Engineering and Work Practice Control
-
Wash down building walls and fixed equipment with water.