Poultry Processing Industry eTool
Poultry Processing Industry » Additional Material
Bent Wrist
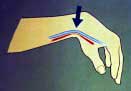
When this posture is used in conjunction with repeated finger activation, the tendons are repeatedly pulled across the bones and ligaments in the wrist. This action is similar to pulling a rope over a ledge or a pulley. The tendon and sheath can become inflamed and frayed and swelling may occur. Swelling may compress the median nerve as it passes through the wrist, causing pain and numbness in the hand and fingers.
Decrease Weight of Loads Lifted
Make the box or tote lighter. Cutting the size of the box in half will significantly reduce weight that must be lifted. Other manufacturers have reduced the size of their packaging and thus the weight that must be lifted.
Domino Sugar has reduced the weight of its shipping boxes to no more than 40 pounds.
Domino Cuts Sugar Packages
Domino Sugar reduced its bundled packages of sugar from 60 pounds to 40 pounds, below OSHA's suggested limit of 50 pounds. This change will make the bundles easier to handle and reduce the total weight of each by 33 percent. All three of its manufacturing locations have adjusted their packaging equipment to accommodate the weight modification. The first shipments of 40-pound bundles began in June.
Diverter Bars
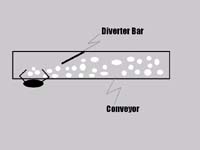
Diverter bars push materials on a conveyor belt closer to an employee. This reduces the amount of reaching and reduces stress to the shoulder, upper back, and neck.
Finger Contact
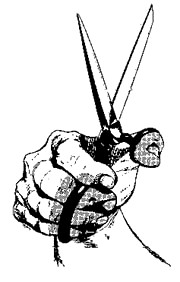
Using conventional scissors can create a contact trauma to the sides of the fingers. This can damage nerves and lead to tingling in the finger tips and thumb.
Fully Adjustable Palletizing Workstations
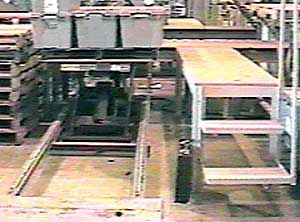
Developing a fully adjustable workstation will allow employees to always lift at about waist height. This type of station can be lowered to below floor height for loading the higher tiers of a pallet, and can be raised to waist height for loading the bottom tiers.
Hand Tools that Require Forceful Finger Exertion
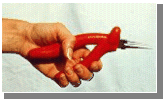
Tools that require using repetitive forceful finger exertions can stretch the tendons and if the wrist is bent, can create contact trauma to the tendons and their sheath as they are pulled across the rigid entities of the wrist. Some tool designs to minimize the impact to the hand by:
- Bending the tool handle so the wrist can remain as straight as possible.
- Producing tool handles long enough to run the full length of the hand. This keeps the handle from pressing into the palm and allows all the fingers to provide force when closing the jaw.
- Padding the handles so there are not sharp edges that will press against the hand and making it out of slip-resistant material.
- Making tools sized to accommodate both large and small hands. For most people the finger and thumb should touch or slightly overlap (handle span between 2 and 3 inches).
Height-Adjustable Stands
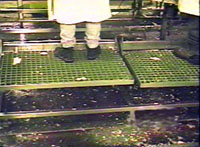
Work stations should generally be designed for the tallest employees who are likely to use them, to reduce the need for these employees to bend at the waist while performing their task. Using height adjustable stands allows employees of shorter body sizes to work at the same workstation without using awkward postures such as reaching above shoulder height. Stands should be easily adjustable at the beginning of shift without special tools or training.
Knives
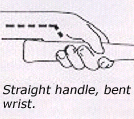
Working on a flat work surface with a straight handled knife can force employees to bend (deviate) the wrist. A hazardous situation can develop when this posture is combined with repeated or prolonged exertion of finger force. Employees often use a significant amount of finger force to control the knife during the cutting process, especially if:
- They wear gloves.
- Their hands are cold and they can not feel the knife in their hands.
- The knife has a slick handle.
- The knife is not sharp.
- Meat is frozen.

The ideal posture when performing hand intensive tasks is to keep the wrist in a straight (neutral) position. Using bent handled knives allows the wrist to remain neutral during the cutting task. Providing knives with different sized handles can also reduce the amount of finger force that is used because a handle that is too big or too small for the employee's hand requires more finger force.
If it is not practical to bend the knife handle, tilting the work surface towards the employee will reduce the bend in the wrist. Glove and knife handle materials that are rough or slightly sticky will improve the grip an employee can place on a knife and reduce the amount of force the fingers must exert.
A loop type handle can sometimes be used which allows the employee to release the handle periodically so the fingers can rest. Because the hand is placed inside the loop of the knife it stays in place without constant exertion or finger force. Encourage employees to put the knife down periodically and stretch, shake, and flex the fingers. Knife sharpening programs are important so that knives are always as sharp as possible. A sharp knife requires less finger force to perform a given task.
