OSHA Field Safety and Health Management System (SHMS) Manual
CHAPTER 27. EXPOSURE MONITORING
-
Purpose
This chapter establishes the OSHA Field Safety and Health Management System (SHMS) Exposure Monitoring Program. The policies and procedures in this Program are intended to set broad expectations for "self-monitoring" to prevent employee illness, injury or death from exposure to chemical and physical health hazards. OSHA expects Regions, DTSEM, and DTE to develop specific procedures that align with this Program as needed.
This Program is also intended to identify if OSHA employee exposures indicate a need for short or long term medical intervention to prevent or respond to hazardous exposures. These procedures describe when and how to collect exposure data from select participating employees. OSHA may also use this self-monitoring data to make broad determinations about all covered employees' exposure history.
-
Scope
This chapter applies to all OSHA employees covered by the OSHA Field Safety and Health Manual, (i.e., Covered Employees).
-
References
-
29 Code of Federal Regulations Section 1910.1020, Access to Employee Exposure and Medical Records
-
OSHA Instruction TED 01-00-015, OSHA Technical Manual, January 20, 1999
-
OSHA Chemical Sampling Information on-line file
-
OSHA Technical Manual, Section II, Chapter 1, Personal Sampling for Air Contaminants, Appendix M
-
OSHA Field Safety and Health Manual, Chapter 2, Safety 2, Safety and Health Management System
-
OSHA Field Safety and Health Manual, Chapter 12, Hazard Communication
-
OSHA Field Safety and Health Manual, Chapter 16, Hearing Conservation Program
-
OSHA Field Safety and Health Manual, Chapter 25, Medical Management
-
Agency Loan Equipment Program (ALEP) catalog
-
NIOSH Pocket Guide to Chemical Hazards
-
ACGIH: Threshold Limit Values (TLVs®) and Biological Exposure Indices (BEIs®).
-
-
Responsibilities
-
Regional Administrators/Directorate Directors (RAs/Directors) are responsible for each employee's work-related safety and health in the Region/Directorate and will:
-
Implement this Exposure Monitoring program in their Region/Directorate and develop specific procedures if necessary.
-
Support self-monitoring when setting performance expectations and developing policies and procedures.
-
Provide managers with the authority and resources necessary to carry out their responsibilities in the OSHA Exposure Monitoring Program.
-
Develop formal procedures to ensure employees are trained and that exposure data is annually reviewed and disseminated to affected employees and the SHMS Executive Steering Committee (ESC).
-
Request assistance from the SLTC's Health Response Team for investigations and inspections with the potential for exposure to chemical or physical hazards when the Region/Directorate does not have the resources to safely assess or conduct work activities.
-
-
Safety and Health Committees (SHCs) and equivalent for SLTC, CTC, and DTE are responsible for tracking and evaluating field personnel exposures and will:
-
Evaluate over-exposure incidents to determine if appropriate protections were used and what follow-up may be needed. This evaluation is not for disciplinary purposes.
-
Consult DTSEM's Office of Occupational Medicine and Nursing (OOMN) when medical expertise is needed.
-
Review at least annually Region/SLTC/CTC/DTE exposure data for trends and lessons learned.
-
Conduct an annual program review and make appropriate recommendations.
-
-
OOMN will provide consultation for OSHA field personnel in accordance with Chapter 25, Medical Management.
-
Area Directors (AD) and equivalent for SLTC, CTC, and DTE are responsible for implementing this Program in each Area Office/SLTC/CTC/DTE and will:
-
Ensure exposure-monitoring data is collected and recorded by field staff and reviewed by supervisors.
-
Ensure sampling media and direct reading equipment is readily available.
-
Train employees on hazardous chemicals, as directed by the Regional Hazard Communication Program and Chapter 12, Hazard Communication.
-
Ensure training is provided for all sampling equipment used.
-
Ensure the Regional SHC/equivalent for SLTC/CTC/DTE is notified of all overexposures.
-
-
Employees covered by the OSHA Field Safety and Health Manual (Covered Employees) will participate in the OSHA Exposure Monitoring Program and will:
-
Exercise professional judgment to determine where potential exposures exist for themselves as well as for employees working on site. OSHA employees may decide to self-monitor even if not required by this Program See Section V.A.1 for required monitoring.
-
Contact their supervisor for guidance if they are unsure about performing monitoring prior to spending time in an area.
-
Perform necessary personal monitoring, wipe sampling, or bulk sampling of occupational health exposures.
