Poultry Processing Industry eTool
Packout » Whole Bird
Whole Bird Bulk Packaging
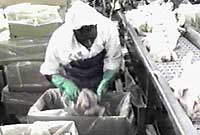
(See: Individual Packaging)
Whole bird bulk packaging involves boxing multiple whole birds. Entire birds are placed in a plastic-lined box. Liners are sealed, the container is weighed, ice is added and the container is sealed. Filled containers are then shipped or stored.
This operation includes the following tasks:
- Task 1: Box Liner: Places large bag inside shipping box.
- Task 2: Line Unloader/Box Filler: Lifts whole birds from conveyor and places them into shipping box.
Task 1: Box Liner
The box liner is responsible for placing a large plastic bag into the packing box. The bag is used to line the box to prevent loss of liquids and maintain freshness. This is important when packing whole birds because they are not sealed with any other waterproof material.
Hazards of this task may include:
Hazardous Situation
Problems can occur at this task because it is often an unplanned workstation, originally intended to be temporary. Placing such a workstation in a process line without adequate planning and space allocation can result in a highly congested work area, creating the potential for injury from working in awkward postures and coming in contact with other moving machinery.
Possible Solutions
- Redesign task station to provide adequate room for worker and performance of task.
- Whenever possible, replace manual operations with automated operations.
Hazardous Situation
Employees are required to repeat the same motion over and over (i.e., reaching and/or bending to obtain box stock and placing finished boxes on conveyor), which can result in work-related musculoskeletal disorders.
Possible Solutions
- Use palletizer to maintain position of box materials so employee can stand upright and keep arms in close to body during tasks.
- Whenever possible replace manual operations with automated operations.
- Rotate tasks.
- Provide an adjustable work table or stand so task can be performed without torso bending or reaching.
Task 2: Unloader/Box Filler
Birds are lifted directly from a conveyor and are placed into a shipping box. Employees may lift up to 3 birds in each hand. They may also need to reach up to about shoulder height to access birds and bend over at the waist to place birds in the packing box.
Hazards of this task may include:
Hazardous Situation
Repeatedly bending forward and reaching out away from the body stresses the back even if there is little weight being lifted because the upper body must be supported. When loads are being lifted, bending over at the waist increases the distance the load is held away from the body and increases the stress placed on the back.
Possible Solutions
- Use a diverter to push birds off the conveyor directly into the box so employees do not need to manually lift product.
- Provide a height-adjustable packing stand so boxes can be loaded without bending at the waist.
- Use a tub dumper at the workstation to empty contents on the conveyor.
Hazardous Situation
Employees lift multiple birds at one time, usually by the legs. Lifting 2-3 birds in each hand is not uncommon. Birds are cold and slick; employees usually wear rubber gloves that are also slick and may not fit well. All these factors increase the finger force that must be exerted. Exerting significant finger force can stretch and fray the tendons of the hand and can create a contact trauma to the tendon and sheath where they come in contact with bone or tendon. These types of actions increase the risk of tendonitis and carpal tunnel syndrome.
Possible Solutions
- Use a diverter to push birds off the conveyor directly into the box so employees do not need to manually lift product.
- Provide a height-adjustable packing stand so boxes can be loaded without bending at the waist.
- Use a tub dumper at the workstation to empty contents on the conveyor.
Hazardous Situation
Employees may be working at a position where they must reach up to access birds for packing. Tasks that force the employee to reach up and/or out are stressful to the shoulders and upper back.
Possible Solutions
- Use a diverter to push birds off the conveyor directly into the box so employees do not need to manually lift product.
- Provide a height-adjustable packing stand so boxes can be loaded without bending at the waist.
- Provide a height-adjustable work platform so employees can adjust their height in relation to the conveyor.
Whole Bird Individual Packaging
(See: Bulk Packaging)
Whole bird individual packaging involves packing the gizzard, liver, and heart with the whole bird and placing it in a bag. Individual bagged birds are then packed in boxes and iced for shipping. Packed boxes are placed on pallets for removal from the processing area.