Load Positioners
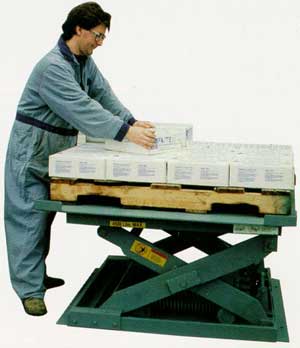
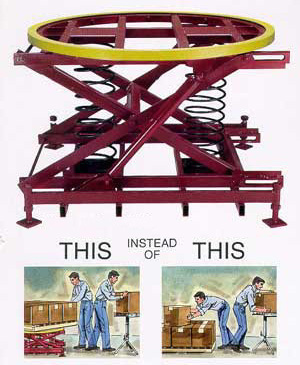
Narrow Conveyor
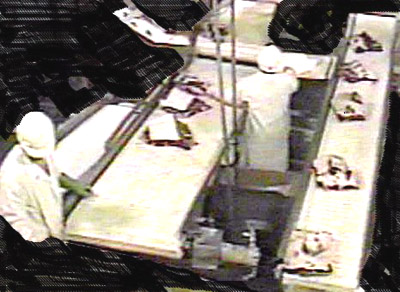
Conveyors should only be as wide as is necessary to accommodate the product. Using overly wide conveyors forces employees to reach out and away from their bodies, which stresses the shoulder, upper back, and neck.
NIOSH Lifting Recommendations
NIOSH has developed a formula for assessing the hazard of a lifting situation. The formula looks at the following elements involved in the lift:
- distance the load is held in front of the body,
- height the load is lifted from and to,
- height of the load,
- frequency of lifting,
- the hand load coupling, and
- the amount of torso twisting that is involved with the load lifting motion.
Using these parameters NIOSH, has established that, for occasional lifting where the load is held close to the body, with no twisting, and at about waist height and where the load has good hand holds, the typical industrial worker could lift about 51 pounds without a significant increase in risk of injury. As these factors deviate from the ideal, the amount of weight that can safely be lifted by an employee is decreased.
A typical box of packed whole chickens or chicken parts can weigh between 40 and 80 pounds. It is obvious that even under ideal circumstances most employees are at an increased risk of back injury when lifting a load of 80 pounds, since this is about 1.6 times the NIOSH recommended limit of 51 pounds. In real life, employees must handle loads that are often held out and away from the body, lowered or lifted to low or elevated locations, involve twisting the torso to access the loading areas, are highly repetitious, and that are in boxes that may not have good handles. These real life situations reduce the amount that can be safely lifted.
The NIOSH Lifting Recommendations can factor all of these reductions together and determine a weight that most people should be able to lift when performing a job the way it is normally performed. A typical recommended weight limit for a task where employees must repeatedly lift loads and place them to low locations, where torso twisting may be required, is about 8 to 12 pounds.
The amounts lifted in these typical boxes of chicken are 4 to 8 times this recommended value, and research indicates that many in the work force will be injured performing these types of lifting tasks.
This Applications Manual for the Revised NIOSH Lifting Equation will help determine safe load weights.
Position
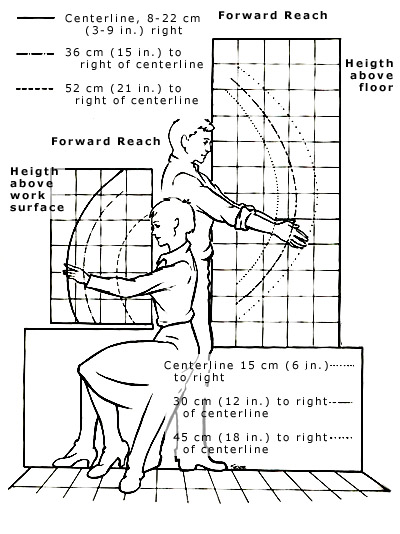
- Employees may have to reach behind their bodies or to distant locations to access product for placement into machines or to cut using manual saws.
- Employees may need to reach a significant distance in front of their bodies to place chicken sections onto machinery that will process the parts.
- Employees may need to work with their arms in elevated postures because the saw is placed too high in relation to the employee.
Repeatedly reaching can increase the risk of chronic injuries such as tendinitis and bursitis as the tendons are repeatedly pulled across the bony entities in the shoulder.
Lifting a load in the hand or holding the arms in an elevated posture for a prolonged period of time can fatigue the muscles of the shoulder and upper back, increasing the risk of developing acute injuries such as strains, sprains, and tears.
Highly repetitive reaches or supporting loads in the hand should be done with the elbows in close to the body. Occasional reaches or supporting light loads for a very short period may be done at full arm extension.
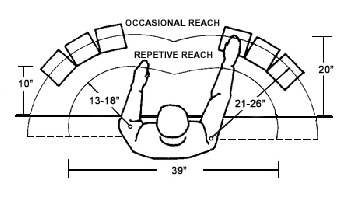
Rotation Strategies
Why Rotate?
