Machine Guarding eTool
Presses » Hydraulic Presses
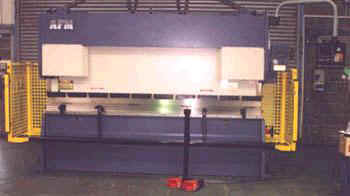
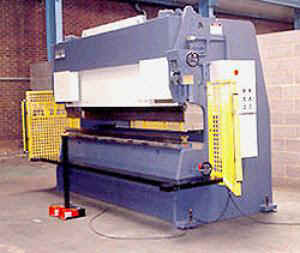
There are many varieties of hydraulic presses performing many different processes. Hydraulic presses can normally be stopped at any point in their cycle and the force exerted by the dies can be varied.
Operating speeds are normally slower than mechanical presses. However, because of their slower operating speeds they are normally not fully automated. Integral operator involvement is necessary, increasing the number of safety hazards and the need for applicable safeguarding.
Operator Involvement
The operator is responsible for feeding or placing the stock on the bottom die, seeing that it is properly positioned, activating the press cycle with a pressure control switch, and removing the completed part.
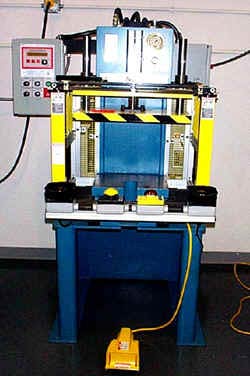
-
A hand or other body part near the point of operation during cycling can result in severe injury.
-
Material handling is hazardous as material may have sharp edges, be slippery or heavy.
Solutions
-
General machine guards (barrier guards, two-hand tripping devices, electronic safety devices, etc.) must be provided to protect the operator and other employees in the machine area from hazards created by point of operation, nip points etc. [29 CFR 1910.212(a)(1)]
-
Guards must not create hazards themselves, and must be attached to the machine where possible. [29 CFR 1910.212(a)(2) and (a)(3)(i)]
-
Use special hand tools to keep hands away from point of operation. [29 CFR 1910.212(a)(3)(iii)]
-
Operating controls should be located away from the die area and should employ dual palm buttons.
-
If a foot pedal control is used, it must be guarded.
-
An emergency stop button should be available with easy access to the operator and a main power disconnect switch is needed.
-
Power transmission components are normally located away from the operator; however, hydraulic pump/motor arrangements should be enclosed. [29 CFR 1910.219]
-
Work area should be kept clean to prevent slipping or falling hazards.