This operation includes the following tasks:
- Task 1: Giblet Packer: Inserts heart, liver, and gizzard back into body cavity.
- Task 2: Bagger: Inserts whole bird into individual bag.
- Task 3: Bag Sealer: Pushes air out of and seals bag.
Task 1: Giblet Packer
Employee places heart, liver, gizzard and neck either directly into the body cavity of the bird or into a paper sack, which is then inserted into the body cavity before bagging.
Hazards of this task may include:
Hazardous Situation
Employees repeatedly reach into bins on supply tables to obtain parts for repackaging and to obtain bags in which to place the parts. Repetitive reaching stresses the shoulder and upper back.
Possible Solutions
- Position packing fixtures, bags, scales, and product so all activities of the task can be performed with the elbows in close to the torso.
- Tilt work surface so product slides to employee.
- Develop both left- and right-hand stations so employees can rotate through different stations and experience periods of working rest.
- Provide height-adjustable work tables, packing stands, or work platforms so task can be performed without torso bending or reaching.
Hazardous Situation
Standing for a long time reduces blood flow to the legs, forces isolated muscles to work for an extended time, and increases risk of fatigue and varicose veins.
Possible Solutions
- Install sit/stand stools, which allow employees to lean and have their weight supported while still remaining in an upright posture.
- Rotate employees between tasks that do not require prolonged standing.
- Provide shoe insoles that cushion the feet and spread foot pressure over a larger surface.
- Provide a foot rest in front of employees so they can shift their posture.
Task 2: Bagger
Bagger places bone-in parts in a plastic bag. A bagging fixture that holds the bag in the open position is often used. After parts are bagged they are generally placed back on the conveyor for packing.
Hazards of this task may include:
Hazardous Situation
Employees repeatedly reach into bins to obtain parts for packaging and to obtain bags in which to place the parts. Repetitive reaching stresses the shoulder and upper back.
Possible Solutions
- Use diverter bars to push the product closer to the employee.
- Reduce width of conveyor so the product is presented closer to the employee.
- Position packing fixtures and product so all activities of the task can be performed with the elbows in close to the torso.
- Tilt work surface so product slides to the employee.
- Develop both left- and right-hand stations so employees can rotate through different stations and experience periods of working rest.
- Provide adjustable work tables or stand so task can be performed without torso bending or reaching.
Hazardous Situation
Standing for a long time reduces blood flow to the legs, forces isolated muscles to work for an extended time, and increases risk of fatigue and varicose veins.
Possible Solutions
- Install sit/stand stools, which allow employees to lean and have their weight supported while still remaining in an upright posture.
- Rotate employees between tasks that do not require prolonged standing.
- Provide shoe insoles that cushion the feet and spread foot pressure over a larger surface.
- Provide a foot rest in front of employees so they can shift their posture.
Task 3: Bag Sealer
The bag sealer removes bagged parts from a conveyor and then directs the end of the bag into the bag sealer. Sealed product is then placed back on the conveyor so it can be boxed.
Hazards of this task may include:
Hazardous Situation
Employees repeatedly reach into bins to obtain parts for repackaging and to obtain bags to place the parts in. Repetitive reaching stresses the shoulder and upper back.
Possible Solutions
- Use diverter bars to push the product closer to the employee.
- Reduce width of conveyor so the product is presented closer to the employee.
- Tilt work surface so product slides to employee.
- Position bag sealing machines so employees may maintain neutral postures.
- Develop both left- and right-hand stations so employees can rotate through different stations and provide periods of working rest for employees.
- Provide adjustable work tables or stands so task can be performed without torso bending or reaching.
Hazardous Situation
Sealing the bag is also repetitive, as the employee must use pinch grips to grasp, lift, and feed the bag into the sealing machine.
Possible Solutions
- Rotate employees to tasks that do not require the use of repetitive forceful pinch grips.
- Use automatic bag sealers.
- Arrange the workstation so bags can slide while being moved from conveyors to sealing machines. This will limit lifting bags and reduce necessary finger force.