Many stressors can not be engineered out of a task, short of complete automation. Rotation of assignments can be an effective means of limiting the amount of time employees are exposed to these stressors. This will often reduce the chance of injury, because the risk of injury is proportional to the amount of time one is exposed to a stressor.
Caution
Rotation of assignments should never be used before significant attempts to eliminate the stressors have been investigated. The job should always be modified to expose the employee to the least amount of stress possible. Analysis of the job is essential, because moving an employee between tasks that affect the same part of the body does not provide any periods of rest.
Rotate to Jobs that Affect Different Parts of the Body:
Many tasks primarily affect different parts of the body. Some example are:
- Lifting a heavy load.
- Repeatedly bending generally affects the low back.
- Reaching to access or to place items in positions that require the elbows to be pulled away from the body often affects the shoulder.
- Grabbing, turning, squeezing or finger strikes can affect the hand, wrist, and elbow.
- Looking down or to the side repeatedly for a prolonged time can affect the neck, head, and shoulders.
- Tasks that require standing for a long time can affect the legs, feet, and back.
Rotation of employees between tasks that affect different parts of the body allows employees to have periods of rest and recuperation while still remaining on the job. An example of a possible rotation scheme might be to move an employee who spends most of the day loading and moving boxes to a job where he is seated and performs a hand-oriented task such as assembly or trimming. While at the seated task the employee's back and legs can rest if a proper workstation is provided. While on the lifting task the hands and arms can rest if the loads lifted are not too large and proper hand holds are provided.
Rotate to Another Job That Has Less Intensity:
In many operations materials are fed to a workstation by conveyor belt. Employees at the leading edge of the belt are exposed to a full supply of product that must be processed, while those employees farther down the belt deal with reduced work demands because some of the product has been processed by the previous employees. Abundance of supply at the beginning of the belt keeps the work intensity high for employees in the lead positions while employees farther down the belt often have periods of time when there is little or no product to be worked on.
It is difficult to regulate work rate such that all employees work at the same pace. It is often easier to rotate employees through different positions on the belt so each is exposed to both fast and slower work positions. Usually this is accomplished by moving the lead person to the end of the line on a regular basis, such as every 15, or 30 minutes. This type of rotation pattern lessens the chance of any single employee becoming over exerted during the work shift.
Sit/Stand Stools
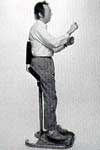
Sit/Stand stools are often an appropriate rest option for tasks that are best performed in a standing position. They allow employees to lean and rest but still keep them in a position to perform the task without the workstation modifications that would be necessary to convert to a seated workstation.
Scissors (Pneumatic)
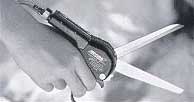
A variety of pneumatic scissors are available that greatly reduce the muscle force that must be exerted to close the scissor blades, eliminate the need to open the blades after completing a cutting motion, and that completely eliminate the contact trauma to the sides of the finger.
Scissors (Spring Activated)
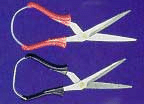
Spring activated, straight handled, hand scissors reduce the hazard to the employee's hand by eliminating the need to repeatedly open the blades, and by elongating the handle. By eliminating the finger and thumb loop, all the fingers can participate in closing the blades. Finger force is reduced and the contact to the insides of the fingers is greatly reduced.
Telescoping Conveyor
A telescoping conveyor capable of reaching into the full length of a transport truck can be used during truck loading operations. A telescoping conveyor that has vertical adjustment as well as horizontal adjustment may reduce the need for bending and reaching to access low and high locations and elevated reach distances.
Tilter Dumper
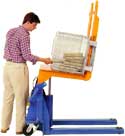
Using a tilter dumper raises the load so that employees do not need to bend to access product and allows the load to slide forward so that reaching motions can be minimized.
Tilted Work Surface
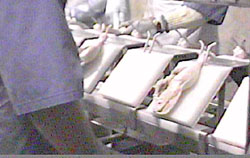
Tilting the work surface towards the employee allows the employee to perform cutting motions using a traditional straight-handled knife while maintaining a more neutral, straight wrist posture.
Tub Dumper
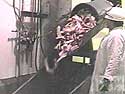
Tub dumpers eliminate most bending and reaching by mechanically emptying the contents of tubs or barrels.
Vacuum Lifts
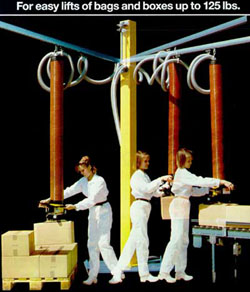
A mechanical lift uses machinery to provide the force that employees would normally need to exert with their back. This employee simply directs the load while the lifting mechanism does the work. Employees can lift 80 to 100 pounds while only exerting a few pounds of force.