Lead: Secondary Lead Smelter eTool
Refining and Casting » Casting
Molten, refined, or alloyed lead is pumped via heated pipes from kettles to a casting reservoir, or casting wheel, which directs a measured amount of lead into steel or cast iron molds. Hand operations include drossing and stacking cooled castings. Castings typically consist of "pigs" (up to 80 pounds) and blocks (up to 2000 pounds) (Fig. 1). Employees may be exposed to lead fumes emitted from the molten lead during the casting and drossing operations.
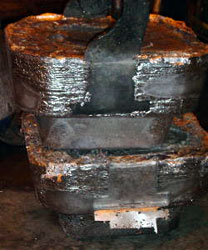
Potential Sources of Exposure
-
Lead fumes may be emitted during heating and cleaning of lead transfer pipes and pumps.
-
Lead fumes may be emitted during the heating of lead reservoir and casting equipment.
-
Lead fumes may be emitted during the pouring and cooling of lead castings.
-
Lead fumes may be emitted during the drossing of lead oxides from the reservoir and casting surfaces.
-
Spillage and emissions of lead fumes and dust may occur during the handling, transport, and storage of drosses.
-
Lead fumes and dust may be emitted during mold casting line cleaning, heating, and maintenance.
-
Lead dust may be generated during the application of mold release agents.
-
Lead dust may be reentrained by mobile traffic moving through the area.
Possible Engineering and Work Practice Controls
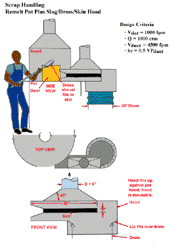
- Provide local exhaust ventilation for the castings and molds while pouring molten lead.
- Provide a supplied air island at the operator work station.
- Use automatic drossing machines when feasible.
- Dross into an exhaust ventilated container.
-
Enclose and exhaust ventilate all launders.
-
Keep molten lead temperature below 1000°F to minimize lead fumes and particulate emissions during lead transfer and drossing of castings and molds.
-
Eliminate or minimize the use of a torch for equipment cleanup and spilled lead or dross.
- If a torch must be used, provide portable local exhaust ventilation or a ventilated torch.
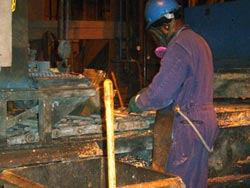
Potential Sources of Exposure
-
Lead fumes may be emitted during heating and cleaning of lead transfer pipes and pumps.
-
Lead fumes may be emitted while heating the lead reservoir and casting equipment.
-
Emissions may occur during the pouring and cooling of lead castings.
-
Lead fumes and dust may be emitted during the drossing of lead oxides from the reservoir and casting surfaces (Fig. 2).
-
Spillage and emissions of lead fumes and dust may occur during the handling, transportation, and storage of drosses.
-
Lead fumes and dust may be emitted during mold and casting line cleaning, heating, and maintenance.
-
Lead dust may be generated during the application of mold-release agents.
-
Lead dust may be reentrained by mobile traffic moving through the area.
Possible Engineering Controls
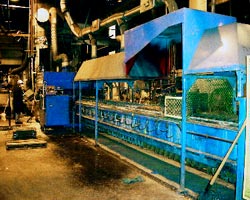
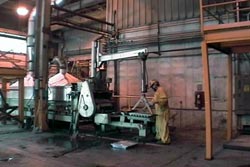
- Provide local exhaust ventilation for the castings and molds while pouring molten lead (Figs. 3 & 4).
- Provide a supplied air island at the operator work station.
- Use automatic drossing machines when feasible.
- Dross into an exhaust ventilated container.
- Enclose and exhaust ventilate all launders.
-
Keep molten lead temperature below 1000°F to decrease lead fumes and particulate emissions during lead transfer and drossing of lead oxides from the reservoir and casting surfaces.
-
Eliminate or minimize the use of a torch for cleanup of spilled lead metal or dross.
- If a torch must be used, provide portable local exhaust ventilation or a ventilated torch.