-
Complete sampling documentation in the OSHA Information System (OIS), see Appendix B, OIS Data Entry.
-
Notify the Assistant Area Director or other appropriate supervisor when self-sampling exposure levels exceed a published Occupational Exposure Limit (OEL) or when experiencing signs and symptoms of exposure.
-
Review the establishment's Safety Data Sheets (SDSs) and/or chemical inventory in accordance with other provisions in the Regional/SLTC/CTC/DTE Safety and Health Program (e.g. Hazard Communication Program) during the opening conference to evaluate the potential exposures that may be encountered during the inspection.
-
-
-
Exposure Data Collection Procedures
Covered OSHA employees will monitor their exposures to hazardous chemicals, noise, radiation, and other physical hazards. Self-monitoring may include full shift monitoring, screen sampling, passive sampling, and direct reading sampling. Covered employees will use professional judgment to determine the appropriate sampling method. When conducting joint safety and health inspections, follow generally accepted industrial hygiene practices.
Sample results are compared to the most protective Occupational Exposure Limit (OEL) among the following: OSHA permissible exposure limit (PEL), the American Conference of Governmental Industrial Hygienists (ACGIH) Threshold Limit Value (TLV), National Institute for Occupational Safety and Health (NIOSH) Recommended Exposure Limit (REL), or the specific manufacturer's OEL.
Based on exposure monitoring data reviews, OOMN may request additional exposure monitoring, in coordination with OSHA's Field SHMS National Labor-Management Steering Committee, to support a special chemical, noise, or other physical agent exposure study, using appropriate measures to prevent exposure.
-
Self-Monitoring for Hazardous Chemicals
Covered Employees will perform self-monitoring for hazardous chemical exposure where appropriate, based on both professional judgment and the following conditions:
-
Self-monitoring is required when:
-
A company's employees are potentially exposed to chemicals at hazardous levels that justify taking air samples for measurement. Covered Employees at the location (e.g. in a joint safety and health inspection effort) may self-monitor, even if not taking samples from the company's employees.
-
Covered Employees have potential for exposure, and
-
At least one of the following is true:
-
The chemical is covered by an expanded health standard.
-
The chemical is a carcinogen.
-
The chemical has poor warning properties.
-
The chemical has a high odor threshold (e.g. difficult to detect by smell).
-
The chemical has an unusually low OEL, for example less than 1 ppm or the mg-m3 equivalent (see the OSHA Technical Manual, Section II, Chapter 1, Personal Sampling for Air Contaminants, Appendix M, to convert between ppm and mg-m3).
-
The chemical has a skin designation from an above OEL.
-
-
Note: The above decision policy is also available in Appendix C as a flowchart
-
Self-monitoring is not required under the previous conditions IF one or more of the following conditions are met:
-
Covered Employees are not in the immediate area where work is being conducted.
-
The chemical has a low volatility or is not part of the process where it is easily aerosolized.
-
Note: If it is determined that self-monitoring is not required due to the above, the Covered Employee needs to document the specific reason in a location designated by the RA/Director (e.g., case file).
-
Covered Employees may self-monitor any time they decide it is warranted.
-
-
Self-Monitoring for Noise
In most situations, self-monitoring for noise is not required. Real time self-monitoring, e.g. a sound level meter, is required when noise levels may exceed expected levels; it is used to determine when hearing protection is not adequate and the situation requires a change in location or proactive hearing protection. Noise exposure data will provide the Covered Employee with real time information to determine the need for additional hearing protection or distance from the source before causing hearing loss. Covered Employees may self-monitor for noise exposure any time they believe it is necessary.
Covered Employees will enter all noise exposure monitoring data into OIS.
-
The OSHA Hearing Conservation Program requires the use of personal protective equipment (PPE) and Audiometric examinations. Audiometric examinations are conducted during routine medical evaluations. See OSHA SHMS Manual Chapter 16, Hearing Conservation Program, for additional information.
-
Self-Monitoring for Other Physical Hazards
Covered employees will perform monitoring for physical agents (e.g. radiation, thermal stress). Covered employees will enter monitoring data results into OIS.
-
When Covered Employees encounter a situation where radiation or thermal stress is present, they will contact their supervisor to determine the need and appropriate method for self-monitoring.
-
Covered Employees may arrange for self-monitoring any time they believe it is necessary.
-
-
-
Exposure Records
-
Exposure Records
An "employee exposure record" is defined in 29 CFR 1910.1020. For purposes of this Program, the information contained in the OIS self-sampling records constitutes an employee exposure record. The employee exposure record shall be recorded as outlined in Appendix B.
