Lead: Secondary Lead Smelter eTool
Raw Materials Processing » Raw Materials Receiving and Storage
Used batteries are usually received in palletized containers and can either be stored or transferred to conveyors for shredding. These are normally low-exposure operations.
Lead-bearing scrap from other operations (such as battery manufacturing plant scrap, dross from lead refining, and scrap metallic lead) should be covered during transfer and stored in an enclosed, ventilated area until the charge preparation phase begins.
Workers may be exposed to lead dust during receiving and storage of lead-bearing materials.
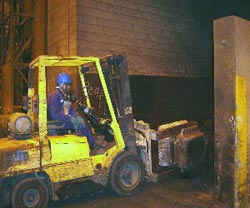
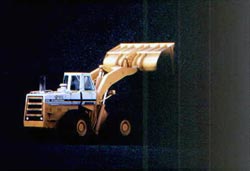
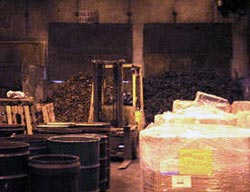
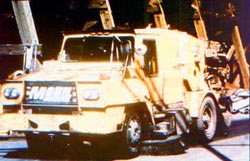
Potential Sources of Exposure
-
Lead dust from scrap materials can become airborne during handling and transportation of materials (Fig. 1).
-
Emissions may occur during dumping and transporting materials to storage areas.
-
Settled lead dust on surfaces and equipment may become airborne due to vehicle traffic and cross-drafts.
Possible Engineering and Work Practice Controls
- Provide vehicles with enclosed cabs that have positive-pressure, HEPA filtered air. (Fig. 2).
- Install full enclosure of bins containing lead-bearing materials.
-
Maintain raw material storage and handling areas under a negative-pressure enclosure to prevent contamination of adjacent work areas. (Fig. 3).
-
Minimize the height of free fall of materials dumped into storage bins.
-
Maintain positive-pressure, filtered air systems on mobile equipment to ensure effective operation. Check and change air filters regularly as part of an effective scheduled preventative maintenance program.
-
Remain inside the vehicle and keep doors and windows shut during operation.
-
Vacuum the inside of mobile equipment frequently.
-
Reduce vehicle speeds to minimize the stirring up of settled dust.
-
Wash vehicles to prevent spread of contamination when exiting storage areas.
-
Pave all roadways to facilitate housekeeping. (Fig. 4).
-
Keep all roadways wet to minimize dust generation.
-
Wet down raw materials storage to suppress dust generation.
-
Install roll-up doors on bin charging decks to permit access for trucks and container dumping.
-
If it is determined through source identification sampling that lead dust is coming from mobile equipment or is coming from adjacent areas, reevaluate material handling patterns and work practices and isolate the area through barriers and provide ventilation as needed.
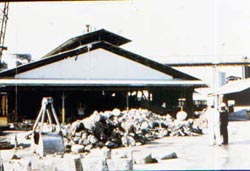
Secondary lead smelters purchase a variety of materials as feed materials for the refining process. These materials include: battery manufacturing plant scrap, lead dross, metallic lead such as linotype and cable shielding, and tetra ethyl lead (TEL) residues (Fig. 5). These materials may be charged directly into smelting furnaces or mixed with other charge materials.
Lead-bearing scrap does not normally require processing prior to being charged to the furnace. Hazards involved are the same as receiving and storage and transport of raw materials.