-
Access to Exposure Records
Covered Employees will have access to their own employee exposure records without the need for submitting a formal, written request for the records.
-
Exposure Records Availability
-
Under the Freedom of Information Act (FOIA), 5 U.S.C. §552, exposure monitoring records, regardless of where they are stored or maintained, might be released in response to requests from various parties. In most cases, the Covered Employee's name and Compliance Safety and Health Officer (CSHO) ID number will be redacted, based on Exemption 6 (information about specific individuals in "personnel and medical files and similar files" when the disclosure of such information would constitute a clearly unwarranted invasion of personal privacy) and/or Exemption 7(c) (records or information compiled for law enforcement purposes to the extent that such information could reasonably be expected to constitute an unwarranted invasion of personal privacy) of the Freedom of Information Act.
-
The Privacy Act of 1974, 5 U.S.C. §552a, is not generally applicable to establishment case files. The Privacy Act permits an individual to seek access to only his/her own records and only if that record is maintained by the Agency within a system of records and retrieved by the individual requester's name or personal identifiers.
-
If an inspection case is contested, exposure monitoring information might be released during the discovery process. Exposure monitoring information would be made accessible to the parties involved in the litigation (the establishment inspected and, if they have elected party status, the union representing the employees at the establishment), their attorneys and the judge. Under discovery, it is unlikely that the covered employee's name or CSHO ID number could be redacted.
-
-
-
Exposure Follow-Up
-
During a site visit, if covered employees recognize that they may be overexposed, they will take appropriate steps to remove themselves from risk and minimize further exposure. The primary action following such an exposure is to implement controls to reduce or prevent additional exposure.
-
Covered Employees will notify their manager, who will notify the applicable OSHA Field SHMS SHC whenever there is a known or suspected overexposure, see Chapter 2, Safety and Health Management System, Section IV, Incident Reporting/Investigation Procedures.
-
The applicable SHC will review any known or suspected exposure incident and determine if the case should be referred to the Director of OOMN, who will determine the need for further medical evaluation. Medical surveillance may be provided to employees exposed at levels greater than established occupational exposure limits or experiencing signs and symptoms of exposure as determined by OOMN.
-
The applicable SHC may make recommendations regarding current and future use of appropriate personal protective equipment, administrative controls, and work practices to the appropriate OSHA management.
-
-
Training
All Covered Employees must receive training annually on:
-
The requirements contained in this Program.
-
Exposure data collection methods, data collection equipment.
-
Trends and lessons learned from the applicable SHC annual review.
-
The specific substances referenced in Appendix A, Chemical Exposure Hazards to ensure familiarity and provide references on where to obtain additional information.
-
How to enter self-monitoring data into OIS.
Additional training is necessary if conditions such as data collection methods change. Retraining will occur when the supervisor determines that a Covered Employee does not possess adequate understanding or skill to self-monitor and/or prevent exposure to hazardous chemicals.
-
-
Data Tracking and Retention
Covered Employee exposure records are established and entered into OIS. Appendix B, Creating a CSHO Sampling Record - OIS Instructions, is detailed and includes screen shots for correctly completing the form and accessing records in OIS. A paper file need not be created because the electronic records are maintained in OIS for the required 30 years. See 29 CFR 1910.1020(d)(i)(ii). CSHOs may create paper copies for their own records.
APPENDIX A
CHEMICAL EXPOSURE HAZARDS
-
Chemicals covered by an expanded OSHA health standard
Carcinogens: 4-Nitrobiphenyl; alpha-Naphthylamine; Methyl chloromethyl ether; 3,3'- Dichlorobenzidine and its salts; bis- Chloromethyl ether; beta-Naphthylamine; Benzidine; 4-Aminodiphenyl; Ethyleneimine; beta-Propiolactone; 2-Acetylaminofluorene; 4- Dimethylaminoazobenzene; and, N-Nitrosodimethylamine.
Asbestos
Vinyl chloride
Inorganic arsenic
Lead
Chromium (VI)
Cadmium
Benzene
Coke Oven emissionsCotton dust
1,2-dibromo-3-chloropane
Acrylonitrile
Ethylene oxide
Formaldehyde
Methylenedianiline
1,3-Butadiene
Methylene chloride -
Chemicals with poor warning properties, high odor thresholds, very low OELs, or special interest chemicals (this list is not all inclusive)
Chemicals covered by NEPs, LEPs, REPs or any other specific targeting program
Silica
Beryllium
Carbon monoxide
Hydrogen sulfide
Pharmaceutical dusts
Isocyanates
Acetylene
N-bromopropaneCarbon tetrachloride
Chloroform
Dichlorobenzene
Ethylene oxide
Formamide
Heptane
Diacetyl
Styrene
APPENDIX B
CREATING A CSHO SAMPLING RECORD—OIS INSTRUCTIONS
Creating a CSHO Self-Sampling Activity
Most CSHO sampling records are associated with an inspection. Enter the associated inspection first, and then enter the self-sampling activity.
To create a self-sampling activity, click on Self-Sampling in the Create New drop down in OIS.
If the CSHO is assigned to more than one RID, they will be prompted to select the RID to which the self-sampling will be attached (the default is the CSHO's primary RID). Otherwise, they will be brought directly into the Self-Sampling activity record. All office information including the RID, Office Name, and office Address are pre-populated into the self-sampling activity based on the RID selection.
The CSHO will then enter the enforcement inspection to which the self-sampling activity will be attached. The system will then pre-fill the opening conference date of the related inspection as well as the associated establishment into the self-sampling activity. Once these field entries are completed, click "Save". This will create the Self-Sampling activity number in OIS.
*NOTE: If the self- sampling is NOT related to an inspection (e.g., sampling at the Area, Regional or National Office), the CSHO can simply enter the date the sampling was conducted as the "Opening Conference Date" and the location of the sampling as the "Self Sampling Activity Name".
To proceed with exposure record and sample sheet entry, click on the ellipsis in the upper right corner of the screen, and then click "Go to Case Summary".
This will return the CSHO to the Case Summary Screen, at which time they will click on + Health Sampling to proceed with Exposure Record and Sampling Sheet Data entry.
The exposure record will automatically be prefilled with the Job Title of CSHO, CSHO ID, CSHO's name, and RID information. The CSHO may choose to enter some basic information about the process as well. Once the CSHO clicks "Save", the Exposure Record will have been created, and the CSHO may proceed with entry of sample sheets as they normally would for any other sampling activity.
APPENDIX C
SITE VISIT CHEMICAL SELF-MONITORING DECISION FLOW CHART
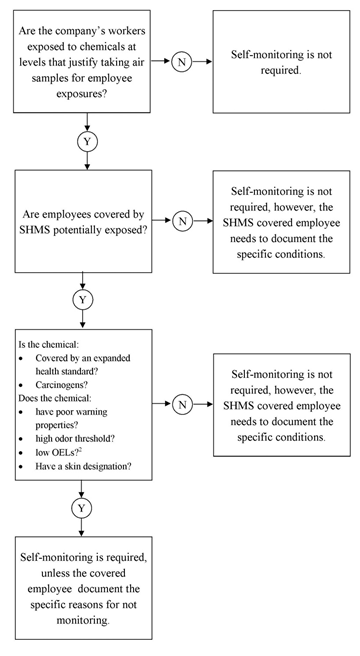
1 See section V.A.2.
2 For chemicals with poor warnings properties, high odor, or low OELs, see Appendix A
APPENDIX D
PASSIVE SAMPLERS
Below is a partial list of chemicals that may be sampled using passive samplers.
OSHA Validated Methods
2-Butanone (methyl ethyl ketone, MEK)
Benzene
Ethyl benzene
Hexone (methyl isobutyl ketone [MIBK])
Hydrogen cyanide
Isobutyl acetate
Methyl ethyl ketone (2-butanone)
Methyl isobtutyl ketone (MIBK), (hexone)
m-Xylene
n-Butyl acetate
Nitrous oxide
o-Xylene
Perchloroethylene (tetrachloroethylene)
p-Xylene
Styrene
t-Butyl acetate
Tetrachloroethylene (perchloreotheylene)
Toluene
Trichloroethylene
Manufacturer Validated Methods
1,2-Dichloroethene (1,2-dichloroethylene)
1-Bromopropane (propyl bromide)
1-Methylcyclohexanol
Acetone
Acrylonitrile
Benzene
Dichloromethane (methylene chloride)
Ethyl methacrylate
Ethylene oxide
Halothane
Isoflurane
Methyl acrylate
Methyl t-butyl ether (MTBE)
Methylene chloride (dichloromethane)
n-Butyl acetate
n-Pentane
Perchloroethylene (tetrachloroethylene)
Propyl bromide (1-bromopropane)
Styrene
t-Butyl methyl ether (MTBE)
Tetrachloroethylene (perchloroethylene)
Trichloroethylene
Vinyl acetate